- 专题资料:
- 中国科学院金属研究所
- 专题制作:
- 国家材料环境腐蚀平台
联系我们
-
-
电话: 010-82387968 -
邮箱: shujushenqing@126.com -
地址: 北京市海淀区学院路30号 -
邮编: 100083
首页 > 舰船和海洋工程用铜合金金属腐蚀专题 > 腐蚀行为
总体概况
铜合金优异的耐海水腐蚀性能源于其表面产生的腐蚀产物膜。关于铝青铜的腐蚀产物膜的研究有很多。Ateya研究了单相α铝青铜在3.4% NaCl溶液中的腐蚀行为,结果显示,自由腐蚀条件下形成的腐蚀产物膜是双层膜结构,其内膜由Al2O3组成,外层由Cu2O、Cu2(OH)3Cl和Cu(OH)Cl组成。X射线结果发现:在开路条件下,Cu2O快速生成;随着浸泡时间盐城,出现Cu(OH)Cl;CuCl仅在阳极电位下形成,比开路电位高很多,在开路电位条件下没有探测到。
以上研究结果可以看出,由于MAB以及镍铝青铜铸态组织粗大,不均匀,甚至包含铸造孔洞等,这些将严重影响它们的机械、耐腐蚀以及空蚀性能。图14为一青铜螺旋桨断口处明显有铸造孔洞,这是导致这一螺旋桨短时间内失效的主要原因。
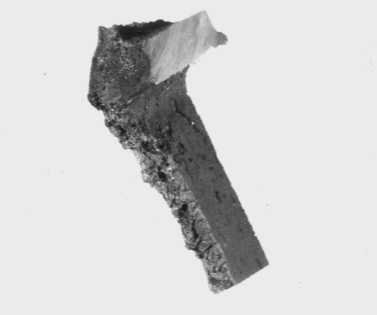
图4-20失效螺旋桨断口(含有铸造孔洞)
为了克服以上缺陷,研究者们提出了一些改善措施。Cheng等人采用了激光表面熔敷以及激光表面合金化对铸态锰镍铝青铜进行了表面处理,研究表明,激光表面熔敷显著细化以及均匀化了铸态组织(单一的β相),在表面形成了一层厚度约几百微米的熔覆层,表面硬度明显大于铸态MAB(铸态:160,激光熔敷后297-342/Hv0.2)。在3.5% NaCl溶液中的空蚀结果显示,激光表面熔敷后的MAB的空蚀性能相较于铸态MAB提高了5.8倍,相较于铸态镍铝青铜提高了2.2倍,图15为铸态MAB、激光熔敷后MAB以及铸态镍铝青铜在3.5%NaCl中平均空蚀深度-时间曲线。铸态MAB因组织比较复杂,会在相界处优先发生开裂,K相会下陷到基体内,裂纹扩展至周围组织发生严重损伤。而熔敷后MAB在空蚀应力下,在三晶交叉处首先开裂,随着时间延长,损伤沿晶界扩展,但是由于其组织比较均匀,硬度较高,因此相比于铸态MAB,空蚀源减少,损伤较均匀且程度较小。
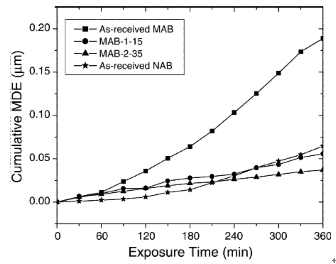
图15 铸态MAB,激光熔敷后MAB以及铸态镍铝青铜在3.5%NaCl中平均空蚀深度-时间曲线
据对铜合金螺旋桨断桨情况的调查分析与统计,桨叶在使用时的折断多为腐蚀疲劳引起的。Kim等人采用超音速喷涂(HVOF)在铸态镍铝青铜的表面制造了涂层并研究其对铸态镍铝青铜耐腐蚀疲劳性能的影响。为了避免电偶腐蚀,涂层的成分与基材是一致的。与其他涂层工艺相比,HVOF具有低孔隙率,涂层与母材结合力较好,成分均匀等特点。研究表明,带有涂层的镍铝青铜的腐蚀疲劳强度是140 MPa,大于铸态镍铝青铜(90 MPa)。然而在3.5%NaCl浸泡80 d后的失重以及形貌结果显示,带有涂层的镍铝青铜耐蚀性能较差。这是由于涂层中的一些缺陷,如孔隙会加重腐蚀,带有涂层的镍铝青铜的表面发现了微小裂纹以及点蚀坑等。在交变应力以及腐蚀性介质中,涂层内部点蚀坑生长,涂层与基体界面处发生腐蚀以及裂纹扩展,这些将优先阻碍铸态镍铝青铜基体发生疲劳失效,因此其耐腐蚀疲劳强度较铸态镍铝青铜高。李庆春等人模拟了船用螺旋桨的受力状态以及使用环境,对五种螺旋桨用铜合金的腐蚀疲劳性能进行了评价,它们的抗腐蚀疲劳性能优劣顺序为:ZQAl12-8-3-2 > ZQ10-6-7-3 > ZHAl67-5-2-2 > Lima55 > ZHMn55-3-1,可见青铜的性能明显高于黄铜。R.C. Barik等人也对铸态以及带有HVOF涂层的镍铝青铜在含砂海水中的耐冲刷腐蚀性能进行了对比,研究表明在低沙粒冲击动能下采用HVOF对螺旋桨进行修复以及翻新是可行的。在低沙粒冲击动能下,HVOF 镍铝青铜 与铸态镍铝青铜都表现出塑性变形以及切削磨损行为,然而在高沙粒冲击动能下,HVOF 镍铝青铜将会出现显著的裂纹扩展以及层状断裂等导致其耐冲刷腐蚀性能低于铸态[28].Hanke等人采用摩擦堆焊在铸态镍铝青铜的表面形成一种涂层(焊料与基体材质一样,涂层厚度600-800微米),结果显示摩擦堆焊后的表面组织明显细化以及均匀化。由于细小魏氏体α以及β‘的形成,堆焊后的表面硬度也明显大于铸态镍铝青铜。在蒸馏水中的空蚀结果显示:堆焊后的镍铝青铜的空蚀孕育期是铸态镍铝青铜的两倍,空蚀失重率是铸态镍铝青铜的一半。在空蚀应力下,堆焊后的镍铝青铜表现出更多的塑性变形行为,表面以下很浅深度内发生了变形,裂纹只在这一深度内进行扩展,因此空蚀损伤较小。而铸态镍铝青铜裂纹延伸至表面以下较深深度处,在相同空蚀时间内,表面空蚀坑深度远大于堆焊后镍铝青铜[33].由于螺旋桨的铸造缺陷和空蚀破坏严重区域常采用熔焊方法进行修复,对堆焊层的空蚀腐蚀性能及其行为的了解是很重要的。Li等人采用了熔焊的方法(钨极氩弧焊)在铸态镍铝青铜制造与基体成分相同的堆焊层。研究表明,堆焊层组织比较细小,空蚀性能明显优于铸态镍铝青铜。在空蚀应力下焊态表面发生塑性变形,在晶界处出现大量突起,随着时间延长演变成微坑。微坑扩展,连接,导致材料的脱落。
Sabbaghzadeh等人也对熔焊以及铸态的镍铝青铜的耐腐蚀性能进行了研究,结果显示铸态,焊态镍铝青铜在初期浸泡时自腐蚀电流分别为2×10-5 μA/cm2,2.1×10-5 μA/cm2,浸泡72h后,分别为9×10-6 μA/cm2以及7×10-6 μA/cm2.可见因焊态组织更为均匀,表面生成的腐蚀产物膜更致密,保护性更好。焊态和铸态之间电偶腐蚀密度差距只有几nA,因此采用焊补不会加重在海水环境中的腐蚀程度。Ohshi以及Ni等人采用了一种新型的工艺--搅拌摩擦处理(FSP)对铸态镍铝青铜进行表面处理[34, 35, 48-50].FSP,来源于搅拌摩擦焊(FSW)[51-53],是在材料熔点以下进行的,图4-22是FSW的示意图。
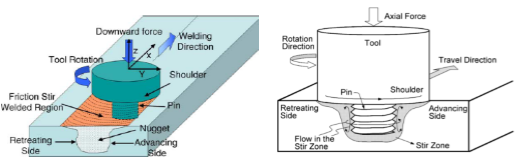
图16 搅拌摩擦焊(FSW)示意图
FSP能有效细化,以及均匀化铸态组织,消除铸态孔洞,此外它还避免了熔焊过程中可能引入的气孔等缺陷,以及涂层工艺中涂层与基体结合力较差的问题,是一种绿色的表面处理工艺。研究表明,FSP大幅度提高了铸态镍铝青铜的机械性能。通过对铸态以及FSP 镍铝青铜进行空蚀性能对比研究,结果表明,在蒸馏水以及3.5% NaCl中铸态镍铝青铜的空蚀失重是FSP 镍铝青铜的1.5和2倍。在相同的空蚀时间内,FSP 镍铝青铜表面的损伤远远小于铸态镍铝青铜,如图17.FSP在空蚀初期表现出更多的塑性行为,随着空蚀时间延长,空蚀坑出现,但是空蚀坑分布比较均匀,且深度远小于铸态镍铝青铜,通过对空蚀以后的截面进行观察发现(图18),其空蚀坑底部无铸态镍铝青铜中见到的较长裂纹。因此可见,由于FSP 镍铝青铜组织更为均匀细小,且机械性能(抗拉强度,硬度,延伸率)更优异,使得空蚀损伤均匀且损伤沿表面以下很浅区域内扩展。由于铸态镍铝青铜组织比较复杂,在3.5%NaCl中,会由于发生电偶腐蚀,粗化材料表面,从而在空蚀应力作用下,损伤加重。而FSP 镍铝青铜组织比较均匀,电偶腐蚀不显著,因此腐蚀对空蚀的增强作用不明显,因此铸态以及FSP镍铝青铜的空蚀失重在腐蚀介质中进一步加大[7].美国的NSWCCD公司已经将FSP实际应用在了螺旋桨的修复以及局部强化上。
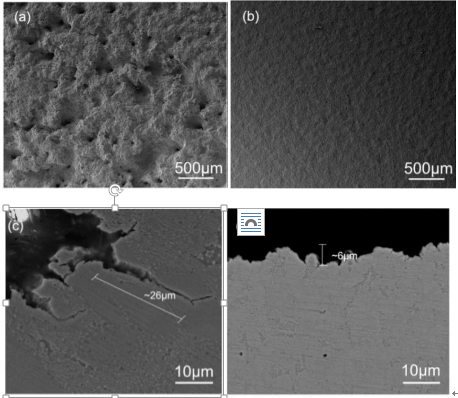
图17 铸态以及搅拌摩擦处理(FSP)后镍铝青铜空蚀不同时间以后的形貌:
铸态:(a)9 h, (b) 24h; FSP:(c) 9h, (d) 24h.
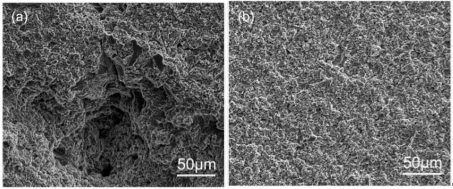
图18 铸态(a)以及搅拌摩擦处理(b)后镍铝青铜在蒸馏水中空蚀20h后空蚀坑截面形貌
(铸态:坑底部较长裂纹,FSP:坑底部无较长裂纹)
此外,Ni和Zheng等人也对搅拌摩擦处理后镍铝青铜的腐蚀性能进行了研究,结果显示,在3.5%NaCl溶液中浸泡相同时间后,搅拌摩擦处理后镍铝青铜的失重远小于铸态,见图19.长期浸泡以后的电化学阻抗谱结果显示,搅拌摩擦处理后镍铝青铜的表面形成了更具有保护性的腐蚀产物膜,见图20.对膜的成分以及结构进行表征,结果显示,搅拌摩擦处理由于未改变铸态镍铝青铜的成分,两者产生的腐蚀产物膜成分上并无明显差异。但是从两者截面形貌上看,腐蚀产物膜内都含有未溶相。与前面章节中的图4-14相比,搅拌摩擦处理后的镍铝青铜膜内的未溶相尺寸较小且弥散分布(见图21),这样能有效分散膜在生长过程中的应力,且在未溶相与周围腐蚀产物之间的薄弱界面不连续,不利于腐蚀介质的渗入,这些使得其表面产生的腐蚀产物膜更具有保护性。从图中也能看出,同样浸泡时间下,铸态镍铝青铜腐蚀坑深度(7 μm)明显大于搅拌摩擦处理后镍铝青铜(2 μm)。
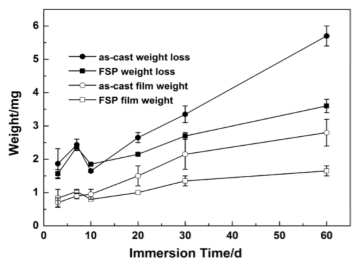
图19 铸态以及搅拌摩擦处理后镍铝青铜在3.5%NaCl中浸泡后的失重-时间曲线
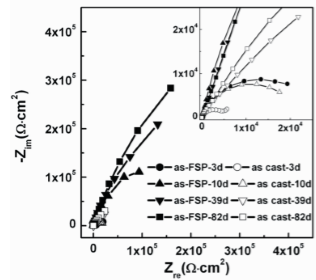
图20 铸态以及搅拌摩擦处理后镍铝青铜在3.5%NaCl中浸泡不同时间以后的Nyquist图
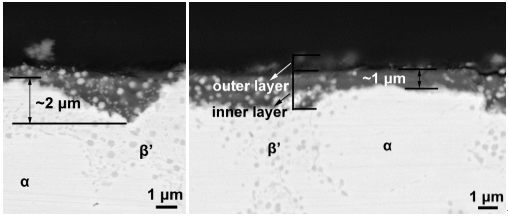
图21 搅拌摩擦处理后镍铝青铜UNS C95800在3.5%NaCl中浸泡2月后截面形貌(未溶相尺寸较小且分布弥散)
但是也有文献研究表明,搅拌摩擦处理后镍铝青铜耐冲刷腐蚀性能较铸态降低,他们认为搅拌摩擦处理后镍铝青铜内部有残余应力,会减低表面加工硬化能力,继而使得在冲刷条件下增加脆性断裂的倾向,导致在剪切唇上材料的断裂以及脱落,从而加重冲刷腐蚀失重,在冲刷角度为30°时最为显著。
为了提高铝青铜在海水中的耐蚀性,添加缓蚀剂也是比较常用的方法之一。ElWarraky等人研究了多种缓蚀剂对铝青铜在酸性4%NaCl(pH:1.8-2.0)中的耐蚀性的影响。随着温度升高,铝青铜在酸性4%NaCl腐蚀速率增加。失重曲线显示初期失重随着浸泡时间增加较慢,随后失重随时间呈线性增加。60 ℃时,BTA在添加浓度超过600 ppm时表现出较高的缓蚀效率;Thiourea(硫脲)延长了失重缓慢增长阶段;BTA和 TU降低了阳极极化电流;iodide ion (碘离子)、BTA以及TU共同作用明显降低腐蚀电流密度。Saoudi等人研究结果表明在3% NaCl中,所有的quinoxalines compounds (P4, YA1,YA2 and YA3)均能作为青铜有效的缓蚀剂,缓蚀效率与缓蚀剂组成有关,2-benzyloxy-dimethyl3,6-quinoxalin1-benzyl (带有酯类官能团的化合物)缓蚀效率高达97%,随着温度升高,缓蚀剂的缓蚀效率并没有明显改变,quinoxalines的加入提高了活化能。他们是通过在材料表面化学吸附形成了保护膜。Neodo等人研究了BTAH在不同pH 3.5% NaCl溶液中对镍铝青铜的缓蚀效率,结果显示在pH值大于4,BTAH对镍铝青铜的缓蚀效率较高(达95%以上),但是当pH值小于4时,BTAH对其缓蚀效率将严重下降。根据上面章节中提到的,镍铝青铜的腐蚀行为将相比于pH小于4的环境中发生阴阳极相的逆转,k相在酸性环境中将作为阳极相优先发生溶解,使得BTAH与镍铝青铜中k相之间的相互作用将减弱。这一行为表明BTAH对镍铝青铜的缓蚀作用并不是在所有环境中都能体现出来。
Zhang等人研究了热处理对Hot-extruded镍铝青铜耐蚀性的影响,研究表明,在3.5% NaCl溶液中浸泡后,annealed(750℃,1h,炉冷)组织中主要包括α+κ,失重最小,quenched(900℃,1h,水冷)组织中主要有α+β,失重最大,三者均表现出选择相腐蚀特征。其中微观组织中β和(α+κIII)相优先发生腐蚀,这些相的消除有助于腐蚀性能的提高。quenched镍铝青铜强度以及硬度明显高于Hot-extruded 镍铝青铜,但是塑性明显降低,耐蚀性变差;annealed镍铝青铜强度以及硬度略低于Hot-extruded 镍铝青铜,但是塑性明显增加,且耐蚀性提高,因此在设计热处理过程时要根据具体工况环境要求做好权衡。