- 专题资料:
- 中国科学院金属研究所
- 专题制作:
- 国家材料环境腐蚀平台
联系我们
-
-
电话: 010-82387968 -
邮箱: shujushenqing@126.com -
地址: 北京市海淀区学院路30号 -
邮编: 100083
首页 > 舰船和海洋工程用铜合金金属腐蚀专题 > 腐蚀行为
总体概况
铜合金优异的耐海水腐蚀性能源于其表面产生的腐蚀产物膜。关于铝青铜的腐蚀产物膜的研究有很多。Ateya研究了单相α铝青铜在3.4% NaCl溶液中的腐蚀行为,结果显示,自由腐蚀条件下形成的腐蚀产物膜是双层膜结构,其内膜由Al2O3组成,外层由Cu2O、Cu2(OH)3Cl和Cu(OH)Cl组成。X射线结果发现:在开路条件下,Cu2O快速生成;随着浸泡时间盐城,出现Cu(OH)Cl;CuCl仅在阳极电位下形成,比开路电位高很多,在开路电位条件下没有探测到。
镍铝青铜的腐蚀行为
由于镍铝青铜中相的多样性,不同相之间合金成分,结构上的差异,造成了它们在腐蚀介质中电位之间的差异,继而形成腐蚀微电池,从而引起腐蚀。根据研究,镍铝青铜在近中性的海水或者3.5% NaCl溶液中,β‘会优先发生腐蚀,此外,α基体以及与共析组织中的片层状α优先发生腐蚀,而组织中的κ相未发生腐蚀。图1是铸态镍铝青铜UNS C95800在3.5% NaCl中浸泡后的表面形貌[17].其中,Zheng等人对镍铝青铜C95800在3.5% NaCl溶液中浸泡后的截面进行了观察,发现共析组织处发生了较为严重的腐蚀,该处的腐蚀坑较α基体处明显深,见图2.
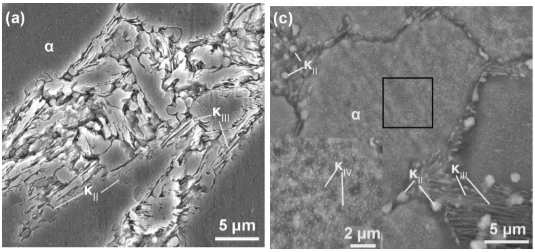
图1 铸态镍铝青铜UNS C95800在3.5%NaCl中浸泡(a)6h 和(b)15 d的表面形貌图
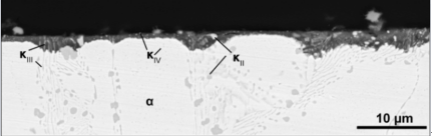
图2 铸态镍铝青铜UNS C95800在3.5%NaCl中浸泡2月后截面形貌(片层状共析体处发生严重腐蚀)
这是由于共析组织处α与κⅢ是相间排列的,即阴阳极相间排列,这样有利于微电池的形成,加速了腐蚀。根据在溶液中的腐蚀行为,各个相的腐蚀电位从低到高的顺序为β、α、κ(加文献)。κ因富含Al,在腐蚀介质中会在其表面生成Al2O3保护膜,Al与O的结合力大于Cu与O,且Al2O3的保护性由于Cu2O,因此κ在合金中作为阴极相。然而在酸性的海水以及3.5%NaCl溶液(pH<4)中的环境中,如缝隙腐蚀环境(低pH值,高Cl-浓度),镍铝青铜中相的腐蚀行为将发生逆转,κ会优先发生腐蚀,见图3.这是由于在酸性环境中,Al2O3已不能稳定存在,对κ相的保护作用将失去[16, 19],κ因含有较多的Fe, Al,因此电位低于富Cu的α相[17],在合金中作为了阳极相,优先发生溶解。
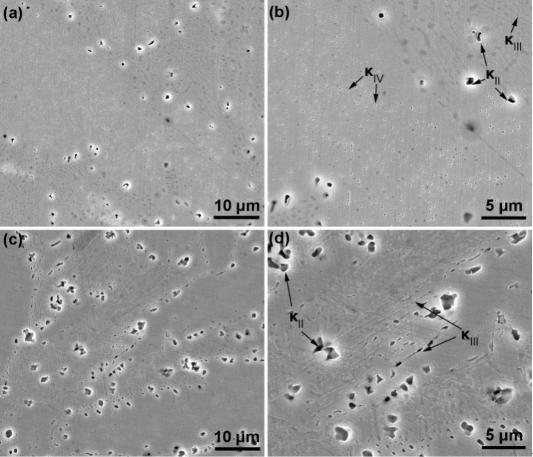
图3铸态镍铝青铜UNS C95800在酸性3.5%NaCl中浸泡不同时间后的形貌:
(a,b)30min;(c,d)6h.(a,c为小倍数图,c,d为大倍数图)
镍铝青铜的腐蚀产物膜
镍铝青铜在海水中优异的耐蚀性得益于其表面产生的腐蚀产物膜[20].在静态以及流动海水中(临界流速以内),镍铝青铜表面生成的腐蚀产物膜保护性随时间持续增加,直至稳定,腐蚀速率为0.015-0.05 mm/y(0.6-2.0 μA/m2)。在高流速下以及处于湍流状态下,镍铝青铜腐蚀产物膜将会发生破坏。研究表明,流速超过4.3 m/s时镍铝青铜腐蚀产物膜发生破坏,且腐蚀速率随着流速的增加呈现对数增长规律,在流速为7.6 m/s时,腐蚀速率为0.5 mm/y (20 μA/m2),当流速增加到30.5 m/s时,电流密度增加到0.76mm/y(31 μA/m2)。即使在流速为7.6 m/s时,镍铝青铜局部的腐蚀速率可达2 mm/y.研究表明,镍铝青铜表面的氧化膜厚度在800-1000nm左右,是外层主要为Cu2O,内层主要是Al2O3,由于Cu2O是P型半导体,因此空位是膜中的主要缺陷,而Fe、Ni能以离子形式占据该空位,从而提高Cu2O的离子以及电子电阻率,继而提高膜的保护性。Zheng等人通过观察镍铝青铜UNS C95800在3.5% NaCl溶液中浸泡后氧化膜进行研究,发现浸泡短期,XRD结果显示氧化膜的主要成分为Cu2O(图4),随着浸泡时间的延长,腐蚀产物膜呈双层膜结构(图5为XRD,图6为SEM形貌图)。EPMA结果显示(见图7),内层膜内Al,Fe、Ni的含量明显高于在基体中的含量,Cu的含量低于在基体中的含量,Cl含量很少,外层Cu含量较内层高,且Cl含量也高于内层,结合XRD以及产物膜截面的EPMA分析,该层主要是即Cu2(OH)3Cl.
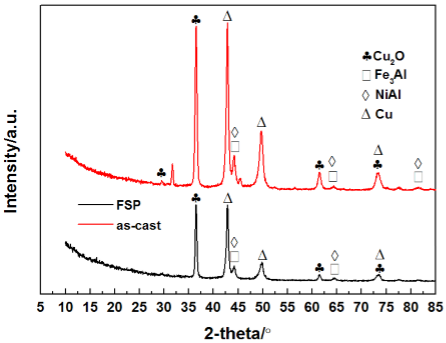
图4 铸态镍铝青铜UNS C95800在3.5%NaCl中浸泡5天后XRD图谱
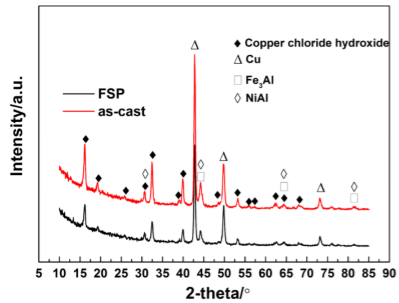
图5 铸态镍铝青铜C95800在3.5%NaCl中浸泡2 月后XRD图谱
对长期浸泡以后的试样进行截面观察,发现在不同组织处上膜是不同的。在α基体上膜较薄,而在片层状共析组织处膜较厚,且外层膜Cu2(OH)3Cl是不连续的,认为对基体没有保护性,并在共析组织处堆积见图6.此外,还发现一些未溶相留在了膜内。这是由于κ在合金中作为阴极相,随着周围α相的腐蚀,κ最终遗留在了氧化膜里。截面形貌显示κⅡ和κⅢ一部分在基体里,一部分在产物膜里,见图8.这些将会造成未溶相与周围腐蚀产物之间形成薄弱界面,有利于Cl-沿着薄弱界面进入氧化膜甚至基体,造成氧化膜的损坏以及基体的进一步腐蚀。而且,未溶相会增加膜在生长过程中的生长应力。α基体中κⅣ尺寸较小,且呈弥散分布,而共析组织处κⅢ呈连续的板条状,α基体晶界处κⅡ尺寸较大,因此共析组织处产物膜的薄弱界面更连续,造成Cl-更容易进入氧化膜,保护性较差,因此在此处腐蚀坑较深,而且Cl-更易与内层Cu2O反应生成更多的Cu2(OH)3Cl,这也是Cu2(OH)3Cl在此处堆积的原因。
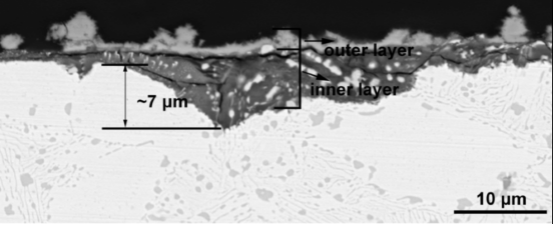
图6 铸态镍铝青铜C95800在3.5%NaCl中浸泡2月后截面形貌(双层膜结构)

图7 铸态镍铝青铜C95800在3.5%NaCl中浸泡2 月后腐蚀产物膜截面元素分布图
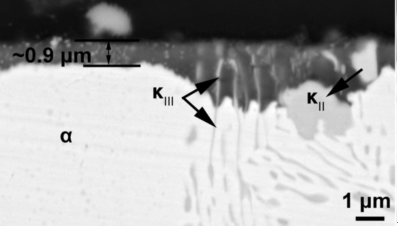
图8铸态镍铝青铜C95800在3.5%NaCl中浸泡2月后截面形貌(未溶相部分在基体,部分在膜里)
镍铝青铜在含硫化物的海水溶液中腐蚀速率会增加,这是由于硫化物会改变表面产生的腐蚀产物膜的结构,产物膜比较疏松且包含大量的CuS,其加快了氧还原反应的电荷转移过程。因此腐蚀过程受阴极过程控制,会在流动介质条件下对流速变化非常敏感。研究结果显示,镍铝青铜在无污染海水中自腐蚀电流密度为0.1 A·m-2,在含硫海水中,自腐蚀电流密度为5 A·m-2.在无污染海水中腐蚀速率稳定为0.001 A·m-2后放进含硫化物的海水中,电位立刻负移200 mV,电流最高增大到0.8 A·m-2,后稳定在0.02A·m-2;新鲜镍铝青铜试样在无污染的海水中短时间浸泡后腐蚀速率为0.07 A·m-2且随流速无明显改变,随着硫化物的加入,腐蚀速率增加到1.5 A·m-2且随流速增加而明显增加。
由于镍铝青铜大型铸件组织粗大,不均匀,且会有铸造孔洞等缺陷,这不仅会影响铸件的机械性能,还会导致在腐蚀介质中形成的产物膜不均匀,不连续,也会影响其耐蚀性。因此一些研究者们针对这些不足,对铸态镍铝青铜进行了处理。比如在表面通过超音速喷涂(HVOF)形成涂层,对表面进行激光熔敷,表面激光合金化处理,摩擦堆焊处理,还有搅拌摩擦处理等,以及通过添加缓蚀剂来进行缓蚀等。