六价铬电镀工艺在电镀行业中占据极其重要的地位,被称为三大镀种之一,至今应用已超过80a。电镀铬工艺作为电解铜箔的防氧化技术,具有工艺稳定、成本低廉、操作简单和耐蚀性好等优点,既能提高铜箔的常温防氧化性能,延长存放时间,又能降低铜箔劣化率,防止出现侧蚀。虽然六价铬电镀工艺的镀层美观、性能优异,但是存在不少缺点。在工艺技术方面,六价铬镀液分散能力和覆盖能力差,电流效率低(仅为10%~25%),并且对非溶性阳极板腐蚀严重,很容易引入其他杂质而污染镀液;在环保方面,六价铬是公认的致癌物质,对人体健康危害极大;同时镀铬废水加重了环境污染,增加了水处理成本。目前,各国政府都在一定程度上禁止或限制六价铬的使用。所以,新的代铬工艺的研究迫在眉梢。
笔者研究了电镀镍钼合金技术代替六价铬电镀工艺。电镀镍钼合金工艺镀液稳定,操作简单,对阳极板腐蚀较轻且镀层具有较好的耐蚀性能,而且镀液对人体健康危害小,废液处理成本低。本文主要对电镀镍钼工艺进行研究,并与六价铬电镀工艺在生产应用方面的一些性能进行比较,希望能够为镍钼代铬工艺的生产应用提供依据。
1·实验
1.1原料
三氧化铬,氢氧化钾,硫酸镍,钼酸钠,柠檬酸,稳定剂,玻璃纤维环氧树脂半固化片(FR-4料),软水,以及厚度35μm的电解铜箔。
1.2电解铜箔的表面处理工艺
为了提高电解铜箔的剥离强度和防氧化性能,需要对其毛(M)面和光(S)面进行表面处理[9],工艺流程分述如下。
(1)毛箔M面处理流程:酸洗—粗化—固化—水洗—锌合金—水洗—电镀铬(或电镀镍钼合金)—水洗—硅烷偶联剂—烘干。
(2)毛箔S面处理流程:酸洗—水洗—锌合金—水洗—电镀铬(或电镀镍钼合金)—水洗—烘干。
1.2.1酸洗
采用高酸低铜溶液,主要目的是清洗掉毛箔表面的氧化层,以便后续处理。
1.2.2粗化
与酸洗液成分相当,主要目的是增加毛箔M面的活性基点,提高铜箔的剥离强度。
1.2.3固化
镀液组成为高铜低酸,不仅能提高铜箔的剥离强度,而且能防止表面粗化层脱落。
1.2.4锌合金电镀
为锌–镍合金镀液,主要是保证铜箔S面和M面具有一定的高温防氧化性能。
1.2.5硅烷偶联剂处理
采用一定浓度的KH560偶联剂,主要是提高铜箔的剥离强度,也有助于提高常温防氧化性能。
1.2.6烘干
采用150~300°C的热风将铜箔S面和M面吹干,便于储存。
1.3电解铜箔电镀铬和电镀镍钼合金的镀液组成及工艺条件
电镀铬和电镀镍钼合金的镀液组成及工艺条件见表1。
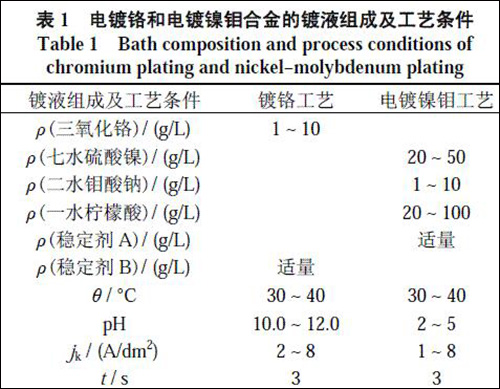
2·铬镀层和镍钼合金镀层的性能比较
2.1表面处理前后铜箔的抗拉强度及延伸率
抗拉强度和延伸率是衡量电解铜箔质量好坏的两个重要内在性能指标。如果铜箔的延伸率和抗拉强度较高,根据物体的热胀冷缩性能,那么在铜箔压成线路板时就不容易出现由于高温或低温引起的断路现象。表2给出了35μm电解毛箔和经过表面处理铜箔的高温和常温抗拉强度及延伸率的测量结果。常温抗拉强度由LD-1000A型1级电子式拉力试验机(济南嘉正仪器制造有限公司)测得;高温抗拉强度测试采用自制的高温抗拉强度仪,该仪器由常温抗拉强度仪和101A-2型电热鼓风干燥箱(龙口市电炉制造厂)组成,将常温抗拉强度仪中铜箔拉伸段移入电热鼓风干燥箱中,待温度升至180°C时进行测量。
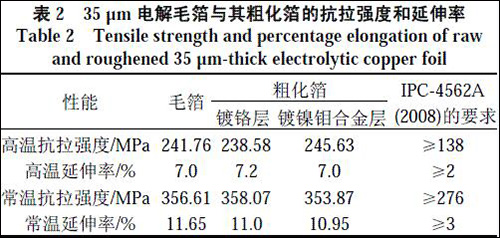
对表2的数据分析可知,电解铜箔和经过表面处理粗化箔的抗拉强度和延伸率的变化均在要求的范围内,表面电镀铬和电镀镍钼合金试样的抗拉强度和延伸率均无明显差异。因为粗/固化层、电镀铬层或电镀镍钼合金层的厚度相对于铜箔本身的厚度来说比较小,表面处理只是在毛箔微观凸起的中上部形成了少量沉积层,基本上不会影响电解铜箔的延伸率和抗拉强度,所以延伸率和抗拉强度主要取决于电解毛箔本身。尽管不同镀层造成铜箔的抗拉强度和延伸率有细微的差别,但均达到国家标准(GB/T5230–2000《电解铜箔》),符合生产要求。
2.22种镀层的耐高温氧化性
分别对电镀铬层和电镀镍钼合金层的试样进行耐高温实验,实验方法为:分别将试样放入210°C的高温电热鼓风干燥箱中,烘烤15min后观察表面氧化情况。通过对试样进行观察发现,电镀铬试样表面被完全氧化成黑色,电镀镍钼合金试样表面超过90%的区域发生了氧化。为了进一步比较2种镀层的耐高温氧化性能,缩短氧化时间后再进行比较。
将氧化时间缩短为10min,发现电镀铬试样被完全氧化,而电镀镍钼合金试样的表面有60%~70%的面积发生了氧化。继续缩短高温氧化时间至5min,发现电镀铬试样表面还是完全氧化,而电镀镍钼合金试样的表面只有30%~40%的面积发生了氧化,表面只形成了一层极薄的氧化层,其余部分均与原来的颜色保持一致。
将高温氧化时间固定为5min,温度分别降至200°C和180°C,观察电镀铬层和电镀镍钼合金层试样表面的氧化情况。当温度为200°C时,电镀铬试样表面完全氧化,电镀镍钼合金试样表面有30%~40%的面积发生了氧化;当温度进一步降低至180°C时,电镀铬试样表面被完全氧化,而电镀镍钼合金试样表面只有20%~30%的面积发生了氧化。由此可见,无论是从烘烤温度还是烘烤时间上来比较,电镀镍钼合金试样的耐高温氧化性能都要好于电镀铬试样。
2.32种镀层的常温防氧化性能
分别对电镀铬和电镀镍钼合金后的铜箔进行常温防氧化性能测试,具体步骤如下:
(1)每台机列取测试样一张,尺寸为300mm×1290mm),均匀地裁切成4张150mm×150mm的样品,取样时注意保护铜箔光面,避免汗水、唾液等外来杂物污染。
(2)运行LHU-213型恒温恒湿箱,设置试验条件,即温度80°C,相对湿度90%。
(3)用不锈钢钎从样品边角处穿入,每张样品之间保持一定的距离,悬置于恒温恒湿箱内,测试24h后检查铜箔光面的氧化情况。
根据客户要求及行业生产标准制定的判断依据为:氧化点个数A=0为优,1≤A≤2为合格,A>2为不合格,表3给出了试验结果。

由表3的实验数据得知,电镀铬试样和电镀镍钼合金试样在150mm×150mm范围内的氧化点个数都合格,满足客户要求。由此可见,电镀镍钼合金镀层和电镀铬镀层的常温防氧化性能相当,都能满足生产的要求。
2.4剥离强度及劣化率
通过双层自动电脑控温双层平板压机(郑州大众机械制造有限公司),将3个电镀铬试样和3个电镀镍钼合金试样分别压制在6张玻璃纤维环氧树脂半固化片(即FR-4料)上,压制温度为170°C,压力为10~13MPa,压制时间为100min,得到覆铜板样品。然后在其光面上覆盖宽为3mm的印制线路板专用胶带,再将其放在蚀刻液中,10~15min后取出,用BK-2型称重传感器(航天科技集团北京嘉祥高科技开发公司)做剥离强度测试,此为蚀刻后试样的剥离强度,结果见表4。将蚀刻后的试样浸泡在15%的盐酸溶液中30min,取出后再用BK-2型称重传感器对蚀刻条进行剥离强度测试,浸泡盐酸后剥离强度降低的幅度称为劣化率(以百分数表示),测试结果也见表4。
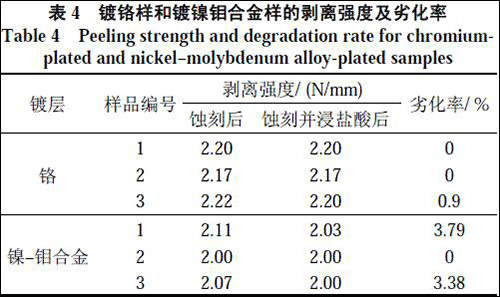
由表4可以看出,电镀铬覆铜板样品的剥离强度要好于电镀镍钼合金覆铜板样品,且劣化率也稍好;虽然电镀镍钼合金覆铜板样品的剥离强度偏低,劣化率偏大,但都符合35μm铜箔压制FR4板浸前和浸后的剥离强度都不能低于1.80N/mm、劣化率小于5.0%的生产要求。通过对两样品浸后的蚀刻条观察发现,两样品在蚀刻和浸泡30min的过程中均未发生侧蚀现象,即铜箔的毛面镀层能够抵抗酸液短时间腐蚀,且毛面的颜色均匀。
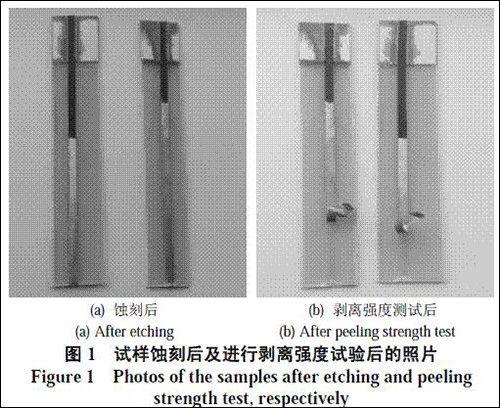
图1为试样蚀刻后和剥离强度测试后的照片。观察已蚀刻掉铜箔的基板可以发现,2种镀层试样在基板上均无残留物,应该蚀刻掉的部分被完全蚀刻干净,而且两者在蚀刻液中的蚀刻速度也相当。
综上所述,电镀铬和电镀镍钼合金的铜箔的化学性质都比较稳定,在印制电路板蚀刻时,可以最大限度地避免侧蚀现象的发生,保证线路板质量的稳定。
3·结论
从满足电解铜箔生产要求的方面着手,对电镀铬镀层和有望代铬的电镀镍钼合金层进行了一些性能上的比较,得出以下结论:
(1)高、常温抗拉强度和延伸率是电解铜箔本身固有的物理性能,通过表面粗化、固化、电镀铬或电镀镍钼合金等一系列处理后,电解铜箔的抗拉强度和延伸率均未发生下降。
(2)电镀镍钼合金试样的高温耐氧化性能好于电镀铬试样,而两者的常温防氧化能力相当,均满足生产要求。
(3)电镀铬层覆铜板的剥离强度和劣化率均好于电镀镍钼合金层的覆铜板试样,但都符合生产要求,并且两者的蚀刻速度相当,蚀刻后基本无残留物,保证了PCB厂家的质量稳定。