渗氢是在电镀、酸洗或阴极电解除油等表面处理过程中,氢以原子状态渗入工件基体或镀层中造成的。渗氢使金属基体内应力增大,硬度及强度增加,塑性降低,严重的造成晶格歪扭,直至断裂。若在基体上镀覆,渗氢使镀层变脆,甚至起泡、剥落或断裂。金属材料在氢和应力联合作用下产生的早期脆断现象就叫氢脆。
1 渗氢的危害及影响
各种元素的原子大小不同,由于氢原子的渗入,使合金的晶格发生歪扭,内应力增大,从而使合金塑性变形阻力增大。渗氢的钢件如不进行除氢处理,会大大降低钢的疲劳强度和使用寿命。以镀铬为例:由于在镀铬过程中,阴极产生的氢气,不仅会渗入铬层晶格之间,而且会渗入被镀的基体金属中,增加了基体金属的内应力,再加上铬层与基体金属的应力,这就大大降低了钢的疲劳强度,如表1所示。当零件越薄时,危险性越大。产生的内应力随着渗氢厚度的增加而增加,当达到一定程度时,会产生网状裂纹,降低零件的疲劳强度。
表 1 铬层厚度与疲劳强度的关系
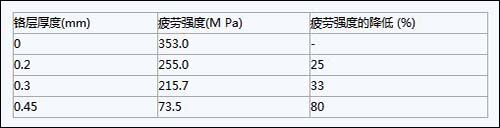
表面处理过程中,氢原子除向内部扩散外,渗入金属的氢原子还向表面扩散,而在金属的缺陷处化合成氢分子。同时,气态氢分子的压力增加,在这些地方,压力可达到很高的数值,以致使材料变坏,或受载力显著增加。特别是高强度钢或薄壁件、弹簧件对氢脆的敏感性较大。
2 渗氢的原因
2.1电镀过程中渗氢
若电沉积在较高的阴极极化作用和较低的氢过电位进行时,那么,氢就会大量析出。对于不同的镀种和工艺条件的不同,氢的析出量也不同。镀层的不同的厚度处会含有不同量的氢。不同的镀层吸收氢的程度也不相同。铬镀层的吸氢量较大(达0.45%,按镀层重量百分比),铁族金属稍小些(达0.1%),锌更小些(达0.001%~0.01%)。其它金属的吸氢量更少,有的甚至不存在。
吴辉煌等测得了碱性镀锌条件下的渗氢电流曲线,其特征是渗氢电流开始急剧上升随后下降,中间出现最大值[]。
2.2零件酸洗时渗氢
电位比氢电位更负的金属,都有被酸溶液腐蚀的倾向,同时有氢的析出。如高强度钢和高碳钢酸处理时,若在酸浓度高的场合,短时间内就容易引起氢脆。
吴辉煌等测得了普通碳钢材料在不同浓度盐酸腐蚀溶液中的渗氢电流曲线[2]。结果表明,稳态渗氢电流随酸浓度的增大而增大,这被解释为酸浓度的提高加快了钢的腐蚀,因而金属表面上产生的氢原子数目增多,它们渗如金属后势必引起较大的渗氢电流。
2.3阴极电化学除油或阴极电化学腐蚀时渗氢
原理同2.1。
3 减少渗氢的措施或消除渗氢
3.1提高析氢的过电位
电镀时使H+不易析出或很少析出。一切使得H+难以放电的因素,都能提高氢的过电位,也就使得阴极上析氢减少,从而减少渗氢。这些因素可归纳如下几点:
①阴极材料的影响。不同材料的阴极(镀件)有不同的析氢过电位。也就是说,氢在不同金属材料上析出来的难易程度是不同的。例如:铸铁、高碳钢、高合金钢比低碳钢及低合金钢析氢量多,这是因为前者含有石墨、镍、铬、钛等元素,降低了氢的过电位。铅、锌、镉、锡作基体时,氢过电位较大;钛、钯、铬作基体时,氢过电位小;铁、钴、镍作基体时,氢过电位居中。以镀锌为例,氢在钢铁上要比在锌层上析出容易得多,所以工件入槽后,氢气泡首先在钢铁工件上析出,当锌层覆盖工件后,析氢量就很少了。
②阴极材料表面状态的影响。喷砂的钢铁件和磨光、抛光的钢铁件,在电镀时阴极上析氢量也不同。喷砂件表面粗糙,氢的过电位小,容易放电,所以析氢较多;而磨光、抛光件表面光滑,析氢就较少。在酸洗中容易“过腐蚀”的零件,特别是铸铁及高碳钢零件,在电镀时析氢特别多,金属沉积速度缓慢,这是因为零件表面存在着游离的石墨即碳,使氢的过电位降低。若已采用强腐蚀而产生挂灰,可用铬酸出光,以提高析氢过电位,减少阴极零件渗氢。
③阴极电流密度的影响。决定析氢量多少,或零件渗氢多少的,不只决定于氢过电位绝对值大小,还决定于氢的析出电位与金属的析出电位的相对值大小以及它们随阴极电流密度变化的程度。
④溶液pH值的影响。在酸性溶液中,氢的过电位随pH值增大而变大,但在碱性溶液中则相反。在酸性溶液中,因为pH值增大后,电极表面附近氢离子的浓度相应降低,故氢的过电位增加。所以,对微酸性及微碱性电解液,控制值是很重要的如普通镀镍电解液pH值为4.0~5.2。
⑤添加剂的影响。有些添加剂能使氢的过电位增大,有些可使氢的过电位减小,因而影响析氢量。锌酸盐与钾盐镀锌所用的添加剂不同,它们的析氢量以锌酸盐为大,可见析氢量与添加剂有一定关系。
⑥电流效率的影响。电流效率高的电镀液,如氯化物镀锌和镀镍电镀液,其电流效率都很高,氢的过电位较大,析氢少;电流效率低的电镀液,如镀铬电镀液,氢的过电位较小,析氢大。相同镀种不同工艺的电镀液,电流效率也不同。钾盐镀锌比锌酸盐镀锌电流效率高,因而析氢量也比锌酸盐的少。
此外,镀液中络合剂的种类及数量,也会影响到氢的析出。一般来说,对金属络合力强的络合剂的游离量增加时,析氢较多,电流效率降低。
3.2用化学除油代替阴极电化学除油
尤其是对薄壁及弹性零件、高温合金零件效果明显。
3.3用低浓度的酸,短时间处理。尽量采用常温条件下的酸洗,盐酸在常温条件下同样对氧化皮有较强的浸蚀能力,而对钢铁基体的浸蚀相对缓慢,故有利于减轻渗氢程度。
3.4使用缓蚀剂
在不能降低酸浓度和缩短处理时间的情况下缓蚀剂能吸附在裸露金属的活性表面上,提高氢的过电位,从而减缓了金属的腐蚀,减少渗氢。在酸洗液中加入0.2%左右的有机缓蚀剂如苯胺、硫脲或磺化蓖麻油,就能有效地抑制金属的腐蚀。
倘若改变缓蚀剂的品种和用量并进行类似的测定,即渗氢电流与腐蚀液种类、浓度的测定,便可根据渗氢电流值的大小来确定最佳酸洗条件[2]。
3.5进行喷砂、抛光等机械处理
为了避免长时间的酸处理,机械处理可以防止零件渗氢。
3.6酸处理后用高温碱液浸渍。
此法可将零件吸收的H2逐出[3]。
3.7酸溶液脱氧
含溶解氧或暴露在空气中的酸溶液,一般比无氧酸溶液中的腐蚀性更大,渗氢更多。所以,脱去酸溶液中的氧,将使其腐蚀性及渗氢量减小[4]。
3.8电镀后进行除氢处理
①一般钢零件:180~220℃,2~3h。
②渗碳、氰化件、细钢丝:140~160℃,2h。
③精密件、复杂组合件及铜合金组合件。在航空润滑油中于140~160℃,保温2h。
④带锡焊的镀锌件:140~160℃,2h。
除氢后,可使镀层和基体的脆性减小,韧性增加,并使镀层和基体的结合力得到改善。
4.结语
渗氢对基体和镀层都有很大的危害,特别是氢脆很少在电镀完工后出现,但存放到一定时间就会“爆发”,所以其隐蔽性很强,往往被忽视。电镀时,只要加强重视,选择能够避免或减少渗氢的工艺流程,严格控制工艺规范,进行镀后处理,渗氢还是可以减少和预防的。