电镀锌板流星状白色亮斑缺陷的研究
2016-07-13 09:55:34
作者:刘亮,桂洲,马珩嗥,周一中,谢懋亮,雷凯,张小红 来源:中国电镀助剂网
某冷轧电镀锌生产线开机生产后,陆续反映生产过程中,某低碳钢牌号钢板表面出现流星状白色亮斑缺陷,单个缺陷大小约1mm×3mm,分布的特征是,主要集中在上表面(对应热轧上表面)宽度方向中部,整卷头、尾50m以内,边部300mm以内没有该缺陷,当上表面缺陷比较严重时,下表面也有少量该缺陷发生。
1、缺陷检测和分析
1.1冷轧电镀锌板SEM分析
电镀锌板上表面的流星状白色斑点如图1所示。将缺陷样脱去镀锌层制成金相试样,能谱分析显示缺陷区域与正常区域化学成分无异常,缺陷区域基板表面缺陷形貌呈柳叶状(图2(a)),局部放大500倍观察(图2(b)),组织存在明显的混晶现象,初步判断亮斑缺陷与基板混晶有关。
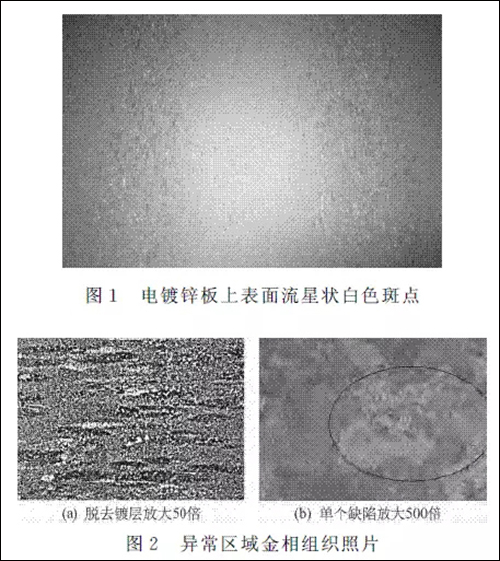
1.2热轧原板金相分析
为了弄清冷轧板出现的混晶是否与热轧工序存在关联。送热轧原板试样6件检验,编号为1号、2号、3号、4号、5号、6号。热轧板板宽约1200mm,1号~6号为沿宽度方向每200mm一个样,检测结果如表1所示。
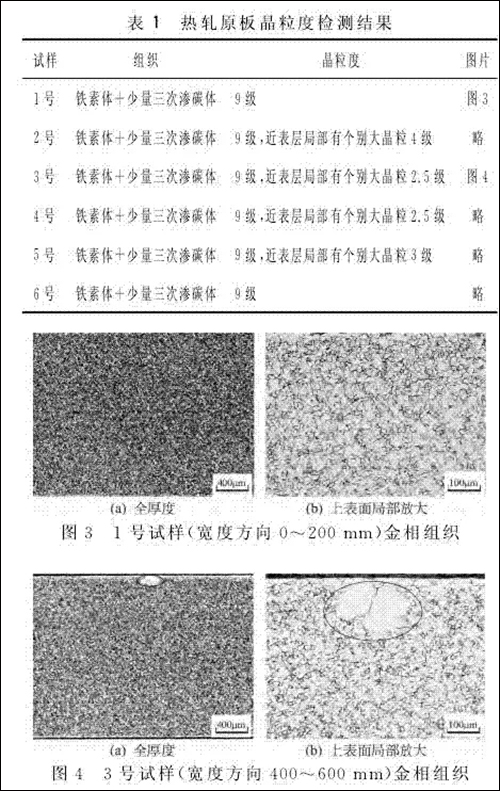
由表1和图3、图4典型金相检测结果可知,混晶均发生在上表面,沿宽度方向边部(0~200mm和1000~1200mm范围内)晶粒度正常。沿宽度方向200~400、400~600、600~800、800~1000mm等局部区域有粗大晶粒出现。综合上述金相检验结果,发现电镀锌板流星状白斑对应位置存在混晶现象,并确认冷轧板混晶现象和热轧板相关。
2、热轧混晶原因及试验结果分析
2.1混晶原因分析
针对热轧板出现的晶粒异常,结合该电镀锌基材化学成分和热轧工艺开展相关因素分析。如表2所示,通过比较发现FT7目标温度较Ar3富余量偏小,相差约10℃。一旦终轧温度控制不稳定,易出现两相区轧制情形,发生混晶。
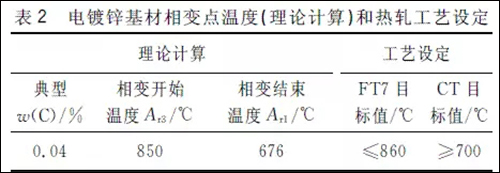
另外,该钢种卷取目标温度设计偏高(CT温度>Ar1),由晶界迁移驱动力公式:
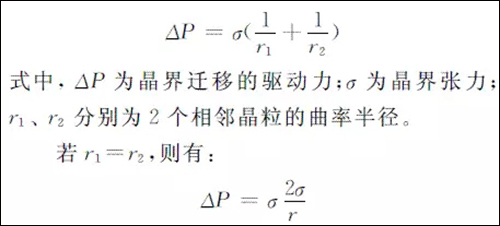
在温度场的影响下,大晶粒具有界面能较低的特点,故界面张力更小。大晶粒曲率半径更大,晶界迁移所需驱动力反而更小,处于优先长大的地位。在较高的卷取温度下,粗大晶粒优先成长起来,将会以较快的速度吞噬周围的小晶粒。在冷轧退火过程中晶粒度差异进一步劣化,最终形成严重的混晶组织。
2.2试验结果分析
为了验证流星状白斑缺陷与热轧板混晶的相关性,开展了多轮热轧工艺调整试验。首先将FT7目标值上调20℃,CT目标值保持不变,经统计,流星状白斑缺陷发生率从54%降低至25%左右;然后,在FT7目标上调20℃的基础上,以每20℃为1个试验批次逐步下调CT目标值,经统计,随着CT的逐步下调,缺陷发生率继续下降,当CT目标值调整到“目标值-40℃”时,缺陷完全消失。统计结果如表3所示。
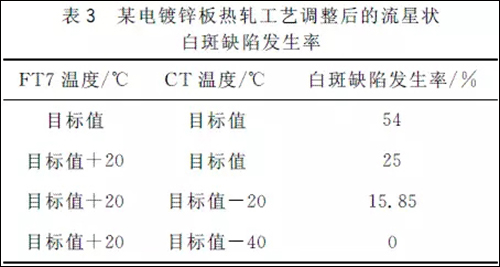
综合分析上述热轧工艺试验结果认为,电镀锌板表面流星状白斑缺陷与热轧板混晶存在关联,且与FT7、CT目标值设定相关性显著。较高的FT7有利于从源头上降低两相区轧制的风险,防止不均匀晶粒的发生。一旦混晶粒形成,则较低的CT有助于改善混晶组织的劣化程度,是一种强力有效的补救措施。
3、消除电镀锌板流星状白斑缺陷的措施
3.1调整热轧生产工艺
在多轮热轧工艺调整试验的基础上,确定了表4所示的最终调整方案。
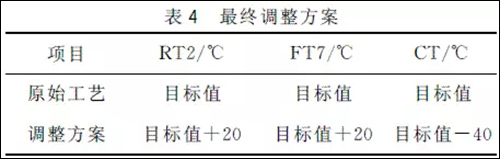
3.2避免精轧漏水
1)采取措施避免精轧F1~F6工作辊冷却水反弹、漏洒,造成带钢表面局部温降过大;
2)生产电镀锌钢板时,关闭某些冷却水,避免漏水滴溅到带钢表面。
4、改进效果
如图5所示,从2012年4月开始,电镀锌板发生批量流星状白斑缺陷,通过6月、7月多个批次的热轧工艺调整试验并最终固化工艺,至2012年8月缺陷基本消除。
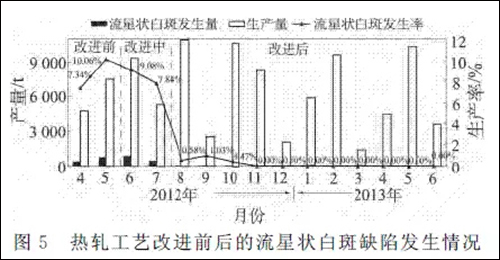
5、结语
1)本次电镀锌板表面批量流星状白斑缺陷与热轧板混晶存在关联,且与FT7、CT目标值设定相关性显著。
2)造成热轧板混晶的主要原因有2个:一是原FT7目标值设计偏低,现场适应性差,一旦终轧温度控制不稳定,易发生两相区轧制情形,引起铁素体混晶;二是原CT目标值设计偏高,钢卷入库后温度长时间保持在铁素体再结晶温度以上,容易发生粗大晶粒吞噬小晶粒的现象,导致混晶更加劣化,并遗传至冷轧退火后最终为混晶组织,表现为电镀锌后上表面流星状白斑缺陷。
3)较高的FT7有利于从源头上避免混晶形成;其次,通过减少精轧F1~F6机架间漏水,可以有效防止板面局部低温;避免发生在两相区轧制的现象,而较低的CT有助于改善混晶组织的劣化程度,是一种强力有效的补救措施。
免责声明:本网站所转载的文字、图片与视频资料版权归原创作者所有,如果涉及侵权,请第一时间联系本网删除。