聚合物先驱体材料体系的陶瓷化研究进展与展望
2016-08-16 16:14:56
作者:本网整理 来源:网络
引言
随着机械装备不断向高速、重载、集成化、高精度、长寿命等苛刻方向发展,其摩擦零部件服役的工作环境日益苛刻,单纯金属材料已难以满足要求。在金属零部件表面制备高性能的涂层材料并赋予其特殊功能,已成为解决金属零部件在苛刻工况下可靠服役的有效途径。陶瓷涂层具有耐高温、耐磨损、耐腐蚀以及抗氧化性能好、密度低等优异性能,但也存在塑性差、裂纹敏感、质脆等不足,故其应用受到了一定的限制。克服陶瓷涂层不足的有效方法是在金属零部件表面原位制备陶瓷涂层,使金属零部件既具备金属材料的强度和韧性,又具有陶瓷材料耐高温、耐腐蚀、耐磨损的优点。近年来,人们发展了一些制备高性能陶瓷涂层材料的有效方法,如激光熔覆法、化学气相沉积法(CVD)、溶胶-凝胶法、先驱体转化陶瓷(PDC)法[3],其中PDC法是一种很有前途的原位制备陶瓷涂层的技术。PDC法是将有机聚合物先驱体进行高温裂解处理,使之从有机聚合物转变为无机陶瓷材料的方法与工艺,其优点是制备工艺简单,先驱体丰富,陶瓷组成、结构和性能可设计和调控,成型和加工容易。其工艺流程如图1所示。
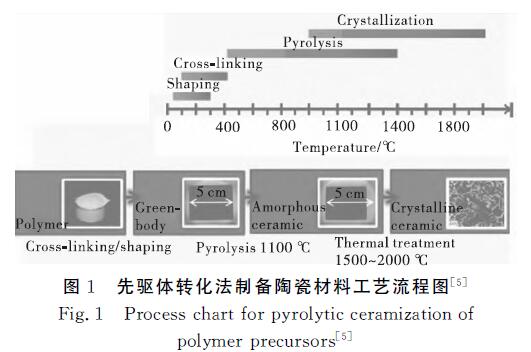
PDC法工艺过程主要分为成形、交联、裂解和结晶四步。成形是在室温下将先驱体溶液采用喷涂、涂覆或浸渍等手段在基材表面制成液态膜。将所得基材在空气中加热到100~300℃交联固化一段时间,通过交联固化可以抑制小分子气体的逸出,提高陶瓷产率。交联后以一定的升温速率逐步升温,在800~1400℃的温度范围内先驱体逐步裂解生成无定形陶瓷。随着温度进一步升高,无定形陶瓷内部分子链断键、结构重排,SiC晶体析出并进一步长大完全结晶,生成SiC陶瓷。
PDC法中的陶瓷相是原位合成的,陶瓷相很细小且分布很均匀,与基体结合非常好,耐磨、防腐性能优异。此外,PDC法克服了传统加入方法中陶瓷相与基体润湿性差的主要弱点,也避免了陶瓷相在增强的同时又成为裂纹产生的根源。但PDC法目前也存在一些不足:其一是有机聚合物先驱体在裂解过程中产生小分子化合物,使制备的陶瓷材料孔隙率较高;其二是有机聚合物先驱体在裂解过程中伴随着体积收缩和密度增大两个变化,使制备的陶瓷材料容易出现裂纹,如图2所示。
本文综合介绍了高陶瓷产率的聚合物材料体系,以及高温裂解制备陶瓷涂层的研究现状,并对未来的研究重点进行了展望。
1 高陶瓷产率聚合物先驱体材料体系
聚合物先驱体在高温裂解中具有高的陶瓷产率是PDC法制备陶瓷材料的首要条件。为了获得具有高陶瓷产率的有机聚合物先驱体,人们从下列三方面进行了较为深入的研究。
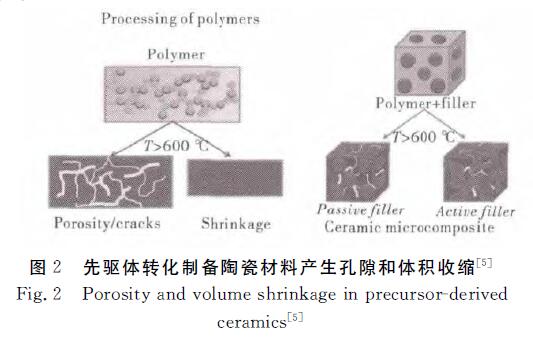
1。1 有机硅聚合物先驱体裂解体系
1975年,日本东北大学的矢岛教授发明了合成聚碳硅烷技术,并成功制备出SiC陶瓷纤维,从此开辟了有机先驱体制造无机陶瓷材料新时代,随后日本、美国、西欧以及我国的国防科技大学、西北工业大学、北京航空航天大学等单位的学者在这一领域进行了较为深入的研究,表1给出了近年来研发的具有高陶瓷产率的有机先驱体以及所制备的陶瓷材料的一些基本情况。
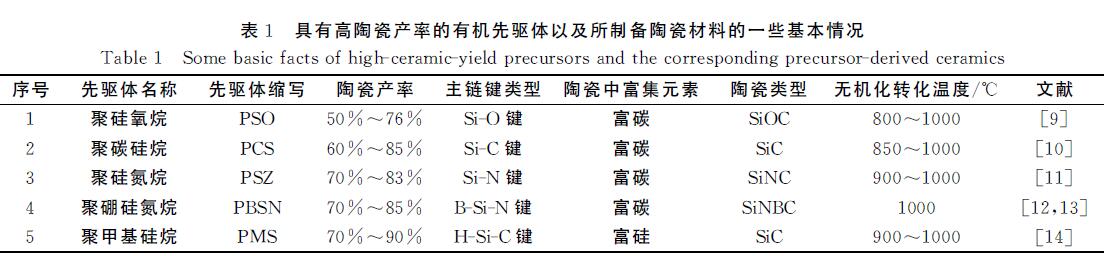
在研制不同主链结构有机硅先驱体的同时,研究发现侧链基团的组成与结构也会影响裂解陶瓷材料的组成、结构和性能,如侧链含有环状结构或Si-H、Si-CH=CH2等活性基团时,热裂解可获得较高的陶瓷产率。
1。2 金属有机硅聚合物先驱体裂解体系
利用分子结构可设计、陶瓷结构和组成可调控的特点,通过在上述几类有机硅先驱体中引入金属原子,使金属原子在裂解过程中与Si、C原子发生化学反应,生成耐高温的硅化物、碳化物或金属间化合物,使裂解陶瓷产率提高,生成的陶瓷材料的综合性能改善,并赋予陶瓷材料一些特殊功能,已成为裂解制备高性能陶瓷材料发展的主流方向之一。
日本宇部兴产公司(Ube Industries)合成的聚钛碳硅烷(PTCS)在氮气保护下高温裂解得到的SiCTi陶瓷材料,其耐温性由1000℃上升到1500℃,Ti原子的引入抑制了β-SiC晶粒的长大和高温析晶,极大地提高了SiC陶瓷材料的耐高温性能。
Wen等通过聚碳硅烷和乙酰丙酮铝反应,获得聚铝碳硅烷,将聚铝碳硅烷热裂解制备出Si-C-O-Al陶瓷材料,Al元素的引入大大改善了陶瓷材料的热稳定性和耐化学腐蚀性,各方面性能明显优于Nicalon系列SiC陶瓷材料,如图3所示。
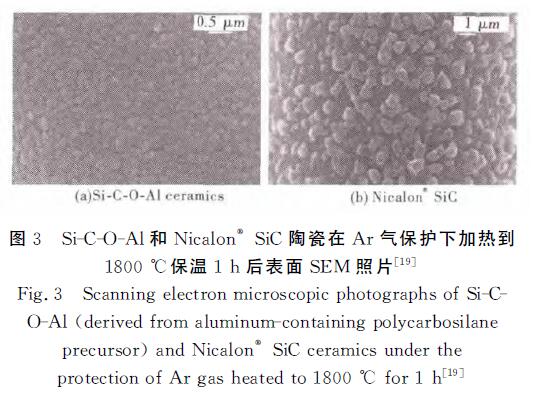
曹峰等采用乙酰丙酮铝和聚碳硅烷反应制备了聚铝碳硅烷,并将其热裂解制得SiAlC 陶瓷材料,其化学组成为SiC1。15O0。026Al0。013,其主要结构是平均晶粒为95nm 的β-SiC,在1800℃下具有良好的抗氧化性能。Yao等利用聚铝碳硅烷为先驱体,通过高温裂解制备出耐高温的含Al的SiC陶瓷薄膜。该薄膜以β-SiC晶粒和游离碳为主,细小的等轴β-SiC晶弥散分布在晶体中。
Manabu等利用三乙氧基甲基硅烷与五乙氧基铌反应,获得聚铌碳硅烷。将其在惰性气氛下经过1000℃高温裂解1~3h,可得到陶瓷产率90%以上的SiNbCO陶瓷材料,该陶瓷材料在氧化气氛中可耐1200℃高温。
陈志彦等采用二茂铁与聚二甲基硅烷在高温和氮气保护下合成出聚铁碳硅烷,将其在N2中1320℃高温裂解,获得陶瓷产率约70%、含Fe富C的SiC陶瓷材料,该陶瓷具有较大的电损耗和一定的磁损耗,是性能优异的吸波材料。
1。3 活性填料+有机硅聚合物先驱体裂解体系
在先驱体裂解体系中加入活性填料被认为是降低陶瓷孔隙率、抑制陶瓷材料出现裂纹的有效方法。目前的研究认为活性填料在先驱体裂解过程中,能与先驱体裂解产生的小分子化合物及保护气氛发生反应,生成新的陶瓷相。新生陶瓷相的作用主要体现在3个方面:(1)碳化物等新生相的体积增加可填补孔隙和裂解过程中的收缩,从而达到提高陶瓷产率、降低收缩率和孔隙率的目的。(2)原位生成的碳化物、氮化物等纳米粒子或微米级粒子与基体构成复相陶瓷,能提高基体的断裂韧性和强度。(3)碳化物等新生相能消耗先驱体转化过程中所生成的自由碳。
Greil和Erny等通过裂解含活性填料Ti、MoSi2的聚硅氧烷制备了复相陶瓷,并发现加热含Ti粉的聚硅氧烷时,400℃左右便有碳化钛TiC固熔体生成,温度超过800℃时,可获得含TiC的SiOC复相陶瓷材料,其弯曲强度可达到330MPa。陈少杰等研究了钛粉对聚硅氮烷裂解制备陶瓷材料的影响,发现钛粉可以有效提高先驱体的陶瓷产率。当钛粉和聚硅氮烷的质量比为3/10时,1300℃高温裂解获得的陶瓷产率为78。7%,比相同条件下裂解聚硅氮烷制备陶瓷时的产率提高了约40%,孔隙率和线收缩率最低,分别为4。9%和13%。朱云洲等研究发现在热裂解聚碳硅烷过程中Al粉能与裂解生成的含碳有机小分子发生化学反应,生成新的物相AlC,产生体积膨胀效应,热裂解陶瓷表现为小收缩、高产率,如在1000℃热裂解并保温1h,线收缩率为0。08%,陶瓷产率为99。68%。谢征芳等分别研究了活性填料Mo、Cr、W、Al、Ta对聚碳硅烷裂解制备陶瓷材料时陶瓷产率、孔隙率及收缩情况的影响,发现活性填料与裂解产生的小分子化合物反应,生成的金属碳化物会产生体积膨胀。体积膨胀一方面可以填充陶瓷材料的孔隙,增加陶瓷材料的致密度;另一方面可以抵消或抑制先驱体裂解后产生的体积收缩,使材料在裂解前后不发生体积变化,实现材料的净尺寸成型。
2 聚合物先驱体材料体系裂解制备陶瓷涂层
2。1 聚硅氧烷体系裂解制备陶瓷涂层
Gadow等将聚硅氧烷先驱体溶于有机溶剂中,然后涂覆于碳纤维上进行加热裂解和煅烧,发现碳纤维表面形成Si-OC陶瓷涂层。在500℃或更高温度下氧化,碳纤维试样的氧化稳定性取决于SiOC陶瓷涂层的化学成分以及涂层厚度。Torrey等用聚硅氧烷作先驱体、TiO2作活性剂,热裂解5h后在不锈钢表面生成厚度大约为18μm、密度为2。56g/cm3 的SiOC陶瓷涂层,该陶瓷涂层含有自由碳。陶瓷涂层与不锈钢界面存在一个扩散层,使陶瓷涂层与不锈钢具有很好的结合强度。Goerke等将聚硅氧烷先驱体制成溶液后喷涂到多孔材料和复杂形状材料的表面,在1000℃惰性环境热裂解,可获得厚度在0。2~3μm的非晶态SiOC陶瓷涂层,该陶瓷涂层大幅提高了基材的氧化稳定性。通过控制固化过程、聚合度大小以及过程中的其他参数,可获得高的陶瓷产率及均匀密度的涂层。Kaindl等采用Mo粉与聚硅氧烷共同裂解来制备陶瓷材料。Mo在裂解过程中反应生成Mo2C、Mo3Si、Mo5Si3等新相,产生的体积膨胀能有效降低陶瓷材料的孔隙率。Pivin等通过离子辐照聚硅氧烷制备出了SiOC陶瓷涂层,并发现辐照制备的陶瓷涂层中自由碳含量比热裂解方式制备的陶瓷涂层多,自由碳呈现出类金刚石形态(热裂解得到的自由碳呈类石墨形态),离子辐照获得的陶瓷涂层的硬度是热裂解的2~3倍。
2。2 聚硅氮烷体系裂解制备陶瓷涂层
Su等在600~1500℃之间热裂解聚硅基乙烯二胺,制得聚合物衍生的SiCN涂层,并将其用作锂电池的阳极。这种SiCN材料的组成可以从有机到无机,相结构可以从非晶态到晶态。在600~800℃热裂解可得到含有有机基团的SiCN材料,在1000~1300℃热裂解得到的SiCN 材料是非晶态的,并在SiCN网状结构中含有自由碳;而在1400~1500℃之间热裂解得到的SiCN材料含有碳化硅微晶,充放电容量与非晶态SiCN阳极相比低得多。Tsali等将聚(脲)甲基乙烯基硅氮烷制成的先驱体溶液涂覆在不同基材上(如硅、蓝宝石、氧化锆),形成交联的聚合物膜(350nm厚),在热恒压下或管式炉中、在氮气或氨气氛围中进行热裂解,制得防腐和抗氧化性能好的SiOCN 陶瓷薄膜。Gunthner等用聚硅氮烷作聚合物材料、氮化硼粒子作填料,制成抗氧化和抗腐蚀涂料;然后将该涂料涂覆于金属表面,干燥后在800℃空气中热处理,得到厚度为12μm的稠密且粘接性极好的SiNO/BN复相陶瓷涂层,该陶瓷涂层具有极好的抗氧化性能和耐腐蚀性能(见图4)。
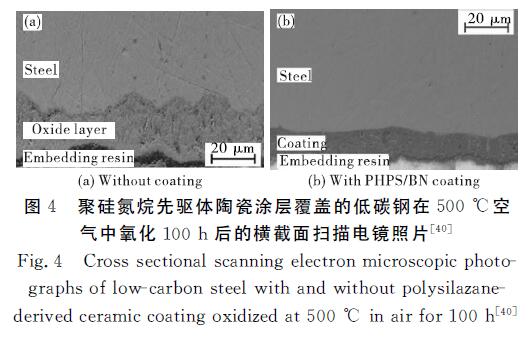
Sarkar等将液态聚硅氮烷与三仲丁氧基铝在160℃反应,合成了固态的聚铝硅氮烷,然后将聚铝硅氮烷与聚环氧乙烷以1∶0。0001的质量比溶于三氯甲烷溶液,并涂覆于碳纤维表面,干燥后经过热裂解可以得到表面光滑的SiCNO陶瓷涂层,其陶瓷产率为80%。Motz等将聚硅氮烷先驱体用金属钛有机金属化合物改性,再将该固体溶解制成涂料,将其刷涂或喷涂在金属表面,再经高温裂解,可获得与金属基材有很高结合强度的陶瓷涂层。陈少杰等将聚硅氮烷和钛粉涂覆在石墨表面,在N2气保护下1000℃ 裂解制备抗氧化陶瓷涂层,结果发现钛粉的添加量为10%~20%(质量分数)时,制备的氮化硅陶瓷涂层抗氧化性能最佳(见图5)。
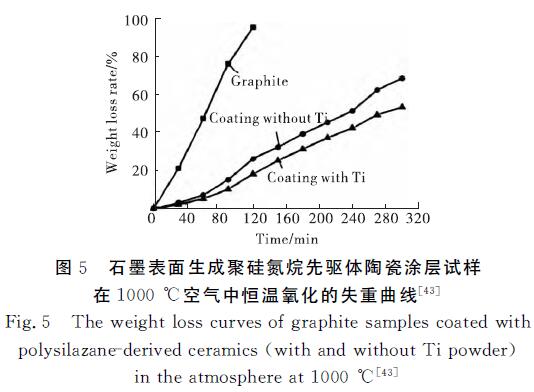
刘洪丽等将微米级的Si、MoSi2加入聚硅氮烷中,将制备的涂料均匀涂覆在石墨表面,并将其放入真空设备内加热裂解,获得涂层厚度约为30μm,表面较为平整、致密,与过渡层结合紧密的SiC陶瓷涂层。Tian等将聚硅氮烷、Al和Cr2O3混合后涂覆在304不锈钢表面,150℃热固化后分别在600℃和800℃空气环境下热裂解,获得了厚10~15μm、含SiO2/Al2O3和Cr2O3等的陶瓷涂层,该涂层与304不锈钢具有良好的结合强度,其中800℃热裂解制备的陶瓷涂层结合强度较600℃时的结合强度高。Hsien等通过在700℃热裂解聚硅氮烷,在AlN表面获得了非晶态的SiOC陶瓷涂层,SiOC陶瓷涂层不仅可以改善AlN粘结性能,而且可以改善AlN的热传导性能。
2。3 聚碳硅烷体系裂解制备陶瓷涂层
李春华等将聚碳硅烷涂覆在石墨基体表面,采用程序升温使裂解温度升至1000℃后保温2h,分析发现在石墨基体上形成了明显的β-SiC晶相;单次涂覆形成的SiC陶瓷涂层均匀、致密,但有少量的微裂纹和孔隙;微裂纹、孔隙和厚度可通过涂覆次数和涂层厚度的改变加以调节。肖平等采用聚碳硅烷先驱体,添加纳米级惰性填料SiC颗粒和微米级活性填料金属Al粉,在金属基体上制备出单层厚度可达50μm的致密SiC/Al2O3复相陶瓷涂层。复相陶瓷涂层中的SiC来自于先驱体热裂解转化的SiC和添加的纳米SiC颗粒,Al2O3来自于微米级金属Al粉的氧化。
3 展望
综上所述,先驱体转化陶瓷法在金属表面原位制备陶瓷涂层具有制备温度低,工艺简单,先驱体丰富,陶瓷涂层组成可设计,结构和性能可调控,成型和加工容易等优势,是一项很有前途的制备陶瓷涂层新技术。但该技术目前还存在孔隙、裂纹不容易主动控制,热裂解时间较长,不能满足人们大规模、高质量、结构可控的制备需求。因此,未来聚合物先驱体转化制备陶瓷涂层的研究应主要集中在以下几个方面。
(1)探索新的可控制备高质量陶瓷涂层的方法与技术。目前,聚合物先驱体转化法制备陶瓷涂层主要采用加热法,存在加热时间长,制备周期长等不足。随着技术发展,出现了很多新的加热技术,如微波加热、激光加热等。特别是激光具有能量密度高和集中、材料逐点加热和凝固速度快、易于控制等诸多优点,因此将激光应用于聚合物先驱体裂解制备陶瓷涂层,在非平衡态下获得高质量的陶瓷涂层,其制备方法、激光裂解机理等值得开展研究。
(2)研制高陶瓷产率的裂解材料体系,注重裂解材料体系的复合化发展。裂解材料体系陶瓷产率的高低与陶瓷涂层中孔隙和裂纹的多少直接相关,也与所制备的陶瓷涂层的性能直接相关,因此需要不断研制新型的高陶瓷产率的裂解材料体系。另外,在聚合物中引入金属元素以及不同类型聚合物的复合化也值得深入研究。
(3)不断完善裂解形成陶瓷涂层的机理。在陶瓷涂层中纳米晶β-SiC、非晶SiO2和自由碳的微结构、微尺度以及化学价态,非平衡态下新生成的金属碳化物相的组成和结构以及与纳米晶β-SiC和非晶SiO2间界面键合形式等问题都需进一步研究,通过建立裂解材料体系-裂解工艺-陶瓷涂层组成结构-陶瓷涂层性能之间的关系,获得裂解制备陶瓷涂层的可控工艺和技术。
免责声明:本网站所转载的文字、图片与视频资料版权归原创作者所有,如果涉及侵权,请第一时间联系本网删除。