泰坦尼克号为什么沉没?钢材竟然是致命缺陷
2018-11-15 13:43:55
作者:本网整理 来源:材料人
1912 年 4 月的一天,号称「永不沉没」的泰坦尼克号遭遇了一场旷世海难,轮船在航行时,和冰山发生了死亡之吻——船体右舷被海平面下的冰山体撕开一条口子,船的前部吃水线下铆钉断裂,货舱开始迅速渗入海水。
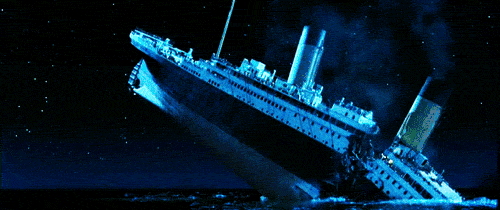
为什么“永不沉没的巨轮在撞上冰山3个小时后就沉没了”?
号称“永不沉没”的泰坦尼克号首航即沉没于冰海,成了20世纪令人难以释怀的悲惨海难。全英乃至全球都对此次海难表示无法接受,众多人士对此发表自己的看法,甚至连UFO都出现在公众的视线。但泰坦尼克号为何会如此迅速沉没依旧是一个未解的谜底。

泰坦尼克号残骸
自1985年开始,探险家们数次探潜到12612英尺(1英尺=0.3048m)深的海底研究这一沉船,找出遗物。在1995年2月,R Gannon在美国《科学大众》(popular science)杂志发表文章,他回答了这个困扰世人80多年的未解之谜——早年的泰坦尼克号采用了含硫高的钢板,韧性很差,特别是在低温呈现脆性。这就是导致“皇家邮轮”迅速沉没的症结。
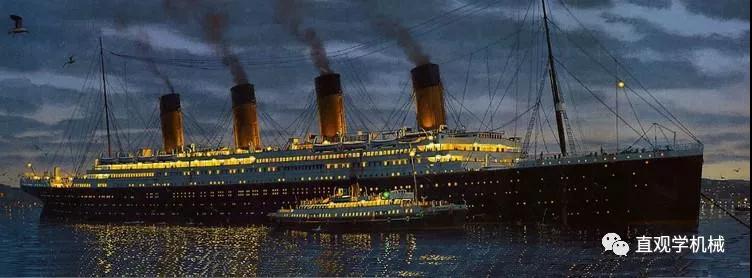
泰坦尼克号全船共分为16个水密舱,连接各舱的水密门可通过电开关统一关闭。泰坦尼克号良好的防水措施,使得它在任意4个水密舱进水的情况下都不会沉没。但实际上防水壁并没有穿过整个甲板,仅仅达到了E层甲板。 如此高配置的豪华邮轮确实是不应该沉没的,但是泰坦尼克号在水线上下的300英尺的船体由10张30英尺长的高含硫量脆性钢板焊接而成,长长的焊缝在冰水中因撞击冰山而裂开,脆性焊缝无异于一条300英尺长的大拉链,使船体产生很长的裂纹,海水大量涌入使船迅速沉没。
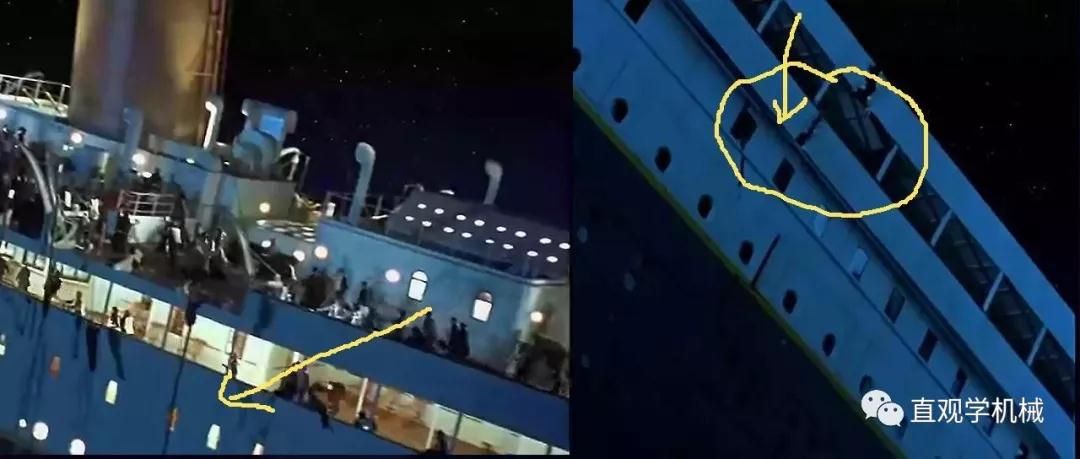
那么为什么高含硫量的钢板就导致了脆性呢?
首先,由于当时造船厂的生产技术还比较落后,在钢板制造过程中,生铁会因使用的燃料(含硫)而混入较多的硫,在固态下,硫在生铁中的溶解度极小,以FeS的形式存在钢中,而FeS的塑性较差,所以导致钢板的脆性较大,更严重的是,FeS与Fe可形成低熔点(985℃)的共晶体,分布在奥氏体的晶界上。
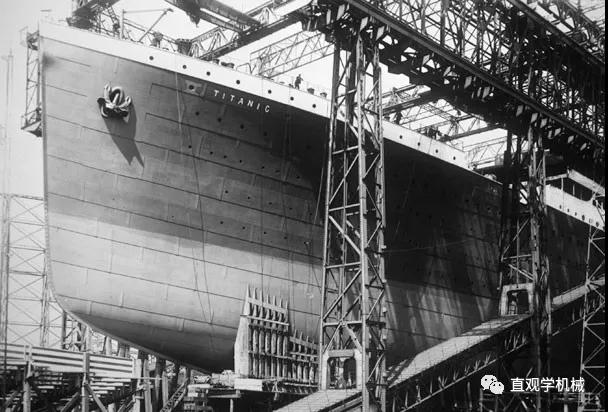
当钢加热到约1200℃进行热压力加工时,晶界上的共晶体已溶化,晶粒间结合被破坏,使钢材在加工过程中沿晶界开裂,这种现象称为热脆性。为了消除硫的有害作用,必须增加钢中的含锰量。因为造船工程师只考虑到要增加钢的强度。而没考虑增加其韧性,所以在制造船体的时候已经留下很大的隐患。
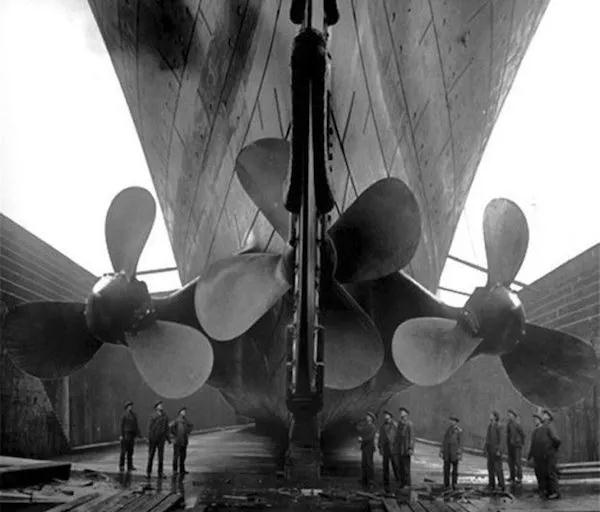
第二点,是泰坦尼克号航行的海域。泰坦尼克号沉没的海域是大西洋,当时的水温在-40℃~0℃,据后来的失效分析专家称:把残骸的金属碎片与如今的造船钢材作一对比试验,发现在“泰坦尼克号”沉没地点的水温中,如今的造船钢材在受到撞击时可弯成V形,而残骸上的钢材则因韧性不够而很快断裂。由此发现了泰坦尼克号所使用钢材的冷脆性,即在-40℃~0℃的温度下,钢材的力学行为由韧性变成脆性,从而导致灾难性的脆性断裂。而用现代技术炼的钢只有在-70℃~-60℃的温度下才会变脆。所以环境因素加上船体材料的致命缺陷导致了泰坦尼克号海难的发生。
更多关于材料方面、材料腐蚀控制、材料科普等方面的国内外最新动态,我们网站会不断更新。希望大家一直关注国家材料腐蚀与防护科学数据中心http://www.ecorr.org
免责声明:本网站所转载的文字、图片与视频资料版权归原创作者所有,如果涉及侵权,请第一时间联系本网删除。