海底“玩泥巴” 港珠澳大桥完成首个曲线段沉管预制
2016-05-06 10:47:20
作者:本网整理 来源:广州日报,中国交通新闻网
近日,经过中交岛隧建设者106天的持续奋战,港珠澳大桥首个曲线段沉管(E32)预制完成,为后续曲线沉管安装创造了有利条件。
港珠澳大桥是连接香港、珠海与澳门,集桥、岛、隧为一体的超级工程,它将成为世界上最长的跨海大桥,被英国《卫报》评为“新世界七大奇迹”。项目中,海上人工岛和海底沉管隧道是整个工程中实施难度最大的部分。其中,6公里的深埋沉管是我国建设的第一条外海沉管隧道,是目前世界上规模最大的公路沉管隧道和世界上唯一的深埋沉管隧道,是公认的“当今世界上最具挑战性的工程”。
“玩泥巴”玩到国内第一
港珠澳大桥海底隧道沉管最深埋在40多米的海底,浇筑沉管混凝土这种“泥巴”需要有足够的强度,确保沉管能够承受各种复杂荷载的作用;要有足够的寿命,保证120年不被海水中氯离子渗透腐蚀;要有优良的抗裂性能,确保沉管在海底40余米水深条件下正常工作。能够将“泥巴”玩到这种程度的人寥寥无几,李超却带领他的团队港珠澳大桥岛隧工程沉管预制厂试验室做到了。港珠澳大桥岛隧工程项目总经理、总工程师林鸣介绍说:“我们的沉管混凝土可以在水深40米以下实现自防水,已经建成的4365米隧道滴水不漏,达到了国内第一,居于世界领先水平。”
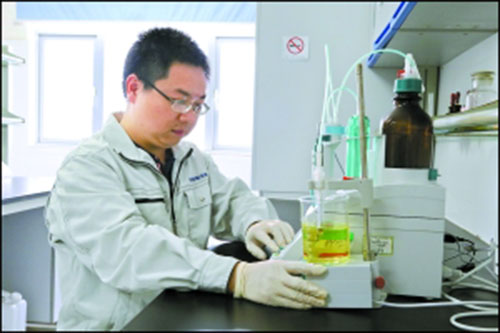
李超在工作
一连“玩”上30小时以上是家常便饭
2月21日凌晨3时,沉管混凝土生产浇筑正热火朝天地进行着。从砂石仓取样检测回来的李超推开4号搅拌站门,屋内的热风迎面扑来,让人发困,他放下对讲机到门外用冷水洗了把脸,回来在工具箱上坐下,因为要盯着E33-S2节段混凝土生产浇筑,李超生怕有任何闪失,一个通宵,盹也不敢打一个。
“4号站用到新砂了,试验室注意!”桌上的对讲机响起。
李超一下站起来,揉揉发红的眼,问搅拌站操作员:“用到新砂了?”
“是啊!”
仔细看了一下控制屏幕的电流曲线,李超说:“新砂含水率4.5%,我刚测的,你按这个调一下,下一盘还要先留10公斤水。”说完之后,掏出笔在记录本上写下,拿起对讲机呼叫:“各位值班员请注意,新砂含水率增大到4.5%了,用到新砂要及时调整。”这是混凝土生产中最常见的工作状态。
李超说,混凝土生产质量控制水平直接决定了沉管隧道的结构安全与使用寿命,是港珠澳大桥预制沉管生产质量控制的关键。通过管控搅拌站实现对现场混凝土生产质量的精确控制,不仅决定着沉管整体质量,也是岛隧工程沉管预制厂最终工作成果的重要体现。
沉管预制持续4年多,仅仅浇筑沉管就需254次,每次都要连续工作30个小时以上,每次都容不得任何差错,这不仅仅是对技术要求精益求精,对人体力上也是极大的挑战。
通宵添缓凝成分 一辈子难忘
港珠澳大桥岛隧工程沉管还剩下三个管节未预制,预制施工已接近尾声,问起李超在施工过程中最深刻的事情,他说:“第一节沉管节段浇筑前,连夜往减水剂储罐里面加缓凝成分,一辈子都忘不了!”
港珠澳大桥沉管首次采用全断面浇筑工艺,混凝土凝结时间怎么控制,没有人能给出确切的答案。时间回到2012年8月,第一节沉管节段浇筑的前一天,最终的试验数据、技术人员的意见、业内专家的建议都已汇总,需要最后的决策了。试验室主任张宝兰再次组织召开讨论会,最终明确了混凝土可塑性、凝结时间控制指标,缓凝成分及添加量。
预制厂搅拌站的四个储罐中存放有40吨减水剂,每吨减水剂还需要添加10公斤缓凝成分,需要一个个罐的补加。这么大量的工作,还要求必须精准,不能有差错。会议结束已经到了深夜11时30分,试验室全体人员都还在等着,要立即行动起来。李超负责缓凝成分的补加工作,他将大家组织起来进行分工,进行缓凝成分称量、校对、成分搭配、分装、投料、搅拌、检测,直到最后一包缓凝成分搅拌均匀,然后从每个储罐抽样检测固含量偏差,忙完这一切已是次日凌晨5时了。
回忆起当时的情形,李超笑着说:“加完就松了口气,人都快瘫了。后来现场情况和试验结果非常吻合,我们就这样一步步走过来了。”
免责声明:本网站所转载的文字、图片与视频资料版权归原创作者所有,如果涉及侵权,请第一时间联系本网删除。