文 | 胡晓轩 王炳英 易小涛 蒋文春 中国石油大学 ( 华东 ) 机电工程学院 化学工程学院
本文主要介绍了Incoloy825/X65双金属复合管焊接接头随机熔合线与外延熔合线处的金相组织,元素扩散及硬度分布情况,并探究了Incoloy825/X65双金属复合管焊接接头在饱和湿硫化氢环境中的应力腐蚀开裂行为。
序言
在油气输送管线的服役过程中,应力腐蚀开裂一直被视为严重的安全问题,尤其是近年来伴随着酸性油气田的开发,油气输送管线面临着越来越苛刻的腐蚀环境。双金属复合管具有良好的耐蚀性和较低的成本因而得到了广泛的应用。然而,如何保证复合管在焊接后仍保持良好的耐蚀性是工程应用中面临的严峻问题。
Incoloy825/X65 双金属复合管焊接接头的熔合线由两部分组成: Incoloy825 与焊缝金属形成的覆层熔合线以及 X65 与焊缝金属形成的基层熔合线。覆层金属与焊缝金属均为镍基合金,物理化学性能相差不大且具有良好的耐蚀性,但基层焊缝处存在异种金属的连接,成为输送酸性介质管道的薄弱环节。之前很多的研究结果表明异种钢焊接接头的熔合区存在复杂的微观结构和较大的化学成分梯度会导致复杂的裂纹扩展行为。HOU 等人指出异种钢焊接接头中平行于熔合线的 Type- Ⅱ晶界因其高角度特征,会提高构件的 SCC 敏感性[1] ;Nelson 等人指出异种钢焊接中特有的Type- Ⅱ晶界提供了一种可能的裂纹扩展路径,并且因其高角度特征,具有很高的应力腐蚀敏感性,极易发生开裂[2] ;1999 年在日本 T 核电站以 Inconel182 为填充金属的压力容器的焊缝熔合线处共发现了 228 条应力腐蚀裂纹,通过观察发现裂纹都终止于 Inconel 钢和低合金钢的界面上[3] ;另外,王伟等人提出多层多道焊的熔合线分为随机熔合线与外延熔合线[4] ,因二者所处位置不同,性能也存在较大差异。因此十分有必要对基层熔合线处的物理化学性能及耐蚀性进行探究。
在本研究中,利用光学显微镜、显微硬度计及电子探针等手段,比较随机熔合线和外延熔合线在微观组织、显微硬度及元素扩散方面的差别,并采用带缝隙的弯曲横梁 (creviced bendbeam ,CBB) 实验探究 Incoloy825/X65双金属复合管焊接接头在饱和湿硫化氢环境下的应力腐蚀开裂机理,为双金属管焊接接头的断裂评价提供理论支持。
实验材料及方法
实验材料选用 Incoloy825/X65 双金属复合管焊接接头,坡口角度分别为45 °和20 °, 试 样 尺 寸 为40mm×25mm×10mm,制成金相样品后在光学显微镜下观察随机熔合线与外延熔合线的金相组织形貌。采用电子探针分别垂直于随机熔合线与外延熔合线进行线扫描和点扫描,分析熔合线处的元素扩散情况。显微硬度的测量在 MH-3型显微硬度计上进行,所加载荷为 2N,载荷持续时间为 10s。
传统的 CBB 实验,样品放置 980 小时都不产生SCC裂纹。因此在本试验中,为了增加裂纹在焊缝中萌生的可能性并缩短裂纹孕育的周期,在试样焊缝侧的表面开 V 型切口并施加一个小应变。将制取的 H 2 S 气体通入盛放试样的广口瓶中,模拟双金属复合管焊接接头在饱和湿 H 2 S 环境下的应力腐蚀开裂行为,实验周期为720h。实验结束后将试样取出,放在丙酮溶液中将腐蚀产物清洗干净,并在试样厚度方向将不同坡口的试样分别均匀的切成三份,用来观察裂纹在试样内部的扩展情况。CBB 实验样品的取样位置及尺寸如图 2-1 所示,45°坡口试样和 20°坡口试样各取两个:
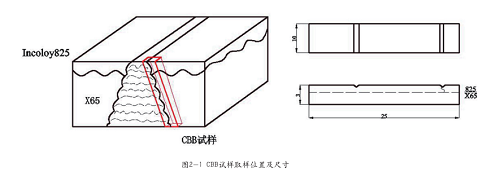
实验结果及分析
1 随机熔合线与外延熔合线的组织形貌
多层多道焊焊接接头的熔合线有两种存在形式:随机熔合线和外延熔合线,二者交替排列并出现在熔合线的特定区域。通过金相观察可以看出,随机熔合线主要分布在两焊道连接的边界拐角处,含量较低,约占整个熔合线总长度的 15% 左右,外延熔合线则位于焊道的中部,比较平直,随机熔合线与外延熔合线的分布如图 3-1 所示。
观察图 3-2(a)(b)可以发现,随机熔合线处的组织以枝晶结构为主,晶粒较为粗大,外延熔合线处的晶粒与之相比较为细小,并以枝晶的方式垂直边界生长。晶粒大小存在差异的主要原因是:随机熔合线与外延熔合线所处位置不同,接受的焊接热循环也不同。随机熔合线位于两焊道连接处,接受了两次加热,吸收了更多的能量从而促进了晶粒的长大;而外延熔合线则位于焊道中部,只经历了一次加热,吸收的能量相对较少。我们已知随着晶粒的长大,晶界的数量减少,单位长度晶界上的杂质增多,由此我们可以推测随机熔合线与外延熔合线相比,随机熔合线对应力腐蚀开裂的敏感性更高,有利于裂纹的扩展。
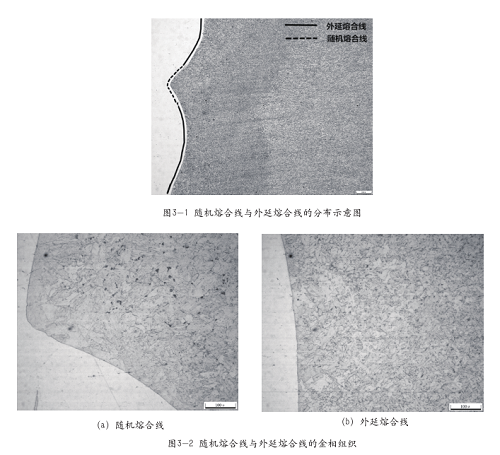
2元素扩散
使用电子探针对随机熔合线和外延熔合线处的元素扩散进行分析。为了提高实验的精确度,分别垂直于随机熔合线和外延熔合线,以 50 微米为单位,分别在熔合线两侧 200 微米的范围内进行点扫描,结果如图 3-3 所示。由图可知,随机熔合线和外延熔合线两侧均发生了合金元素的扩散,扩散距离约为 50微米,且元素扩散的趋势相同,Fe 元素由 X65 一侧向焊缝扩散,Cr、Mo、Ni 由焊缝向 X65 中扩散。值得一提的是,随机熔合线处的元素扩散范围关于熔合线对称,元素扩散梯度大,但因其所占熔合线长度比例较低,扩散元素的总含量仍较少;而外延熔合线中的元素扩散主要集中在焊缝一侧,元素扩散总量较高。 产生这种现象的主要原因是:焊缝金属为主要的半熔融金属,在焊接热循环过程中外延熔合线处吸收的热量较少,所以成分扩散主要发生在焊缝金属一侧。
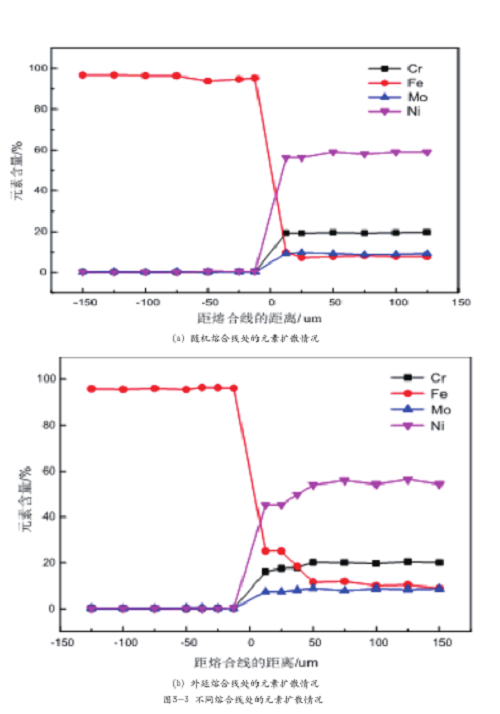
显微硬度
为了进一步研究熔合线两侧元素扩散造成的影响,分别垂直于随机熔合线和外延熔合线,以 50 微米为一个测量单位进行显微硬度的测量,测量结果如图 3-4 所示:
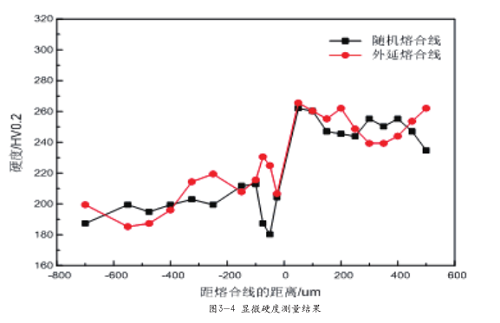
由测量结果可知,焊缝侧的硬度均高于基材 X65,满足了双金属复合管焊接接头对强度的要求。显微硬度从热影响区到母材逐渐呈下降趋势,并逐渐接近于母材的硬度,热影响区的硬度波动较大且硬度均高于母材。然而,外延熔合线靠近焊缝约 100 微米范围内的硬度变化远大于随机熔合线处,可能的原因是主要存在于外延熔合线中的 Type- Ⅱ晶界增加了该处的硬度。靠近熔合线的 X65侧硬度也有所上升,该处硬度增加的原因可能是由于元素扩散,该侧的合金元素含量升高,冷却曲线向右移动,增加了形成马氏体组织的可能性,但其扩散距离小,硬度增加的范围有限。因此影响双金属复合管焊接接头硬度分布的主要因素是熔合线两侧的晶格类型、元素扩散和焊接热循环造成热影响区的分布。
CBB 实验结果分析
检查所有带 V 形切口的 CBB 试样可以观察到 SCC 裂纹的萌生及扩展。观察图 3-5 可以看出,两个试样中的裂纹均起始于 V 形切口根部,由焊缝向 X65 扩展,到达熔合线后发生球形钝化,裂纹暂时停止继续向前扩展,另外在界面处观察到了氧化物。
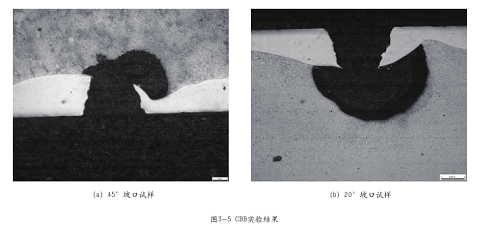
综合 CBB 实验结果可以得出,裂纹到达熔合线后成分发生了突变,Fe 元素的含量急剧升高,裂纹尖端与开口处存在腐蚀电位差,导致 X65 受到了急剧的氧化,从而在熔合线处发生球形钝化,钝化边缘比较平滑,应力集中程度小,裂纹继续向 X65 中扩展的动力减小,即熔合线对应力腐蚀裂纹的扩展起到了阻碍作用。由于裂纹再活化所需时间较长,因此在本次实验中没有观察到裂纹的再活化现象。
除了裂纹在熔合线处产生球形钝化外,还发现不同坡口试样中的球形钝化均向随机熔合线偏转。根据对熔合线的性能分析可知,随机熔合线吸收的能量较多,晶粒相对比较粗大,单位面积内的晶界数量较少。虽然随机熔合线两侧的元素扩散量大,但扩散距离小,所以X65 侧的 Fe 元素含量相对于外延熔合线来说仍较高。因此随机熔合线与外延熔合线相比,对硫化氢应力腐蚀的敏感性更高,从而诱导裂纹向该处扩展。
结论
(1)Incoloy825/X65 双金属复合管焊接接头基层焊缝的熔合线分为随机熔合线与外延熔合线两种存在形式。随机熔合线位于两焊道连接处,晶粒较为粗大,元素扩散梯度大,且元素的扩散范围关于熔合线对称分布;外延熔合线位于焊道中部,晶粒较为细小,元素扩散量小,主要集中于焊缝一侧。
(2) 饱 和 湿 硫 化 氢 环 境 下Incoloy825/X65 双金属复合管焊接接头的 CBB 试验结果表明,应力腐蚀裂纹到达熔合线后会在基材 X65 一侧发生球形钝化,减缓裂纹的扩展速率。
(3)应力腐蚀裂纹到达熔合线后产生的球形钝化向随机熔合线偏转,说明该处具有更高的应力腐蚀敏感性。