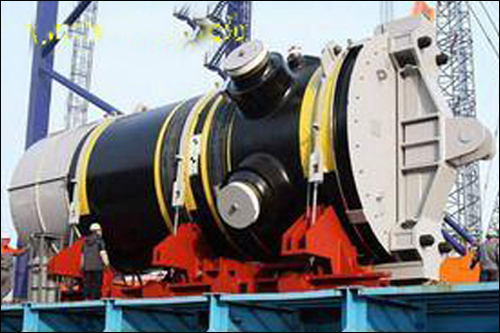
核反应堆设备
AP1000正常余热排出系统RNS执行停堆工况下低温超压保护、将堆芯衰变热带出,冷却堆芯,事故工况后向反应堆冷却剂系统补水以及冷却安全壳内置换料水箱等[1].正常余热排出泵管嘴带ERNiCr3镍基堆焊层与Type304L奥氏体不锈钢管道焊接,如图1所示,采用ER308L焊丝,GTAW焊打底焊过程中发现焊缝表面产生裂纹,且多处存在类似情况.由于缺陷的存在对核电站的安全运行造成极大的隐患,所以分析焊接裂纹的产生原因,采用合理正确的预防措施,对确保核电站质量和运行有重要意义.

1 裂纹产生原因分析
由试验结果验证:由于铁素体一方面打乱单一奥氏体柱状晶的结晶方向性,细化晶粒.由于铁素体铬含量高于奥氏体,而且铬在铁素体中的扩散比在奥氏体中快得多,所以可以帮助克服任何贫铬问题.M23C6碳化物倾向于在凹凸不平的铁素体-奥氏体边界析出,而不是在通常比较直的奥氏体-奥氏体边界析出.所以这些因素都大大限制了在含有铁素体的奥氏体不锈钢焊缝金属的敏化.
S、P低熔共晶的存在扩大凝固温度范围,当焊接过程中大部分晶粒边界仍然处于液态,增加了热裂纹的敏感性.而铁素体存在另一方面可以破坏焊缝结晶时低熔液态薄膜的连续性,且铁素体对硫、磷等杂质有较高的溶解度,这样以铁素体为初始相的凝固过程中就能够限制这些杂质元素在枝晶间的偏聚.
出现奥氏体+铁素体组织,产生凹凸不平的晶界而改变晶界浸润性质,液体薄膜很难浸润该边界,且裂纹一旦起裂,很难在这个凹凸不平的边界上扩展.
纯奥氏体组织晶界平直,低熔共晶液态薄膜容易浸润该晶界,抗裂性差.图2为不含铁素体和含有铁素体在奥氏体基体分布图。
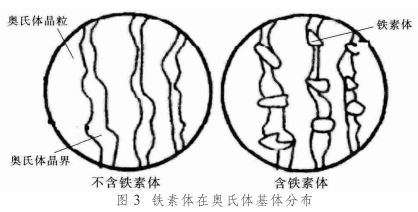
图2 不含铁素体和含有铁素体在奥氏体基体分布图
打底焊焊道的表面为凹形,凹形表面受到焊趾和焊根的拉应力作用,同时奥氏体不锈钢导热系数小,线膨胀系数大,在焊接局部加热和冷却条件下,接头在冷却过程中形成大的拉应力.
采用ER308L焊丝焊接镍基合金与304L不锈钢焊缝金属以A模式凝固时为全奥氏体(不含铁素体),此时热裂纹最为敏感,分布在晶界的S、P低熔共晶液态薄膜与拉应力共同作用下产生了热裂纹.
2 改善焊缝腐蚀和抗热裂纹措施
为了提高焊缝耐腐蚀性和抗热裂纹性能,焊丝改为ERNiCrFe3,提高了焊缝镍含量,提高晶粒整体电极电位和耐腐蚀性.
焊接顺序进行调整,正式焊接之前采用ERNiCrFe3镍基焊丝GTAW焊接对Type304L坡口进行堆焊,小电流、低热输入堆焊可以减少Type304L稀释率,同时可以较少整体热输入和拘束度而使晶粒边界裂纹减到最少,同时降低结晶凝固时的应变量,有利于减少粗大枝晶的形成.
焊缝表面采用凸形表面,由于根部收缩将对凸形表面产生压缩作用从而抵消焊趾拉应力,从而最终减小焊缝表面拉应力作用,如图4(b)所示,同时需要填满弧坑[4].
3 结论
(1)采用ER308焊丝GTAW焊接带镍基堆焊层管嘴与Type304L不锈钢管,焊接过程中产生热裂纹的原因为焊缝中无铁素体,奥氏体晶粒间液态薄膜与拉应力共同作用下产生.
(2)采用ERNiCrFe3焊丝,焊接前采用小电流对Type304L不锈钢管道侧坡口侧进行堆焊,正式焊接采用小线能量,凸形焊缝表面,填满弧坑解决焊缝热裂纹及耐腐蚀性下降问题.
参考文献:
[1]孙汉虹.三代核电技术AP1000[M].北京:中国电力出版社,2010.
[2]SindoKou.WeldingMetallurgy[M].Wisconisin:AjohnWiley&Sons,INC.Publication,2003.
[3]满达虎.奥氏体不锈钢焊接热裂纹的成因及防止对策[J].热加工工艺,2014,43(11):181-184.
[4]JohnCLippold,DamianJKotecki.不锈钢焊接冶金学及焊接性[M].北京:机械工业出版社,2008.