新技术!用 (Ti, Nb)C 增强镍基复合涂层提高钢材抗磨性能
2016-07-01 13:15:03
作者:本网整理 来源:行业技术
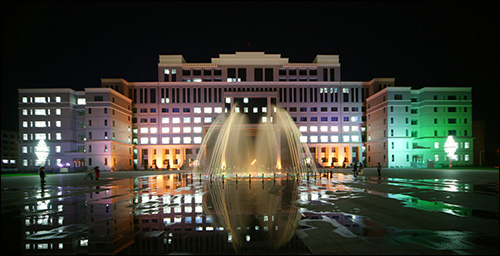
通过熔覆技术在廉价材料表面制备耐磨和耐蚀涂层具有重要的实用价值。黑龙江科技大学近期报道了以Ti、C、Nb粉和Ni60A合金粉末为原料,采用氩弧熔覆技术在16Mn钢基材表面制备(Ti,Nb)C颗粒增强Ni60A复合涂层的工作,明显提高了钢材的耐磨性能。常用的表面熔覆技术有激光熔覆、等离子熔覆、堆焊、热喷涂、感应熔覆和钨极氩弧熔覆等,其中氩弧熔覆热量集中,在熔覆的整个过程中,电极和电弧及金属粉末都处在氩气的保护之中,加热、冷却过程中无氧化、烧损现象;而且可实现手工操作,灵活性高,可对形状复杂的基件进行熔覆。他们以热轧态16Mn钢作为基体材料,表面除油去锈。以C、Ti、Nb和Ni60A合金粉末为原料,粉末的平均粒度为40~45μm。首先按照3%C-10%Ti-3%Nb-84%Ni60A的质量配比称量原料粉末,在研磨罐中混合均匀,然后采用普通胶水作为粘结剂,将混合粉末调成糊状,涂覆在16Mn钢表面,涂层厚度约为1.0~1.5mm,烘干后,通过氩弧熔覆获得原位自生(Ti,Nb)C颗粒增强镍基复合涂层(即C-Ti-Nb-Ni60A涂层)。
对熔覆涂层的组织检测表明:C-Ti-Nb-Ni60A复合涂层与基体间呈冶金结合,界面间无气孔和裂纹;复合涂层由γ-Ni,TiC和Cr23C6组成。TiC和(Ti,Nb)C颗粒在涂层厚度方向具有明显的梯度分布特征,在表层TiC和(Ti,Nb)C的体积分数较大;从涂层的底部到表面,由单个细小颗粒逐步演化成多个颗粒的团絮状。其主要形成原因为熔池的快速流动及其速度场的不均匀性加速陶瓷颗粒上浮,导致涂层凝固后出现颗粒梯度分布的特征。在熔覆层里层,TiC和(Ti,Nb)C颗粒分布较少,颗粒相主要分布在晶界处;熔覆层中间部位和表面,TiC和(Ti,Nb)C颗粒以花瓣状形态存在,尺寸约为2μm左右。
TiC颗粒具有硬度、模量和抗弯强度高等特点;原位自生TiC增强相具有热力学稳定、尺寸细小、分布均匀、界面洁净并与基体结合良好的特点。由于在复合涂层中加入了Nb,故生成(Ti,Nb)C颗粒增强Ni基复合涂层。
硬度测试表明,C-Ti-Nb-Ni复合涂层的显微硬度较基体提高近5倍,200N载荷下,C-Ti-Nb-Ni60A复合涂层的耐磨性能较基体16Mn钢提高6倍。对磨损表面的扫描电镜观察表明,16Mn钢磨损表面塑性变形严重,既有很深的犁沟,又发生严重粘着,表面布满块状磨屑脱落的痕迹和许多即将脱落的磨屑,说明16Mn钢表面发生了严重的磨粒磨损和粘着磨损;而Ti-C-Nb-Ni复合涂层的磨损表面相对较光滑。原因是Ti-C-Nb-Ni复合涂层中的耐磨硬质相(Ti,Nb)C颗粒在摩擦过程中对位错的运动起阻碍和钉扎作用,使得摩擦过程中需要更大的摩擦力和更多的摩擦功,因此,相同载荷条件下熔覆层的磨损量大大减小。由于熔覆层具有很高的硬度,对磨环难以有效压入涂层产生犁削磨损,只能依靠轻微擦划而缓慢地磨损涂层,因而涂层的磨损面较光滑,整个磨损表面如同经细的水磨砂纸打磨一样,看不到明显的磨沟,只有大量细小的擦痕。
免责声明:本网站所转载的文字、图片与视频资料版权归原创作者所有,如果涉及侵权,请第一时间联系本网删除。