采用有机涂层对金属构件进行保护是最常用且有效的防腐蚀手段之一。在严酷的海洋腐蚀环境中,往往使用双组分重防腐涂料,并采用多种涂层配套施工,涂层体系一般由底漆、中间漆、面漆三部分组成。底漆通常与基材有很好的粘接力并具有良好的耐腐蚀性能;中间漆可增加涂层厚度,增强整个涂层体系的屏蔽性能,也起到承上启下的作用;面漆通常具有装饰性、耐候性,并能防止环境介质的渗透破坏。
电化学交流阻抗技术(EIS)是目前研究涂层性能劣化以及涂层下金属腐蚀的重要方法之一。通过对阻抗数据进行解析,可以得到许多与涂层失效以及基体金属腐蚀有关的电化学参数。前人多利用EIS研究不同涂层体系在腐蚀环境中的失效过程和机理[1-4],但关于涂层配套体系中底漆、中间漆与面漆在服役过程中的阻抗变化的对比研究却很少。本研究采用由环氧富锌底漆、环氧云铁中间漆和氟碳面漆3种涂料制备而成的单层、双层及三层涂层体系,测试这3种涂层/碳钢试样在3.5%氯化钠溶液中浸泡过程的EIS谱图,通过分析与比较电化学参数,研究底漆、中间漆和面漆在整个涂层体系性能劣化过程中的主要作用。
1、实验材料和方法
1.1材料及试样制备
涂料为石家庄金鱼涂料厂生产的801环氧富锌底漆、701-2环氧云母氧化铁中间漆和SF-M300氟碳面漆,均为双组分。基材为Q235碳钢,试样尺寸为40mm×75mm×1mm,用120#水砂纸打磨后用丙酮清除表面油污。依据表1,制备3种配套涂层体系,底漆、中间漆和面漆依次为环氧富锌、环氧云铁和氟碳3种涂料,每种涂料涂刷1道,涂刷间隔24h,涂刷后室温固化1周。用TT220数字式覆层磁性测厚仪测量涂层厚度。
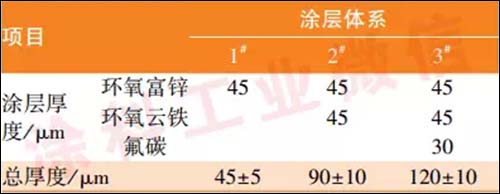
表1 3种配套涂层体系及其厚度
1.2电化学交流阻抗测试
将制备的3种涂层/碳钢试样分别浸泡于3.5%的NaCl溶液中,定期取出进行交流阻抗测试。测试仪器为PARSTAT2273电化学测试系统,交流正弦信号幅值10mV,频率范围105~10-2Hz。采用传统的三电极体系,参比电极为饱和甘汞电极(SCE),辅助电极为铂电极,工作电极为碳钢/涂层试样,研究面积12.5cm2。在开路电位下测试,室温下进行。采用ZSimpWin软件进行数据拟合。
2、结果与讨论
2.13种涂层体系的电化学阻抗谱
图1为3种涂层体系在3.5%NaCl溶液中浸泡2h的交流阻抗谱。
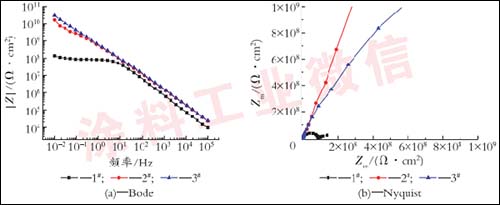
图1.3种涂层体系在3.5%NaCl溶液中浸泡2h的EIS谱图
由图1可以看出,2#试样和3#试样的Bode图都表现为斜率近似为-1的一条直线,低频阻抗|Z|0.01Hz均在1010Ω·cm2以上,并且两者相差不大;Nyquist图中仅出现1个时间常数,表明在浸泡初期,涂层相当于一层电阻很大的隔绝层,金属基体得到很好的保护,面漆在浸泡初期作用不是很明显。只涂刷富锌底漆的1#试样阻抗|Z|0.01Hz接近108Ω·cm2,比2#和3#低2个数量级,Bode图的中低频区出现明显的平台,Nyquist图中呈现2个时间常数的特征,说明电解质溶液很快到达锌粉与有机层界面,引起锌的腐蚀反应。
随着浸泡时间的延长,阻抗谱发生了明显的变化,图2为各试样浸泡30d后测得的EIS谱图。
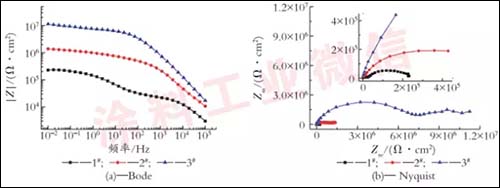
图2.3种涂层体系在3.5%NaCl溶液中浸泡30d的EIS谱图
由图2可以看出,3种涂层的低频阻抗|Z|0.01Hz均比浸泡初始大幅下降,分别为1.1×107Ω·cm2、1.3×106Ω·cm2和2.2×105Ω·cm2,依次减小1个数量级。2#和3#涂层的Nyquist图出现了第2个时间常数,说明电解质溶液渗入,涂层防护性能降低,面漆在浸泡中后期的防护作用明显显现。1#涂层Bode图在中频和低频区出现2个平台,分别对应于具有不同时间常数的2个过程,说明此时电偶作用减弱,锌腐蚀产物累积造成的屏蔽作用增强,电解质溶液己经渗透到涂层/基材界面,在界面区形成了腐蚀反应的微电池,此时涂层对基体已经失去保护性能。
低频阻抗|Z|0.01Hz可用来评价涂层防护性能,图3是3种涂层体系的|Z|0.01Hz随浸泡时间的变化。
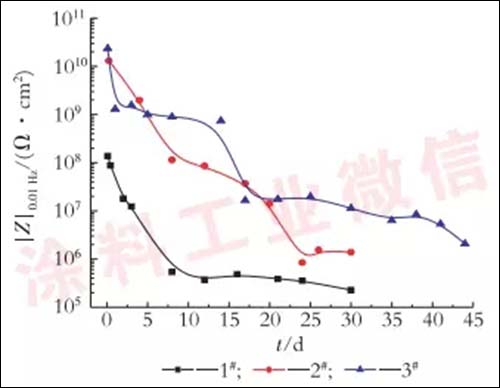
图3.3种涂层体系的低频阻抗|Z|0.01Hz随浸泡时间的变化
由图3可以看出,浸泡时间延长,各涂层的|Z|0.01Hz均下降,由高到低依次为:三涂层>两涂层>单涂层。其中,环氧富锌单涂层的阻抗初始值最低、下降最快,总体变化可分为2个阶段:0~10d,阻抗快速降低,由108Ω·cm2降至5×105Ω·cm2,此为第1阶段;第2阶段阻抗变化则趋于平稳。Vilche等研究发现,富锌涂层在模拟海水中浸泡1h,锌粉表面就有腐蚀产物形成,在浸泡1h~6d期间锌腐蚀产物逐渐增多,时间再延长则变化不大。因此,阻抗快速下降是源于涂层中锌粉不断腐蚀,当全部锌粉反应完毕后阻抗变化进入平缓期,此时电解液也到达基体表面,碳钢发生腐蚀。
双涂层的低频阻抗呈3个阶段的变化:0~8d为第1阶段,阻抗由初始的1010Ω·cm2快速降低至108Ω·cm2,接近1#富锌涂层的初始阻抗;第2阶段,阻抗的下降速率略微降低;第3阶段,25d后趋于平缓,达106Ω·cm2。比较单涂层和双涂层的阻抗变化可以看出,环氧云铁中间漆有效阻止了涂层对电解液的渗透,延长了介质的渗透时间,显著提高总阻抗,第2阶段可能是介质到达两层涂层的界面处,底漆中的锌粉发生腐蚀而发挥阴极保护作用的阶段。三涂层低频阻抗总体呈现4个阶段的变化:0~2d,阻抗快速下降1个数量级,可能是氟碳面漆快速吸水的过程;2~12d,阻抗下降变缓,可能是面漆吸水接近饱和;12~18d,阻抗再次快速下降,可能是中间漆吸水的过程;18d后,阻抗逐渐趋于平稳,可能是底漆开始发挥作用。比较三涂层和双涂层的阻抗变化曲线可以看出,在浸泡刚开始氟碳面漆的作用似乎不太明显,在浸泡中、后期的防护作用显现,提高了体系的总阻抗。
2.23种涂层体系吸水率和孔隙率的变化
涂层电阻Rc可反映涂层内部的微孔性质和涂层的屏蔽性能,涂层电容Cc反映涂层的水渗透性能。一般有机涂层干膜的介电常数远小于水的介电常数,因此涂层吸水后介电常数将增大,引起涂层电容增大。在浸泡过程中,有机涂层的分子链发生断裂,导致涂层表面粗糙度不断增大,也使涂层孔隙率不断增加。本研究分别对3种涂层体系浸泡不同时间的阻抗数据进行解析(等效电路如图4所示[5]),得到涂层电容Cc和涂层电阻Rc,然后分别代入式(1)和式(2)计算涂层吸水率及孔隙率。
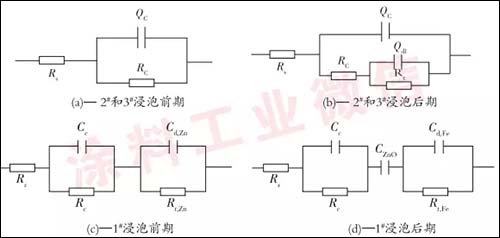
图4 等效电路模型
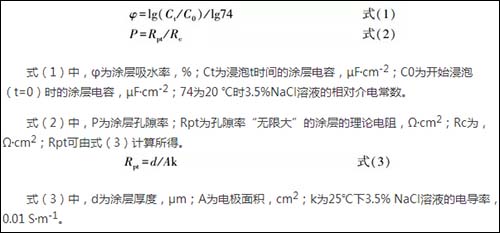
图5为3种涂层体系吸水率和孔隙率随浸泡时间的变化。
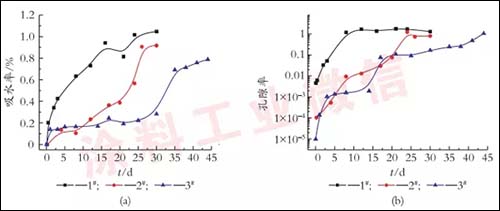
图5.3种涂层体系的吸水率和孔隙率随浸泡时间的变化
从图5(a)可以看出,1#试样的涂层吸水率增长最快,这是因为富锌涂层中大量的锌粒分布使涂层中存在许多孔隙,为电解质向涂层内部的渗入提供了很多通道;另外,浸泡初期涂层中的锌粒就与介质发生反应,形成向涂层内部延伸的缝隙或孔洞,也会加快水分子的渗透过程;随着浸泡时间的延长,锌粉腐蚀速率逐渐减小,锌腐蚀产物堵塞孔隙,因此吸水速率在后期又略有降低,最后水分子到达涂层/金属界面。2#和3#涂层吸水率比1#显著降低,变化趋势大致都呈现“三段增长”的特点:浸泡初期由于水分子的快速渗透涂层吸水率较快增加;当吸水逐渐接近饱和,增长速率趋缓;最后涂层吸水率再次迅速增长,是因为基体发生腐蚀反应[10],涂层的粘接力下降。比较3条曲线可以看出,富锌底漆上涂刷环氧云铁中间漆后(即试样2#),涂层吸水率大幅降低,这可能是因为云母氧化铁使水分子在中间漆中的渗透路径有所增长;3#的初始值比2#略高,但是在10~30d之间的较长浸泡时间内,三涂层体系的吸水率一直保持在很低的水平(<0.3%),说明三涂层体系对于水和离子渗透起到了很有效的屏蔽作用,显著延迟了电解液到达中间漆和底漆以至基体的时间。
从图5(b)可以看出,各试样的孔隙率均随着时间的延长而增大,总体上1#>2#>3#。浸泡初期各试样孔隙率的增长都较迅速,其中2#孔隙率的增长相对慢些,可能是由于环氧云铁涂层中密布了平行排列的云母氧化铁,水分子只能沿着云母氧化铁与树脂中间的孔隙缓慢曲折渗透,致使孔隙率增长缓慢。1#孔隙率在浸泡10d左右趋于稳定,可能是由于底漆的“自修复能力”,即锌腐蚀产物堵塞涂层的孔隙,所致。三涂层体系在浸泡中后期孔隙率比两涂层体系的更低。
图6是3种涂层体系在3.5%NaCl溶液中浸泡30d的表面情况。
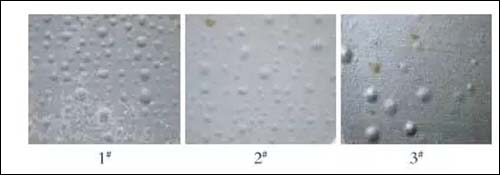
图6.3种涂层体系在3.5%NaCl溶液中浸泡30d的表面照片(放大倍数为6倍)
图6中各涂层表面均出现了鼓包,其中1#涂层的鼓包最多,2#次之,3#最少。鼓泡是涂层保护性能严重下降的初始现象之一,在此局部区域涂层与基体的粘接力丧失,水发生积累并且腐蚀开始发生。图6也显示,3种涂层表面均出现了黄褐色锈迹,说明碳钢基体发生腐蚀且腐蚀产物在界面处聚集。结合图5可知,涂层孔隙率增大为腐蚀性介质提供了更多的传输通道,使得腐蚀性介质在涂层中的渗透更加容易,同时引起涂层吸水率的增加。环氧云铁中间漆的孔隙率和吸水率均比富锌底漆大大降低,氟碳面漆虽然吸水性比中间漆好,初期孔隙率增加也较快,但是增加这一道屏障后,三层体系整体孔隙率进一步降低,吸水率显著下降,屏蔽作用最好。
3、结语
1、对于氟碳/环氧云铁/环氧富锌涂层体系,浸泡初期,中间漆对涂层防护性能影响很大,有效阻止了涂层对电解液的渗透,延长了介质的渗透时间,显著提高总阻抗,对三层涂层体系的屏蔽性能起到了重要作用;浸泡中后期,环氧富锌底漆发挥自修复能力,有效提高涂层的防护性能。
2、环氧富锌单涂层的吸水率能力较强,富锌底漆外面涂刷环氧云铁中间漆后涂层吸水率大幅降低,可能与云母氧化铁使水分子在中间漆中的渗透路径增长有关;氟碳面漆比环氧云铁中间漆的吸水性略大,但三涂层体系吸水率总体最低且能在较长时间保持在较低水平,说明三涂层体系对于水和离子渗透起到了有效的屏蔽作用。