- 专题资料:
- 中国科学院金属研究所
- 专题制作:
- 国家材料环境腐蚀平台
联系我们
-
-
电话: 010-82387968 -
邮箱: shujushenqing@126.com -
地址: 北京市海淀区学院路30号 -
邮编: 100083
- 粉末涂料在大口径给排水管道上的应用
管道几乎无处不在,是气体、液体等流体最有效的输送方式。管道运输不仅运输量大、连续、迅速、经济、安全、可靠、平稳以及投资少、占地少、建设及维护费用低,而且可实现自动控制。各种管道像人的血管一样,遍布全球,连接着城市与乡村,连接着千家万户。我国城镇化建设正在不断地推进,而评价一个区域城镇化水平的重要指标是供水、供气、供暖、排水等与管道相关的因素。中国是一个正处在快速发展中的大国,人口众多,人均能源、水资源等重要资源的占有量严重不足。例如我国人均能源占有量不到世界人均水平的一半,石油仅为十分之一;水资源仅仅是四分之一,是世界严重缺水、污染严重的国家之一。面对如此严峻的现实,我国政府决定执行"建设资源节约型、环境友好型社会"的发展战略方针,解决好可持续发展所面临的问题。为此,我国正在全力实施"节能、节水、节地、节材"等战略工程。近几年大力推动给排水管道产业的发展,也具有重要的战略意义。钢质管道具有承压效果好及耐老化性能高的特点,因此供水、供气管道的主干线一般采用大口径钢管,这就把钢管的防腐提到较高高度,可以说防腐的好坏决定着管道的使用寿命。埋地钢管的腐蚀一直是个难题,20 世纪 50 年代之前,所使用的防腐涂层主要是煤焦油和沥青,后来又出现了热压聚乙烯缠带,这些材料在使用中被证明是有效的,但是由于环境污染、应用效率低、适应性差等原因限制了这些材料的使用,直到 50 年代以后熔结环氧粉末涂层的出现,才使钢管防腐出现了革命性变化,并且熔结环氧粉末与聚乙烯涂层配合使用使管道防腐的水平达到了前所未有的高度,是一种较完美的组合防腐方式。
1 熔结环氧粉末
熔结环氧粉末是一种以环氧树脂为基料的热固性粉末涂料(加热熔化,然后固化成膜,以后不再遇热熔化),应用于管道防腐领域已有 50 多年的历史,最早服役的环氧粉末涂料涂层防腐的管线现在还依旧发挥着作用。熔结环氧粉末涂料是一种以空气为载体进行输送和分散的固体涂料,将其施涂于经预热的钢铁制品表面,熔化、流平、固化形成一道均匀的涂层,故得此名,英文名称 Fusion Bonding Epoxy Powder Coatings,简称 FBE.熔结环氧粉末的每个颗粒都均匀地包含所有组成成分,使涂敷的操作过程以及形成的涂层都具有连续稳定的均匀性。其优异的物理性能、化学性能、使用性能、耐久性能、安全环保性能、经济性(涂层薄,只有 300~500μm,成本低)得到防腐界普遍认可, 经得起实践和时间的考验, 广泛应用于输水、输油、输气等方面,并发挥着其独特作用。几十年来,经过不断的发展完善,这项技术已经走向成熟。在不同的管径、传输介质、连接方式、地理环境都有出色的表现。由于环氧树脂分子上具有两个以上的活性官能团(羟基和环氧基),固化后形成立体网状分子结构,而且能与钢铁表面发生化学反应形成化学键,所以具有极好的附着力和刚性。
2 管道工程用聚乙烯粉末涂料
管道工程用聚乙烯PE粉末是一种以非极性的低密度和线性低密度聚乙烯为基料的热塑性粉末涂料(可反复熔化),其历史比熔结环氧粉末涂料更早一些。由于其分子是非极性分子,不具有活性官能团,所以附着力不佳,这个致命的缺点限制了其发展,后来接枝改性技术发展,让聚乙烯分子具有了一些极性基团,附着力有所提升,但还远远达不到熔结环氧粉末涂料涂层与钢铁的粘接强度。然而聚乙烯具有超强的韧性和抗冲击能力,以及耐水性和边角覆盖性,非常适合一些外层包覆的或有锋利边角的工件涂覆,只是由于附着力原因,一般不推荐内涂。
3 管道腐蚀与防护材料比较
虽然地下不含极强的腐蚀性化学物,但埋地管道长期接触含盐的地下水,土壤中的微生物产生的各种有机酸,以及杂散电流,会产生电化学反应而腐蚀。众所周知电化学腐蚀的三要素是:水、氧和离子。环氧和聚乙烯两种涂层都是高聚物薄膜,能不同程度地阻缓上述三种因素的透过而发挥防腐蚀作用。但由于分子结构的不同,两种涂层各有优缺点。
表1是熔结环氧粉末涂层和聚乙烯粉末涂层的一些对比数据。由表1可以看出,PE和FBE有较强的互补性,如果两种材料结合使用,FBE做内涂或底涂,PE做外涂,可以彼此弥补缺点,发挥长处,最大限度发挥各自优点,而成为一个绝佳组合。
4 FBE 粉末的施工工艺
FBE 粉末的涂敷方法主要有:静电喷涂法、热喷涂法、抽吸法、流化床法、滚涂法等。管道内涂敷一般采用摩擦静电喷涂法、抽吸法或热喷涂法;管道外涂覆一般采取静电喷涂法;异型件采用流化床法或静电喷涂法。这几种喷涂方法都有一个共同特点,即喷涂之前需要将工件预热到某一温度,使粉末一接触即熔化,余热应该能使涂膜继续流动,进一步流平覆盖整个钢管表面,特别是在钢管表面的凹陷处,以及焊缝两侧,熔融的涂料流入填平,使涂层与钢管紧密结合,最大限度减少孔隙,并在规定时间内固化,最后用水冷却终止固化过程。
表 1 熔结环氧粉末涂层和聚乙烯粉末涂层的对比数据
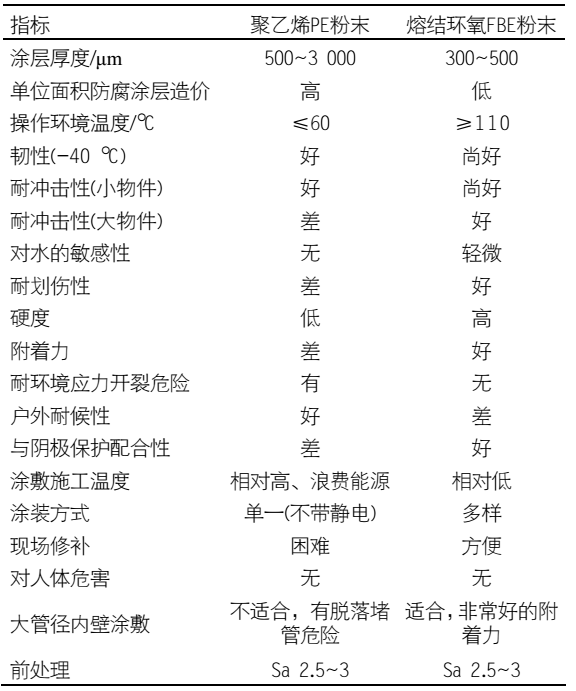
4.1 外涂单层熔结环氧粉末的施工工艺
(1) 预热钢管,去除表面杂物、疏松氧化皮;
(2) 进行喷砂或抛丸处理,使钢管达到金属白色,一般锚纹深度控制在 50~100 μm,然后清除表面灰尘;
(3) 经过表面处理的钢管采用无污染的热源均匀加热。一般利用中频线圈加热钢管(即电感应加热,钢管通过载有交变大电流的线圈所形成的交变磁场可产生涡流加热),加热温度可根据生产速度、管壁的厚薄以及希望的涂层胶化、固化时间进行调整,一般控制在 180~250 ℃之间,以 230 ℃为宜;
(4) 环氧粉末先在流化床内充分流化,然后通过静电喷枪使粉末颗粒带负电,均匀地粘附在经预热的接地钢管表面。粘附在预热钢管表面的环氧粉末受热熔化并流动,进一步流平覆盖整个钢管表面,特别是覆盖在钢管表面的凹陷处,以及焊道两侧,熔融的涂料流入填平,使涂层与钢管紧密结合,最大限度减少孔隙。流平后的涂层进一步胶化、固化。根据不同的生产速度,以及对胶化、固化温度、时间的要求,有不同类型的粉末与之相对应。固化时间一般为 1~1.5 min.涂膜厚度普通级为 300~500 μm,加强级可达到 700 μm;
(5) 浇水冷却,终止反应;
(6) 当温度降到 90 ℃以下时,进行涂膜性能检测(如图 1 所示)。
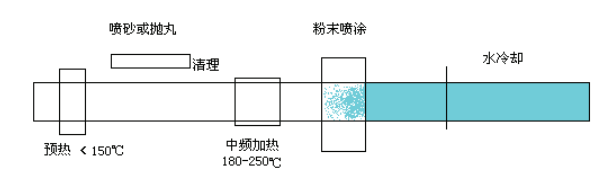
图1 单层外涂熔结环氧粉末的施工工艺
4.2 内涂熔结环氧粉末的施工工艺
内涂工艺与外涂工艺类似,前处理工艺基本一致,只是内抛丸工艺不能实现,一般采用内喷砂工艺,加热方式有电炉加热、燃气炉加热、中频加热等,涂覆方法主要有喷涂法和真空吸涂法两种:
(1) 内喷涂
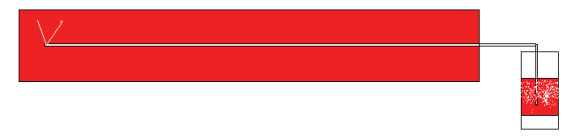
图 2 内喷涂示意图
(2) 真空吸涂
真空吸涂法属于热涂覆技术,一般用于小口径管道和弯管的内壁涂装。真空吸涂工艺流程如图 3 所示。
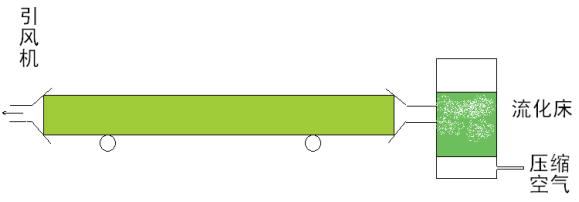
图 3 真空吸涂示意图
粉末与空气混合后进入管道内,它与高温管壁接触时熔融粘附于管壁表面。抽吸过程中气流带走管壁部分热量使其温度下降,粉末粘附量也随之减少,甚至粘附不上。因此管道预热温度的高低对涂膜厚度影响很大。吸涂时涂膜厚度随供粉量增大仅略有增加。由于真空吸涂时粉末涂料总是过量供给,多余粉末被抽入回收装置,因而粉末过量多与少对厚度影响不大。涂膜厚度对供粉时间十分敏感。在同等条件下供粉时间越长涂膜越厚。吸涂施工过程中,管道温度因散热、粉末吸热和抽吸气流带走的热量使其不断下降。当管壁温度下降到难以熔粘粉末时,即使供粉时间再长涂膜厚度也不可能增加。在生产施工中,随着管径大小、批量大小、生产节奏等因素的变化,应该相应调整有关工艺参数来达到满意的涂膜。
4.3 三层防腐结构及工艺
(1) 三层防腐(以下简称 3PE)结构组成包括:熔结环氧粉末底层、聚合物胶粘剂中间层和聚乙烯面层(如图 4 所示)。
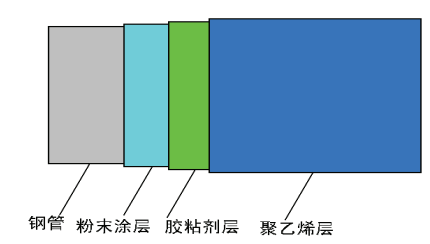
图 4 三层防腐结构示意图
其中环氧底层的作用是形成连续的涂膜,通过与钢管表面粘结、固化而提供良好的附着力,并具有很好的耐化学品性和抗阴极剥离能力。聚合物胶粘剂的作用是在粉末涂料胶化之前与之融合,并与外面的聚乙烯层粘结,使三层连成为一个整体, 最外层一般选用中高密度聚乙烯(国外也有使用聚丙烯), 这样三层防腐结构综合了环氧粉末的附着性、防腐性与聚乙烯层的耐候性、抗机械损伤性,弥补了各自的缺点,从而大大提高了涂层的使用寿命,是目前我国大型管道工程上首选的涂层,这种防腐方式只适合管道外层防腐。3PE 防腐层从 1995 年在库鄯线、陕京线应用以来,客户反映是国内所用过的最好的覆盖层。但有一种观点认为:3PE覆盖层破损后,由于聚乙烯具有较好的绝缘性和耐水性,可阻碍阴极保护电流的通过而形成屏蔽,阴极保护作用不能很好地发挥。目前我国应用中对此观点尚未重视。此外,3PE 防腐层造价相对较高,也是其缺点之一。
国家重点工程"西气东输"主管线基本都选择 3PE 作为外防腐层。
(2) 施工工艺(侧向缠绕法)如下:前处理与熔结环氧单涂层相同;用静电喷涂法将熔结环氧粉末均匀涂覆在钢管表面,厚度 60~150 μm;在其胶化前将胶粘剂涂于粉末层上;将挤出的粘流态聚乙烯带侧向缠绕于胶粘剂之上,并辊压使之与胶层牢固结合,这样三层连接成为一个整体。
4.4 双层熔结环氧粉末结构及施工工艺
单层外涂 FBE 耐划伤性能比较差,施工性受到影响。为了完善这一体系,克服上述不足,着重在 FBE 材料改性上做文章, 提出了双层 FBE 涂层防腐体系, 即以标准的 FBE涂层为底涂层,以改性的 FBE 涂层为外防腐层。这种双层FBE 涂层防腐体系进一步提高了机械性能,增强了涂层的抗冲击、耐划伤、耐高温等能力以及高温抗渗透性,同时保持了单层 FBE 涂层与阴极保护的相容性能,不会产生阴极保护屏障,可适用于各种管径的钢管、弯头、异型件及补口的防腐涂装。
(1) 双层熔结环氧粉末的结构
双层熔结环氧粉末体系是由两种不同的熔结环氧粉末在喷涂过程中一次喷涂成膜完成的,底层为普通单层环氧粉末层,提供防腐性及附着力;外层为增强型,提供抗机械损伤性能;两层中间是混合层。因为两层的基料具有相同的分子结构,所以具有较好的相容性,可形成一个有机的整体,不会产生层间分离现象(如图 5 所示),整个涂层整体厚度在 625~1 000 μm 之间,使用温度可达 115℃,可适用于各种管径的钢管防腐涂装。
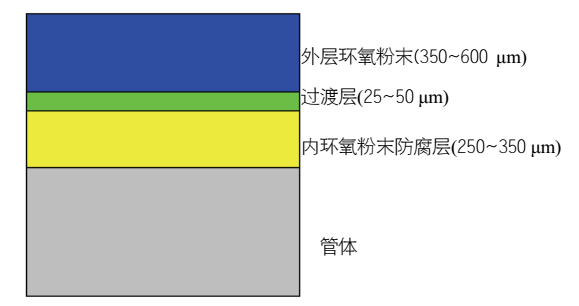
图 5 双层熔结环氧粉末涂层结构示意图
双层熔结环氧粉末防腐体系具有以下优点:与基材粘接强度大,抗阴极剥离性能好,吸水率小,使用温度范围大,综合性能与 3PE 防腐涂层相当,耐划伤性优异。此外,补口也用双层 FBE,相容性好,操作方便,质量控制容易,覆盖层表面光滑,可避免阴极屏蔽问题,与阴极保护体系的匹配性比 3PE 结构更好。这是一种国际上新研制出的覆盖层,最适于腐蚀比较强的穿越地段使用,双层熔结环氧粉末防腐体系的缺点是造价较高。 "西气东输"拟在淮河以南的水网地区和河流、铁路、公路等穿越地段使用。
(2) 涂覆工艺
双层熔结环氧粉末涂层的涂覆工艺比 3PE 简单,只在原有的单层熔结环氧粉末喷涂设备的基础上进行微小改造即可,即把喷枪分成三组,第一组喷涂底层粉末,第二组喷涂外层粉末,第三组喷涂回收粉末。喷涂粉末可单独回收,也可一起回收(如图 6 所示)。
4.5 流化床热浸涂覆
(1) 涂覆工艺
这是一种施工非常简便的涂覆工艺。需要一个竖井式流化床,粉末倒入流化床,呈沸腾式流化状态,然后将经前处理且预热的管道放入竖井,浸没在粉末中,5~10 s后取出管道,即可完成管道内外的同时涂覆,根据情况考虑是否二次固化。
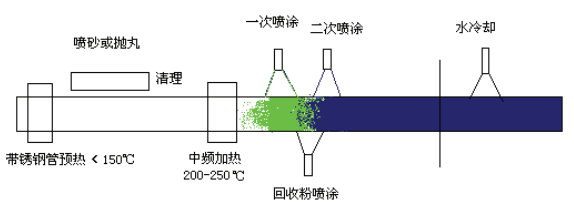
图 6 双层外涂熔结环氧粉末的涂覆工艺示意图
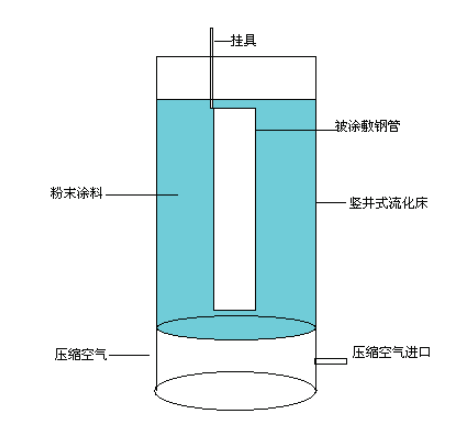
图 7 流化床热浸涂覆示意图
(2) 优点:生产效率高,内外涂同时进行,施工简单,占地面积小。
(3) 缺点:管道上下端涂层厚度不一致,一般上薄下厚,差距很大;一次性投入流化床的粉末用量巨大,少则几吨,多则十几吨,也有几十吨的,粉末出了问题无法挽回;由于有积粉问题,带有法兰的管道生产时不容易控制涂覆质量。
5 PE 粉末的涂覆
PE 粉末密度较小,适合流化床涂覆、滚涂等方式,由于不带静电,不适合喷涂,而且一般管道预热所需的温度较高。
6 大口径给排水管道内外涂覆
大口径管道不同于一般小口径管道,由于内外壁面积大,所以涂覆时间要长,必须选择合适的粉末和合理的涂覆工艺。内壁涂料要求坚硬耐磨,具有良好的附着力,流平要好,摩擦系数低,有良好的输送效率,外部要有韧性、抗冲击,对野蛮施工造成的损伤不敏感。所以环氧、外聚乙烯是一个很好的组合。
大口径管道一般指直径大于 600 mm 的管道,管壁厚度一般大于 10 mm,因为管径较大,长度较长,所以内壁不适合真空吸涂和流化床浸涂的方式,可采用喷涂或滚涂方式。国内大口径给排水管道防腐一般采用内 FBE 外 PE涂覆,这样防腐的管道内涂层致密、光滑,附着力好,外涂层坚韧,抗磕碰,便于操作。因为管壁较厚,余热足够涂层固化,所以不用考虑后加热固化,但因为直径较大,所以应考虑较快的上粉速度和粉末胶化时间,否则前面涂
覆的粉末已经固化,后面再飞上去粉末,不能熔于一体,造成表面粗糙。
工艺上有两种,(1) 先涂外层 PE,采用瀑布滚塑法,将经前处理好的管道加热到 250 ℃左右, 以瀑布下泄的方式涂到旋转的管道表面, 等管道温度下降到 230 ℃以下再喷涂或滚涂环氧粉末于管道内壁, 然后靠余热固化; (2) 也可以采用先内涂环氧,然后外层采用 3PE 涂覆,这就要求内涂 FBE 有很好的耐温性能。需要注意的是:被涂覆的大口径管道一般长为 12 m,利用余热使之固化,凝胶时间必须足够快,使之冷却前完全固化;同时,固化速度又要足够慢,使表面适当润湿和流平, 也就是说熔结环氧粉末涂料是热固性涂料, 涂装后,不但要流平,而且要完全固化,要发生一系列化学反应,形成立体网状结构的大分子,这需要在一定温度下,保持一段时间,使之完全反应和熟化,如果没有完全反应,固化率达不到 95%以上,则涂层的物理、化学性能不能实现,涂膜中的树脂还是脆的预聚体,没有强度和耐性,更谈不上对钢管的保护,这一点在熔结环氧粉末的使用中是非常重要的。这是一个平衡,也是一个技巧。不同于石油、天然气管道,给水管道涂层一般要求符合相关卫生标准,不应含有对人体有害的重金属及其他有害物质。
7 大口径管道的阴极保护
阴极保护是一种用于防止金属在电介质(海水、 淡水及土壤等介质)中腐蚀的电化学保护技术, 该技术的基本原理是对被保护的金属表面施加一定的直流电流,使其产生阴极极化,当金属的电位负于某一电位值时,腐蚀的阳极溶解过程就会得到有效抑制。根据提供阴极电流的方式不同,阴极保护又分为牺牲阳极法和外加电流法两种,前者是将一种电位更负的金属(如镁、铝、锌等)与被保护的金属结构物电性连接,通过电负性金属或合金的不断溶解消耗,向被保护物提供保护电流,使金属结构物获得保护。后者是将外部交流电转变成低压直流电,通过辅助阳极将保护电流传递给被保护的金属结构物,从而使腐蚀得到抑制。简单来说,都是使金属表面电子达到饱和的一种电化学技术。不论是牺牲阳极法还是外加电流法,其有效合理的设计应用都可以获得良好的保护效果。阴极保护的费用通常只占被保护金属结构物造价的 1%~5%, 而结构物的使用寿命则可因此而成倍甚至几十倍地延长。即使没有涂层的保护,只要阴极保护电流足够大,被保护的物体也不会被腐蚀,但这样耗材消耗太快,维护费用非常高(如水库、河流的闸门的保护)。 管道防腐一般采用涂层和阴极保护一起使用,将 FBE 与阴极保护有很好地配合,能同时发挥作用, 使管道得到长期有效的保护, 特别是在城市(杂散电流)或沿海地区尤为重要。PE 涂层由于绝缘性太好,对阴极保护电流具有一定屏蔽作用,所以它们的配合使用效果有待评估。
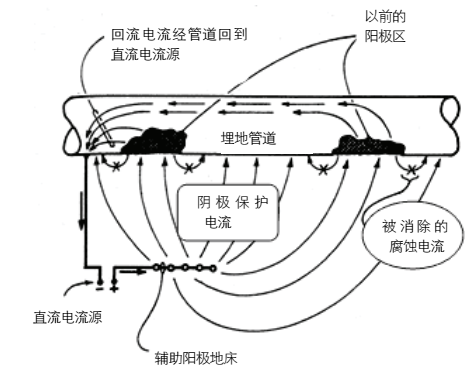
图 8 阴极保护的原理
阴极保护和涂覆层的联合应用,可以使地下或水下金属结构物获得最经济有效的保护。良好的涂覆层可以保护构筑物99%以上的外表面不受腐蚀,地下或水下的金属结构物通常在使用前涂覆防护涂层,以将金属与电介质环境电绝缘隔离。如果金属构筑物能够做到完全电绝缘隔离,金属在电介质中的腐蚀电池的形成将受到抑制,腐蚀电流将无法产生,从而防止金属的腐蚀。然而,完全理想的涂覆层是不存在的,由于施工过程中的运输、安装及补口,热应力及土壤应力、涂层的老化及涂层微小针孔的存在,金属结构物的外涂层总会存在一些缺陷,而这些缺陷最终将导致金属的局部腐蚀产生。阴极保护技术和涂层联合应用可以有效解决这一问题。一方面阴极保护可有效地防止涂层破损处产生的腐蚀,延长涂层使用寿命;另一方面涂层又可大大减少保护电流的需要量,改善保护电流分布,增大保护半径,使阴极保护变得更为经济有效。对于裸露或防腐涂层很差的地下或水下金属构筑物(如水闸),阴极保护甚至是腐蚀防护的唯一可选择的手段。8 大口径管道的补口管道连接方式有许多种:法兰连接、焊接、丝扣连接、卡箍连接等,其中大口径接管采用焊接方法连接,接口处需要补口,防腐预制的管道管端要预留 5~10 cm 不涂覆,
国外叫做"剪尾" ,因为将来焊接时也要受高温而损坏,焊接后接口部分还要防腐,即"补口" .根据相似相容的原理,补口材料要用与预制管道防腐相同的材料,如果预制管道是用 FBE 涂覆的,那么补口材料也要用环氧材料,如环氧粉末或液体双组分环氧漆。在施工现场用环氧粉末补口有一定难度,补口用的最广泛的是液体双组分环氧漆,这是一种 100%固体含量快速固化双组分液体环氧涂料,分 A、B 两个组分,用于管道防腐涂层漏点和较大面积缺陷区的防腐和修补,也可用于管道补口及内涂减阻涂层的涂装和修补。使用时把 A、B 组分按一定比例准确称量加入容器中,充分搅拌均匀后,可立即涂覆,无需熟化。视环境温度、相对湿度、配料的量,决定 B 组分的用量。如温度低,相对湿度大,B 配料量大一些,反之 B 配料量小一些。双组分环氧漆涂覆方便,固化速度快,适合施工现场使用,而且与环氧粉末涂层性质相似,能够完全融合在一起,不会发生分层、脱落,是目前单层 FBE 层补口的较好方式。
PE 粉末涂层或 3PE 防腐管道补口,一般用热收缩套,因为化学结构相同,所以补口效果很好。
9 结语
给排水管道工程是百年大计,一切都应从高起点、高规划、高标准出发,这关系到人民群众的生命财产安全,关系到中国未来几十年的发展。所以需要材料生产厂家、研究部门、设计部门、使用部门、监理部门共同努力,根据最终用途合理选择、正确使用粉末涂料,对影响质量的每一个环节都要充分考证、严格把关,并借鉴国外先进的技术和成熟的经验,结合国内的实际情况具体应用,科学规划,周密选材,合理施工,认真检测,严格监理,以确保各项工程的施工和运行万无一失。