油气管道腐蚀防护系统是确保管道长期安全运行的基本保障,随着国家对油气管道安全监督力度的加强,油气管道腐蚀检测成为管道安全防护的重要环节和技术手段。腐蚀贯穿钢质管道全生命周期,是导致油气管道失效事故的主要诱因之一。定期对管道开展腐蚀检测,及时、准确地发现腐蚀缺陷,并采取相应的控制、维修、更换措施,可有效降低腐蚀事故发生概率。目前,中国在油气管道腐蚀检测方面已经形成以直接评价为核心的相对完善的检测与评价技术体系,包括外腐蚀直接评价(ECDA)、内腐蚀直接评价(ICDA)、应力腐蚀开裂直接评价(SCCDA)。2000年左右,直接评价技术被引入中国,经过大量工程应用,已经形成自己的行业标准,相关内容也纳入油气管道定期检验项目“。近年来,针对油气管道管体缺陷的非开挖检测技术也得到较多工程应用,如瞬变电磁技术(TEM)、超声导波检测技术、磁应力检测技术(MTM)等。工程实践表明:直接评价虽然存在一定的局限性,但仍是目前用于评估油气管道腐蚀控制状况或腐蚀风险的有效手段,对于埋地长输油气管道而言,外腐蚀直接评价的工程应用最为广泛,技术也更加成熟。
1 技术现状
1.1外腐蚀检测与评价技术
1.1.1发展概况
在2000年以前,埋地钢质管道的外腐蚀检测主要依靠开挖调查。当时主流的防腐层质量检测技术是中国自主研发的变频-选频法,其以一定长度的管道为评估对象,通过测试单位面积防腐层与远方大地之间的电阻,评估埋地钢质管道外防腐层的状况[2]。该方法适用于评价一段管道防腐层的整体质量,无法定位找出防腐层破损位置,目前已很少应用。关于阴极保护有效性的评价,虽然提出了IR降的概念,但电位测量仍主要依赖于试片或极化探头,检测效率低。
在2000年以后,随着一些检测设备(如英国雷迪公司的RD-PCM测量设备、加拿大CATH-TECH公司的CIPS测量设备、中国自主研发的SL系列防腐层检漏仪)的研发与应用,外检测和评价技术得到快速发展,逐步形成以交流电流衰减法(ACAS)、交流电压梯度法(ACVG)、皮尔逊法(PERSON)、密间隔电位测量法(CIPS)、直流电压梯度法(DCVG)为核心的技术体系,建立了一套科学的外腐蚀直接评价技术流程(图1),提高了外腐蚀检测的效率和准确率,成为目前外腐蚀检测和评价的主流方法。
通过不同检测方法的组合应用,可系统评估管道外防腐层质量、阴极保护有效性、杂散电流干扰的总体状况,并结合防腐层破损处的开挖调查,对管体腐蚀缺陷及环境腐蚀性进行直接检测和评价。但相关检测设备的应用需要通过大地形成良好的回路,在一些特殊管段的应用存在困难,测量结果的准确性也因此受到影响,主要包括:①大型穿跨越、连续水网区等测试人员难以到达的管段;②铺砌路面、冻士、钢筋混凝土、含有大量岩石回填物等导电性较差的管段;③防腐层剥离、套管、保温层等易造成电屏蔽的管段;④杂散电流干扰严重的管段。
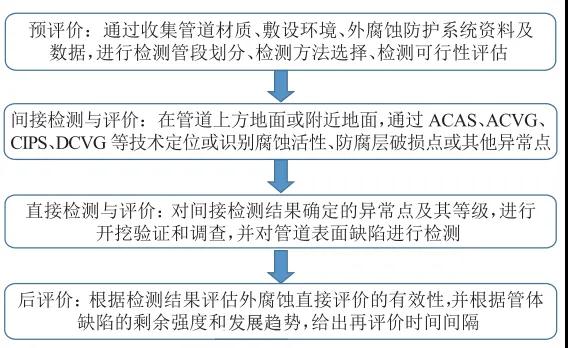
图1油气管道外腐蚀直接评价( ECDA)技术流程图
1.1.2技术标准
中国最早用于指导油气管道内外腐蚀检测的标准是SY/T0087-1995《钢质管道及储罐腐蚀防护与调查方法标准》,其中开挖调查相关规定一直沿用至SY/T5919-1994《埋地钢质管道干线电法保护技术管理规程》主要用于指导阴极保护和交直流杂散电流干扰的检测与评价,其中的阴极保护度、阴极保护有效率概念也一直沿用至今。2004 年,中国石油规划总院、中国石油大学(北京)、中国石油管道公司沈阳调度中心等单位,非等效采标美国防腐蚀工程师协会(NACE)标准NACE RP 0502-2002《管道外腐蚀直接评价方法》,编制了SY/T 0087.1- 2006《钢制管道及储罐腐蚀评价标准埋地钢质管道外腐蚀直接评价》,形成了以间接检测为核心的外腐蚀直接评价技术规程。目前,该标准已经完成第二次修订,最新发布版本为SY/T0087.1-2018,该标准较好地指导和推动了中国油气管道外腐蚀检测工作的开展,在工程实践中积累了大量宝贵经验,同时也发现一-些不足,如流程过于复杂,检测技术适用范围受限,评价指标可操作性不强等。
自NACE RP 0502-2002之后,NACE又先后发布了一系列标准,对于提高ECDA的有效性起到了很好的支撑作用。NACE SP 0207-2010《埋地或地下水金属管道上密间距和直流电压梯度测量》提出了CIPS和DCVG检测流程及技术要求,NACE TM0109-2009《地下管道防腐层状况评价地面检测技术》提出了间接检测技术的操作流程和数据分析方法,NACE SP 0210-2010《管道外腐蚀确认直接评价》提出了综合运用多个指标、多种因素评估和判断外腐蚀风险的流程。目前,中国除SY/T 0087.1之外,针对具体检测方法的标准尚未形成完整的标准体系,SY/T0087.1- 2018在原标准的基础上重点修订了评价准则以及间接检测与评价部分,由原来的单-指标评价改为综合指标评价,采用风险矩阵的思路将土壤腐蚀性、防腐层破损程度、阴极保护水平、杂散电流干扰程度等单一指标进行组合,以综合评估外腐蚀风险,确定开挖调查的优先级,促进了评价思路的完善,但尚未完全解决检测技术的规范性问题。
1.2内腐蚀检测与评价技术
1.2.1 发展概况
埋地钢质管道内腐蚀检测与评价技术的发展与外腐蚀检测与评价技术基本相同,最初也是主要依赖介质腐蚀性分析和开挖调查。目前,针对内腐蚀的检测与评价,除内检测技术外,主要采用内腐蚀直接评价(ICDA)方法。2006 年,NACE发布了干气管道内腐蚀直接评价标准NACE SP 0206-2006《干气管道内腐蚀直接评价方法(DG-ICDA)》,国内也同步开始了输气管道内腐蚀直接评价的应用研究,随后多相流管道内腐蚀直接评价方法(MF-ICDA),湿气管道内腐蚀直接评价方法(WG-ICDA)、液体管道内腐蚀直接评价方法(LP-ICDA)陆续进入研究应用阶段。中国石油规划总院通过持续开展ICDA研究与应用,积累了丰富经验。ICDA分为预评价、间接检测、详细检查、后评价4步流程(图2),其中间接检测是核心,主要通过流体力学模型计算给出可能的内腐蚀风险点,再结合腐蚀预测模型分析其发展趋势。常用的流体分析软件包括Fluent、OLGA等,结合管道走向、流体状态,预测水或腐蚀性介质易沉积的位置,并通过现场开挖进行验证。
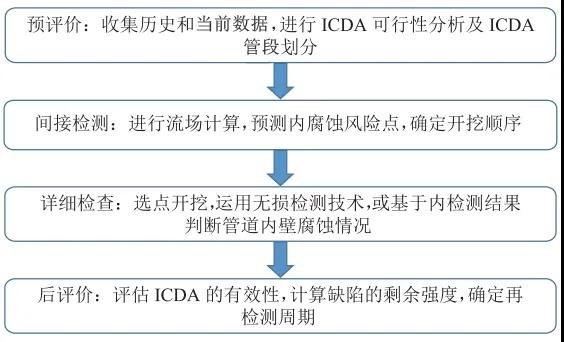
图2油气管道外腐蚀直接评价(ICDA )技术流程图
这些预测方法或模型并不是唯一的,通常不具有普遍适用性。北美地区的一些管道运营公司往往结合所辖管道的实际情况,开发有针对性的计算模型或软件,可以重复使用和持续修正。
近年来,一-些油气长输管道因游离水沉积或介质质量控制不到位等问题而发生内腐蚀,因而推进了ICDA技术的应用,但总体应用效果不如ECDA技术成熟。在各种内腐蚀直接评价技术中,天然气干线管道内腐蚀预测模型较为成熟,在国外已有较多的成功应用案例,而液体管道、多相流管道的腐蚀分析模型因介质情况复杂,成功应用案例较少,目前大都处于探索阶段。科威特石油公司采用液体石油管道内腐蚀直接评价技术,通过引入新的点蚀因子,实现了对内腐蚀的准确预测。张国忠等在成品油的携水能力方面开展了大量的数值计算和实验研究,提出了水相梯度计算公式,分析了成品油在不同工况下的携水能力1-8]。中国虽然在输气管道、液体管道、多相流管道均开展了ICDA应用,但整体处于试验研究阶段,目前面临的问题主要包括:①在流场计算和腐蚀模型预测方面经验不足,特别是液体管道、 多相流管道计算参数繁多,不同模型对不同管道的适用性各不相同;②现有计算软,件或模型在长距离管道流体计算分析方面精度不高,计算能力有限。
1.2.2 技术标准
自2006年起,NACE先后发布了针对不同输送介质管道的ICDA技术标准,包括NACE SP 0206-2006、NACESP0208-2008《液体石油管道内腐蚀直接评价方法(LP-ICDA)》、NACE SP 0110-2018《湿气管道内腐蚀直接评价方法( WG-ICDA)》、NACE SP 0116-2018《多相流管道内腐蚀直接评价方法》。每一部标准都针对具体的流体特性,给出流场计算和腐蚀预测的推荐模型,如Adams模型、Crolet 模型、Dayalan模型等。这些模型与管道输送介质的属性、运行工况、敷设条件等参数的选取密切相关,直接决定计算精度和预测准确率。工程应用实践表明:选择合适的流场计算模型、腐蚀预测模型及工况参数是保证内腐蚀直接评价结果准确性的必要条件。
在2006年之前,中国用于指导内腐蚀检测与评价的标准主要是SY/T 0087-1995。2010 年,中国石油规划总院牵头编制了SY/T 0087.2一2012《钢制管道及储罐腐蚀评价标准第2部分:埋地钢质管道内腐蚀直接评价》。SY/T 0087.2-2012与NACE发布的标准虽然都建立了ICDA”四步“流程,但核心内容存在本质区别。SY/T 0087.2 - 2012推荐采用地面非开挖检测技术(TEM、超声导波、超声测厚等)确定管道内腐蚀位置,这些非开挖检测技术在实际应用中存在诸多局限性,对管道敷设条件和外界环境干扰较为敏感,也无法区分内、外腐蚀缺陷。目前,在管道内腐蚀检测与评价方面,中国一般参照NACE标准推荐的做法,而流场计算模型的运用则多种多样。GB/T 34349-2017《输气管道内腐蚀外检测方法》和GB/T34350一2017《输油管道内腐蚀外检测方法》中关于内腐蚀检测与评价的要求与NACE标准一致。
1.3 应力腐蚀开裂检测与评价技术
1.3.1 发展概况
应力腐蚀开裂(SCC)是材料在应力和腐蚀环境共同作用下产生的以裂纹生长和脆性断裂为特征的一种环境敏感断裂形式,油气长输管道以外壁应力腐蚀开裂为主,裂纹常以群落的方式集中出现在某- -区域, 裂纹群内可能存在几十到几百个相互平行的微小裂纹‘ 12]。1965年3月,美国路易斯安那州Natchitoches输气管道发生第一起SCC事故。20,世纪90年代,高pH值SCC开裂机理得到业界的普遍认可,近中性pH-SCC开裂机理也得到不断发展。中国从2001年开始对埋地钢质管道的应力腐蚀开裂问题开展专项研究,对四川天然气管网、陕京输气管道、涩宁兰输气管道进行现场调查,并开展系统的实验室研究工作[13-14]
SCC从萌生到引发事故是一个非常缓慢的过程,不易被发现或检出,引发事故前,裂纹常潜伏于管体几十年。应力腐蚀开裂直接评价方法(SCCDA)包括预评价、间接检测、直接检查、后评价4步流程,通过敏感性分析及开挖调查识别、确认管道的SCC风险,建立SCC敏感段开挖选点原则(图3)。
在SCCDA之外,北美地区的管道运营公司开展了数千公里基于内检测的应力腐蚀裂纹检测。漏磁检测是目前比较成熟的管道内检测方法,但管道表面裂纹形态各异,增加了裂纹检测和量化难度,通过检测信号难以精确识别出裂纹,只有当外加磁场方向最大限度地与被检缺陷正交时,才能激励出最大的漏磁场。美国TDW公司开发的螺旋漏磁检测技术(SMFL),结合周向漏磁检测技术的优点及传统轴向漏磁检测技术的精度特性,在未明显增加测量节长度的情况下,能够实现对各个方向狭长裂缝的精确测量。但针对轴向裂纹、尺寸较小裂纹和其他类裂纹缺陷的漏磁检测技术有待开展深入研究。超声波检测技术对裂纹等平面型缺陷较敏感,检测精度高,但对耦合条件要求较高。GE-PII、ROSEN、NDT等管道检测公司均拥有基于压电超声的腐蚀、裂纹检测技术。ROSEN公司研发的电磁超声裂纹检测器不需要液体耦合剂,适用于输气管道的检测,可以检测裂纹、防腐层剥离,但检测效果仍需通过工程应用加以验证。Enbridge公司的检测实1践表明,管道夹杂会影响超声波信号的传播,超声检测在裂纹尺寸和深度测量方面存在- -定误差,需要结合管道实际情况和开挖验证情况,对检测信号进行分析处理。目前,中国裂纹内检测设备尚处于实验室研发和样机试验阶段,实际应用效果不理想。应力腐蚀裂纹检测的另一个技术难点是定量化问题,超声相控阵(PAUT)是目前唯--能够检测应力腐蚀裂纹并给出定量尺寸和深度的技术,但对管道表面的耦合条件要求较高,检测效率低,只适用于开挖调查。
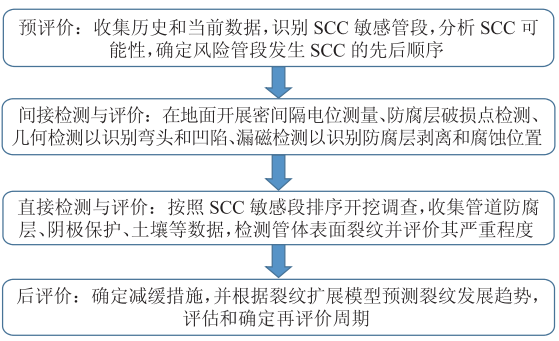
图3应力腐蚀开裂直接评价方法(SCCDA )技术流程图
1.3.2 技术标准
国外针对埋地管道应力腐蚀开裂开展了大量的实际调查和科学研究,形成多个技术标准,包括NACE.SP0204-2008《应力腐蚀开裂直接评价方法》、ASMEB31.8S-2014《输气管道系统完整性管理》、ASME STP-PT-011-2008《高后果区内天然气管道应力腐蚀开裂的完整性管理》、API RP 1160-2013《危险液体管道的完整性管理》,以及加拿大能源管道协会编制发布的《应力腐蚀开裂评价推荐作法》。这些应力腐蚀风险识别和直接评价方面的标准,主要借鉴北美地区的相关经验,受服役环境影响在中国的适用性有待验证。目前,中国的应力腐蚀开裂检测与评价标准GB/T36676-2018《埋地钢制管道应力腐蚀开裂(SCC)外检测方法》和SY/T 0087.4- 2016《钢质管道及储罐腐蚀评价标准第4部分:埋地钢质管道应力腐蚀开裂直接评价》在应力腐蚀开裂敏感性分析、敏感段识别和SCC裂纹评价方面主要参照NACE SP0204-2008。
1.4穿越段管道外腐蚀检测与评价技术
1.4.1 河流穿越
河流定向钻穿越段管道埋深大,无法实施地面检测,主要依靠设计、建设期提高防腐等级保证其使用寿命。GB/T 37369一2019《埋地钢质管道穿跨越段检验与评价》对穿跨越段管道的检测与评价提出了年度检查和定期检验的要求,重点提出了检测项目和要求,但具体的检测方法和技术手段涉及较少。NACE TM0102-2002《地下管道涂层电导率测试标准》推荐采用防腐层电导率评价定向钻穿越段管道防腐层质量,但该方法仅适合在施工完成后尚未与其他管段连接时应用。中国石油天然气集团有限公司企业标准QSY1477- -2012《定向钻穿越管道外涂层技术规范》要求河流穿越段管道在水平定向钻穿越后且未与主管道碰头前,实施穿越段管道防腐层测试与评价,该方法可实现对穿越段管道防腐层质量的整体评价,但无法准确定位防腐层缺陷位置。罗旭[5)研究了基于”电缆回路“和”管地回路“的电磁法水下管道埋深检测及防腐层缺陷定位技术的可行性,绘制了沿管道方向的磁场强度曲线,可实现对管道防腐层缺陷区域的定位,该方法目前尚未在实际检测中应用,而且应用于实际检测的工程量将非常大。中国石油管道科技研究中心研发了评价定向钻穿越段管道阴极保护有效性的数值模拟计算模型,假设定向钻穿越段管道防腐层破损点均匀分布,通过测量管道的极化曲线、不同层土壤电阻率,结合加拿大SES公司CDEGS软件模拟结果,评估了爬坡段管道阴极保护电流需求量及电位分布情况。天津嘉信技术工程公司自主研发的河流穿越段管道外腐蚀检测系统River-ROV,结合潜水和声呐设备,实现了对穿越段管道的定位。埋深测量、电位测量及防腐层破损点的定位功能,在多条河流穿越段实现了应用。
定向钻穿越段管道投入运行后,防腐层质量评估的意义已经不大。现有检测技术大都无法准确判断防腐层破损位置和破损程度,即使定位后也无法采取修复措施。目前,对于普遍使用的3PE防腐层,局部破损也并不会显著影响其绝缘电阻率。因此,应该重点关注阴极保护有效性评价,目前主要是基于数值模拟计算的方法来分析河流穿越段管道的阴极保护电流和电位分布状况,但在模型边界条件选取、土壤分层、防腐层破损点分布、绝缘电阻等方面仍需开展深入细致的研究。
1.4.2 金属套管穿越
关于金属套管穿越段管道的检测与评价问题,目前相关标准并未给出具体的测试与评价方法,以至于管道运营公司无法及时掌握金属套管穿越段管道的腐蚀状况。近年来,金属套管已逐渐被水泥套管取代,金属套管穿越段管道检测与评价的需求越来越小。美国交通运输部管道与危险物质安全管理局(PHMSA)根据美国《2002年管道安全改进法令》提出了高后果区管段完整性管理的要求,并于2010年3月发布了《高后果区套管中天然气管道的完整性评价导则(0版)》,强调了套管穿越段管道的完整性管理问题。
金属套管与输送管道的腐蚀问题与两者之间的绝缘状况密切相关。NACE RP 0200-2000《管道钢质套管操作规程》推荐了通过测量金属套管与管道电位差评估腐蚀风险的方法。Pikas',I6]提出了金属套管穿越段管道的腐蚀风险评价指标及金属套管穿越段管道腐蚀直接评价的4步流程。中国石油管道公司基于上述方法,曾连续开展金属套管穿越段管道的检测工作,实际验证了该流程的可靠性,以及超声导波技术在金属套管穿越段管道检测上的技术优势。
1.5 其他地面非开挖检测技术
1.5.1 瞬变电磁技术
1951年,加拿大物理学家Wait首先提出瞬变电。磁(TEM)技术原理。1960 年,苏联研制出第一。台检测装置,用于地下矿体探测、地质勘探及埋地管道检测。中国从20世纪70年代开始研究,已成功研制出可用于埋地钢质管道检测的装置。该技术原理是:利用施加脉冲电流的发射线圈在埋地管道周围激励磁场,脉冲电流的瞬间变化会引起磁场的变化,变化的磁场在埋地管道上激励出一种随时间衰减的”涡流“,由衰变”涡流“激励出随时间衰减的磁场又会在接收线圈中感应出电动势,感应电动势的大小与电阻率和磁导率相关,当管道无缺陷时,电阻率和磁导率是均匀的,而缺陷截面则会引起电导率和磁导率的变化,感应电动势的大小随之变化17。
TEM技术根据管道壁厚或物理特性变化识别缺陷,优缺点包括:操作简单,无需开挖和清管;可获得埋地钢质管道平均壁厚或金属损失量,但与实际壁厚有一定偏差,无法识别出缺陷面积,不能检测点蚀缺陷;检测时受管输介质、土壤、并行管道及外部电磁干扰影响较大;难以对埋深过大的管道进行检测。总体而言,该技术在长输管道应用较少,在埋深浅、干扰小的油田集输管道应用较多。
1.5.2 超声导波技术
1997年,英国导波公司(GUL)成功推出压电式超声导波检测设备,并迅速在欧洲得到应用。美国西南研究院(SWRI)也于20世纪90年代,研发出磁致伸缩式超声导波检测设备。这是目前超声导波的两大技术流派。其原理是:利用阵列式超声波探头激发沿管道轴向传播的超声导波,当遇到管道横截面积的任何改变时,都会反射一一个回波信号,信号强度取决于橫截面积的改变量。通过信号的对称与非对称特征可识别出管道上的环焊缝、弯头、法兰、支管、缺陷等特征,最小可检测到横截面积变化的3%。
超声导波可在不开挖或局部开挖条件下,在较长管段上实现”点“对”线“的快速扫查,定位出整个管段的内、外壁缺陷,识别出法兰、焊缝、支管等特征,但无法精确测量缺陷深度,面积等参数,需要局部开挖,配合采用其他无损检测技术实施缺陷定量测量。对于地上管段,可检测上百米,但对于埋地管段,检测距离较短,单侧检测长度一般只有5~25m。目前,超声导波技术主要应用于站场工艺管道和套管穿越段管道的检测。
1.5.3 磁应力检测技术
1994年,俄罗斯Doubov教授首次提出金属磁记忆概念,即铁磁性金属构件因受载荷和地磁场共同作用,在应力和变形集中区域发生具有磁致伸缩性质的磁畴组织定向和不可逆的重新取向,这种状态的变化是不可逆的,在载荷消除后不仅会保留,而且与最大作用应力有关,”记忆“着金属构件表面微观缺陷或应力集中的位置,即所谓的磁记忆效应18-21。磁应力检测(MTM)技术就是基于金属磁记忆效应开发的一种弱磁检测技术,检测处于地磁场环境中的铁磁性构件在缺陷或应力集中区域的漏磁场,从而实现缺陷定位。检测人员只需要手持检测仪器,在管道正上方行走,即可开展缺陷扫描。
MTM技术可检测管道金属损失缺陷和应力集中区域,对应力集中缺陷较敏感,但受外界电磁干扰及管道内检测后的剩磁影响较大。该技术产品自2002年商业化以来,目前已发展至第二代产品,在埋地钢质管道实现了应用,主要应用于俄罗斯。中国近年来也开展了试应用,但检测效果差异较大,仍需通过大量工程实践验证其检测的准确性。
总体而言,上述检测技术都是通过识别管道横截面变化判断管体缺陷,并不能区分外壁缺陷和内壁缺陷。其优点是:无需开挖,操作简单,检测效率高,对管道检测条件要求不高,适合局部管段的快速扫查,应用于长输管道全面检测效率不高。其缺点是:精度低,易受外界电磁环境影响,检出率不高,只能给出缺陷的相对,严重程度,无法精确测量管壁或缺陷尺寸。2019 年,中国石油管道公司尝试采用MTM技术定位管道环焊缝,结果表明定位准确率只有50%。
2 应用现状
长输油气管道外腐蚀检测与评价技术相对成熟,内腐蚀和应力腐蚀开裂检测与评价技术尚处于试点和摸索阶段。油气管道腐蚀检测技术选型和检测强度与企业生产需求和管理水平密切相关。TSGD7003-2010《压力管道定期检验规则一-长输管道》将外腐蚀、内腐蚀、应力腐蚀开裂的检测与评价统称为外检测,并未明确要求在定期检验过程中对所有管道全部开展。上述检测,管道运营公司可根据需求灵活选择。
2.1外腐蚀检测
外腐蚀检测与评价是长输管道定期检验的重要内容,通常按照新建管道3年内完成基线检测,随后每5年定期开展ECDA,最大时间间隔不超过8年。虽然当前外腐蚀控制水平有很大提升,但随着管道运行年限的增加,防腐层老化、剥离、破损及杂散电流干扰问题将越来越突出。2019年,中石油管道有限责任公司组织开展了针对所辖管道ECDA效能评价工作, .针对各地区公司所辖管道ECDA实施情况进行了调研,发现存在以下问题:①ECDA的4步流程执行效果不好,尤其预评价和后评价不充分;②检测服务商技术水平参差不齐,存在技术运用不当的问题;③检测服务商自行制定的评价准则差异较大,或评价指标运用不当;④对检测数据的分析和利用不够,数据统计分析形式多种多样,导致多次检测结果无法对比分析。主要原因可归纳为4个方面:
(1)标准的指导作用有限。SY/T 0087.1是一部方法类的标准,重点规范的是ECDA的流程和评价准则,对检测技术执行和数据分析的指导作用十分有限。总体而言,中国缺乏相应的技术规范来指导检测技术执行、数据分析,现行标准中评价指标、准则以定性为主,检测服务商运用评价准则的尺度把握各不相同,在实际应用过程中难以规范操作。而国外除ECDA方法标准外,还有配套的技术规范作为支撑。
(2)检测技术的局限性大。现有的间接检测技术对检测人员的经验和水平依赖性较大,且本身存在局限性,在涂层剥离、高电阻率环境、深埋管段、杂散电流干扰段、管道埋深超过正常值的特殊管段,外腐蚀检测与评价技术难以应用,部分方法抗干扰能力差,精度低。
(3)过程管理不够严格。在工程实践中,相同条件下ECDA评价结果存在差异,这与管道运营公司的管理水平及检测服务商的技术水平密切相关。管道运营公司虽然制定了管理流程,但一些公司的过程管理由分公司或基层站队负责,因缺乏专业技术人员,故对检测方案审查、检测过程管理监督、报告验收、质量控制的管理力度不够。
(4)数据分析和利用不充分。在ECDA工作完成后,部分检测服务商只提供报告,不提供原始数据,报告中也只列出一-些典型问题。管道运营公司无法验证检测数据的准确性,也无法对数据进行再分析和深度挖掘,多次检测数据无法进行对比分析,无法与管道内检测、风险评价、完整性评价数据深入融合。
2.2内腐蚀检测
在对1.1X10*km涵盖天然气、原油、成品油等输送介质管道内检测数据进行分析的过程中,将内部金属损失确认为内腐蚀缺陷,得到不同输送介质管道的内部金属损失缺陷密度(图4)。可见:原油管道内腐蚀较为严重,其次为成品油管道,天然气管道内腐蚀最轻。天然气管道内腐蚀分布没有明显规律,管道底部相对较多,其他部位内腐蚀分布随机性较大,没有明显的时钟特征,与服役年限没有明显的对应关系,表明内腐蚀由投产前形成的可能性较大,局部位置的内腐蚀可能与清扫后干燥不彻底有关。液体管道内腐蚀存在明显的时钟分布规律,主要集中在管道下半部分,表现为显著的积水腐蚀特征。服役年限较长的马惠线、秦京线、铁秦线、铁抚线等原油管道及兰郑长线、港枣线、兰成渝线等成品油管道,内腐蚀缺陷密度高,内腐蚀相对严重,表明内腐蚀随着管道服役年限的增加趋于严重。
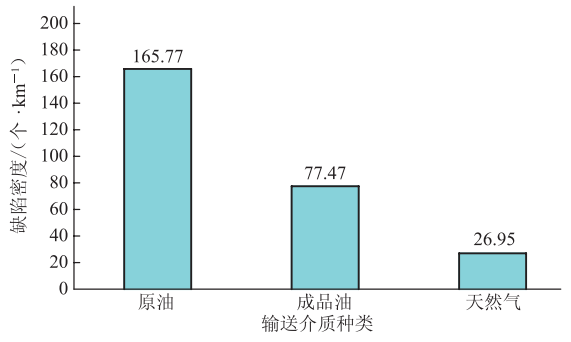
图4不同输送介质管道内部金属损失缺陷密度柱状图
目前,在内腐蚀检测方面,对于具备内检测条件的长输管道,管道运营公司优先选择内检测技术手段识别出内腐蚀高风险点,再结合定点监测和检测持续关注内腐蚀高风险点的发展,如超声定点测厚、安装腐蚀监测探头等,而ICDA在长输管道上的应用目前整体处于尝试阶段。
2.3应力腐蚀开裂检测
在应力腐蚀开裂检测方面,除2001年开展了系统研究和调查以外,直未开展大规模研究与应用,主要原因是:目前中国埋地钢质管道尚未发生典型的高pH-SCC或近中性pH-SCC案例。对于影响应力腐蚀开裂敏感性的各项因素,中国管道具有以下特点: .
(1)管道服役时间短。国外统计资料表明,应力腐蚀开裂通常在管道运行20年后进入高发期,且主要发生在采用沥青、缠带和煤焦油瓷漆类等低性能防腐层或施工质量低的管道。中国输气管道仅陕京-线投产运行超过20年,涩宁兰- -线投产运行接近20年,而且中国管道普遍采用工厂预制的3PE和FBE防腐层,防腐层使用寿命长。
(2)管道运行压力相对较低。国外案例分析表明,应力腐蚀通常发生在运行压力大于管道屈服强度60%以上的管段。中国大部分管道设计压力在屈服强度的60%~70%之间,但实际运行压力低于设计压力,只有陕京一线和西气东输--线的实际服役压力大于管道屈服强度的60%。同时,中国自行生产的管线钢的屈服强度一般高于标准要求,如X80管线钢屈服强度实测值通常在600MPa以上,高于标准要求的555MPa,因此,管道实际运行压力高于管道屈服强度60%以上的情况较少。
(3)中国管道发生应力腐蚀开裂的主要风险点为补口、划伤等易产生阴保屏蔽、阴保不足及存在杂散电流干扰的位置。近年来,中国长输油气管道外腐蚀控制水平持续提升,内、外检测技术大规模应用后,通过及时开挖修复及杂散电流干扰专项治理,外腐蚀风险降低,应力腐蚀开裂风险也随之降低。
3 总结与思考
近20年来,中国油气管道腐蚀检测技术水平整体提升较快,管理精细化程度不断提高,但也存在一些技术和管理问题亟待解决。未来的管理和技术提升应重点关注以下内容。
3.1管理提升
(1)建立统一的技术规范。目前,油气管道腐蚀检测相关标准以直接评价标准为主,更注重方法流程,对技术应用条件和实施过程的规定不够细化。管道运营公司应着手建立统一的规范,从检测资质、检测方案、技术运用、评价准则、数据格式、报告内容、验收标准等方面提出统一要求。
(2)建立数据管理平台。目前,外检测服务商提交的报告差异大,不便于后期的数据挖掘和综合分析。北美地区的检测服务公司会自行编制数据管理软件,并提供给管道运营企业,从而为管道运营企业后期数据使用提供便利。对于同-一条管道,通过重复利用原始数据,可有效提高ECDA工作效率。管道运营公司应该着手建立统--的数据管理平台,对腐蚀检测数据进行集中管理,并且加大内外检测数据的对齐和对比分析。
(3)建立专业化腐蚀检测效能评价队伍。外检测实施效果与具体检测人员的素质、责任心有很大关系。为了提升外检测管理效果,管道运营公司应建立专业化腐蚀检测效能评价队伍,统一管理标准和尺度,加强腐蚀检测的过程管理和最终检测质量的评估。
3.2技术提升
(1)持续开展应力腐蚀开裂检测与评价技术研究。中国长输油气管道虽然尚未发现应力腐蚀开裂的案例,但随着运行年限的增加,应力腐蚀开裂风险会越来越大。3PE防腐层粘结力降低或发生剥离,都可能导致应力腐蚀开裂风险增大。北美地区针对应力腐蚀开裂的研究持续了50年,直至2012年仍有应力腐蚀开裂事故发生。目前,近中性pH-SCC的断裂机理、硫酸盐还,原菌(SRB)在应力腐蚀开裂中发挥的作用,都还。有很多细节需要深入研究。未来仍需在高强钢应力腐蚀开裂机理、敏感性分析,风险识别和现场检测技术等方面持续开展深入研究。
(2)启动微生物腐蚀机理和检测技术研究。中国关于微生物的腐蚀最早发生在成品油管道内壁,而最近在长输管道外壁也发现了微生物腐蚀案例。微生物腐蚀机理复杂,腐蚀发展快,目前仍处于实验室研究阶段。对于长输油气管道,微生物与土壤成分、管道金属材料、防腐层类型、运行温度等因素的相互关系尚不确定,且缺乏有效的检测手段和防护措施。
(3)开展针孔腐蚀缺陷的检测与验证技术研究。内检测可以检出针孔缺陷,但要测量缺陷的真实深度却很难。目前已有案例表明,在存在交流干扰腐蚀的管道上,漏磁内检测报告结论是缺陷深度为壁厚的40%,但实际开挖检测发现,缺陷深度已达壁厚的60%。漏磁内检测技术对针孔缺陷的检出率低于80%,缺陷深度检测误差均大于20%,报告给出的缺陷深度远低于实际缺陷深度,严重影响评价结果的准确性。对于管道内腐蚀形成的直径小于4mm的针孔缺陷,常规的超声波检测技术也很难准确检出缺陷的实际深度。对于发展不规则的针孔缺陷,定点的超声波测厚和壁厚监测均难以满足工程实际需求。此时,不仅需要高精度的探头,还需要精密控制探头的扫描步进。
(4)开展组合式内外检测工具研发。为了保障长输油气管道安全平稳运行,需要定期开展外腐蚀检测及内检测。如果在内检测设备。上,搭载- -些可以实施腐蚀检测的装置,如管中电流测试、积水测试、微生物浓度检测,则可在实施内检测的同时同步完成管道的内外腐蚀检测。2008年,壳牌、贝克休斯公司开发了阴极保护电流在线检测工具CPCM(CathodicProtection Current Measurement),并已实现工程应用。
参考文献
[1]陈敬和。管道外腐蚀直接评价技术[J].油气储运,2011,30(7):523-527.CHEN J H. Direct asessment technology of pipeline externalcorrosion[J]. Oil & Gas Storage and Transportation, 2011, 30(7):523-527.
[2]陈宏,梁成浩,李海田。变频-选频法检测和评价钢质燃气管网腐蚀损坏[J].石油化工腐蚀与防护,2002, 19(4): 53-56.CHEN H, LIANG CH, LI H T. Variable frequency andfrequency modulation technique and evaluation of corrosionfailure of steel gas pipelines[J]. Petrochemical Corrosion andProtection, 2002,19(4): 53-56.
[3] SURYA P S, ABDUL R A, SHABBIR S, AMER A J. Internalcorrosion managenent of crude pipelins[ C]. Calgary: Procedingsof the 2014 10th International Pipeline Conference, 2014:IPC2014-33369.
[4]徐广丽,张国忠,刘刚,张鑫,张永样。管道中油携水流动时的水相界面分布模型[J].油气储运, 2010, 29(11):821-826.XU G L, ZHANG G Z,LIU G, ZHANG X, ZHANG Y X.Distribution model of water phase interfacein oil transportationpipeline with water[J]. Oil & Gas Storage andTransportation,2010, 29(11): 821-826.
[5]文松青,张涛,张奇超。成品油上倾管道油水两相流相分布识别方法[J].油气储运, 2019, 38 (9): 1022-1028.WEN S Q, ZHANG T, ZHANG Q C. Phase distribut ionidentification method for oil-water two-phase flow in updipproducts pipelines[J]. Oil & Gas Storage and Transportation,2019, 38(9); 1022- 1028.
[6]刘刚,汤苑楠,李博,赵家良,陈雷。成品油管道内杂质运移沉积及其影响规律[J].油气储运, 2017, 36(6): 708-715.LIUG,TANGYN,LIB,ZHAOJL,CHENL.Movementdepositionand influence laws of impurities in theproduct oilpipelines[J]. Oil & Gas Storage and Transportation, 2017, 36(6):708-715.
[7]隋冰,李博,赵家良,刘刚,于斐,张丽萍,等。起伏管道中成品油携杂质的流动状态[J].油气储运, 2017, 36(5):519-525.SUI B,LI B, ZHAOJ L,LIUG, YU w, ZHANGL P,etal. Flow regimes of oil product carrying impurity in undulatepipeline[J]. Oil & Gas Storage and Transportation, 2017, 36(5):519-525.
[8]宋晓琴,熊柯杰,朱建平,余东亮成品油携水特性对管道内腐蚀的影响[J].油气储运,2015, 34(8): 834-838.SONGXQ,XIONGKJ,ZHUJP,YUDL.Influenceofwater carrying capacity of oil products on internal corrosion ofpipelines[J]. Oil & Gas Storage and Transportation, 2015, 34(8): .834-838.
[9]胡亚博,刘智勇,董超芳。埋地钢质管道的外壁应力腐蚀开裂[J].腐蚀科学与防护技术, 2015, 27(2):207-210.HU Y B,LIU Z Y, DONG C F. Stress corrosion crackingonexternal wall of underground steel pipeline[J]. Corrosion Scienceand Protection Technology, 2015,27(2):207-210.
[10]帅健,翁永基,李克敏。油气管线外部应力腐蚀开裂控制方法的初步研究[C].北京:第四届全国腐蚀大会,2013: 197-199.SHUAIJ, WENG Y J, LI K M. Primary research on control toexternall stress corrosion cracking of oil &gas pipeline[C]. The4th National Corrosion Conference, 2013: 197- 199.
[11] 杨秘,赵东胜,王聚锋,向安,张立娜,刘智勇,等。 X65管线钢焊接接头抗H2S应力腐蚀开裂性能[J].油气储运, 2013,32(3): 334-338.YANG M,ZHAODS, WANGJ F,XIANG A,LIUZ Y,etal.Anti-HS stress corrosion cracking performance of X65 pipelinesteel welded joint[J]. Oil & Gas Storage and Transportation,2013, 32(3): 334-338.
[12]赵新伟,张广利,张良,罗金恒,于美外加电位对X80管线钢近中性pH土壤应力腐蚀开裂行为的影响[J].油气储运,2014, 33( 11): 1152-1158.ZHAOX W, ZHANGG L, ZHANG L, LUOJ H, YU M.Influence of appliedpotential on stress corrosion crackingbehaviorof X80 pipeline steel innearneutral pH soilenvironments[J]. Oil & Gas Storage and Transportation, 2014,33(11): 1152- 1158
[13]李晓刚,杜翠薇,董超芳,刘智勇。X70钢的腐蚀行为与试验研究[M].北京:科学出版社,2006: 198-199.LI XG,DUC W, DONGC F,LIU Z Y. Corrosion behaviorand experimental study on X70 steel[M]. Beijing: SciencePress, 2006; 198-199.
[14]范伟, 高继峰,刘畅。高酸性条件下点腐蚀深度对L360管道性能的影响[J].油气储运, 2018, 37(2): 162- 168.FAN W,GAOJ F,LIU C. Effect of pitting corrosion depth onthe performance of L.360 pipeline under high acid conditions[J].Oil & Gas Storage and Transportation, 2018, 37(2): 162- 168.
[15]罗旭。电磁法水下管道埋深检测及防腐层缺陷定位技术研究[D].成都:西南石油大学, 2013: 58-61.LUO X. Study on electromagnetic method for depth and coatingdefect detection of submarine pipeline[D]. Chengdu: SouthwestPetroleum University, 2013: 58-61.
[16] PIKAS J. Technologies for diret assment monitoringtechniques carrier pipes within cased crossings[ EBOL]. (2009-03 ) [2020-03- 11]. https://www .researchgate.net/scientific-contributions/2099584331_ J_ Pikas.
[17]李永年,陈德胜,尚兵,李晓松。瞬变电磁技术在检测管体缺陷上的应用研究[J].管道技术与设备,2013(4):27-29.LIYN,CHENDS,SHANGB,LIXS.Studyoftheapplication tem technology to pipeline defect detection[J].PipelineTechnique and Equipment, 2013(4):27-29.
[18] 王丽,冯蒙丽,丁红胜,白世武,刘方明。 .金属磁记忆检测的原理和应用[J].物理测试,2007,25(2):25-30.WANGL,FENGML,DINGHS,BAISW,LIUFM.Theory and application of test for metal magnetic memory[J].Physic Examination and Testing, 2007,25(2): 25-30.
[19] 林俊明,林春景,林发炳,萨辉。基于磁记忆效应的一-种无损检测新技术[J].无损检测,2000, 22(7): 297-299LIN J M,LIN C J,LIN F B,SA H. A new nondestructivetesting technique based on magnetic memory effect[J].Nondestructive Testing, 2000, 22(7):297-299
[20]杨理践,刘斌,高松巍,陈立佳金属磁记忆效应的第--性原理计算与实验研究[J].物理学报,2013, 62(8): 399-405.YANG L J,LIU B, GAOS W, CHEN L J. First-principlescalculation and experimental study of metal magnetic memoryefects[J]. 2013, 62 (8): 399-405.
[21]任吉林,陈曦,宋凯。金属构件磁记忆效应影响因素研究[J].无i0l, 2006, 28(6): 15-18.REN J L, CHEN X, SONG K. Study on the influencing factorsofmetal magnetic memory effect of metallic structures[J].Nondestructive Testing, 2006.28(6): 15-18.
第一作者简介
吴志平,男,1971年生,教授级高工, 1994年毕业于西安公路交通大学桥梁工程专业,现主要从事长输油气管道保。护、管道维抢修、地质灾害等方面的管理工作。