金属管道作为石油油气输送工具,是工业生产与民用设施的重要组成部分。长距离布置的输送油气的管道大多处于复杂的土壤环境中,所输送的介质也多有腐蚀性,因而金属管道会逐渐減薄、穿孔或破裂,造成对管道的容量、性能、完整性及安全性的损害。
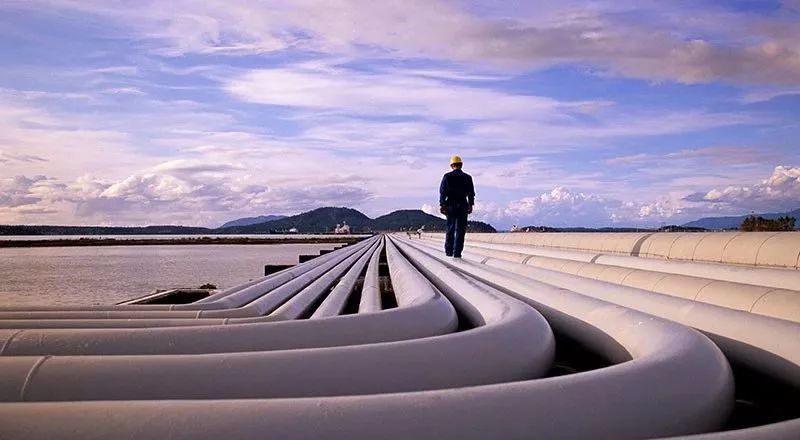
金属管道腐蚀是一个世界性的问题,随着时间的推移,金属管道的腐蚀是不可避免的,即使做了防腐涂层,其涂层也会逐渐老化而丧失防腐蚀性能。金属管道的腐蚀将严重影响其使用寿命,一旦管道发生腐蚀穿孔,就会造成油气的漏失,不仅发生运输中断,而且会污染环境,甚至可能引起火灾,对人民生命财产安全、社会稳定和工业生产构成威胁,造成严重的经济损失。国内每年因金属材料的腐蚀破坏造成的经济损失已高达约3万亿元。
为此,在管道建设迅速发展的同时,如何保证管道的安全运行也成为越来越重要的问题。管道发生腐蚀后,通常表现为管道的管壁变薄,出现局部的凹坑和麻点。管道内腐蚀检测技术主要是针对管壁的变化来进行测量和分析的。
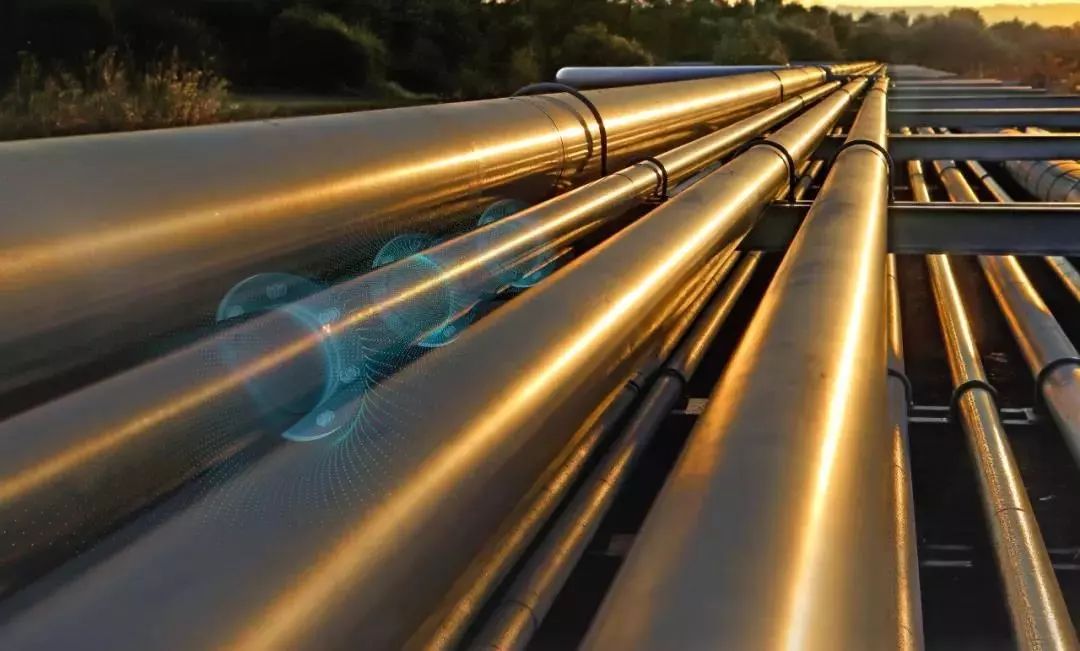
目前,国内外在管道腐蚀方面已做了大量的研究,开发了各种各样的检测方法,如漏磁通法、超声波法、涡流检测法、磁记忆法、激光检测法和电化学检测法等,利用这些方法对在用管道的腐蚀程度进行检测,可有计划、有针对性地更换危险管段,防止事故发生。但上述方法都由于本身的检测原理及技术特点而存在一定的局限性。
除此之外,相比于国外,国内的地下金属管道监测技术仍处于起步探索阶段,大部分管线不仅没有使用网络系统进行监控,而且各种检测金属管道腐蚀的技术也大都停留在管外检测阶段,不仅方法陈旧落后,而且无法对埋地金属管道的腐蚀及安全性进行及时准确地检测与评估。
基于此,爱德森(厦门)电子有限公司和集美大学的研究人员设计了一种监测管道壁厚变化、腐蚀减薄和结构应力分布变化的管道集成检测系统,包含超声波测厚、涡流、电化学腐蚀速度监测和磁记忆应力诊断等4种方式,同时获得多方面有关管道腐蚀及安全性的信息,显著提高了检测的可靠性及效率。另外,在实施管道监测时,将多套监测模块布置在不同管道及管道上的不同位置,从多参数识别到数据融合,检测人员可对被监测管道的总体安全做出综合判断,在管道的腐蚀状态监测、健康监测和寿命预估等方面将有广泛的应用前景。
1 管道的腐蚀机理
管道腐蚀是指管道金属与周围接触到的气体或液体进行化学反应而发生腐蚀的过程。基本上可分为化学腐蚀和电化学腐蚀两大类。
化学腐蚀
化学腐蚀指管道金属单纯由于化学作用而引起的腐蚀,如:金属在干燥空气中或非电解质溶液(酒精、汽油、苯等)中的腐蚀;铁在高温下跟氧气直接反应生成氧化铁(皮状),钢铁或其他金属与氯气直接反应而发生腐蚀,铁、铝、锌等在干燥空气中也可被氧化而形成一层氧化膜。总之,化学腐蚀的化学反应比较简单,仅仅是金属跟氧化剂之间的氧化-还原反应。
电化学腐蚀
金属接触到电解质溶液,发生原电池效应,比较活泼的金属原子失去电子而被氧化,腐蚀过程中有电流产生,叫电化学腐蚀或电化腐蚀。如钢铁在潮湿空气中,表面吸附一层薄薄的水膜,纯水是弱电解质,能电离出少量的H+和OH-,同时由于空气里的CO2溶解,使水里H+增多,结果在钢铁表面形成了一层电解质溶液薄膜,其跟钢铁的铁和少量的碳(或其他杂质)恰好构成了原电池。因此,钢铁制品的表面就形成了无数微小的原电池。在这些原电池里,铁是负极,碳是正极,这时作为负极的铁就失去了电子而被氧化;在正极,溶液里的H+得到电子而被还原,最后产生氢气在碳的表面放出,这种腐蚀通常叫析氢腐蚀。如果钢铁表面水膜的酸性很弱或呈中性,在负极上也是铁失去电子而被氧化成Fe2+,而在正极上主要是溶解于水膜里的氧气得到电子而被还原,这种腐蚀叫吸氧腐蚀。
从本质上看,化学腐蚀和电化学腐蚀都是铁等金属原子失去电子而被氧化的过程,而电化学腐蚀过程伴有电流产生,化学腐蚀过程却没有电流产生,在一般情况下,两种腐蚀往往同时发生。造成电化学腐蚀的外因主要是大气中的CO2、O2等成分及材料表面的灰尘、锈蚀伤痕等;内因则是金属材料的化学成分及材料内部的组织不均匀性等。
由金属管道的腐蚀机理可知:
一方面,金属管道的缺陷会增加管道的渗透性,加速金属管道的碳化和侵蚀性介质的侵蚀,使金属管道的腐蚀加重;
另一方面,金属管道的腐蚀膨胀又会造成进一步开裂,金属管道的缺陷与腐蚀相互作用,将加剧金属管道的腐蚀破坏。
以上过程循环作用,使金属管道结构的耐久性大大降低。
2 管道的检测方法
超声波测厚
超声波测厚是利用超声脉冲反射原理,超声波脉冲在不同的钢材中都会有一个固定的传播速度,探头发射的超声波在钢材中传播并到达材料分界面时会被反射回探头,测量超声波在材料中传播的时间可以确定被测钢材的厚度。超声波测厚在管道检测中已非常成熟,只要能保证超声波以恒定速度在材料内部传播,就可使用此方法对管道进行壁厚测量。
涡流监测
涡流监测可以利用套在金属管棒材上的涡流线圈,拾取金属棒材监测点的涡流时间序列信号,可以对所采集的涡流时间序列信号进行分析,建立涡流时间序列信号与金属棒材腐蚀进展规律之间的关系,进而从涡流监测信号的变化分析判断金属管道的腐蚀进展情况,并采取相应的处理措施。
电化学检测
管道腐蚀是一个电化学过程,电化学测量是反映电化学本质过程的有力手段。电化学方法通过测定管道腐蚀体系的电化学特性来确定管道腐蚀程度或速度。电化学方法具有测试速度快、灵敏度高、可连续跟踪和原位测量等优点。管道腐蚀的电化学检测方法主要有自然电位法、交流阻抗谱技术和极化测量技术等。笔者采用电化学实时监测管道pH值、氯离子浓度、腐蚀电位、腐蚀电流密度等参数,通过观测电化学腐蚀检测信号间接判断受检管道的腐蚀量,多参数综合评价受检管道的腐蚀倾向性、腐蚀速度、安全性及服役寿命。
磁记忆应力诊断
磁记忆应力诊断技术是一种新型的利用铁磁材料的内在漏磁信息对材料进行检测和评价的无损检测技术。利用金属管道的磁弹性和磁机械效应,通过载体与地磁场共同作用下产生的磁记忆现象来确定管道表面或近表面的应力集中部位。磁记忆应力诊断技术可以发现在用管道的应力集中区域的宏观缺陷,在管道早期诊断检测中具有很大的优势,检测结果可为其他检测技术提供参考。
3 在用管道的无损云检测
在长距离输油气管道上按一定的间距布置一个检测点,并定时采集管道上各个点和各种类型(即多源数据结构的采集信号)的检测数据,并将采集的数据通过网络向云端服务器传送,可以通过服务器所收集的检测数据对整条管道从时间和空间等多维度方面进行分析判断,了解整个管道的质量状态。这种建立在基于互联网、物联网、大数据、云计算和无损检测集成技术的检/监测系统就是一种无损云检测系统全新概念,通过各种先进的物理与化学无损检测集成技术和云检测、监测的结合,将智能终端采集的数据送至云端,进行数据管理、分析、处理、存储、评估、预测、交互等,实现信息共享和远程服务。
按照检测计划,将目前常规的超声波测厚仪、电化学检测仪及磁记忆应力诊断仪,从集成技术的角度加以分解细化,将其专有部分设计为云检测终端,该终端包含检测传感器、信号发生、信号接收、调理电路及无线信号传输等基本组件,其他组件如参数控制、信息融合、专家评估软件系统、信息反馈、传播、共享、存储、打印输出等组件集成到云端服务器和数据库中,图1为无损云检测网络结构示意,图2为云检测与评价服务技术平台结构示意。
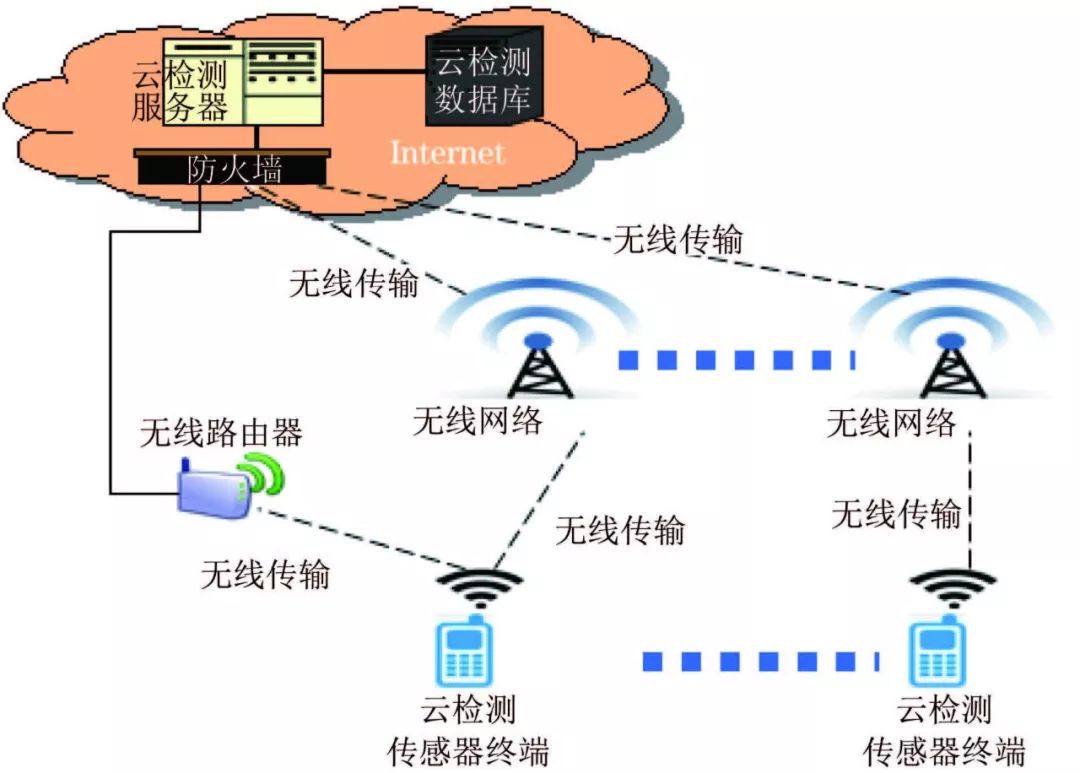
图1 无损云检测网络结构示意
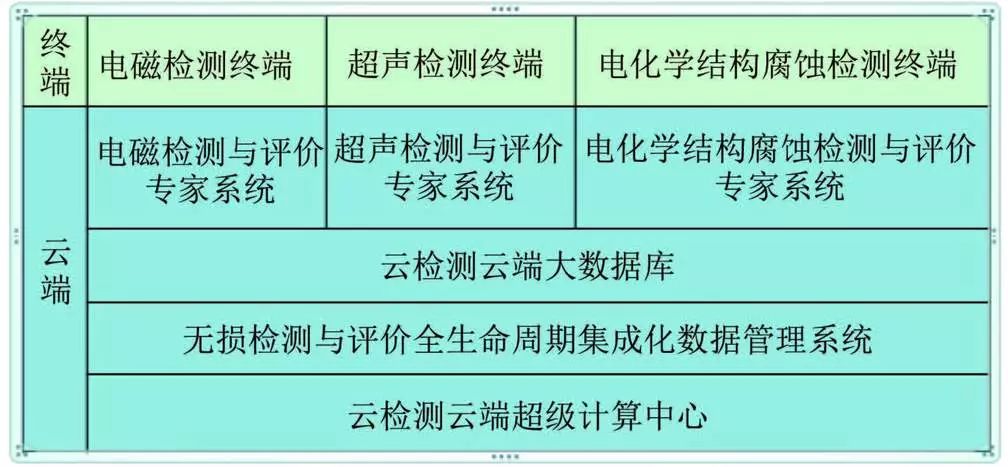
图2 云检测与评价服务技术平台结构示意
检测方案
系统将超声波测厚传感器、电化学腐蚀检测传感器及磁记忆传感器、信号发生、信号接收、集成检测仪和无线信号传输等组成的终端预埋固定在被检管道周围,通过云端远程控制无线信号传输装置启动检测任务,检测结束后,通过无线信号传输装置,将终端的超声波测厚信号、电化学腐蚀检测信号、磁记忆诊断信息等发送到云检测平台,从而实现在用管道的远距离遥感检测。
(1)
通过云端无线信号控制装置,控制集成检测仪定时激励超声波测厚传感器检测在用金属管道,超声波测厚传感器将采集的检测信号传至集成检测仪,通过终端无线信号传输装置,并集成检测仪将超声波测厚信号发送至云检测平台进行处理和存储,检测人员通过云端观察管道的壁厚变化判断被检管道的变薄程度和趋势。
(2)
通过云端无线信号控制装置,控制集成检测仪定时激励电化学腐蚀检测传感器检测在用金属管道,电化学腐蚀检测传感器将采集的检测信号传至集成检测仪,通过终端无线信号传输装置,集成检测仪将电化学腐蚀检测信号发送至云检测平台进行处理和存储,检测人员通过云端观察电化学腐蚀检测信号,间接判断被检管道的腐蚀量。
(3)
通过云端无线信号控制装置,控制集成检测仪定时激励磁记忆诊断传感器检测在用金属管道,磁记忆诊断传感器将采集的检测信号传至集成检测仪,通过终端无线信号传输装置,集成检测仪将磁记忆诊断信息发送至云检测平台处理和存储,检测人员通过云端观察磁记忆诊断信息,间接判断被检管道是否存在缺陷或应力集中区。
(4)
检测人员通过远程用户终端比对超声波厚度变化监测曲线、电化学腐蚀检测信号监测曲线及磁记忆检测信号,从而预测被检管道的使用寿命。
工程应用
在工程应用方面,爱德森(厦门)电子有限公司与厦门大学已成功研制出在用金属管道超声、涡流、电化学、磁记忆综合监测终端(见图3),并使用智能手机作为检测系统的用户终端(见图4)。将物联网技术和设备远程智能维护服务有效结合,管理人员通过手机、计算机就可以远程掌握在役设备的运行情况,用于设备报警、故障报警等。
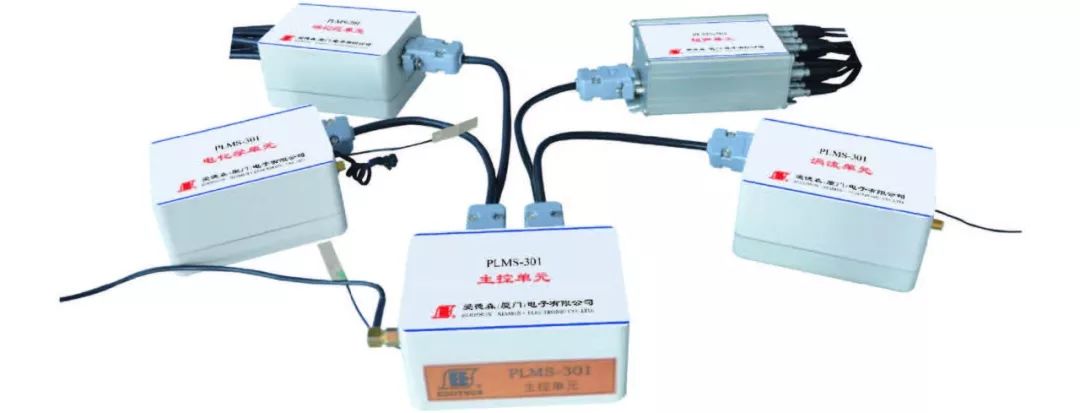
图3 在用金属管道超声、涡流、电化学、磁记忆综合监测终端外观
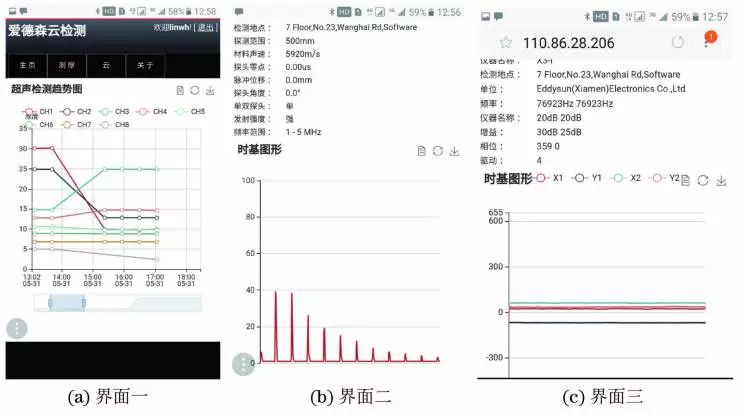
图4 管道实时超声、涡流、电化学、磁记忆监测信息-手机查询界面
在实施金属管道监测时,将多套监测模块布置在不同金属管道及金属管道上的不同位置,采用无线信号传输方式,实现对在用金属管道的腐蚀与减薄程度的远程、长期原位监测(见图5)。从多参数识别到数据融合,检测人员可利用智能手机来查询金属管道实时超声测厚和电化学腐蚀速率监测信息,对被监测金属管道的总体安全性做出综合判断,并进一步预测或修正被检金属管道的使用寿命。
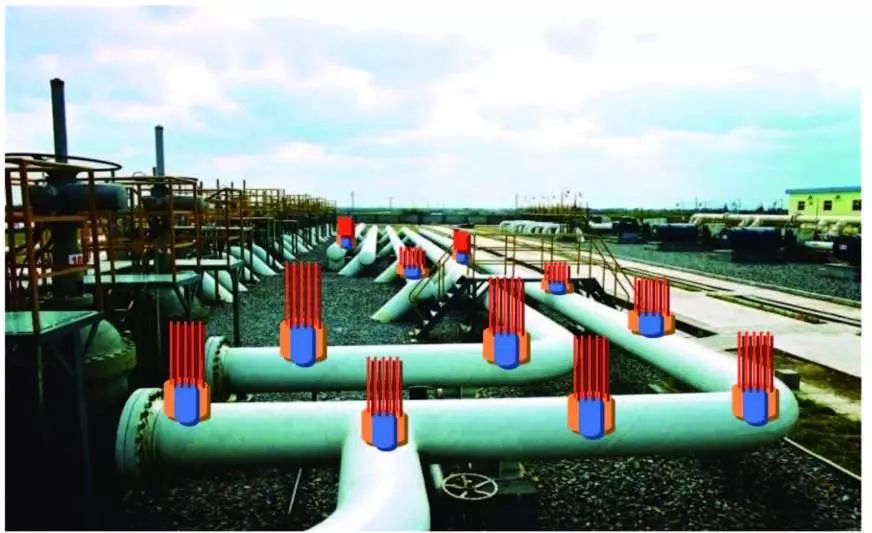
图5 管道实时监测系统布置
基于大数据、云检测技术的城市管网云监测系统将改变以往检测设备落后、功能单一、监测方法不完善的现状,将监测系统与预警系统联动,提升系统的安全性,加强系统的信息化管理程度。实现对管网运行状态的实时监控,并进行大数据动态监测分析,为管网突发事件处理、灾害预警综合防御、相关信息分析、管网合理规划设计提供依据;实现对管网图籍资料等信息进行科学有效地管理,为精确判断管网中出现的灾情及损坏提供准确信息和决策支持。
结 语
随着工业智能化的发展,在互联网、物联网以及大数据分析的时代背景下,面对检测领域的迫切需求,无损云检测旨在构建无损检测技术物理资源和管理的资源池,其广泛应用将会对无损检测的发展带来深远影响。将超声波测厚、涡流、电化学腐蚀速度监测和磁记忆应力诊断等4种技术集成应用于在用管道监测中,实现了对在用管道腐蚀及安全性的云检测及评价,这在金属管道的腐蚀状态监测、健康监测和寿命预估等方面将有广泛的应用前景。
作者:林俊明1,张开良1,林发炳1,李寒林2,郑水冰1,吴晓瑜1
1.爱德森(厦门)电子有限公司
2.集美大学 轮机工程学院
作者简介:林俊明(1956-),男,研究员,主要从事电磁无损检测及其集成技术和云检测方面的研究。
来源:《无损检测》2019年9月