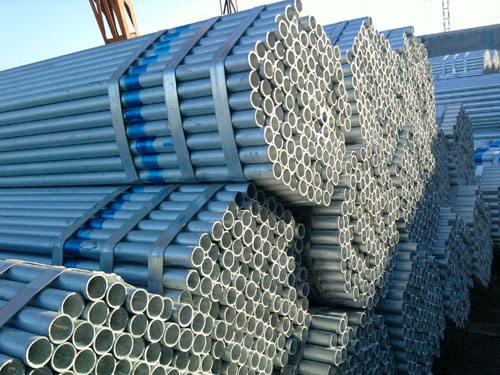
1.石油行业腐蚀的危害性
据有关部门统计,金属设备、机具的平均年腐蚀报废率大致在4%左右,如果我们将腐蚀对国民经济造成的损失降低一个百分点,即由4%降到3%,就可以挽回600-800亿的腐蚀损失。石油工业已经认识到腐蚀是一个非常严重的问题,而钻杆和井筒的油井管柱腐蚀造成的经济损失尤为突出。一旦发生失效,就会造成:人员伤亡、环境污染、废井、停钻、掉井等后果。全国油田每年大约发生数千起腐蚀失效事故,除浪费大量的原材料外,有的还会造成严重的环境污染和人身伤亡事故等严重后果。据不完全统计,中国每年石油行业由于腐蚀造成的直接经济损失就要上十亿元,加上间接损失,数额更是相当惊人的,是各个部门都不能忽视的。
2、石油专用管腐蚀状况
油套管、集输管线、储罐的腐蚀主要是油气井产出物、浅层水、注入液等产生的腐蚀,主要介质有H2S、CO2、溶解氧和SRB等。钻具往往会受到包括钻井液在内的许多介质的作用,发生点蚀和腐蚀疲劳,重力拉伸和旋转等应力腐蚀破坏和断裂等。
2.1 油管/集输管线的腐蚀特点
产出水中有硫酸盐还原菌、二氧化碳、碳酸氢根离子和氯化物的侵蚀作用,共同引起的垢下腐蚀和丝扣腐蚀。当井中出现硫化氢时(特别是气井),油管破坏具有危险特征,腐蚀破坏的主要原因是氢脆HIC和SSCC。油管在自重、外部压力和其他因素作用下处于复杂的应力状态,拉应力是促使金属保护膜破坏和基体腐蚀的重要因素。油管和集输管线还存在结垢,当出现Sr2+、Ba2+垢时无法用常规的酸洗方法清理,严重影响正常生产。油管和集输管线还存在结蜡现象,高的清蜡作业频次严重影响正常生产。油管和集输管线的冲刷腐蚀也是常见的腐蚀失效形式,有磨蚀、气蚀等。某油田油管内壁腐蚀形态(CO2腐蚀)典型的均匀内腐蚀典型的腐蚀穿孔。
2.2 钻杆的腐蚀特点
主要的失效形式:过量变形、刺穿或断裂及表面损伤。过量变形是由于工作应力超过材料屈服极限引起;刺穿或断裂在钻柱失效事故中所占的比例较大,主要由于应力腐蚀、疲劳和腐蚀疲劳等原因造成。表面损伤主要有腐蚀、磨损和机械损伤。 70%的事故是由钻杆内加厚过渡区部位刺穿或断裂引起的。刺穿的先决条件是已存在裂纹。钻杆外壁的腐蚀较轻并且均匀,而钻杆内壁表面的腐蚀很不均匀,内加厚过渡区与管体交界处的腐蚀较严重,有许多点蚀坑,而裂纹正起源于这些点蚀坑底部。内涂层是解决钻杆腐蚀疲劳失效的主要解决方案。
2.3套管的腐蚀特点
套管腐蚀主要是由于产出水(地层水)中硫酸盐还原菌以及CO2、碳酸氢根离子和氯化物的侵蚀作用,共同引起的垢下腐蚀造成的。丝扣腐蚀严重,主要由于细菌腐蚀、缝隙腐蚀和应力腐蚀的综合作用。周期性摩擦,加速了套管的腐蚀穿孔,特征是具有方向性。固井质量不高造成套管水泥层的保护作用失去。
2.4 油井管在储运过程中遭受的外腐蚀
油井管在储存、运输过程中;遭受的腐蚀形态:大气腐蚀(O2腐蚀)、垢下腐蚀(防护层失效、热轧氧化皮等表面附着物的局部氧浓差电池形成)、盐雾(海运过程中)、酸雾腐蚀(重庆典型);应当引起制造商(出厂长效涂敷防腐涂层、出口海运、外观质量)、用户(存放、运输应采取防护措施)的重视。对外防护涂层的要求:良好的耐水性(7d);良好的耐盐雾性(1~2级);良好的耐候性(各种环境不变色);良好的附着力(1级);良好的抗冲击性(3J)。
3. OCTG服役环境中的腐蚀因素
3.1溶解氧:钻井液中的溶解氧是钻杆腐蚀的主要原因,生成氢氧化铁沉淀。它有两种加速腐蚀机理,一是氧的去极化作用;二是氧在阳极处直接攻击金属。
3.2硫化氢:在硫化物存在的环境中,氢原子进入钢材而造成氢脆。维持钻井液的PH值在8以上是控制硫化氢腐蚀的有效方法。另外,钢材的硫化物应力开裂与温度、外部应力或残余应力及钢材本身的金相组织和化学成分密切相关。
3.3二氧化碳:溶于水后形成碳酸,腐蚀特征是坑蚀。腐蚀强度取决于二氧化碳的分压和PH值。
3.4 SRB:在引起油套管的腐蚀中,细菌腐蚀特别是硫酸盐还原菌(Sulfate-reducingBacteria,SRB)是一种主要的腐蚀性细菌。
4. OCTG腐蚀的主要影响因素
4.1 PH值:氢离子是阴极去极化剂,一般PH值越小,金属腐蚀越严重。当pH值大于6.6时,腐蚀速度开始降低。
4.2 Cl- 、总矿化度:Cl-是破坏钝化膜的主要因素,是产生点蚀坑的加速剂,在许多环境下如CO2腐蚀,它是破坏CO2腐蚀膜和加速蚀坑的主要因素。矿化度增加,提高了液体导电性,有害离子的增加,加速腐蚀;易产生沉淀,发生垢下腐蚀。
4.3温度:通常腐蚀速率随温度升高而增大。主要因为粒子扩散速度增大,反应加快。
4.4流速:这是一个极其重要而又复杂的因素。它包括了物理、机械和电化学内容,主要有以下三种形式的破坏,即气蚀、磨蚀和腐蚀。
4.5溶解氧:溶解氧浓度是腐蚀的主要影响因素,钻井泥浆、污水回注的脱氧环节显得非常重要。
4.6其它:如含水、保护膜、杂质、含氧、细菌等影响因素。
5.OCTG的腐蚀机理
5.1电化学腐蚀为主的腐蚀机理:以钢材的铁素体为阳极,阴极是电位较高的碳素体,形成了腐蚀电偶,阳极逐渐溶解,即电化学失重腐蚀。
5.2 CO2腐蚀特点:局部腐蚀,呈现点蚀、轮癣状腐蚀和台面状坑蚀,穿孔率高。
5.3 H2S腐蚀特点:形成应力腐蚀开裂(SSCC)。氢硫酸容易电离,产生的H+导致低强度钢的氢腐蚀和高强度钢的氢脆。
5.4介质中水的作用:
①水是电化学反应必不可少的媒介。
②与CO2腐蚀都是通过与CO2溶解在水中,形成酸性物质(碳酸和氢硫酸)而发生的腐蚀作用。
③酸性条件加剧电离和电化学腐蚀。
5.5硫酸盐还原菌(SRB)腐蚀特点和机理:套管长期处于死水缺氧状态,硫酸盐还原菌(SRB)大量繁殖,将硫酸盐还原为H2S,产生严重腐蚀。表现形式为低强度钢的氢腐蚀与高强度钢的氢脆。
5.6应力腐蚀:由于钻具自身具有很大的重量,由于钻具的旋转,特别是定向井的钻探,钻具和地层或套管的摩擦力很大,也就是说具有很大的应力存在,在腐蚀介质中的交互作用致使腐蚀开裂。
5.7机械磨损和人为碰伤:特别是有应力存在下局部磨损或划伤会成为腐蚀失效的发源地。
6. 油井管防腐的基本措施
6.1遵循标准设计选材,不同的服役环境选用不同的材质和钢级。在腐蚀环境下也应用高合金管如不锈钢管(成本是碳钢的4倍以上),但不锈钢管也存在Cl-的点腐蚀问题。
6.2采取适当有效的防护涂层。如防腐涂层和金属镀层保护技术;
6.3采取其它辅助手段:如加入缓蚀剂和封闭式注水系统,减少O2、CO2、H2S的溶解量;使用硫酸盐还原菌杀菌剂。
6.4采用阴极保护,建立腐蚀监测系统,把握腐蚀动态,防患于未然。
7. 油井管对涂层的性能要求
油井管防腐实质上就是屏蔽阻隔。就是阻隔H2S、CL-与CO2及其溶解于水形成的酸性化合物与管材本体的接触。具体要求是:涂层表面光滑、无缺陷和好的附着力;具有一定的耐温性;对环境中腐蚀介质具有良好的阻隔性;涂层材料的化学性质稳定;具有可靠的机械性能。
8.内防腐涂层的作用
由于涂层的电绝缘性,可以防腐耐蚀;由于表面光滑,可提高流体效率;由于表面光滑和化学性质,可减少结蜡;由于涂层的化学性质可减少结垢;可提高管子重复使用率;避免打捞和修井作业工作;有利于提高注水水质。