陶瓷材料拥有许多极具吸引力的性能,包括高比刚度、高比强度和在许多环境下的化学惰性。同时,因其相对于金属的低密度、高硬度和高抗压强度,使其在装甲系统上的应用十分具有吸引力,己成为一种广泛应用于防弹衣、车辆和飞机等装备的防护装甲[1-2]。在20世纪60年代,B4C最先用于设计防弹背心,之后装配到飞机飞行员的座椅上。之后,又将陶瓷面板与复合材料背板共同构成防弹陶瓷复合装甲,且于70年代后被美国等西方军事强国应用于运兵车、坦克及军机等。陶瓷装甲主要应用于装甲车辆,在实际应用中常以复合装甲的形式出现,如英国“挑战者”坦克、EE-T1奥索里约主战坦克等。陶瓷作为装甲防护材料的主要优势是强度和硬度高、耐磨、密度小等,而易破碎、抗多发打击性能弱的劣势在一定程度上限制了其应用。目前,防弹陶瓷主要朝着提高抗多发打击性能、减轻质量及降低成本这3个方面进行。国内外现阶段主要使用的特种防弹陶瓷有B4C、Al2O3、SiC、TiB2、AlN、Si3N4、Si-alon等。
俄罗斯“台风”战车的主体部分由钢板和陶瓷装甲提供防护,其陶瓷装甲可以承受30 mm 口径炮弹袭击。2016年,中国陆航的武直10在座舱肩膀两侧加装了防弹陶瓷装甲板,可抗12.7 mm大口径机枪子弹的打击,提高了飞行员的防护能力。但是随着弹丸材料和性能的逐步升级,装甲材料也面临着大的挑战。例如目前穿甲弹的弹丸使用高密度合金钢、碳化钨或钨、贫铀合金钢等材料,弹丸初速为0.9~1.8 km/s,穿甲厚度达1 m以上,穿甲能力强、飞行速度损失小,极具威胁力。破甲弹虽然弹着速度不高,但其利用炸药的锥型中空装药的聚能原理,爆炸时形成一束高速金属射流来击穿装甲。现代大威力破甲战斗部的静破甲威力可击穿1.2 m厚度以上的装甲。碎甲弹则是通过塑性炸药在装甲板上产生冲击波,利用超压崩落坦克装甲内层碎片来达到杀伤破坏目的。而一发装4 kg药的122 mm的碎甲弹,在100 mm厚的装甲上起爆后,能在装甲背面崩下厚度为10~30 mm、质量为4~6 kg的碟形碎甲和几十块小碎片,并对1.3~1.5倍口径厚的装甲起破碎作用。
面对威胁力日益提高的“矛”,必须铸就坚不可摧的“盾”以提高军事防护性能和安全等级。为此,作者综合分析了国内外普遍使用的装甲陶瓷的制备工艺、材料性能、发展趋势,以期对防弹陶瓷未来的发展提出预期和展望。
1 陶瓷材料的防弹原理
装甲防护的基本原理是消耗射弹能量、使射弹减速并达到无害。绝大部分传统的工程材料,如金属材料通过结构发生塑性变形来吸收能量,而陶瓷材料则是通过微破碎过程吸收能量。装甲陶瓷的吸能过程可分为3个阶段[3]。1)初始撞击阶段:弹丸撞击陶瓷表面,使弹头变钝,在陶瓷表面粉碎形成细小且坚硬的碎块区的过程中吸收能量;2)侵蚀阶段:变钝的弹丸继续侵蚀碎块区,形成连续的陶瓷碎片层;3)变形、裂缝和断裂阶段:最后陶瓷中产生张应力使陶瓷碎裂,随后背板变形,剩余的能量全部由背板材料的变形所吸收。
弹丸撞击陶瓷的过程中,弹丸和陶瓷均受到破坏。因为陶瓷本身的脆性,其受到弹丸冲击时发生断裂而不是塑性变形。在拉伸载荷作用下,断裂首先发生在非均质处如孔隙和晶界上。因此,为使微观应力集中降低到最小程度,装甲陶瓷应当是孔隙率低(达理论密度值的99%)和细晶粒结构的高质量陶瓷。陶瓷吸收能量的能力与陶瓷的硬度、弹性模量有关,可以用M 值(弹道质量因素)来衡量陶瓷的抗弹性能:
M = EH/ρ 。(1)式中:E 是弹性模量;H 是硬度;ρ 是密度。可看出,陶瓷的弹性模量和硬度越大,密度越小,抗弹性能越高,陶瓷对于动能的吸收能力越强。
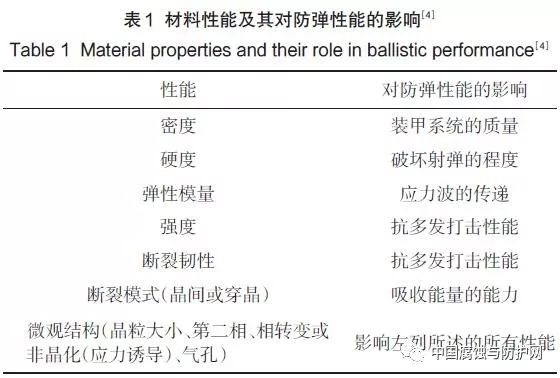
表1列出了材料性能及其对防弹性能的影响。陶瓷的硬度越高,弹丸撞击陶瓷时弹头越易钝化和破碎,弹丸侵蚀陶瓷的过程中因磨损犁削作用消耗的能量越多[5]。文献[3]对防弹陶瓷的力学性能提出了一个具体的要求范围:弹性模量E≤280 GPa,硬度H≥2 000kg/mm2,密度ρ≤3 g/cm3。但公式(1)忽视了断裂韧性对防弹性能的影响。事实上,陶瓷的高断裂韧性可延迟弹丸撞击陶瓷的断裂时间,提高陶瓷的断裂耗能和抗弹阻力,使陶瓷对弹丸的磨蚀和犁削作用增强,从而消耗更多的弹丸动能,提高陶瓷的抗弹性能。
2 单相陶瓷的弹道性能及制备技术
用于装甲防护的单相陶瓷主要包括氧化铝、碳化硼和碳化硅,表2为3种陶瓷的特征性能。
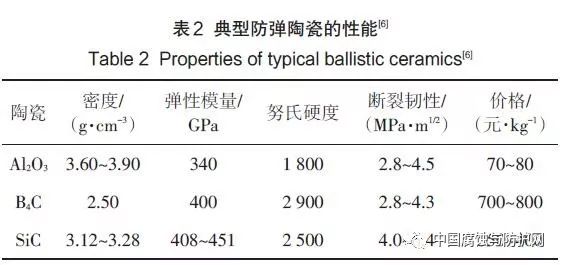
氧化铝陶瓷作为离子键化合物,化学键力强,熔点高(2050 ℃),具有良好的抗氧化性和化学惰性[7],烧结制品表面光洁、尺寸稳定、价格低廉,故广泛应用于各类装甲车辆和军警防弹服等。但Al2O3较高的密度、偏低的硬度和断裂韧性,使其抗弹性能较低。
碳化硼是强共价键化合物,共价键高达93.9%,具有高的熔点,超常的硬度(35~45 GPa),仅次于金刚石和立方氮化硼,尤其是近于恒定的高温硬度以及良好的力学性能,使B4C成为发展潜力很大的高温耐磨材料之一。B4C的密度在几种常用装甲陶瓷中最低,加上弹性模量较高,使其成为军事装甲和空间领域材料方面的良好选择[8]。B4C存在的主要问题是价格昂贵(是氧化铝的10倍左右)、脆性较大,限制了其作为单相防护装甲的广泛应用[9]。
碳化硅共价键极强,在高温下仍具有高强度的键合,这种结构特点赋予了碳化硅陶瓷优异的强度、高硬度、耐磨损、耐腐蚀、高热导率、良好的抗热震性等性能;同时碳化硅陶瓷价格适中,性价比高,是最有发展潜力的高性能装甲防护材料之一[10]。SiC陶瓷在装甲防护领域具有广阔的发展空间,在单兵装备和特种车辆等领域的应用趋于多元化。作为防护装甲材料时,考虑到成本及特殊应用场合等因素,通常将小块排布的陶瓷面板与复合材料背板黏结成陶瓷复合靶板,以克服陶瓷由于拉应力引起的失效,并确保弹丸侵彻时只粉碎单块而不破坏装甲整体。
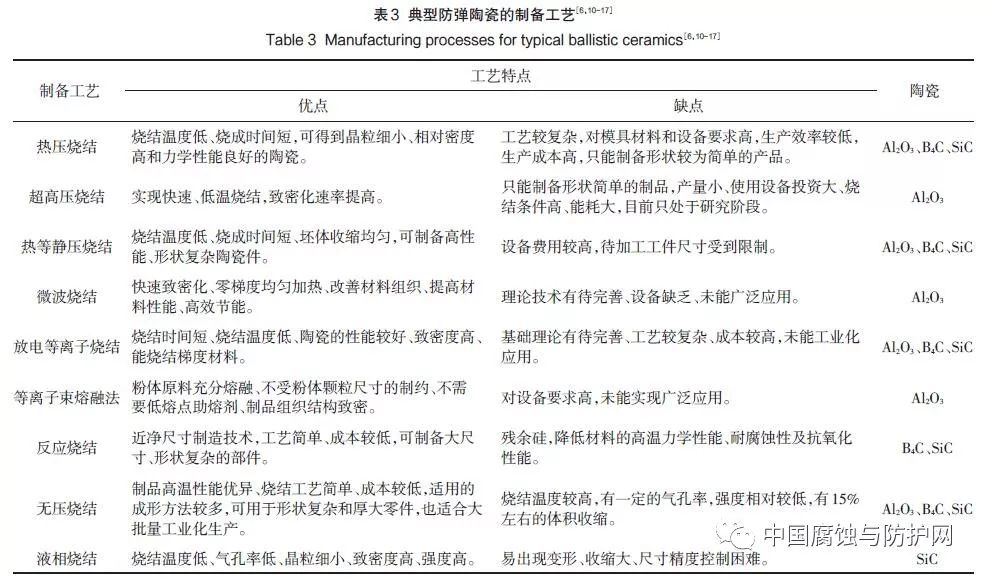
表3 对3种单相防弹陶瓷的制备工艺进行了比较。一般来说,热压B4C和固相烧结SiC中可能出现石墨和碳夹杂物;反应结合的材料一般不具有气孔,但会存在残余硅作为次要相。次要相的存在会导致陶瓷弹性模量的降低,降低程度取决于次要相的类型,其中气孔会最大程度地降低弹性模量。晶粒尺寸对于陶瓷的硬度和强度有一定的影响。强度与晶粒尺寸的关系遵循Hall-Petch定律,即晶粒尺寸的增加会降低材料的强度[18]。因此,加压烧结在获得细晶陶瓷方面具有显著优势。细晶陶瓷提高断裂韧性的机理是裂纹沿晶界的路线更曲折,需要消耗更多的能量以形成更大的断裂面。文献[4]中的显微照片显示热压烧结B4C和固相烧结SiC出现了穿晶断裂,而和液相烧结SiC出现了晶间断裂,证实了热压SiC和液相烧结SiC的断裂韧性比和固相烧结SiC的断裂韧性更高,由此说明了两种断裂模式中,晶间断裂的断裂韧性比穿晶断裂的高。
从陶瓷材料制备工艺的特点可以看出,目前工艺发展较为成熟的是反应烧结、无压烧结和液相烧结,这3种烧结方式的生产成本较低,制备工艺较简单,实现大批量生产的可能性较高。热压烧结和热等静压烧结相对来说会受到产品尺寸的限制,生产成本较高,成熟性较低,超高压烧结、微波烧结、放电等离子烧结和等离子束熔融法综合来说成熟性最低,是较为新颖的制备手段,但对于技术和设备的要求较高,需要投入的生产费用高,实现批量化的可行性较低,常用于实验探索阶段,对实际应用意义不大,较难实现产业化。
3 多相陶瓷的制备及性能特点
尽管单相陶瓷具备一定的防弹能力,但共性的问题是断裂韧性低、脆性大,因此,防弹陶瓷的强韧化一直是研究的热点方向。强韧方法主要包括多元陶瓷体系复合、功能梯度陶瓷、层状结构设计等。Medvedovs-ki[19]对SiC-Al2O3、SiC-Si3N4-Al2O3、SiC-Si-Al2O3和SiCSi3N4-Si-Al2O3这些碳化硅基的复合材料进行了研究,通过无压烧结和反应烧结实现制备,并进一步证实其物理性能如硬度、声速等,以及吸收能量的能力比单一的材料体系都有一定程度的提高,反应烧结SiC基复合陶瓷的防护系数可达到3 级或4 级,制得的SiCSi3N4-Al2O3和反应烧结SiC也具有很好的抗多发打击性。Huang等[20]在1 500 ℃下通过无压烧结制得4层和11 层的Al2O3-ZrO2 功能梯度材料,证实了90%Al2O3-10%ZrO2 的硬度可以达到15.12 GPa,50%Al2O3-50%ZrO2的断裂韧性可以达到4.7 MPa·m1/2,拥有相同面密度(4.64 g/cm3)或厚度(11 mm)的梯度材料的能量吸收达到最大,防弹性能最优异。Gupta等[21]运用放电等离子烧结法制得TiB2-Ti功能梯度材料,通过小口径射弹冲击的弹道深度测试,得到TiB2-Ti和TiB2基复合材料的弹道效率η 均在5.1~5.9,与其他防护陶瓷材料相比,除了比B4C稍差一点,TiB2基复合材料的弹道深度更小、弹道效率更高、防弹性能更佳。Pettersson等[22]运用放电等离子烧结技术制备得到Ti-TiB2功能梯度材料,并进行力学性能和7.62 mm口径射弹的防弹测试,证实了SPS-(Ti) 0.05(TiB2)0.95的硬度为26 GPa,断裂韧性为4.5 MPa·m1/2,弯曲强度为640 MPa,各性能均优于HIP-TiB2,防弹性能优异。Sano等[23]采用粗晶和细晶两类AlN粉体与TiB2粉体经过热压烧结制备得到不同配比的TiB2-AlN 复合材料,其中50%TiB2/50%AlN(粗晶AlN粉体)的断裂韧性达到了7.0 MPa·m1/2,比预期高出了3.12 MPa·m1/2,整体复合材料的抗弯强度和抗弹深度等的测试结果都明显优于单相的TiB2或AlN材料。McCauley等[24]通过放电等离子烧结成功制得了密度接近98%的TiB2/TiB/Ti功能梯度材料,制得的梯度材料层数不同、配比不同。观察结构发现,材料发生了分层现象。在防弹测试中,4层和6层梯度材料的TiB2顶层显示出与单相TiB2一样优异的防弹性能。
为进一步提高陶瓷的断裂韧性,Orlovskaya 等[25]设计了层状结构的B4C-SiC复相陶瓷材料,将不同成分的陶瓷轧制成薄片,薄片叠层后热压烧结,综合考虑陶瓷的热膨胀系数、弹性模量、泊松比、密度、装甲总体厚度,确定组分层的成分与厚度,得到了具有高压缩残余应力(高达650 MPa)和低拉伸残余应力(低于150MPa)的3层或9层陶瓷材料。这种B4C-SiC层状材料存在大量界面,为多重开裂创造了机会。许多微小脆性断裂的累积效应能够使层状材料拥有超越整体韧性材料的能量吸收能力。文献[26]中指出,3层的B4C-30%(质量分数)SiC/B4C层状材料的断裂韧性可以达到(7.42±0.82)MPa·m1/2,在抗弹深度的测试中,含有约4%气孔率的B4C-30%SiC/B4C层状材料和高纯的致密B4C单相陶瓷的射弹深度几乎没有差异。
4 纤维增韧陶瓷复合材料
战争中人员和装备的快速安全移动对轻质结构防护材料提出了持续需求,纤维复合陶瓷材料则是提供能量吸收和质量减轻的最佳组合方式。用于增韧陶瓷的纤维主要包括玻璃纤维和碳纤维。如轻型车辆吉普的面板通常都是基于S-2玻璃纤维(65%的SiO2,25%的Al2O3和10%的MgO),这会比传统的低碱铝硼硅酸盐E玻璃纤维(名义组成是54%的SiO2,14%的Al2O3,22%的CaO+MgO和10%的B2O3)有更高的断裂应变和弹性模量[27]。尽管玻璃纤维复合材料能有效应对轻武器,但对于大口径弹药和穿甲弹形成的严重威胁,玻璃纤维增韧则显得力不从心。
碳纤维由原料纤维高温烧成,经历了低温氧化、中温碳化、高温石墨化等工艺,具有强度高、模量高、密度低、耐高温、线膨胀系数小、热导率高等优点,可作为很好的补强增韧陶瓷材料[28]。增韧机理主要包括裂纹偏转、纤维桥联和纤维拔出3种机制。该复合材料能够最大限度地抑制陶瓷缺陷的体积效应,有效偏折裂纹和最终纤维拔出来消耗断裂能,从而发挥纤维的增韧和补强作用,改善复合材料的防弹性能。
5 透明陶瓷
随着材料制备技术的发展,更高性能的新材料不断被开发和研究。现代化战争对装甲系统的要求越来越高,不仅要求能够实现全方位的防护,还要求不能妨碍士兵们的行动能力,而化“被动”为“主动”,发展能预先识别目标,并利用诱饵触发和物理摧毁方式破坏来袭武器的“主动装甲”[29],成为作战中的一大优势。以氮氧化铝(AlON)和镁铝尖晶石(MgAl2O4)为代表的透明陶瓷已应用于装甲防护领域,既能保护人体又能随时观察敌情[30]。透明陶瓷因高的强度和硬度,已成为可替代防弹玻璃的具有发展潜力的防护材料,如面罩、导弹探测窗口、地面作战车辆保护窗、飞机的挡风玻璃和降落窗等,主要有单晶氧化铝(蓝宝石)、氮氧化铝和镁铝尖晶石[31-32]。
透明陶瓷的制备方法包括热压烧结、热等静压烧结、真空烧结、放电等离子烧结和微波烧结等,对光的透过性使透明陶瓷的制备工艺要求很高。除此之外,透明陶瓷要求原料纯度高、烧结致密度高,晶粒和晶界中的残余气孔、第二相和杂质等的含量越少越好,以最大程度地减小材料内部的散射、折射中心。因而,透明陶瓷对原料纯度、工艺先进性都是一次挑战和升级。
StraBburger[33]通过钢板框架将陶瓷/玻璃/聚碳酸酯固定在一起,用7.62 mm×51 mm AP钢芯射弹进行防弹性能测试。结果表明,前置层为烧结氧化铝时显示出最好的防护强度,其次是氮氧化铝、尖晶石和蓝宝石(单晶氧化铝)。同时,实验过程中运用了闪光X射线成像方法,使子弹的侵蚀过程实现可视化,为透明陶瓷装甲的系统优化提供了有利条件。Klement等[34]制备得到三明治结构的多层透明装甲,并进行两种子弹的防弹性能测试。具有蓝宝石前置层浮法玻璃的子弹侵蚀深度比具有玻璃前置层浮法玻璃的小,防弹性能得到了显著提高。6层8 mm厚的浮法玻璃和1层7 mm厚的蓝宝石前置层能够阻挡7.62 mm×51 mm AP8碳化钨芯射弹的冲击,3层8 mm厚的浮法玻璃和1层7 mm厚的前置蓝宝石层能够阻挡7.62 mm×54R B32 API硬质钢芯射弹的冲击。王雄高[35]讨论了利用聚合体和陶瓷等材料来减轻透明装甲系统的质量,并指出与传统的玻璃/塑料透明装甲系统相比,透明陶瓷已被证实在质量更轻的条件下能提供更强的防护能力。
6 结语
随着装甲系统轻量化、高效化的发展需求,防弹陶瓷的优越性愈加凸显。从单相陶瓷、多相陶瓷到纤维复合陶瓷,材料的断裂韧性在逐步提高,抗多发打击能力不断得到升级。随着材料制备技术的发展,更高性能的新材料不断被开发和研究。纳米材料、层状结构为材料设计者提供了许多新的选择,用于创造更加奇特的复合材料以最大限度地降低冲击破坏的扩展。碳纳米管显示出了极高的强度和刚度,无机富勒烯在能量吸收方面潜力巨大。
除了材料的发展,设计新型复合装甲也是研究的另一个热点。美国研究人员Gama等[36]设计了三明治结构的防弹装甲,即在氧化铝陶瓷和S-2玻璃纤维复合材料之间插入泡沫闭孔铝金属层,以减少应力波的传输;在纤维复合材料变形之前,通过击碎泡沫可使射弹减速,减小变形装甲侵入背面空间的程度。文献[27]提出了一些新的理论,包括制备出钉子形陶瓷,像短螺栓插入六角形螺母中一样插入背板结构的孔中,提高抗多发打击性能。
总体而言,防弹陶瓷需要考虑防弹性能、质量(面密度)、成本这3种因素,在不同的条件下,应根据不同的防护要求,在防弹性能、质量以及成本之间达到一种平衡,即在满足防弹性能的前提下,使质量与成本更低,才能更好地满足需要[37]。
更多关于材料方面、材料腐蚀控制、材料科普等方面的国内外最新动态,我们网站会不断更新。希望大家一直关注国家材料腐蚀与防护科学数据中心http://www.ecorr.org