铝型材静电粉末喷涂常见质量缺陷原因简析
2017-02-27 11:41:35
作者:本网整理 来源:网络
摘 要:本文通过简析静电粉末喷涂铝型材产品常见的质量缺陷,探讨了影响粉末喷涂产品质量的相关因素及控制措施。
1 前言
近些年来,随着建筑的多样化、个性化,建筑铝型材表面朝着颜色多样化方向发展。静电粉末喷涂工艺采用绿色环保技术,具有工艺操作简单、节能、安全、污染小等特点,生产的铝型材表面涂层具有颜色多样、色泽均匀、耐腐蚀、附着力强、耐候性及环保性能好等优点,寿命优于一般的氧化型材。但在铝型材静电粉末喷涂过程中,型材表面涂层也经常出现一些缺陷,对于这些问题,找出形成的原因及解决方法,并加强生产过程工艺控制,是保证粉末喷涂产品表面质量的关键。
2 粉末喷涂常见质量缺陷原因简析
2.1 涂层色差
色差又称色像差,是透镜成像的一个严重缺陷,简单来说就是颜色的差别(如图1所示),GB 5237.4中要求粉末喷涂型材色差不大于1.5。在铝型材静电粉末涂装中,涂膜产生色差的原因主要有粉末涂料和粉末涂装工艺控制两方面。
2.1.1 粉末涂料方面
在粉末涂装产生色差,从粉末涂料本身考虑,可能的原因是配方选择的原材料,例如颜料、固化剂等的耐热性不太理想;另外,粉末涂装厂的烘烤固化条件与粉末涂料生产厂调色时的烘烤固化条件之间有一定差距也可能引起涂层色差。
2.1.2 粉末涂装过程方面
从粉末涂装方面考虑,以下几个方面的因素会影响粉末涂层的色差:
(1)涂层厚度不均匀,尤其是浅色粉末涂层,涂层膜厚不均而引起的色差更明显。为了尽量减少涂层色差,在粉末涂装中,必须保证一定程度的涂层厚度,而且涂层厚度要均匀;
(2)固化炉的温度控制灵敏度差,温度分布不均匀时涂层也容易产生色差。为了减少烘烤固化中的色差,要求固化炉的温度分布较均匀;
(3)在粉末涂装的烘烤工艺中,固化时间对涂层色差也有明显的影响。特别是工件材料的厚度不同时,工件材料厚的比薄的升温时间长,在输送链速度固定的固化炉中,工件达到设定温度后的有效固化时间短,这样不同材料厚度工件之间也容易产生色差。因此,在粉末涂装那些不同材质、厚度、形状和大小的工件时,就应按照工件的材质、厚度、形状和大小进行分类,然后分别设定不同烘烤时间进行烘烤固化;
(4)粉房换色,悬链停止时间太久,固化时间太长,导致型材在炉子中固化过度变色。
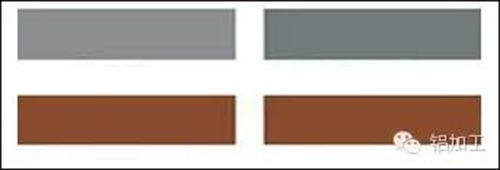
图1 涂层色差
2.2 涂层附着力差
国家标准规定,粉末喷涂型材的干附着性、湿附着性和沸水附着性达到0级。
2.2.1 粉末涂料方面
从粉末涂料考虑,如果在配方设计中树脂的选择或固化剂的品种和用量选择不合理,成膜助剂的质量百分含量或者体积浓度不恰当都会影响到涂膜的附着力。
2.2.2 粉末涂装过程方面
从粉末涂装过程考虑,影响涂膜附着性能的主要原因有如下几个方面:
(1)工件表面处理得不好。工件表面油污未清洗干净,或者铬化膜质量不好,表面沾污前处理槽液残渣等,在此情况下,粉末涂装以后涂膜与底材的附着力不好,同时导致涂膜耐冲击性能下降,此时应通过加强工件的表面处理工艺来解决;
(2)固化炉的烘烤固化温度、固化时间未能达到工艺要求,实际生产过程中需根据型材大小、粉末类型合理设置固化温度及时间。在粉末涂料的固化条件中,固化时间是指被涂物达到固化温度以后保温的时间,而不是指工件放入烘烤炉以后就开始计算的时间。当工件材料愈厚,挂的件愈多,那么工件的热容量也就愈大,工件升温至控制温度所需要的时间就愈长。如果有效烘烤时间不够时,涂膜固化不完全,涂膜的物理力学性能就达不到要求。因此,在粉末涂装中,需定期用炉温跟踪测定仪测定固化炉炉温状况,以确定合理的烘烤固化温度和时间,这样才能保证涂膜的完全固化;
(3)空压机为涂装过程提供辅助空气,空气排水、除油不充分会对涂装质量产生直接影响。因此油水分离器、干燥机及排水装置需做好日常维护保养工作,制定日常专人维护制度。
2.3 涂层橘皮
橘皮即涂层不均匀、不平整,目视如橘子皮状(如图2所示),引起橘皮的原因主要包括以下几个方面:
(1)粉末质量问题,粉末流平剂等原材料质量不合格或配方问题;
(2)涂膜太薄,流平受阻不能很好展开,此时能看到型材基体纹理;涂膜超厚,涂膜表面呈斑纹状桔皮;
(3)粉末涂料固化速度太快,自身流平性差;
(4)烘烤温度过低,熔融流动性差;
(5)喷粉时粉末雾化不好。
其解决措施也应相应地从以下几个方面去考虑:
(1)重新调整粉末涂料的固化速度和流平性,或选用新粉末涂料;
(2)做好涂装过程膜厚控制,避免膜厚太薄或超厚;
(3)调整好静电喷涂的工艺参数,主要应控制高压静电和工件表面与喷枪之间的距离,达到控制膜厚大小及涂装均匀性的效果。

图2 涂层橘皮
2.4 涂层缩孔
缩孔即在涂层表面由一个中心点始发,在涂层表面形成的一个圆形凹陷。
2.4.1 粉末涂料方面
从粉末涂料本身考虑:
(1)粉末涂料本身的质量问题,如粉末涂料制造过程中混入油和水,以及树脂本身的质量问题等;
(2)树脂成份不同的粉末涂料混用,粉末涂料之间兼容性差;
2.4.2 粉末涂装过程方面
从粉末涂装角度来考虑,容易产生涂膜缩孔等弊病的原因有以下几个方面:
(1)前处理脱脂不干净,表面有油污,或者脱脂后水洗不净造成处理液残留而引起的缩孔;
(2)粉末涂料静电喷涂所用的压缩空气中油、水含量超标,导致粉末涂料受污染;
(3)悬挂链上油污掉落到工件表面引起的缩孔;
(4)粉末涂料受潮严重时,也容易使涂膜产生缩孔。粉末涂料应在室温和干燥的条件下存放,对那些已打开包装但尚未用完的物料,一定要扎好塑料口袋防止受潮。特别要注意回收粉末涂料在回收过程中容易吸潮和带进杂质等问题,回收粉要与新粉末涂料按一定比例混合后马上使用。
2.5 颗粒
2.5.1 粉末涂料方面
从粉末涂料本身考虑,在粉末涂料制造过程中,粉末中带入杂质或环境中的灰尘进入粉末涂料中,都可能引起表面颗粒(如图3所示)。
2.5.2 粉末涂装过程方面
从粉末涂装过程考虑,下列问题容易引起涂膜颗粒:
(1)工件表面毛刺、麻坑等缺陷容易使涂膜出现颗粒。这是因为当粉末涂料烘烤固化,粉末涂料熔融流平时使工件表面封闭,随着工件温度的升高,毛刺和麻坑中的空气压力加大,从而拱起熔融流平的涂膜。解决这种问题的根本措施是控制型材挤压过程的表面质量;
(2)工件表面处理不干净,表面处理液中的残渣等杂质仍附着在工件表面上,在进行粉末喷涂时容易产生涂膜颗粒。这种问题只要通过及时清理前处理残渣,在水洗工艺中将工件清洗干净就能解决;
(3)在静电粉末涂装中,喷粉室周围的生产环境不干净,特别是空气中的一些粉尘和颗粒物被带进粉末涂料或喷粉室,在粉末涂料熔融流平时,成为涂膜中的颗粒。这种问题通过将喷粉室与生产车间隔离,以防止生产车间的灰尘和污物带进喷粉室;
(4)在回收粉末涂料过程中,回收粉末未过筛或筛网目数太小会引起涂层颗粒。解决这种问题的方法是选用合适目数的筛网,回收粉末经自动或手动振动筛,筛后的粉末再与新粉按比例混合后使用;
(5)粉末挥发物在固化炉内结成絮状物或输送链挂具上颗粒掉落,都会产生涂层颗粒。解决这种问题的方法是及时清理固化炉及输送链上附着的杂质。
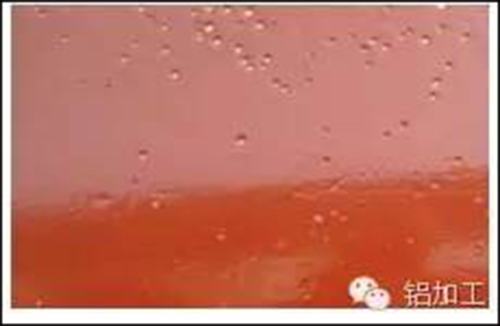
图3 颗粒
3 小结
静电粉末喷涂生产过程中,需正确控制好各个工艺环节,并根据生产实际情况进行调整。对生产中出现的质量问题要及时分析并解决,通过加强生产工艺控制,形成操作规程并严格落实,以保证产品质量的稳定与可靠。
参考文献
[1] 陈小雷。粉末涂装缩孔的控制[J].表面技术,2001,30(6)。
[2] 王锡春。粉末涂料、涂装的国外现状及最新动态[J].中国第一汽车集团公司汽车工艺研究所。
[3] 张魏忠。铝合金建筑型材表面处理技术及发展趋势[J].第六届全国表面工程学术会议,2006,8.
[4] 孙忠锡,李淑环,苗玉慧。粉末喷涂中易出现问题简析[J].家用电器科技,2001(12)
更多关于材料方面、材料腐蚀控制、材料科普等方面的国内外最新动态,我们网站会不断更新。希望大家一直关注国家材料腐蚀与防护科学数据中心http://www.ecorr.org
免责声明:本网站所转载的文字、图片与视频资料版权归原创作者所有,如果涉及侵权,请第一时间联系本网删除。