镁合金资源丰富,密度小,生物相容性好,力学性能优良,应用日益广泛,但是镁合金化学活性高,易于腐蚀,通常采用添加合金元素来调整基体的微观结构,以及表面处理来提高耐蚀性。但由于合金元素在镁基体中的溶解度低,且大部分合金元素都以第二相形式析出,从而导致微电偶腐蚀。因此,通过调整基体微观结构来提高镁合金的耐蚀性效果有限,而使用防护涂层的效果更加明显。效果较好且商业化应用最广泛的防护涂层有化学转化膜和微弧氧化膜,在实际使用时,常常还要再涂覆有机涂层。
经过合理设计的镁合金涂层已经能够基本满足镁合金的耐蚀性要求,但是涂层在使用过程中将不可避免地遭到破坏, 如果涂层不具备自修复能力,腐蚀就会从涂层破损区域开始,发生比均匀腐蚀危害性更大的局部腐蚀。铬酸盐转化膜(CCC)具有良好的屏蔽效应和自修复能力, 是最有效的镁合金防护涂层。但是,由于 Cr 6+ 易于诱发肺癌,目前已经被限制使用, 因此需要开发同时具备良好屏蔽能力和自修复能力的涂层替代铬酸盐转化膜。
目前市场上几乎没有镁合金自修复涂层的产品,但对于使用环境恶劣、保养维护困难、寿命要求长的涂层,尤其需要具备自修复能力。因此,性价比较高的自修复涂层有极大的应用前景。
1 自修复涂层的原理和分类
涂层的自修复可以定义为涂层修复材料表面由于机械或化学损害而导致的缺陷和破损的行为,最终实现涂层破损处物理或化学功能的恢复。修复剂是涂层破坏后释放出来的能够修复膜层性能的物质。 自修复涂层是在普通涂层提供屏蔽效应的基础上,通过技术改进被赋予仿生自修复功能。一般原理是涂层在破坏后释放出修复剂, 然后修复剂与环境反应,生成的产物覆盖在基体上,阻碍缺陷或破损区域进一步扩展。
涂层的修复方式包括两类。一类是对原有涂层进行修补, 一般是利用修复剂 (可聚合的有机物)之间的反应来实现, 例如释放出的有机单体与分散在涂层中的催化剂接触或与环境接触而发生聚合反应。另一类是形成新的物质覆盖缺陷,一般是利用修复剂(缓蚀剂)与基体的反应来实现修复,例如释放出的 8-羟基喹啉(8-HQ)与裸露基体形成稳定疏水的螯合物 Mg(8-HQ)2 ,释放出的钝化剂与裸露基体反应生成新的转化膜等。
第二类修复过程严格上来讲并未真正地修复涂层,但修复了涂层的耐蚀能力。
自修复涂层有许多分类方法。 例如根据自修复过程是否自动发生,分为自发式和触发式。自发式是指涂层在破坏后,修复过程自动完成;触发式是指涂层需要在一定的 pH 值、光、水、热、氧气等环境下发生自修复。
2 自修复涂层类型
要实现涂层的自修复,需要修复剂能够复合到涂层中,并在涂层破坏后能成功释放出来,在涂层破坏处生成相对平整且具有良好屏蔽能力的膜层。自修复涂层可以分为下几种。
2.1 化学转化膜型
一些化学转化膜在形成过程中会在膜层中残留或新形成一部分钝化剂。 这些化学转化膜不仅能提供屏蔽能力, 还能通过转化膜的离子交换机制和溶解机制释放出修复剂,修复破损处。
对 镁 合 金 进 行 重 铬 酸 盐 浴 ( K 2 Cr 2 O 7 或Na 2 Cr 2 O 7 ) ,镁基体被氧化时,Cr 6+ 被还原成 Cr(OH)3(s)或 Cr 2 O 3 (s) ,同时 Cr 6+ 浸入或残留其中,形成Cr 6+ /Cr 3+ 混合氧化物膜层,即 CCC。CCC 可以阻隔水、氧分、盐分等腐蚀性物质浸入到金属表面,具有良好的屏蔽能力。膜层破坏后,氧化层中的 Cr 6+释放出来, 在裸露的基体上形成 Cr 3+ 沉淀使裸露的金属再钝化,实现涂层的自修复。
镁合金的磷酸盐转化膜在划伤后置于细胞培养液中,可以通过修复反应,形成含有磷和钙的自修复保护膜覆盖在划痕处, 培养液的流动还可以促进自修复过程 。
钒酸盐转化膜能够在点蚀坑处生成花状氧化钒化合物抑制点蚀, 具有一定的自修复能力。
马普所的 Hamdy 课题组将钒酸盐转化膜作为双层自修复涂层(钒酸盐转化膜+含有无毒缓蚀剂的有机涂层)的底层,用于 AZ31、ZE41 、AA2024 等合金后,研究腐蚀环境下的耐蚀性和局部微观修复情况, 结果证实了钒酸盐转化膜的自修复能力,并得到处理液中钒酸盐浓度的最优值。
钒酸盐作为缓蚀剂, 已经被应用于铝合金和复合材料的涂料和涂层中。
稀土氧化物能够使膜层更致密并提供“清理效应”。 传统观点认为, 膜层中游离的 Ce 3+ 能够作为阳极缓蚀剂, 在活泼的阳极点形成 Ce 4+ /Ce 3+ 的氧化物和氢氧化物,与 Mg(OH)2 、Al(OH)3 形成致密且粘附性较好的混合膜层,局部覆盖 α-Mg,降低微电偶腐蚀,提高耐蚀性。然而 Williams 却发现,氧化膜中含有稀土氧化物时,腐蚀速率反而很高,因此稀土氧化物渗入到氧化膜中,只是稀土元素提高膜层耐蚀性的一个比较次要的因素。当铈以转化膜的形式覆盖在镁合金表面时,铈会溶解,导致转化膜粘附性较差且不致密,加快镁合金腐蚀,但当转化膜设计合理时,溶解的铈则可作为修复剂。
Aramaki 等在 锌 电 极 上 制 得 了 一 种 用Ce(NO 3 )3 ·6H 2 O 修饰的 Ce 2 O 3 含水涂层,该涂层在划伤后, Ce 3+ 能作为修复剂, 迁移至裸露的锌基体,反应生成 Ce 2 O 3 实现修复。 当涂层为含铈的混合氧化膜时,Ce 也能提供自修复能力。
硅酸盐转化膜非常薄且透明, 形貌上与未处理的合金相似。但硅酸盐转化膜在划痕-腐蚀过程中,Si 元素能够通过“溶解-再沉淀”机制向划痕处扩散,形成含有 O 和 Si 的修复膜,减缓划痕区的腐蚀。镁合金的锡酸盐转化膜是富含 SnO 的Mg(OH)2 ,Sn 2+ 在腐蚀环境下会转化为更为稳定的Sn 4+ ,并阻碍氯离子的吸附,使涂层耐蚀性随着腐蚀浸泡时间的延长而升高。虽然锡酸盐转化膜很薄, 但是它对自修复能力和耐蚀性的提高也有非常积极的作用。
化学转化膜型的自修复涂层制备简单,成本低,但是涂层较薄,耐蚀性能有限,能够承载的修复剂有限,还有可能疏松或有毒,因此一般作为自修复防护涂层的底层, 需要再涂覆一层有机涂层来提高耐蚀性。
2.2 掺杂型
将修复剂直接混入溶胶或有机物等涂层原料中,制得的涂层也能在被破坏后表现出自修复能力。当修复剂是无机盐时,涂层的耐蚀性提高不明显,当修复剂为有机化合物时,涂层的耐蚀性显著提高。
溶 胶 - 凝 胶 法 常 用 于 制 备 涂 层 。 掺 杂 有Ce(NO 3 )3 的 ZrO 2 溶胶凝胶涂层中含有铈离子。浸泡腐蚀时,由于铈向合金表面运动,涂层的耐蚀性降低得更慢, 其机理类似于自修复。 将 Ce(NO 3 )3直接混入 SiO 2 溶胶凝胶的前驱体中制得的涂层,其耐蚀性随着 Ce(NO 3 )3 浓度的变化存在峰值。
前期耐蚀性增加是因为可释放的缓蚀剂增多, 后期耐蚀性降低,是因为无机盐直接加入前驱体后,前驱体黏度增大,涂层变薄,浸泡时膨胀更强烈,凝胶涂层中链分解程度增大, 导致涂层提供的初始屏蔽能力降低 ,Ce(NO 3 )3 对涂层稳定性的影响如图 1 所示。但将 8-HQ 作为缓蚀剂混入 SiO 2 -ZrO 2溶胶凝胶体系水解后的前驱体中,并不会导致溶胶凝胶层的退化。
壳聚糖原料广泛、环境友好,成膜能力强,与金属基体和聚合物的结合力好, 且能与一些缓蚀剂形成复合物,是制备自修复涂层的良好候选方案。
将 Ce(NO 3 )3 混入壳聚糖酒精溶液,通过浸渍提拉法制得的掺杂涂层,用溶胶凝胶封闭表面后,耐蚀性因为铈的存在而明显提高, 微区电化学结果则证实了涂层的自修复能力。
利用静电纺丝技术制备涂层易于控制。 Firouzi等将乙酰丙酮化铈加入聚乙烯醇溶液中, 通过静电纺丝的方法在 Al6082 表面上制得纤维状涂层。
面扫结果表明,涂层破坏后释放的 Ce 能够在 pH升高的地方形成新的涂层,涂层具有自修复能力,长久耐蚀性提高。掺杂型自修复涂层制备简单, 对于成熟的涂层制备工艺,只需增加将修复剂混合在原料中的步骤,但是修复剂的加入可能会影响涂层的稳定性,从而降低涂层的屏蔽能力, 因此需要选择合适的修复剂。
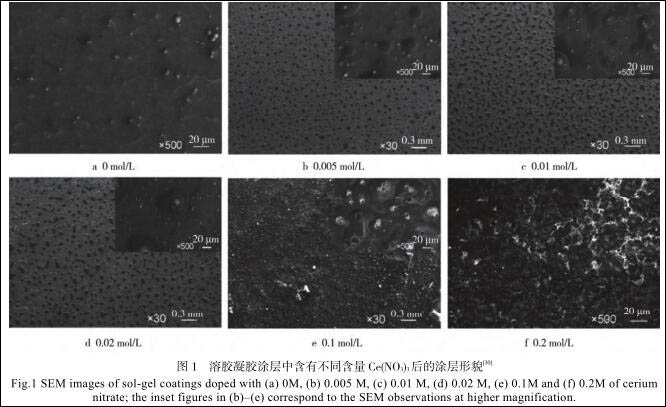
2.3 填充型
在基体上先制得多孔涂层, 再将修复剂填充入涂层微孔中,可以赋予涂层自修复能力。多孔涂层丰富的表面积可以吸附足够的修复剂, 还能提高与面漆的结合力,同时,避免了往涂层中直接添加颗粒和修复剂给涂层屏蔽性能带来的负面影响。 当涂层出现破损时,修复剂就会释放出来,阻碍基体的进一步腐蚀。
微弧氧化膜的均匀微孔, 是填充修复剂的理想结构。Gnedenkov 等在镁合金的微弧氧化膜中浸渍入 8-HQ 并干燥后,体系的耐蚀性更强,且涂层破坏后,8-HQ 可以减缓裸露基体的腐蚀。
多孔层可以通过模板法制得。Lamaka 等以刻蚀的铝合金表面为模板, 利用 Ti(OPr i )4 的水解在合金表面得到 TiO 2 微纳米多孔膜层,填充缓蚀剂后用溶胶凝胶层封闭微孔。 所得涂层的结构及自修复原理如图 2 所示。
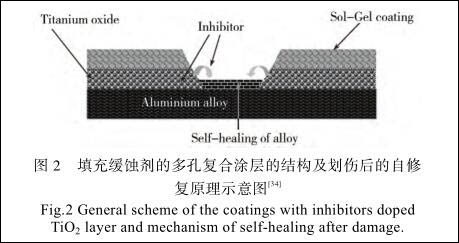
将填充有修复剂的自由的多孔薄膜粘结到基体上,也能得到填充型自修复涂层。Yabuki 等在植酸膜中填充入苯甲酸钠缓蚀剂后, 粘结在冷轧碳钢上,并用有机物封闭表面,所得涂层具有自修复能力, 且植酸膜孔隙越大, 材料自修复能力越强。
植酸膜的孔径可以通过制备时溶剂的挥发时间进行控制。
填充型自修复涂层中的修复剂分布均匀,因为修复剂并不直接参与涂层骨架的形成过程,因此比掺杂型自修复涂层更稳定,另外,多孔涂层丰富的比表面积可以保证修复剂的储存空间,还可以增加多孔涂层与表面封闭层的结合力。然而修复剂加入后,可能进入封孔用的有机涂料中,降低其稳定性,降低层间结合力,还有可能增加涂层内部的渗透压,使腐蚀介质更易浸入涂层内部。因此需要选择合适的修复剂,并尽量清除层间修复剂,保留孔内修复剂。
2.4 微容器型
微容器型自修复涂层是将修复剂用微容器封装后埋植于涂层基体中,涂层破坏时,微容器在力学或环境(如 pH 和湿度)的刺激下破裂,修复剂被释放出来,并在虹吸作用下向涂层基体中扩散,并最终按某种机制修复破损处。常用的微容器有微胶囊、微脉络、多孔材料和储层等微结构。原理如图 3 所示。
White 等设计了经典的微胶囊自修复复合材料体系。采用脲醛树脂作为微胶囊,包覆二环戊二烯单体,同时在基体中分散着能使单体发生聚合反应的 Gibbus 催化剂。当材料发生破坏时,微胶囊破裂,单体被释放,并在虹吸作用下向裂纹尖端流动,与基体中的催化剂接触发生聚合反应,修复材料。
微胶囊结构的修复剂含量有限,不能对同一处进行多次修复,于是研究者仿造生物体微循环结构设计了一种微脉络结构。微脉络犹如人体血管一样分布于涂层中,当某处涂层遭到破坏后,修复剂能够在微脉络中流动并抵达破坏处,实现多次修复。
带有微孔的颗粒也能装载修复剂。Qiao 等用介孔 SiO 2 纳米颗粒作为 2-巯基苯并噻唑缓蚀剂的载体,分散在镁合金的有机涂层中,得到的涂层具有部分自修复能力。同时,划痕实验表明,当涂层中不含缓蚀剂时, 环氧涂层中残留的涂层原料之间也会发生反应,实现对划痕的部分修复。
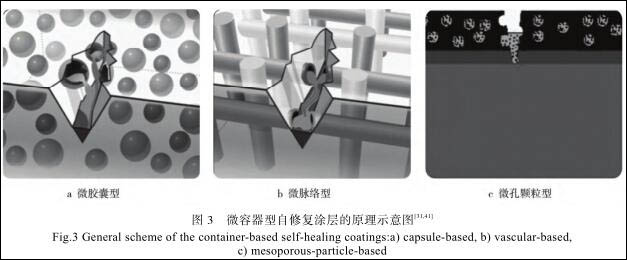
微容器一般需要复合到涂料中使用, 将修复剂与涂层基体隔开有利于提高涂层的稳定性, 且结构更可控,修复更智能,但是制备这类自修复涂层较困难,主要面临几个难题 :
1)工艺难度大。需要先制得微容器,再埋植在有机涂层中,微胶囊尺度一般需要 50~200 μm,以保证封装的修复剂足量且微胶囊能在涂层破坏后破裂, 但是涂层厚度一般不超过 200 μm 。
2)破裂。要求微容器在制备过程中完好无损,在涂层破损后则易于开裂,而液态修复剂通常利用真空浸渍填充入微容器中后, 可能还需要烘干,这对微容器和涂层基体的力学要求、环境要求较大。
3)液态修复剂。修复剂为液态时可能对涂层的耐蚀性和耐磨损性产生负面影响,还可能在低温下由于冻结而无法进行自修复,在高温下由于热胀冷缩或修复剂蒸发而出现微裂纹。
4)与涂层基体的粘附性。当微胶囊与涂层基体的粘附性较好时,可以作为硬质第二相,提高涂层的韧性,相反则会降低涂层的质量、耐蚀性和耐磨性。
5)分布。微容器在涂层中难以均匀分布,非均匀分布不仅会降低涂层的自修复能力, 还会降低涂层本身的质量。
2.5 层层组装型
带有异种电荷的物质, 如聚电解质、 纳米颗粒、酶和聚合物等, 依次沉积后的层间即为纳米尺度的微容器,可用于存放和释放修复剂。当水浸入涂层后,带有相反电荷的聚电解质层之间的键能降低,聚电解质流动加剧,也可以促进涂层的自修复。
Li 等在载玻片上利用层层组装制得纳米CaCO 3 颗粒强化的聚丙烯酸/枝状聚乙酰亚胺(PAA/bPEI)涂层,每一层都是大分子聚合物和小分子聚合物的混合物。涂层破坏后,涂层能够通过小分子聚合物的移动实现自修复, 形成光滑透明的修复结构。
将缓蚀剂封装在层间,是常用的层层组装型自修复结构。Andreeva 等在带负电的 AA2024 合金表面上, 依次沉积带正电荷的 PEI、 带负电的 PSS (苯乙烯磺酸盐) 、8-HQ、PSS 和 PEI 上,制得的涂层被破坏后,可以通过局部 pH 的缓冲、缓蚀剂的释放和聚电解质的移动得到修复,原理如图 4 所示。
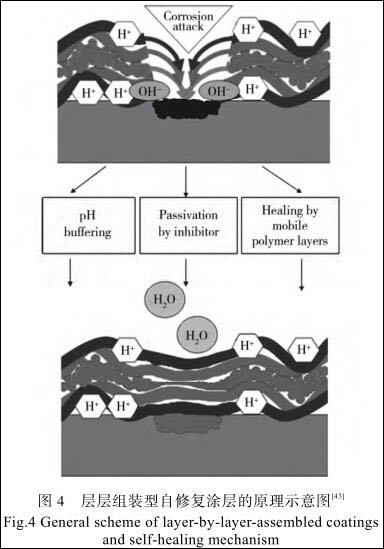
设计自修复涂层时, 综合几类自修复涂层的原理,可以丰富自修复涂层的结构类型。利用层层组装的原理,可以将缓蚀剂封装在微容器中。
Shchukin 等在带负电的纳米 SiO 2 颗粒上依次沉积 PEI、PSS、苯并三唑、PSS、苯并三唑,从而将苯并三唑储存在层间, 然后将纳米颗粒混合到溶胶凝胶涂层中,其原理与微容器型相似。
层层组装型自修复涂层选材广泛, 基体的成分和形貌对涂层形成过程的影响小, 能储存更多的修复剂,且涂层结构可被精确控制,修复过程更加智能,是极具前景的研究方向。
2.6 超分子本质修复型
一些超高分子中的键合断裂后, 可以通过可逆反应、 链重组和共价键修复而重新成键, 利用这个机制,可以制备自修复涂层。有机物单体和高聚物在一定条件下可逆转化, 如热力学恢复性能出色的狄尔斯-阿尔德(DA)可逆反应。进行 DA 反应的单体中含有的特定官能团, 通过 DA 反应能形成高分子,所得的高分子在加热时分解成单体。在冷却时,单体又能通过 DA 反应恢复为高分子。
在热固性高分子材料中加入热塑性高分子, 所得涂层被破坏后,进行加热处理,涂层可以实现一定的自修复。
形状记忆自修复涂层由结构稳定的共价键和微弱且可逆的氢键组成,变形后共价键保持,氢键被破坏。向涂层提供能量时,涂层能够通过分子的运动和键合状态的改变来实现自修复。
Ghosh 等用氧杂环丁烷取代壳聚糖作为前驱体,制备了一种基于聚氨酯的涂层,聚合物网络破损时,氧杂环丁烷开环形成两个活性尾端,断链的壳聚糖, 在紫外光下与活性的氧杂环丁烷端链交联,修复网络结构。
超分子本质修复型自修复涂层制备简单, 且一般可以在同一处实现多次修复, 但是不能直接用在表面碱性前的镁合金上, 而且修复过程通常需要外部的能量输入,同时有机涂层的耐磨性差,易于被破坏或划伤。
3 总结与展望
自修复涂层在保证涂层屏蔽能力的基础上兼具自修复功能,要点在于修复剂的成功封装和释放。同时,自修复涂层的设计还需要考虑更多的其他因素,诸如机械性质、美观、成本和环保等。化学转化膜型自修复涂层在镁合金上应用最多, 其制备工艺简单, 成本低, 但是涂层较薄, 耐蚀性有限,能够承载的修复剂有限,且铬酸盐转化膜有毒;掺杂型自修复涂层的制备工艺简单, 但是修复剂的加入会影响涂层的稳定性; 填充型自修复涂层可以降低修复剂对涂层稳定性的影响, 但会降低层与层之间的结合力;对微容器型自修复涂层的研究最多,可以避免修复剂与涂层基体的直接接触, 但是制备过程复杂且需要满足多种条件; 层层组装型自修复涂层更智能; 超分子本质修复型涂层可以实现多次修复,但是修复过程常常需要外部能量输入,且有机涂层耐磨性差。无论哪种自修复结构,目前都还不能完全替代铬酸盐转化膜。因此,进行自修复涂层设计时,需要结合实际情况,选择合适的自修复结构和修复剂,扬长避短,综合考虑几类自修复涂层的原理和工艺,通过多种途径实现涂层的自修复。
更多关于材料方面、材料腐蚀控制、材料科普等方面的国内外最新动态,我们网站会不断更新。希望大家一直关注国家材料腐蚀与防护科学数据中心http://www.ecorr.org