航空发动机的制造是一项极其复杂的系统工程,其中最核心的部件当属“叶片”,它的制造占据了整个发动机制造30% 以上的工作量。航空发动机工作时,不管是风扇叶片、压气机叶片,还是涡轮叶片都要承受十分恶劣的工况,但是又存在一些差异。因此,航空发动机不同部位的叶片往往会采用不同的材料来制造。目前,金属材料与先进复合材料是航空发动机叶片制造的两大类主要材料,对其加工方法及工艺技术的研究已经成为制造高性能航空发动机的关键。
本文以金属和复合材料叶片为对象,论述、分析了现阶段航空发动机叶片制造采用的加工方法及关键技术,并对其优缺点进行了阐述。
航空发动机金属叶片机械制造技术
高强度不锈钢、钛合金、高温合金等高强金属材料的大量应用极大地提高了航空发动机的综合性能,但其难加工的“通病”却成为航空制造业遭遇的普遍瓶颈。航空发动机金属叶片的制造方法众多,如数控加工、精密锻造、精密铸造、电解加工等。以风扇/ 压气机叶片和涡轮叶片为例,分别论述了航空发动机金属叶片的加工方法及关键技术。
风扇/压气机叶片制造技术
随着发动机性能的不断提高,叶片的结构也愈加复杂,加工难度也越来越大。目前,风扇/ 压气机叶片主要以数控加工、精密锻造、超塑成形/扩散连接方法为主,辅以表面处理技术来完成叶片的高品质制造。
叶片数控加工技术
叶片的数控加工工艺,包含装夹方法、数控编程、切削工艺、颤振抑制、在线检测、辅助工艺等,在此对切削工艺、数控编程、颤振抑制进行重点阐述。
高速高效切削技术。高速铣削一般采用较高的切削速度、适当的进给量、较小的径向和轴向切深,铣削时大部分的热量被切屑带走,因而工件的表面温度较低。并且随着铣削速度的提高,切削力略有下降,表面质量有所提高,生产效率随之提高(图1)。在高速铣削过程中,刀具轨迹的平滑过渡是保证切削质量的关键技术。插铣是实现高效切削最有效的方法之一,相较于其他的铣削方式,可大幅降低刀具的径向切削力,有效抑制切削振动,在叶片的切削过程中,对于榫根、缘板、叶身等需要去除大余量的部位具有很高的加工效率。西北工业大学现代设计与集成制造技术教育部重点实验室近几年提出快速铣的概念,这种铣削方式采用大进给、小切深的工艺方法,在保证切削质量的同时,进一步提高了加工效率。
数控编程技术。随着数控加工和自动编程技术的不断发展,智能化、集成化和并行化已成为其发展趋势。可以利用CAPP/CAM 等集成的自动编程系统对叶片曲面零件进行程序编制,甚至有些叶片高效切削机床将具有工艺知识的编程系统集成在机床控制系统里。国内对CAM 系统在不断进行开发,航空叶片制造编程系统通过二次开发把特定的工艺知识融合以取得更有效的程序代码,即CAPP 与CAM 高层次集成。
颤振抑制技术。加工颤振的抑制方法目前主要分为在线预报控制和离线预测控制两种。前者主要是通过对实际加工系统的监测与颤振信号的提取,在预先设定的控制策略下抑制颤振。这种方式对预测系统多方面提出高的要求,包括容错性、颤振控制策略和灵敏度等方面(判断速度)。离线预测控制方法是依据系统切削参数稳定性极限图,通过控制切削工艺参数和系统结构实现抑制颤振。目前,时域仿真法、半解析法和解析法是获得切削参数稳定性极限图的主要方法。除以上两种方法之外,也有一些学者提出在加工过程中采用主动振动阻尼法抑制颤振。
综合应用以上数控加工技术可以有效解决风扇/ 压气机叶片加工的技术瓶颈,西北工业大学航空发动机先进制造技术国防创新团队进行了深入的研究和应用。
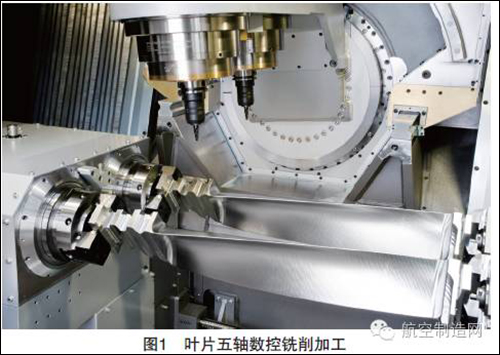
叶片精密锻造技术
叶片精锻是采用高精度的锻压设备,依托完善的检测手段和辅助处理工艺,锻造出余量小、质量高的叶片毛坯。精锻叶片可以更完整地保持金属流线的连续,保证叶片的强度和承载能力,极大提高叶片的性能和寿命。
精锻叶片余量小,强度高,加工周期短,寿命长,但由于叶片结构的复杂性和当前精锻技术的特点,部分精锻叶片的阻尼台、前后缘部分仍需保留机械加工余量。叶片精锻是一项综合工艺技术,对原材料和制造工艺有较高的要求。由于工艺技术的限制,精锻叶片局部仍然需要依靠机械加工来保证表面质量和截面尺寸。叶片成形过程中,前后工序要严格匹配,对每道工序的变形温度、变形速度、变形程度以及金属的流动方向均要严格控制,这同时对叶片精锻工序的设计、锻造设备的精度和刚性、检测设备的精度都提出了极高的要求。
叶片超塑成形/扩散连接制造技术
超塑成形是利用某些材料在特定条件下呈现优越的塑性变形能力而发展出的一种成形工艺。采用此种工艺可以制造高精度的复杂结构,同时由于其拥有极好的变形能力,使得制造件加工重复性好,而且没有回弹。扩散连接是利用被连接材料的表面在不足以引起塑性变形的压力和低于被连接工件熔点的温度条件下,使接触面通过原子间相互固态扩散而形成连接的方法。
超塑成形/ 扩散连接技术充分发挥了两种工艺的优势,在成形中空结构的应用中已经越来越广泛,是成形空心叶片的较好选择。利用钛合金的扩散连接温度与它的超塑成形温度相似的特性,在加工叶片时,可以在一个工序中完成成形和连接两种工艺,节省了加热以及冷却的时间,提高了叶片的生产效率。并且使用该技术制造的叶片无需额外的机械装配以及焊接处理,使得零件整体性更强,对于航空发动机减重增推有着重要的意义(图2)。Rolls-Royce公司在钛合金风扇叶片上不断创新,经历了第一代窄弦实心风扇叶片。第二代蜂窝夹芯结构宽弦风扇叶片并从TRENT 800 开始,包括后续的TRENT 1000、TRENT XWB,均采用了第三代钛合金风扇叶片。该叶片采用全新的夹芯结构,即采用桁条结构芯部取代了蜂窝结构,并且利用超塑成形/ 扩散连接工艺制造,使得叶片在尺寸增加的同时,有效控制了结构重量。
中航工业北京航空制造工程研究所采用这种技术在钛合金、铝合金及铝锂合金等材料的超塑成形/ 扩散连接技术研究和应用方面开展了大量工作,进行了钛合金宽弦空心风扇叶片、可调叶片、防火墙、卫星贮箱等超塑整体构件的成形工艺试验和应用研究。
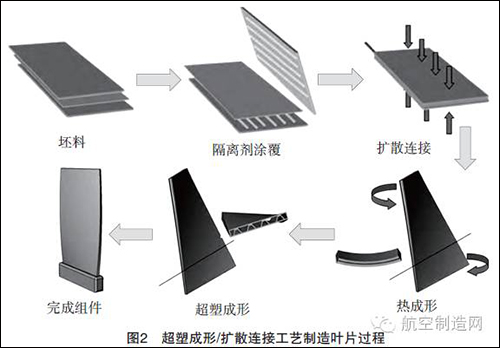
涡轮叶片制造技术
由于涡轮叶片所处的环境更为恶劣,相较于风扇/ 压气机叶片,对其材料和加工工艺都提出了更为严苛的要求。目前,涡轮叶片的加工普遍采用精密铸造的方式(图3),辅以磨削等其他一些加工方法。
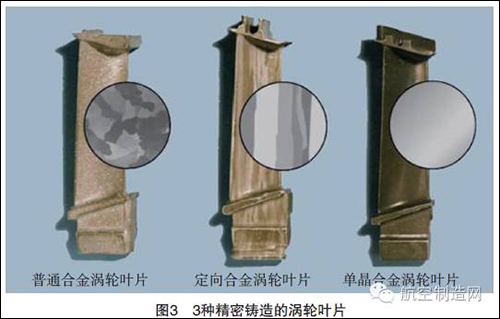
熔模无余量精密铸造技术
熔模无余量精密铸造技术是一种能够直接制造具有复杂曲面,并省去叶身表面材料去除环节的技术。该技术能改善叶片的工作性能,提高其工作寿命,常用来制造定向/ 单晶空心无余量叶片,现已成为先进航空发动机涡轮叶片制造技术的重要发展趋势,如使用该技术制造γ-TiAl合金低压涡轮叶片,如图4 所示。熔模无余量精密铸造空心叶片的关键技术是制造冷却结构的陶瓷型芯。
愈是高效冷却的空心涡轮叶片,其内腔结构愈加复杂,所处的工作条件更加苛刻,相应的陶瓷型芯结构更为精密,因此对陶瓷型芯尺寸精度的控制要求也更高。最常用的制造陶瓷型芯的方法是预制成型陶瓷型芯, 运用该方法可以铸出各种形状复杂的冷却结构, 其主要步骤包括制浆、压制型芯、型芯校正、入炉烧结、强化处理。
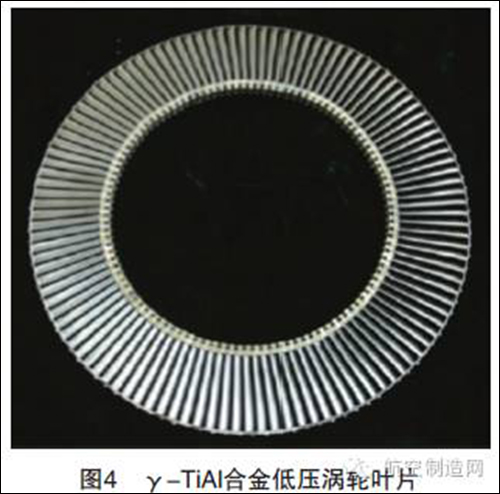
定向凝固结晶控制技术
定向凝固结晶控制技术指的是在熔模铸造型壳中使熔融合金沿着与热流相反的方向结晶凝固的一种铸造工艺。采用这种工艺成形的涡轮叶片具有很高的抗热疲劳和抗热冲击性。早期的定向凝固技术方法众多,大致可分为以下几类:发热剂法、功率降低法、快速凝固法、液态金属冷却法以及流态冷却法等。
现如今,诸多集传统技术优势与最新工艺方法于一体的新型定向凝固技术不断涌现,包括区域熔化液态金属冷却法、电磁约束成形定向凝固法、深过冷定向凝固法、激光超高温梯度快速凝固技术以及连续定向凝固技术等。
再结晶抑制技术
再结晶的出现将会导致原单晶合金的耐高温性能显著下降。叶片制造过程中因机械处理(如:吹砂、机械抛光等)而产生塑性变形,随后又经固溶、退火等高温处理或在使用中受高温、高压燃气的作用,均有可能导致再结晶的出现。因此,国内外对此进行了针对性的研究,提出了预回复热处理、渗碳、涂层以及去除表面变形层等抑制再结晶方法,并对再结晶叶片开展了加入界强化元素的修复工作。
其他加工技术
高速强力磨削技术。世界航空强国纷纷开始对高速强力磨削在叶片制造中的应用开展研究,如利用该技术可一次加工出涡轮叶片的榫头齿形,能够极大地提高生产效率。当前世界各国磨削技术的发展趋势为:研发具有更高刚性、精度的数控磨床,研制超硬磨料及磨具,进一步开展对精密磨削及高速磨削的理论研究和技术探索。高速和超高速磨削作为先进制造的一项全新实用技术,已引起我国航空发动机行业的极大重视,是国内未来磨削技术的一个重要发展方向。
自适应加工技术是叶片高效精密制造技术的重要组成部分。该技术主要用于精密锻造、辊轧叶片缘头精密加工、整体叶盘的加工和修复,复杂空心叶片的数控加工以及余量不均匀复杂曲面的加工。
航空发动机复合材料叶片制造技术
先进复合材料由于其质轻、高强、耐腐蚀、抗疲劳等诸多特性越来越多地应用在航空、航天领域。树脂基复合材料制造的风扇叶片、金属基复合材料制造的风扇/ 压气机叶片、陶瓷基复合材料制造的涡轮叶片已经成为航空发动机减重增推的关键技术手段。
树脂基复合材料叶片制造技术
自20 世纪70 年代GE 开始研制并使用树脂基复合材料风扇叶片以来,近50 年的技术探索与经验研制了多款集先进材料与工艺于一体的商用航空发动机风扇叶片。这其中涉及了复合材料的加工及预制体制备和叶片成型相关技术。
复合切削技术
在预制体及复合材料构件的切削加工中,采用传统钻、铣等工艺加工时,由于纤维的高硬脆性、切削力变化、刀具磨损等原因可能会造成加工件表面不完整,甚至出现分层、纤维拉出及脱开等缺陷。近些年,非传统加工技术在复合材料方面的应用愈加成熟,比如加工碳纤维预制体时采用超声切割或者激光加工可以得到很高的精度(图5),水射流加工去除复合材料多余材料成本更低,旋转超声加工在CFRP/Ti 合金的叠层结构制孔上有较大优势。
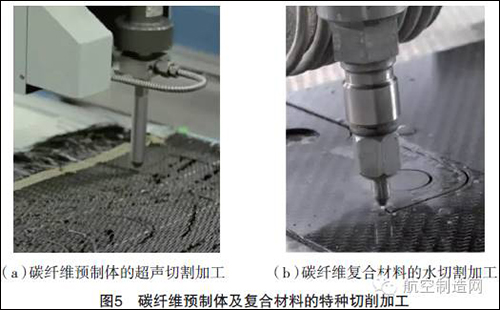
预制体制备技术
复合材料叶片预制主要有两种制备工艺,分别是预浸料铺放工艺以及3D 编织工艺。预浸料铺放工艺。使用预浸料铺放工艺来制备预制体需要着重把握预浸料的平面- 曲面变换裁切优化、预浸料铺贴的精确定位以及预浸料层间的穿刺强化。国外普遍采用分层切片法配合自动裁床进行变换裁切优化,采用激光放样法进行精确定位,采用特种专用设备进行层间穿刺强化。近些年,随着技术的进步,自动铺丝工艺(AFP)也被成功应用于预制体的制备当中,如Rolls-Royce公司将AFP 技术应用于在研TRENT系列发动机复合材料风扇叶片,实现了其预制体的自动化生产。
3D 编织工艺。3D 编织工艺是将纤维在三维空间里沿多个方向按规律相互交织、交叉在一起从而获得完整的结构。这种技术彻底解决了制件层间分离的问题,可极大地提高其结构性能。目前,常用的3D编织方式有4 种,分别是极线编织、斜线编织、正交编织和饶锁线编织。3D 编织又有多种形式,如二步法、四步法、多步法等。CFM 公司的LEAP-X 发动机风扇叶片是目前唯一使用3D 编织工艺制备预制体的复合材料叶片。该叶片以其高比强度、高比模量的特性在耐冲击、抗疲劳、抗开裂等方面具有独特的优势。
叶片成型技术
航空发动机风扇叶片采用双曲面、大扭转与变截面的结构形式,仅仅依靠热压罐成型工艺已经难以保证零件的成型精度,而闭模成型工艺可以很好地解决成型精度不足的问题,故该技术已经成为复合材料风扇叶片的主流成型技术(图6)。
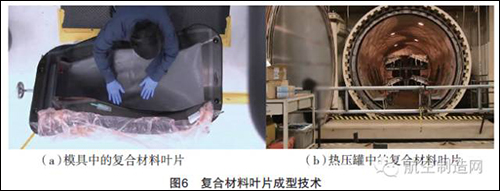
并且,随着技术的不断革新,采用复合材料成型模具取代金属模具以及采用混杂纤维替代单一纤维风扇叶片逐渐成为国外发展趋势。由于复合材料模具与复合材料零件本身拥有相似的热胀系数,因而保证了成型零件的尺寸精度,而混杂纤维复合材料除铺层时需要考虑混杂方式、最优纤维比等因素外,在成型工艺方面与单一纤维叶片差别不大。
树脂基复合材料风扇叶片的两个基本制造工艺是预浸料铺放/ 模压成型技术以及3D 编织/RTM 成型技术。前者指的是以预浸料为成型原料,以模压工艺为成型方法来制造复合材料风扇叶片的技术手段,主要以GE 公司生产的GE90( 见图 7(a))、GEnx 发动机风扇叶片为代表;此外,罗-罗公司和GKN 集团也联合采用了该技术为TRENT 系列发动机开发风扇叶片。3D 编织/RTM成型技术,指的是使用纤维丝束通过3D 编织制备预制体,再放入成型模具中使用RTM 工艺制造复合材料风扇叶片的技术手段,主要代表型号有CFM 公司的LEAP-X 发动机风扇叶片(见图7(b))。
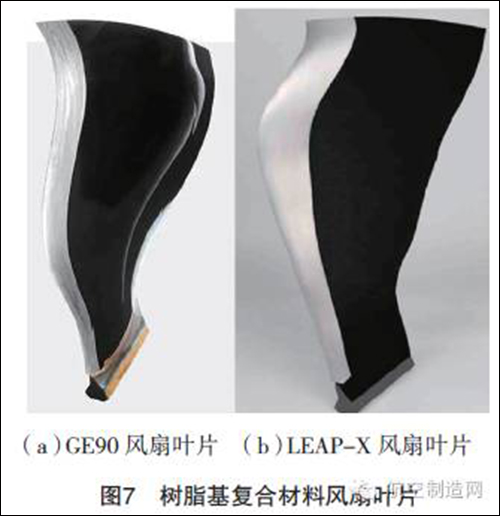
为提高叶片的抗冲击性能,需要在复合材料叶片缘头增加金属加强边,目前金属加强边的制造方法主要有:数控加工法、超塑成型/ 扩散连接工艺成型法、金属沉积成型法,GE公司采用数控加工技术加工钛合金包边且效果良好,其他相关技术尚未有文献报道应用于现役航空发动机。国内在相关技术领域的可查阅文献较少,但对于树脂基复合材料叶片的研究已经起步。
金属基复合材料叶片制造技术
金属基复合材料具有优于传统金属材料的比强度、比刚度和结构稳定性,可按需设计产品性能,实现结构功能的一体化(图8)。
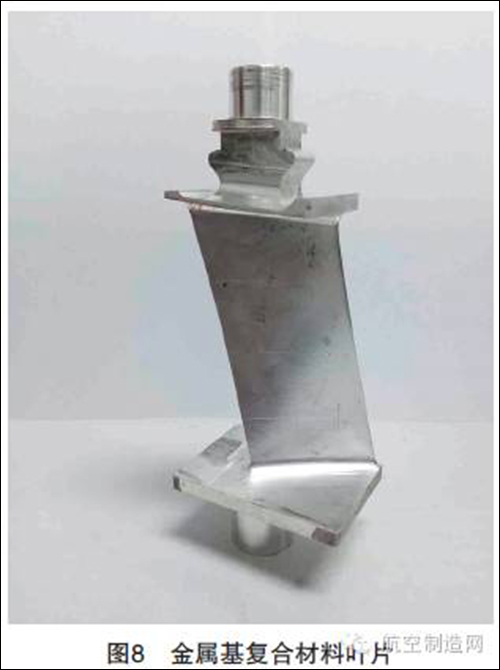
P&W 公司曾采用等离子喷涂与真空热压成形相结合的工艺成功研制B/Al 风扇叶片,该叶片通过了试验台、抗腐蚀及抗冲击试验,比原先的钛合金叶片减重40%,并成功应用于JT8D 的第一级风扇叶片和TF30的第三级风扇叶片;普· 惠公司和TRM 公司采用等离子喷涂6061Al的B/Al 预制带,成功研制了F100 的第一级风扇叶片与第一级出口导向叶片,并通过了静载和热疲劳试验,减重达35%~40% ;从PW4084 发动机开始,普·惠公司逐渐在风扇出口导流叶片上使用DWA 公司生产的挤压态碳化硅颗粒增强变形铝合金基复合材料。其研发工作表明:采用铝基复合材料的风扇出口导流叶片或压气机静子叶片,其耐冲击性能优于树脂基复合材料;普·惠公司还借助超塑成形/ 扩散连接工艺成功研制了碳化硅纤维增强钛基复合材料空心风扇叶片,该叶片可使发动机结构减重14%。
我国在原位自生TiB2 颗粒增强铝基复合材料风扇叶片研究方面取得了较大进展,但在其高效加工、表面强化、抗疲劳性能等方面仍存在诸多难点
陶瓷基复合材料叶片制造技术
陶瓷基复合材料(CMC)既保留了陶瓷耐高温的特性,又具有很高的机械强度和抗热裂性。目前应用最为广泛的陶瓷基复合材料主要有两种,分别是碳纤维增韧碳化硅(Cf/SiC)以及碳化硅纤维增韧碳化硅(SiCf/SiC)。前者使用温度可达1650℃,后者可达1450℃。陶瓷基复合材料涡轮叶片的制造主要可分为“叶片雏形制造”和“精密去除加工”两个阶段。
叶片雏形制造
内核层叠+ 外层编织技术。西方国家在为新一代的航空发动机制造复杂曲面的CMC 叶片时,其总体思路是叶片内核层层叠加,外层编织保护,制造过程如下:(1)将连续的增强纤维制成预浸体;(2)通过精密预浸体切片与装配形成复杂构件的几何体,随后附加外包层;(3)制成的三维体在石墨箱体内将单晶硅高温浸润注入,实现其致密化;(4)施加表层保护后,成为结构件的雏形,如图9 所示。
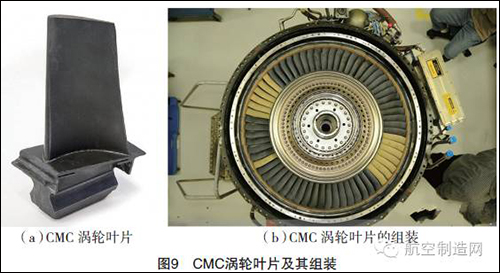
3D 打印技术。随着技术的进步与工艺的发展,3D 打印技术也逐渐成为制造陶瓷基复合材料叶片的先进手段之一。国内已经有研究采用凝胶注模成型技术成功制造出了金属增韧陶瓷基复合材料涡轮叶片,制造过程如下:(1)通过金属3D 打印工艺制备涡轮叶片的金属增韧骨架,然后通过气相沉积在金属增韧骨架表面形成陶瓷界面层;(2)将具有陶瓷界面层的金属增韧骨架与涡轮叶片的光固化树脂模具相结合,得到内部带有金属增韧骨架的树脂模具;(3)通过化学腐蚀方法去除树脂模具,采用真空冷冻干燥去除陶瓷坯体中的水分,然后在保护气氛下于1200~1400℃烧结3~6h,实现多孔复合材料涡轮叶片原型;(4)通过化学气相沉积在复合材料涡轮叶片的孔隙中生成碳化硅陶瓷进行致密化,实现陶瓷基复合材料涡轮叶片雏形的制备。
精密去除加工
通过上述技术成形的叶片雏形经过进一步的修边钻孔等精密去除加工,才能最终成为合格的产品。因此,能够满足制造高精度精密去除的加工技术是制造高质量叶片的关键之一。CMC 的叶片雏形不仅需要精密切边以实现配合所需的精度,还需要打冷却孔和安装孔,目前应用于CMC 切削加工的主要方式有水射流加工、电火花加工、超声加工(包括旋转超声加工)以及激光加工等。水射流加工容易造成材料的撕裂和表面崩口,电火花加工效率偏低,超声加工需要对刀具磨损进行精确补偿并解决好材料的崩边问题,激光加工很难避免热效应造成的影响。
综上,在采用去除加工工艺制造高质量、高效率的CMC 发动机叶片,其重点研究方向有:更精密的CMC预浸体切片与装配;更低成本、更小损伤的CMC 致密件切边与打孔工艺;CMC 安装孔成型工艺及表面精密磨、抛等处理工艺[28]
结束语
我国在航空发动机叶片制造技术领域既面临着难得的机遇,也承受着巨大的挑战。对航空发动机中最重要部件叶片的精密制造,需从以下几个方面进行探索。
(1)从设计、材料、工艺等多方面综合分析叶片的加工特性,完善对新材料、新工艺的技术探索。
(2)参考、借鉴、学习国外的成功应用,作实基础研究,深入探索加工方法与加工对象的精确匹配。
(3)研发叶片制造所需的关键特种制造工艺及装备,掌握特种叶片制造的核心工艺技术。唯有深入研究叶片制造基础理论,紧密结合工程技术应用,持续探索叶片制造的核心技术,最终必将提升我国航空发动机叶片的综合制造技术水平。
更多关于材料方面、材料腐蚀控制、材料科普等等方面的国内外最新动态,我们网站会不断更新。希望大家一直关注国家材料腐蚀与防护科学数据中心http://www.ecorr.org