风电作为快速发展的绿色可再生能源,逐渐成为许多国家可持续发展战略的重要组成部分。海洋风能资源丰富,比陆地高 20%-40%,风速高,发电量大,运行稳定,发展潜力大。根据我国国家风能资源普查数据,我国 5 米 -25 米水深50 米高的海上风力开发潜力 200GW,5 米 -50 米水深 70 米高的海上风电开发潜力 500GW,沿海潮间带、滩涂及深海的风能资源也较为丰富,海上风电建设成为风能开发利用的新方向。2015 年全球新增海上风电装机 4GW,累计海上风电装机11GW,预计到 2020 年全球海上风电装机将达到 40.3GW。
然而,与陆上风电相比,海上风电的技术要求更高,施工难度更大,运行环境更为复杂,造价约为陆上风电的 2-3 倍。
高湿度、高盐雾、紫外照射、海水浸泡、浪溅区形成的干湿交替等运行环境对海上风电设备的防腐提出了更高的性能要求。
海上风电腐蚀环境
海上风电的腐蚀环境较为严酷,其腐蚀区域可分为:海洋大气区、浪溅区、潮差区、海水全浸区和海泥区,风电机组各部位所处区域如图 1 所示。
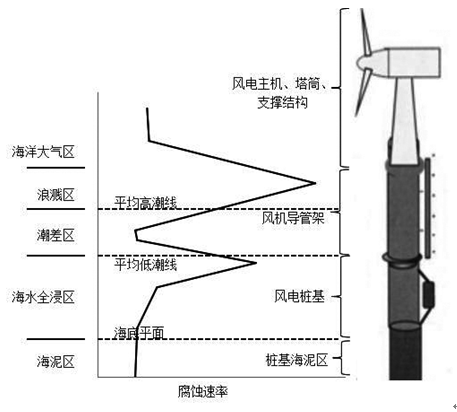
图1 海上风电机组的腐蚀分区
1、海洋大气区
海水蒸发形成了高盐含量高湿度的海洋大气,在钢结构表面可附着积聚盐分和水膜,同时由于钢结构成分中有少量碳原子的存在, 极易形成无数个原电池, 有利于电化学腐蚀的进行,腐蚀等级为 ISO 12944 规定的 C5-M 级,腐蚀速率为内陆地区大气腐蚀速率的 4-15 倍。海上风力发电机组并非全部完全曝露在 C5-M 的环境中,通过防腐结构设计,可将内部区域腐蚀等级下降。海上风力发电机组主要结构件及部件、设备所处海洋大气腐蚀环境细分如表 1。
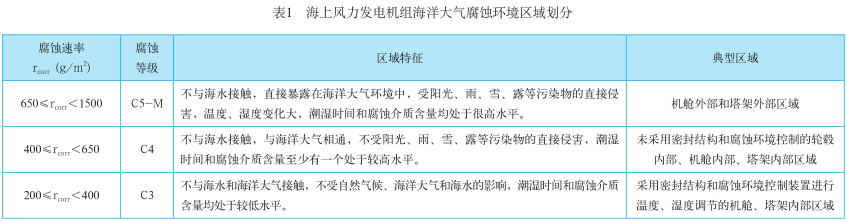
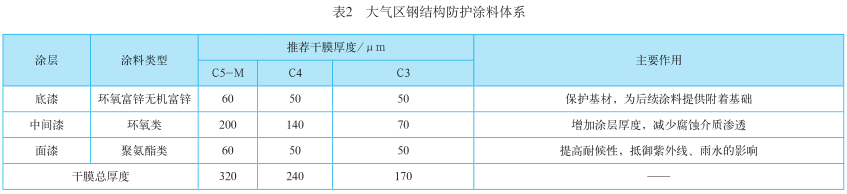
2、浪溅区与潮差区
浪溅区与潮差区均为干湿交替区, 表面盐含量高于大气区,海水氧含量高于全浸区,同时海水中夹杂的泥沙和海面浮游物体对其进行冲刷撞击,因此形成了最为苛刻的腐蚀环境。一般腐蚀速率为 0.3-0.5mm/ 年,最高可大 1mm/ 年,约为全浸区的 3-10 倍。
3、海水全浸区和海泥区
全浸区的设施长期浸泡在海水中,腐蚀受到海水盐度、海水温度、溶解氧浓度、水中污染物和海生物的影响。图 1 所示,在平均低潮位以下附近的海水全浸区又出现一个腐蚀峰值,在平均低潮位以上附件的区域则出现腐蚀最低值,这是因为随着潮位的涨落,水线上方湿润的钢表面供氧总要比浸在海水中的水线下方钢表面充分得多,而且彼此构成一个回路,形成氧浓差腐蚀电池,富氧区为阴极,得到了不同程度的保护,腐蚀最弱,相对缺氧区为阳极,则作为阳极而出现一个明显的腐蚀峰值。海泥区是饱和的海水土壤,盐含量高、电阻率低、供氧不足,还存在土壤的化学腐蚀与生物腐蚀。
海上风电防腐涂料设计
海上风电所处腐蚀环境是复杂的,海上风电机组的防腐蚀是一个系统的问题,对于机组的每一部分,首先在结构密闭性设计方面和材料选择方面应考虑到防腐蚀问题,再从防腐涂层方面进一步加强。针对各个部位的腐蚀特点,设计合理的涂层配套体系,才能保障风电设施的安全运行,达到设计寿命 20年以上。我国海上风电防腐涂料的设计标准未完善,通常采用或借鉴海洋工程的设计规范,如 ISO 12944、NORSOK M501、JTJ 275 等。
1、海洋大气区
对于海洋大气区的钢结构,包括主机和塔筒,一般采用涂层保护或喷涂金属层加封闭涂层保护,“环氧富锌底漆 + 环氧云铁漆 + 脂肪族聚氨酯面漆”的三层复合防腐体系为最常用涂层体系设计,见表 2。挪威标准 NORSOK M501 要求该涂层体系需耐受 4200h 循环老化试验,即“72h 紫外老化试验(UVA-340)-72h 盐雾试验 -24h 冷冻试验(-20℃)”为一个周期,共进行 25 周期,腐蚀蔓延≤ 3mm。目前常用 NORSOK M501 标准要求来评价风电海洋大气区钢结构涂层性能。
厦门双瑞涂料公司研发的涂层体系“725-H06-21 环氧富锌底漆 +725-H53-81 环氧中间漆 +725-S52-60 脂肪族聚氨酯面漆”可满足 NORSOK M501 要求,经 4200h 的循环老化试验后,人造划痕的腐蚀蔓延平均仅为 1.7mm,粉化 0 级,试验样板见图 2。试验结果表明该配套体系具有优异的屏蔽性和耐候性,可抵挡海上盐雾和紫外的侵蚀,是耐 1000h 盐雾 400h 紫外老化的常规配套不可比拟的。同时,该配套体系固体含量高,涂布率高,VOC 排放少,其中 725-S52-60 的体积固含可达到72%。该配套体系在塔筒的防腐涂装见图 3。对于海洋大气区的风电叶片,一般采用腻子修补缺陷后涂装叶片涂料来进行防护,推荐设计如表 3。叶片涂料的性能需通过 DNV-GL 船级社的认证,其要求叶片涂料的部分检测项目见表 4。
厦门双瑞涂料公司开发了 725-N43-92 聚天门冬氨酸酯叶片涂料,可达到表 4 的认证要求。这是一种新型脂肪族、高性能双组分涂料,被称为第三代聚脲,与传统的聚氨酯叶片涂料相比,具有更为优异的附着力、 快干性、 耐候性、耐磨性、耐盐雾性等优点。725-N43-92与某进口聚氨酯叶片涂料比较,在固体含量和一次涂装厚膜化方面更胜一筹,施工省时省料,可有效降低涂装成本。
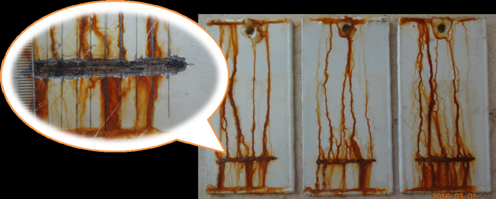
图2 双瑞大气区涂料体系NORSOK M501试验结果
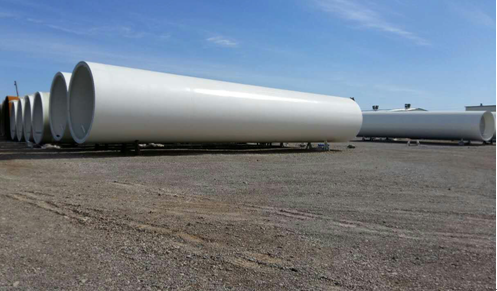
图3 双瑞大气区涂料在海上风电塔筒的应用
2、浪溅区与潮差区
浪溅区与潮差区钢结构的防腐蚀一般采用重防腐涂层,亦可采用包覆玻璃钢、树脂砂浆以及包覆合金等方法进行保护,重防腐涂层通常与阴极保护联合使用。浪溅区与潮差区的涂层设计见表 5,这是防腐的重点区域,可采用环氧玻璃鳞片涂料或者无溶剂环氧涂料。
NORSOK M501 对浪溅区与潮差区的重防腐涂料提出性能要求,循环老化 4200h人工划痕腐蚀蔓延≤ 8mm,耐阴极剥离试验 4200h 人造孔剥离直径≤ 20mm,耐海水浸泡 4200h 人造划痕腐蚀蔓延≤ 8mm。
浪溅区与潮差区的钢筋混凝土承台一般采用“环氧封闭漆 + 重防腐涂料 + 聚氨酯面漆 / 环氧面漆”的复合涂层体系进行防腐,见表 6。厦门双瑞涂料公司针对浪溅区的特殊要求,开发了 725-H53-38 环氧玻璃鳞片涂料,经 4200h 循环老化试验腐蚀蔓延为 6.5mm,4200h 耐阴极剥离试验剥离直径为 6.1mm,4200h 海水浸泡试验腐蚀蔓延 0.2mm,表现出优异的性能,见图 4。双瑞特有的高触变技术赋予该产品优异的施工性能,体积固含高达 85%,粘度仅约2000cP,且可实现大于 300?m/ 道的厚膜施工。
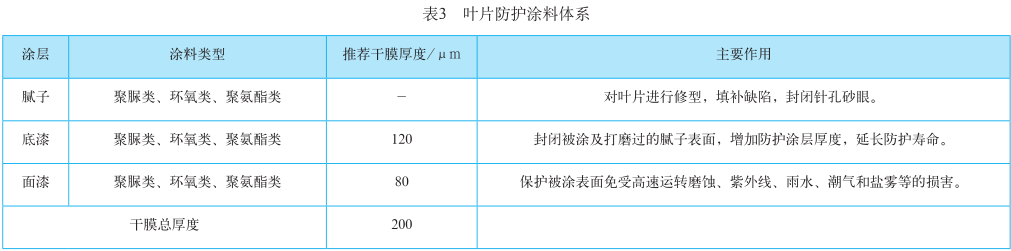
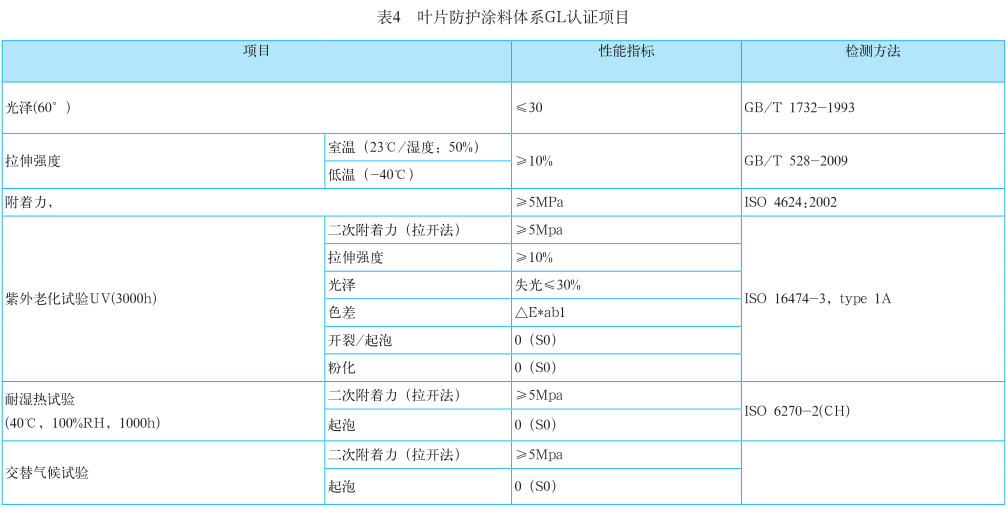
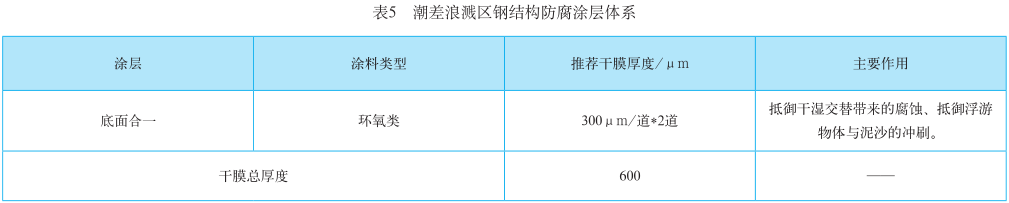
3、海水全浸区
水下全浸区的钢结构防腐蚀一般采用重防腐涂层与阴极保护联合防腐的措施,也可单独采用阴极保护,当单独采用阴极保护时,应考虑施工工期的防腐措施。全浸区的涂料体系可与潮差区一致,设计见表 7。NORSOK M501 规定了全浸区的重防腐涂料的性能要求,耐阴极剥离试验 4200h 人造孔剥离直径≤ 20mm,耐海水浸泡 4200h 人造划痕腐蚀蔓延≤ 8mm。
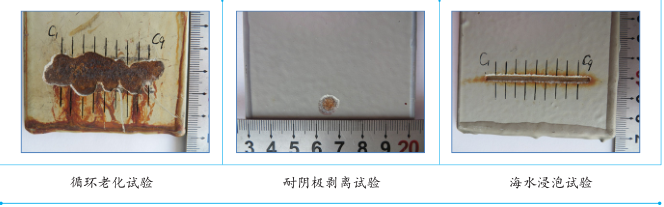
图4 双瑞浪溅区涂层NORSOK M501试验结果
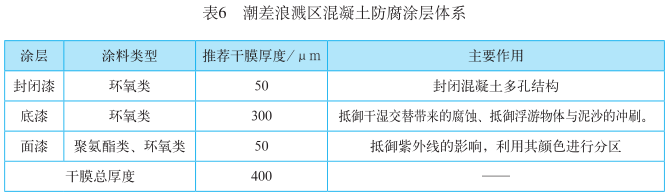

4、海泥区
对于深入海泥区的基础钢结构,一般不涂装防腐涂层,只采取阴极保护措施,也可采用防腐涂层加阴极保护联合防腐措施。
结语
防腐涂料体系是依据腐蚀环境设计的,海上风电的腐蚀环境特点不同,决定了涂层设计的差异,文中介绍了目前风电机组自大气区到海泥区的防腐涂料体系设计,但我国海岸线长,各海域腐蚀环境存在差异,应依据实际环境调整设计。文中未提及风电设备电气元器件和紧固件的防腐设计,这也是风电防腐需要关注的部分。我国海上风电装机量已排名世界第三,随着海上风电产业的快速发展,要求进一步提升风电腐蚀防护涂料的产品性能和涂装技术,同时前期的风机逐渐进入待维修状态,海上风电的维修难度大,将是未来严峻的挑战。
作者简介
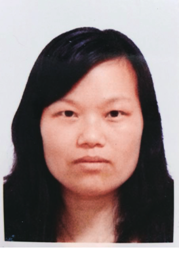
苏雅丽,女,高级工程师,硕士,厦门双瑞船舶涂料有限公司研发部部长。长期从事船舶涂料和工业涂料的开发工作,参与科技部、工信部、国防973、总装预研等多项涂料研究课题。主持修订国家标准GB/T 6747《船用车间底漆》,目前已申请3项国家发明专利,其中1项获得授权。