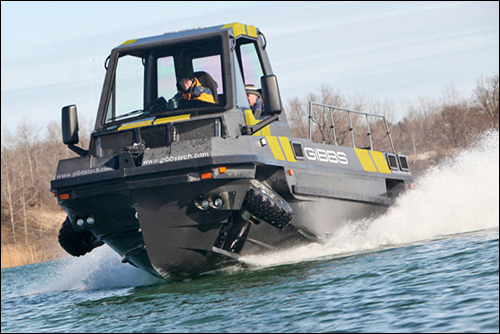
0 引言
铝合金材料具有比重轻、硬度大、耐腐蚀性好的特点,广泛应用于航空航天工业和国防工业中,沿海两栖车辆主要采用此种材料。海水具有强电解质特性,加之海水的冲击加剧材料失效,海水中的气泡对金属表面的保护膜及涂层有很大的破坏性,导致漆膜老化加快,铝合金材料在高温、高湿、高盐雾以及高日照的苛刻海洋环境中面临严重的腐蚀问题。海洋环境中铝合金构件最易发生点蚀现象,它是晶间腐蚀和剥蚀等其他形式腐蚀的起源,如疲劳腐蚀的裂纹源正是从点蚀开始的。腐蚀的产生极大地降低了车体铝合金构件的使用寿命和整体的可靠性,直接制约了两栖车辆在海洋环境中的应用和性能的发挥,因此,开发和使用高效的海洋环境下两栖车辆腐蚀防护技术,对减小海水对两栖车辆的腐蚀破坏,保证车辆的可靠性有着极其重要的意义。
1 两栖车辆腐蚀现状
海洋环境中两栖车辆构件的腐蚀问题主要包括: 点蚀、缝隙腐蚀、电偶腐蚀、应力腐蚀、剥蚀、晶间腐蚀、磨损腐蚀、腐蚀疲劳等腐蚀形态,这些腐蚀问题与结构设计以及冶金因素密切相关。通过分析车辆零部件在干湿交替、振动、冲击等复合工况中所产生的腐蚀故障问题,统计分类研究,归纳总结海洋环境中两栖车辆的腐蚀状况和特征。
1. 1 车辆外部腐蚀问题
两栖车辆采用的材料一般为Al-Zn-Mg 超硬铝合金,该材料具有高的比强度、优良的可焊性、较好的断裂韧性,但是其应力腐蚀敏感性和剥蚀倾向较大。两栖车辆的铝合金表面由于预处理工艺不当易存在的缺陷,车辆使用时,表面缺陷与海水中的活性氯离子促进阳极反应,形成点蚀孔,导致涂层脱落严重;两栖车辆构件中使用材料种类较多,当腐蚀电位相差较大的异种金属材料互相搭接使用时,易发生严重的电偶腐蚀问题;海滩砂石与车体底部铝合金相互摩擦,易导致车体底部腐蚀磨损严重,其腐蚀状况如图1 所示。

两栖车辆下海时,海水浸没的部分在上岸以后难以彻底清洗干净,缝隙间滞留海水中的氧在修复金属表面钝化膜时消耗加快,易造成严重的缝隙腐蚀,导致诱导轮、主动轮以及螺栓等严重锈蚀。铝合金构件承受大的拉伸应力,在腐蚀介质下易产生应力腐蚀,在环境腐蚀和动循环载荷的同时作用易引起严重的腐蚀疲劳损伤。
1. 2 车辆内部腐蚀问题
在车辆内部,由于密封不严导致海水渗漏到车内,在局部运动构件内形成高温盐雾的腐蚀环境; 部分零件浸泡在海水中,表面涂层不能抵御侵蚀,锈蚀问题严重; 车辆保养过程中用淡水难以清洗干净,加剧了零部件的腐蚀,如离合器、螺栓螺杆锈蚀严重、拉杆接头及销子等部分零件锈蚀致使操纵阻力变大、制动弹簧件的失效和断裂直接导致操作失灵; 电子仪器设备和线路在实际使用中,易发生绝缘击穿、接触不良、电阻值改变等问题,导致电器故障频发;海水渗漏到发动机部分机件,在发动机工作部件产生高温的情况下,形成高温盐雾腐蚀环境,致使发动机冷排气管道、发动机支架及附件等腐蚀严重,腐蚀状况如图2 ~ 图4 所示。
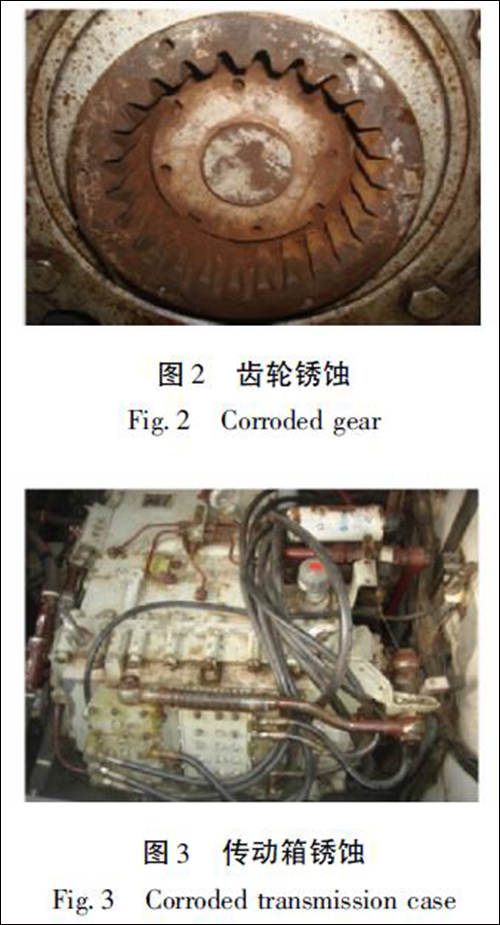
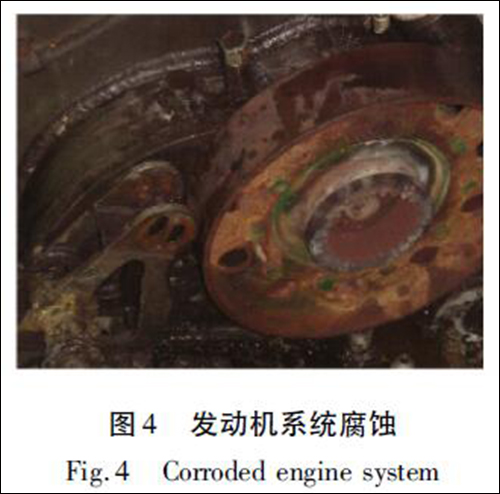
2 两栖车辆腐蚀综合控制技术
两栖车辆腐蚀问题具有多诱因、大范围和全方位的特征,是涉及材料、环境、机械、腐蚀等多学科的复杂难题,严重腐蚀现状导致两栖车辆的性能降低,维护保养困难,维修费用增加,形势严重。
2. 1 腐蚀综合控制理论
两栖车辆在使用中,零部件易发生锈蚀、退化、变质等腐蚀现象,控制零部件的锈蚀、退化、变质等腐蚀问题,有助于两栖车辆的性能发挥以及车辆安全可靠性和使用寿命的提升。腐蚀综合控制需采取全寿命、全系统的有效防腐措施,这些措施包括防腐蚀设计、防腐蚀技术工艺、两栖车辆维修和日常维护保养等全过程中腐蚀预防体制的建立: 1) 合理的防腐蚀结构设计; 2) 良好的耐腐蚀材料; 3) 正确地选用表面工程技术; 4) 合理采用阴极保护技术;5) 采用密封剂或缓蚀剂进行两栖车辆内部的环境隔离; 6) 在两栖车辆的运行、运输、停放等过程中建立腐蚀预防制度; 7) 控制两栖车辆的各级维修过程,有效进行装备的防腐保护为原则; 8) 进行两栖车辆的腐蚀控制管理,实施全方位、全过程、全员参与的腐蚀控制系统工程。
要获得经济、高效、高质量的防腐工程设计,提高车辆可靠性和延长两栖车辆的使用寿命,首先需要认识两栖车辆的性能要求及运行环境状况、可能发生的失效类型,从而确定设计和选择的各项技术;其次是了解各种技术的工艺特点及其适用范围的基础上,选择合适的工艺并制定相应的配套工艺。在两栖车辆防腐工程设计中应遵循以下原则: 1) 采用耐腐蚀材料,提高零件自身性能; 2) 材料耐蚀性差的零部件表面采用先进适用的涂覆层保护; 3) 有效密封、及时除湿使两栖车辆零部件、系统处于相对干燥环境; 4) 经济上的合理性,防腐技术使用后要有一定的经济效益,如两栖车辆的使用性能提高、使用寿命的延长、故障与维修的减少,两栖车辆在使用的全过程中成本降低等。
两栖车辆腐蚀综合控制关键在于建立覆盖设计、制造、使用及维修的腐蚀控制技术体系,以需求为牵引,在设计制造方面,注重防腐结构设计和材料的选用; 在技术方面,采用涂层技术、缓蚀剂以及阴极保护等相关技术解决不同部位的腐蚀问题; 在维修方面,侧重于维护管理制度实施和专业技术人才的培养。采取系统集成、综合应用多种新材料、新技术、新方法并与装备维护保养和维修制度相结合的腐蚀控制系统方法,有效提升两栖车辆的防腐能力。
2. 2 腐蚀综合控制技术
根据两栖车辆腐蚀状况、腐蚀规律的不同,以及各部位采用腐蚀控制技术方法的不同,将两栖车辆划分为车体部分、车底部分、异种金属连接部分、整车等进行腐蚀防护。
2. 2. 1 新型Al-Zn-In-Mg-Ga-Mn 六元牺牲阳极材料
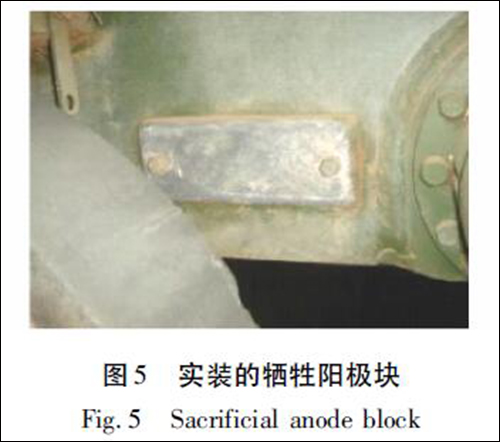
针对两栖车辆现用牺牲阳极在干湿交替使用中出现启动时间慢、阳极表面结壳、电流效率低等问题,提出采用建立车体电位平衡时间、阳极块电流效率作为评价标准,通过添加Ga、Mn 元素调整阳极材料配方,研制新型高活化和高极化速度的Al-Zn-In-Mg-Ga-Mn 六元牺牲阳极材料( 见图5) 。通过对新型六元阳极材料电化学性能测试、金相组织观察和溶解形貌扫描电镜观察,进一步分析新型六元阳极材料的溶解和活化性能的影响与作用机制,验证了牺牲阳极溶解———再沉积理论,建立六元牺牲阳极工作过程模型,分析其热力学和动力学工作过程,采用BESAY 阴极保护数值模拟软件设计与布置,系统设计车辆牺牲阳极保护方案并模拟其保护效果,优化阳极块分布,安装匹配车体阳极块,力争使保护效果显著提高。
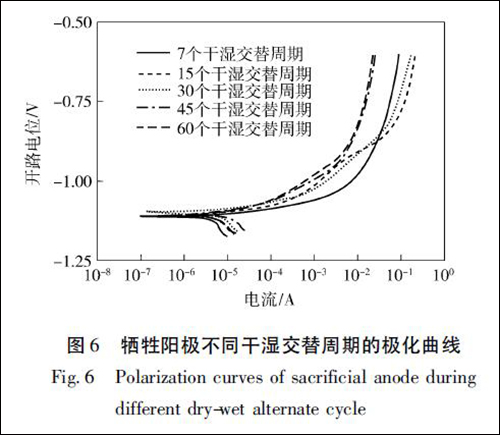
从图6 测试的结果中得到,在整个试验周期内,牺牲阳极具有小于- 1. 10 V 的开路电位,随着电位升高,各周期阳极电流急剧增加,浸入活化状态,且其极化率很小,表明该阳极输出电流能力较好。在45 和60 个工作周期时,维钝电流变小,说明牺牲阳极表面已经开始钝化。通过实车保护电位测试,试验表明: 在干湿交替条件下,新型六元牺牲阳极保护下的车体电位平衡建立时间缩短至5 min 以内,车体平均电位负移50 mV,工作电位达到- 1. 10 V,电流效率高达90%,溶解形貌均匀,腐蚀产物自动脱落,无结壳现象,对车体起到很好的保护作用。
2. 2. 2 陶瓷型耐磨蚀涂层
针对两栖车辆铝合金底板磨损、腐蚀严重等问题,在底甲板处涂覆陶瓷型耐磨蚀涂层,该方法选用环氧树脂作为粘料、脂肪胺与芳香胺作为混合型固化剂、Al2O3颗粒作为耐磨填料。利用“颗粒级配”理论,解决了涂层耐磨难题,利用“脱模定型”
工艺,解决了涂层粗糙和针孔难题,运用堆积级配理论,通过正交试验,对Al2 O3涂层填料的颗粒度、颗粒级配组合进行优化,确立了陶瓷型涂层的配方与成分,测试和分析陶瓷型涂层的相关性能,研究陶瓷涂层耐磨蚀机理,结合实车涂覆规范工艺,规范施工工艺流程,优化工艺参数,有效降低了陶瓷涂层缺陷,提高了两栖车辆底板的耐磨蚀能力。
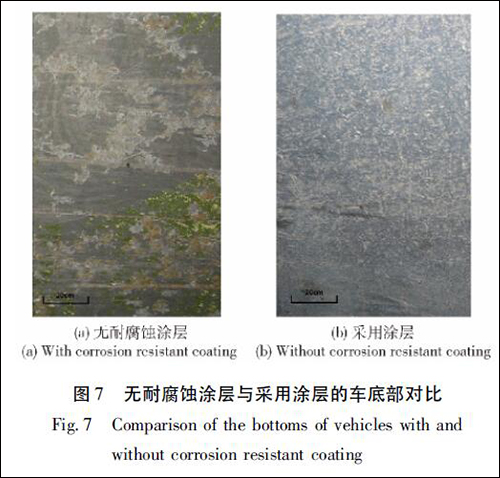
经过实车测试试验,结果表明: 车体底板陶瓷耐磨蚀涂层化学稳定性好,与车体结合强度高,达到30 MPa,邵氏硬度80 ~ 90 HA,相对耐磨性4 ~ 5( 45 号钢为1) ; 涂层无脱落,无锈蚀; 无明显划痕( 涂层效果对比见图7) 。
2. 2. 3 复合防腐涂覆层技术
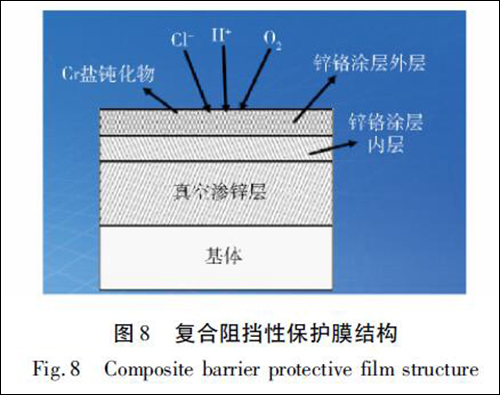
针对履带腐蚀锈死问题,研究采用化学镀Ni-P合金镀层、真空渗锌、锌铬涂层等复合涂覆层对履带进行防护,通过从单一涂层到涂覆层的系统试验,得到涂层总厚度为40 ~ 60 μm 真空渗锌+ 锌铬涂层+ 高分子厌氧胶的复合防腐涂覆层技术方法( 复合涂覆层结构见图8) ,能够有效解决履带腐蚀问题。

经过实车测试试验,结果表明: 复合涂层在一个工作期内能够对履带起到较好的防腐作用,防腐效果优于单一的锌铬涂层和化学镀Ni-P 合金镀层,锈蚀情况大大减少,可轻松实现履带紧固件的多次拆卸,降低车辆维修保养强度( 效果对比见图9) 。
2. 2. 4 异种金属电位匹配技术
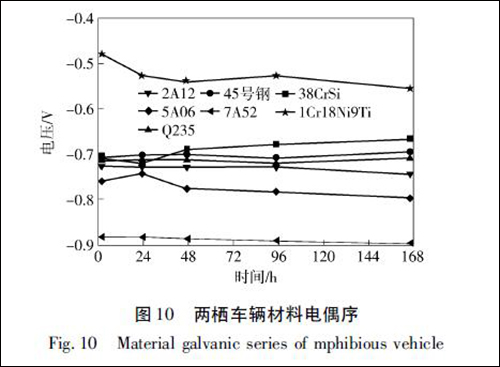
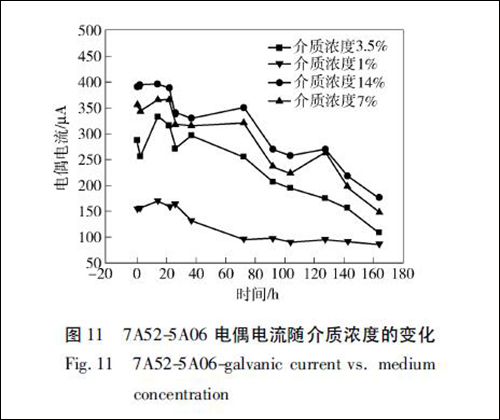
针对两栖车辆中异种材料连接带来的电偶腐蚀严重的问题,在全面统计两栖车辆上使用的各类材料基础上,系统整理了车体上金属连接件的数量、位置、名称及所使用材料的表面处理,确定了某种两栖车辆上共使用了26 种材料,共产生30 多种异金属固定连接, 150 多种异金属部件活动连接,建立了两栖车辆电偶腐蚀数据库。通过电偶基础实验( 材料电偶测试曲线见图10、图11) ,得到主要材料在海水中的电偶序: 7A52、5A06、2A12、Q235、45 号钢、38CrSi、1Cr18Ni9Ti 的自腐蚀电位。
通过研究1%、3. 5%、7%、14% 4 种浓度条件下的电偶电流,结果显示: 电偶电流随着介质浓度的增加而增加; 介质浓度较低时,增加介质浓度对电偶电流影响较大; 介质浓度大于7% 时,介质浓度的改变对电偶电流影响较小,表明电解质浓度的改变在一定范围内对电偶腐蚀影响较大。同时研究了阴/阳面积比、温度和含氧量对电偶腐蚀的影响,模拟两栖车辆在干湿交替状态下电偶腐蚀现象、特点,提出两栖车辆电偶腐蚀防护原则为: 1) 尽量避免腐蚀电位相差悬殊的异种金属做直接导电接触; 2) 腐蚀电位相差悬殊的异金属必须组装在一起时,应采取可靠的绝缘措施; 3) 有效控制阴/阳面积比,抑制加速电偶腐蚀的因素。
根据两栖车辆电偶腐蚀防护原则,研究制订异种金属电偶腐蚀防护措施,见表1.
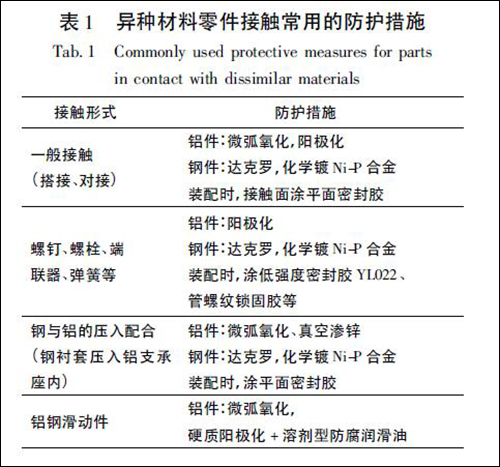
经过实车测试实验,结果表明: 两栖车辆电偶腐蚀数据库为两栖车辆腐蚀综合控制打下基础,提出的电偶腐蚀控制原则和防护措施使异种材料的电偶电位相差小于0. 05 V,大大降低了两栖车辆电偶腐蚀程度。
2. 2. 5 高分子密封胶防腐技术
在两栖车辆的设计中,采用了机械密封设计,如密封圈、密封垫等密封技术,一般情况下,在两栖车辆的使用和维修中,不会改变原有的密封设计。为了改善装备的防腐效果,更多是采用高分子密封防腐材料,以填充的方式隔离腐蚀介质,起到防护作用。消除密封间隙的技术方法就是在需要密封的部位涂一些高分子密封胶,这些高分子胶经固化后就密封了间隙。图12 为系列防腐密封材料。
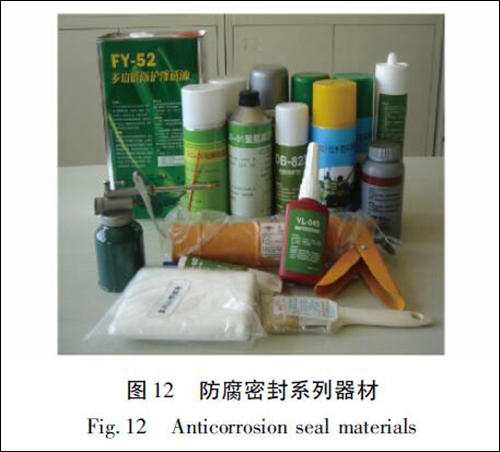
对于两栖车辆的车外紧固螺栓,螺栓螺纹与螺母螺纹之间总是存在一定间隙( 内螺纹设计所致) ,在海水中,海水会渗入间隙而造成螺纹的锈蚀,甚至形成“锈死”现象,在海水或盐雾环境中锈蚀严重。在车辆维修保养时,经常需要拆卸这些螺栓,在拆卸过程中,已经严重锈蚀的螺栓很难顺利拆卸,严重时易造成螺栓被拧断的现象,给维修保养带来困难。要消除螺纹锈蚀现象的根本途径是消除间隙,让海水无空可渗。在高分子螺纹密封锁固胶的系列产品中,设计有两个功能: 一个是螺纹间隙的密封,另一个作用是锁固,使螺栓不会在使用时松动脱落。对于两栖车辆的车外螺栓,主要是密封防腐,锁固功能是次要的。用低强度的高分子螺纹密封锁固胶,而决不可选用高强度和超高强度胶,否则螺栓拆卸时相当困难,甚至无法卸下。
两个平面之间的密封,例如发动机上、下箱体的密封、变速箱上、下箱体的密封等,大都采用固体衬垫密封,使用中渗漏现象比较普遍。采用高分子平面密封胶进行密封,大幅度提升了密封可靠性能。在装配前,将膏状的密封胶涂在密封平面上,利用高分子密封胶优良的填充性使平面的不平度、粗糙度等缺陷填平。当合上对偶平面并固化后,形成了一个密封性优良的密封层,阻绝海水进入密封零部件内,大大降低两栖车辆的内部腐蚀问题。
3 结论
海洋腐蚀环境具有多样性和复杂性的特点,导致在海洋环境中使用的两栖车辆的腐蚀防护工作是一项复杂的系统性工程。两栖车辆各部位工作环境、腐蚀状况、腐蚀规律是不同的,所以,对于各部位采用的腐蚀控制技术应当是不同的,不能一概而论。当前,针对海洋环境下材料的腐蚀防护技术有很多,每项技术都有其鲜明的特点,体现在使用环境的不同、防护寿命的差异和成本的高低等方面。采用综合防腐控制技术的目的,在于整合现有的各种防腐技术的独特优势,并针对两栖车辆不同部位在海洋环境下产生的腐蚀情况不同,提出综合性地解决方案,使得两栖车辆在综合性地兼顾了相关腐蚀防护因素之后,进而在两栖车辆的整个腐蚀防护设计及控制层面上达到最优。两栖车辆腐蚀综合控制技术研究是一项系统工程,必须树立全系统和全过程腐蚀综合控制思想,制定以预防、控制和治理为主要内容的工艺规程,构建两栖车辆腐蚀控制维修保障的配套技术手段,从顶层到控制各层面发展和完善两栖车辆腐蚀控制理论体系,对海洋环境下两栖车辆腐蚀问题的控制和解决具有重要的意义和价值。