顶刊综述:碳纳米管纤维研究及未来
2019-07-05 09:30:23
作者:本网整理 来源:材料科学与工程
碳纳米管是一种潜力巨大的超级材料,是构建未来超强结构和碳基半导体器件的理想核心基础材料。将碳纳米管组装成宏观体(如纤维、薄膜和泡沫等)是实现碳纳米管宏量应用的重要途径之一。碳纳米管纤维是碳纳米管的一维连续组装体,其不仅可以单独使用,而且可以通过编织形成二维薄膜或者三维编织结构,成为最受关注的碳纳米管宏观体。近二十年来,人们致力于开发碳纳米管纤维连续纺丝工艺,揭示碳纳米管纤维的工艺-结构-性能关系,并且开发碳纳米管纤维的工程应用等。现有的大量研究已经表明,碳纳米管纤维在结构功能一体化复合材料、纤维状能源器件、人工肌肉以及轻质导电线缆等方面具有非常广泛的应用前景。然而遗憾的是,从纳米尺度的单根碳纳米管到宏观尺度的碳纳米管纤维,碳纳米管在力、电、热等性能上发挥的效率甚至不到10%,限制了碳纳米管纤维的工程化应用。理解和明晰碳纳米管纤维的工艺-结构-性能关系是进一步提升碳纳米管纤维性能的关键。
中国科学院苏州纳米技术与纳米仿生研究所研究员李清文团队自2007年成立以来,在碳纳米管纤维领域开展了大量的基础研究与应用开发工作。近期,该团队应邀在《先进材料》(Advanced Materials)期刊撰写综述文章(DOI:10.1002/adma. 201902028),系统回顾过去近二十年来人们在碳纳米管纤维基本物性研究方面开展的工作,并对碳纳米管纤维未来的发展关键做了展望。
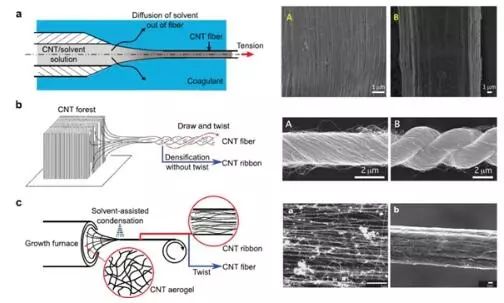
回顾碳纳米管纤维的发展历程可以发现,我国在国际上较早开展碳纳米管纤维研究。2000年,法国科学家首次报道了通过湿法纺丝工艺,制备碳纳米管含量高达50%以上的连续纤维材料,拉开了碳纳米管纤维研究的序幕。2002年,清华大学教授吴德海团队和美国伦斯勒理工学院教授P. M. Ajayan合作,首次报道了利用浮动化学气相沉积方法制备直径约为300至500微米的碳纳米管束,其长度达到20厘米;同年,清华大学教授范守善团队首次报道了从碳纳米管阵列拉丝制备碳纳米管纤维的方法;2004年,我国科学家李亚利在英国剑桥大学访学期间,与Alan Windle教授合作,实现了浮动催化化学气相沉积法连续制备碳纳米管纤维。期间,美国科学家报道了湿法制备纯碳纳米管纤维工艺。2018年,清华大学教授魏飞团队报道了厘米级碳纳米管管束,其强度达到80 GPa。总体来看,自2000年左右科学家成功实现碳纳米管在宏观尺度的纤维组装后,碳纳米管纤维的研究迅速兴起,并在20年的发展中大体经历了三个发展阶段:
(1)碳纳米管纤维纺丝方法的探索阶段——基于凝固过程的湿法纺丝、利用碳纳米管垂直阵列的抽丝纺纱以及基于生长过程预形成碳纳米管凝胶的直接纺丝成为当前最主要的制备方法;(2)针对碳纳米管纤维宏量连续制备、基本性能提升以及功能特性开发的快速发展阶段;(3)当前碳纳米管纤维的发展已进入到产业应用的攻关阶段,如何啃下硬骨头需要科研工作者以及产业界的共同努力。
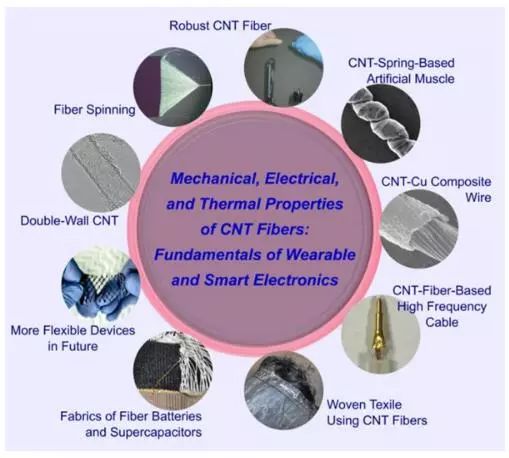
基于不同的纺丝方法,碳纳米管纤维展现出极为丰富的组装结构。相比于其微观结构,碳纳米管在纤维中的取向度、紧密度、纠缠度,在纤维径向的分布差异、表面形貌等结构特性更加决定了纤维的宏观物性。更为重要的是,如果在改进纤维组装结构的基础上,对管间的力、电、热的传递进行有效调控,是提高纤维性能、充分发挥单根纳米管性能的关键所在。
在该研究进展的综述中,作者分别对碳纳米管纤维的力、电、热性能进行了全面的阐述。在力学性能方面,目前可以通过溶剂致密化、机械致密化、逐级牵伸、纤维内引入聚合物网络结构、管间诱导共价连接等方法实现纤维断裂强度和弹性模量的显著提升。另一方面,纤维内极为丰富的界面结构带来了多样化的能量耗散过程,使得碳纳米管纤维(以及薄膜和复合材料)展现出传统碳纤维所不具备的阻尼、蠕变等动态力学特性,实现了刚柔并济的双功能结合。此外,纤维的纱线结构以及独特的柔性,则在旋转驱动、生物电极等领域展现出独特的优势。 碳纳米管纤维还是优良的“导”体。在导电特性上,通过掺杂手段拓宽管间电子跃迁通道后,纤维在比电导率性能上有望超越金属导体的极限,在轻量化导线方向展现出发展优势;而通过与金属的复合,基于碳纳米管快速导热的性能,能够大幅度提高复合导体的极限载流能力,在未来超大电流的应用中有望取代传统金属导体。在导热特性上,由于独特的组装特性,纤维表面的热辐射尤为显著,导致在实际测量中表观热导率与实际热导率间存在巨大差异,并且前者随样品尺寸增加而快速发散。为此,除了优化纤维结构以改进管间声子输运之外,进一步发展测试方法也是碳纳米管纤维导热研究的重要内容。 在该综述中,作者分别对力、电、热性能相关的理论研究进行了介绍,指出未来纤维性能的进一步提高以及产业化实现的基础,依然在于对加工—结构—性能三者内在关系的深入认识。尽管碳纳米管纤维物性已有一系列突破、器件应用取得多项成功,从源头重新认知纤维的纺丝工艺过程依然显得尤为必要。
免责声明:本网站所转载的文字、图片与视频资料版权归原创作者所有,如果涉及侵权,请第一时间联系本网删除。