2018年我国粗钢产量达到9.28亿吨,同比增加6.59%。2018年中钢协会员单位转炉废钢料消耗、劳动生产率、利用系数指标均有一定提高,但是企业指标先进值与落后值的差距仍然较大,说明转炉技术进步还有较大潜力。电炉企业采取了吹氧、喷碳、余热回收等节电措施,对我国电炉工序能耗节约起到积极的作用。高效连铸技术的工业化应用取得很大成效,连铸生产的品种和质量均有较大提高,说明我国连铸技术已接近国际先进水平。
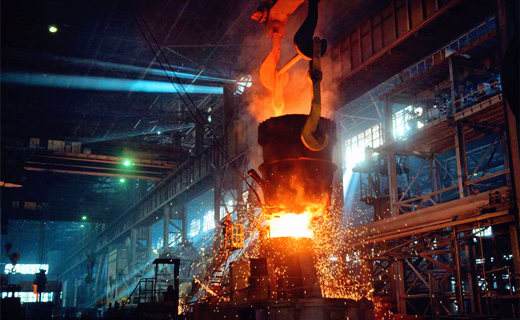
1 我国钢产量情况
2018年我国粗钢产量92826.44万吨,同比增加6.59%;占世界66个国家/地区总钢产量的51.87%。重点统计钢铁企业产钢量70621.72万吨,同比增加4.63%,其他企业产钢22564.72万吨,同比增加13.22%;说明钢铁产业集中度在降低。2018年中钢协会员单位转炉钢年产量620817.324万吨,同比增加5.65%;电炉钢年产量3802.372万吨,同比增加8.56%,电炉钢占比为5.384%;其他炉钢产量925.893万吨,同比增加4.63%,非合金钢产量321561.371万吨,同比降低1.86%,低合金钢产量288011.376万吨,同比增加12.33%;合金钢产量4995.477万吨,同比增加7.27%;不锈钢产量1158.88万吨,同比增加1.47%。非合金钢产量占比下降,合金钢和不锈钢产量增长,说明我国钢质量得到提升,钢的品种和结构得到优化。
2 转炉生产指标情况
因各钢铁企业之间的转炉炉容不同、装备水平不同、冶炼钢种不同、生产条件不同、操作技术水平不同等情况,造成企业之间的技术经济指标有较大差异。表1为2018年中钢协会员单位转炉生产指标。
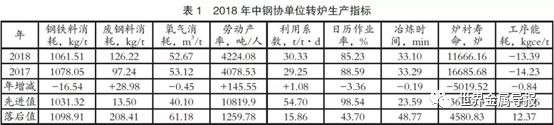
2.1转炉钢铁料消耗分析
理论上,转炉用热铁水冶炼,要吹掉铁水中4%左右的碳,还要脱除铁水中硅、锰、硫、磷等元素,炉渣还要带走1.5%-2.0%的金属,转炉尘泥中也有一定的金属量。所以说,转炉一般钢铁料消耗不应低于1060kg/t。据统计,2018年中钢协会员单位中,有18家单位钢铁料消耗低于1060kg/t,最低的企业钢铁料消耗仅为1031.32kg/t。转炉努力降低钢铁料消耗是未来的技术发展方向,有利于降低成本,提高劳动生产率。
2.2废钢料消耗分析
技术上,转炉冶炼可以消耗15%-20%的废钢料,有利于提高钢产量、节能减排、降低氧气消耗、减少冶炼时间,是技术发展方向,但要求铁水温度要高。2018年社会废钢量增加且价格偏低,有利于转炉多用废钢;所以2018年中钢协会员单位转炉多用废钢28.98kg/t,是好的势头,有46家企业增加了废钢使用量,占统计单位的77%。
2.3氧气消耗分析
一般转炉冶炼消耗氧气在50-55m3/t,耗氧量与冶炼钢种有关,正常波动范围<0.2m3/t。用废钢量多、用热铁水多、冶炼高级钢种及操作水平等因素,均会对转炉氧气消耗有影响。据统计,2018年中钢协会员单位中有14个单位氧气消耗低于50m3/t,有10个单位氧气消耗高于55m3/t;2018年有26个单位氧气消耗得到下降,氧气消耗最高的企业达61.58m3/t。
2.4冶炼时间分析
转炉冶炼开始时是先进行铁水脱碳、脱硅、脱锰、脱硫等,此时可以进行煤气回收,时间约为冶炼时间的一半。因企业之间使用铁水中含碳、硅、锰、硫量的不同,各企业间转炉吹炼时间是有差异的。以后的冶炼是对钢水进行质量调整及温度控制,因各企业之间冶炼钢种的差异,所用时间也有不同。
2018年中钢协会员单位转炉冶炼时间平均为33.10min,同比下降0.19min,冶炼时间最短的企业是石横特钢为23.59min。各企业之间因生产条件不同(钢种、使用废钢料、铁水成分、供氧强度、操作技术等),冶炼时间差异较大。
2.5转炉工序能耗分析
转炉工序能耗包括铁水预处理、转炉冶炼、转炉精炼和连铸的能耗。2018年它们的能耗值分别为0.34kgce/t(0.04kgce/t)、-18.57kgce/t(-0.25kgce/t)、8.68kgce/t(+0.21kgce/t) 和6.29kgce/t(-0.16kgce/t)。括号为2018年与2017年数据比较的变化值。
2018年中钢协会员单位钢产量占全国钢产量的75.69%;因打击地条钢,社会废钢量增加,价格下降,转炉使用废钢量增加28.98kg/t,同比增加40.08%,使钢产量增加。2018年中钢协会员单位转炉工序能耗为-13.39kgce/t,同比升高0.84kgce/t。
转炉工序煤气消耗占能源总量的42%,电力和氧气各占消耗的20%左右;转炉能源回收中,蒸汽占27%,煤气回收占73%;提高煤气回收量,转炉工序能耗值就可实现为负值。一般煤气回收量大于100m3/t,蒸汽回收量大于80kg/t的企业,转炉工序就可以实现负能炼钢。2018年会员单位转炉煤气回收量为115.32m3/t,同比升高1.25m3/t。转炉工序能耗升高的主要原因是煤气和蒸汽进行回收利用,可回收约24kgce/t的能量,实现负能炼钢。
验证企业转炉炼钢能耗时,不仅要看煤气回收量,还要看煤气的发热值,这样才科学。企业对标时,要看回收煤气量和煤气热值,如蒸汽回收量大,必然要多烧一些转炉煤气。所以,对转炉工序能耗对标时要进行综合分析。
3 电炉技术经济指标分析
2018年我国电炉钢产量3802.37万吨,同比增加8.56%,电炉钢占比为5.411%,呈升高趋势。打击“地条钢”生产后,一批企业没有停产,又建设了电炉,故电炉钢产量统计数据偏低。2018年中钢协会员单位的电炉金属料消耗升高12.59kg/t,使用钢铁料反而减少76.56kg/t,电炉冶炼综合电耗334.51kWh,同比下降7.55kWh;冶炼时间1.00h,同比增加0.01h。2018年中钢协会员单位电炉技术经济指标见表2。
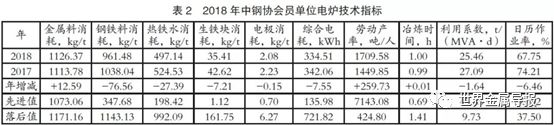
3.1电炉工序能耗分析
2018年中钢协会员单位,电炉工序能耗包括电炉冶炼能耗、电炉冶炼电耗、电炉精炼能耗、电炉精炼电耗和连铸能耗。2018年它们的指标分别为43.14kgce/t(+0.94kgce/t)、273.43kWh/t(+20.11kWh/t)、26.53kgce/t(+2.22kgce/t)、86.81kWh/t(+0.79kWh/t)和9.72kgce/t(+1.79kgce/t)。括号为2018年与2017年数据比较变化的数值。
2018年中钢协会员企业电炉工序能耗平均为55.70kgce/t,比上年升高0.37kgce/t。电耗占电炉工序总能耗的60%左右,节电是电炉工序节能工作的主要内容。2018年中钢协会员单位电炉使用热铁水比例由上年的524.53kg/t下降到497.14kg/t;吨钢综合电耗由2017年的342.06度/吨下降到2018年的334.51度/吨。主要原因是部分电炉进行吹氧、喷碳、造泡沫渣;使用热铁水比例下降27.39kg/t,使用钢铁料消耗下降76.57kg/t。
3.2电炉使用热铁水分析
因多种原因,我国大多数电炉企业建设了小高炉,使用热铁水炼钢,造成我国电炉工序能耗很低,与国际电炉全用废钢冶炼,是不能进行指标对比。各企业之间电炉工序使用热铁水的比例差距较大(2018年行业平均使用热铁水497.14kg/t,同比下降27.39kg/t)。热铁水用量±1%,影响电耗1.2kWh/t,能耗0.484kgce/t。从技术发展方向进行分析,电炉使用60%以上的热铁水进行冶炼,这样电炉生产是不科学的,由短流程变成长流程,能耗和污染物都会升高;与转炉相比成本也会升高。使用热铁水比例过高的企业,应当停下电炉,改为转炉生产(转炉是负能炼钢,有铁水预处理和炉外精炼后,几乎能生产所有钢种),这是技术发展方向。电炉企业之间使用吹氧、喷碳的数量也不一样,造成企业之间电炉工序能耗和生产技术经济指标有较大的不可比性。
3.3电炉冶炼时间分析
2018年中钢协会员单位电炉冶炼时间1.00h,同比升高0.01h,在热铁水比例下降27.39kg/t和使用钢铁料下降76.56kg/t条件下实现的,这是技术进步的体现。2018年有11个企业电炉冶炼时间下降,下降较多的企业是安钢、长治、新余等。
钢铁企业之间电炉生产条件差异较大,特别是使用热铁水比例和使用废钢量的不同,影响了电炉冶炼时间、氧气消耗指标;现在,一些电炉在吹氧、喷碳,能源利用多样化;电炉类型不同(普通电炉、超高功率电炉等),故对电炉指标对标,要进行具体分析。
3.4电炉综合电耗分析
2018年中钢协会员单位电炉综合电耗平均为334.51kWh,同比下降7.55kWh。有10个企业综合电耗下降,下降较多的企业有安钢股份、石钢、天管、长治等。
4 2018年中钢协会员单位连铸技术指标分析
目前,我国钢铁企业的连铸技术已达较高水平,一些特钢企业的连铸技术也在不断进步,主要技术指标如表3所示。连铸技术的进步,促进了我国钢铁企业的技术进步和节能减排;高效连铸技术的工业化应用取得很大成效;连铸生产的品种和质量均有较大提高;这些均说明我国连铸技术已接近国际先进水平。
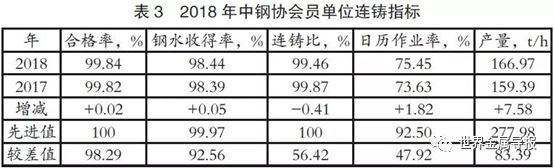
更多关于材料方面、材料腐蚀控制、材料科普等方面的国内外最新动态,我们网站会不断更新。希望大家一直关注国家材料腐蚀与防护科学数据中心http://www.ecorr.org