众所周知,涂料是一种材料,用于涂装物体表面而能形成涂膜,从而起到保护、装饰、标志及其他特殊作用。对于水性工业防腐漆来说,大家最关注的就是它的 防腐蚀性能,那么,优异的金属防腐蚀性能究竟与哪些因素有关呢,小编用下图来概括~
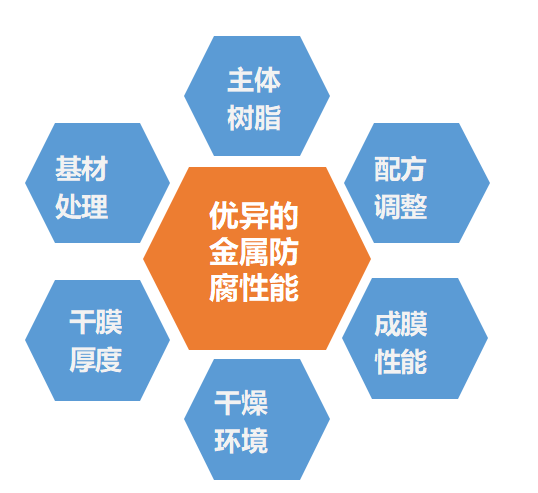
01 主体树脂
防腐蚀涂料的成膜物质在腐蚀介质中具有化学稳定性,其标准与成膜物质的组成和化学结构有关。主要是看它在干膜条件下是否易与腐蚀介质发生反应或在介质中分解成小分子。无论从防电化学腐蚀还是从单纯的隔离作用考虑,防腐蚀涂料的 屏蔽作用 都很重要,而漆膜的屏蔽性取决于其成膜物的 结构气孔 和 涂层针孔。
水、氧和离子对漆膜的透过速度是不同的。水的透过速度远远大于离子。氧的透过比较复杂,与温度关系很大。水和氧透过漆膜后可在金属表面形成腐蚀电池。离子透过漆膜较少,可不考虑它们对底材金属的直接作用,但会增加漆膜的导电率。
当成膜物结构中分子有较多的官能团时,漆膜的结构气孔少,并且在成膜过程中能彼此反应,形成 交联密度高的网状立体结构,从而增强涂料的防腐蚀性。漆膜的物理机械性能在很大程度上影响到防腐蚀涂料的防腐效果。它们与成膜物的分子量、链节、侧基因等有关。
上期我们已经对比讨论过不同种类树脂的应用~
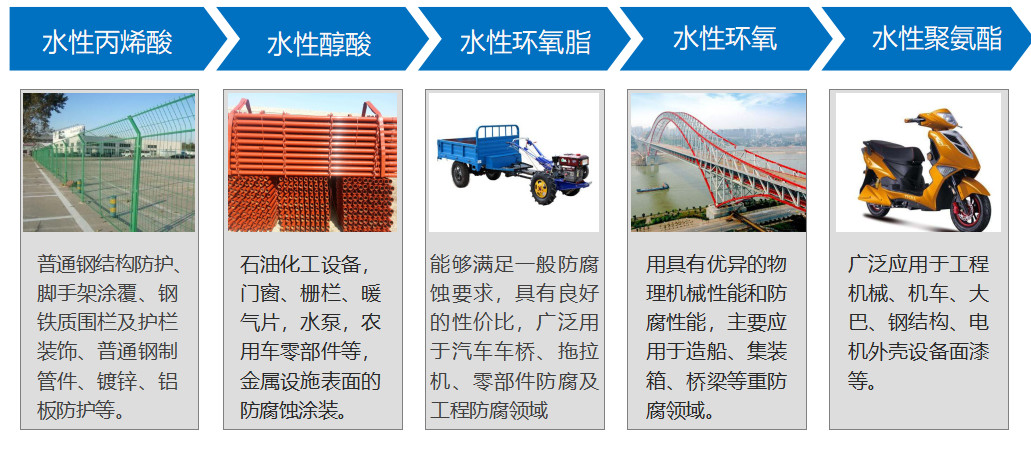
小编有话要说~贵的不一定是最合适的,一定要根据实际情况,综合考虑:应用场景,性能要求,成本要求等,选择合适的树脂体系以及涂层配套。
02 基材处理
如果表面处理不当或不彻底,即使最昂贵、技术最先进的涂料体系也将失败。在实际应用中,采取金属表面处理工艺,其最主要的目的有三个方面:
一是增强金属基材表面与涂层附着力,二是提高涂层防腐性能,三是提高基体表面的平整度。
一般金属表面处理方法有:
01除油:去除金属工件表面油污,增强与各种涂层附着力。包括溶剂清洗、碱液清洗、超声波除油和乳化除油4种。
02除锈:除去钢铁基材表面锈垢,可以有效延长涂膜使用寿命。包括手工打磨除锈、机械除锈、喷射除锈和化学除锈4种。
GB/T 8923.1-2011 是目测评定钢材锈蚀等级和表面处理等级的依据。
锈蚀等级钢材表面的四个锈蚀等级分别以A、B、C、和D表示,如下:
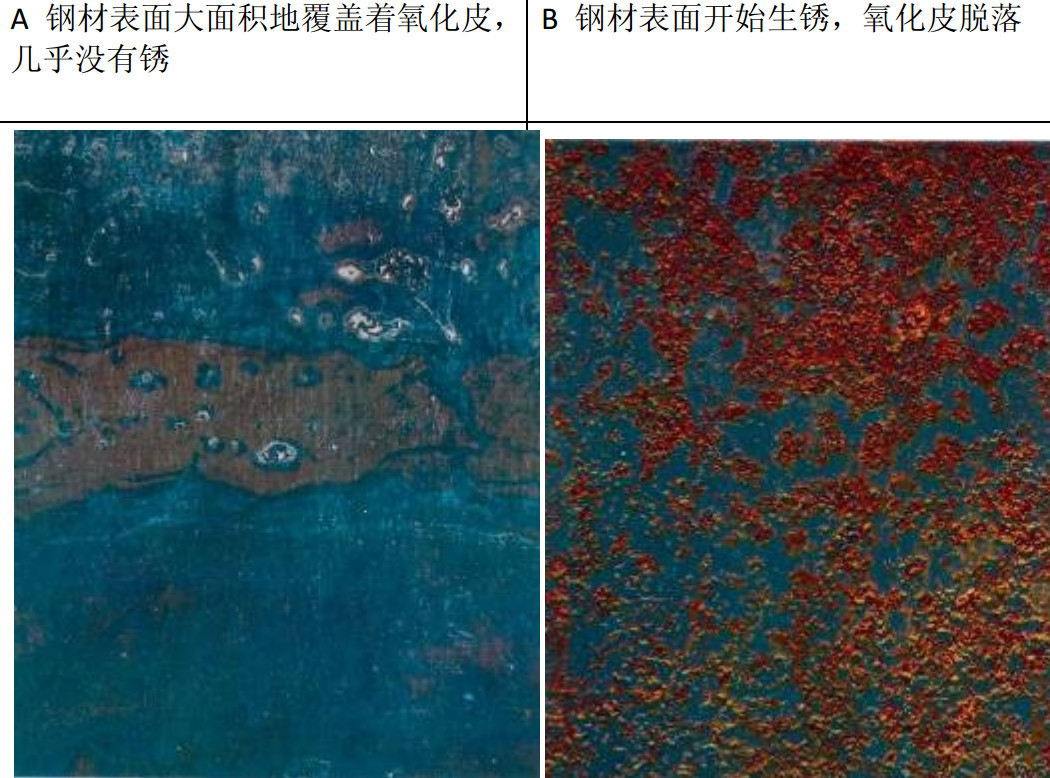
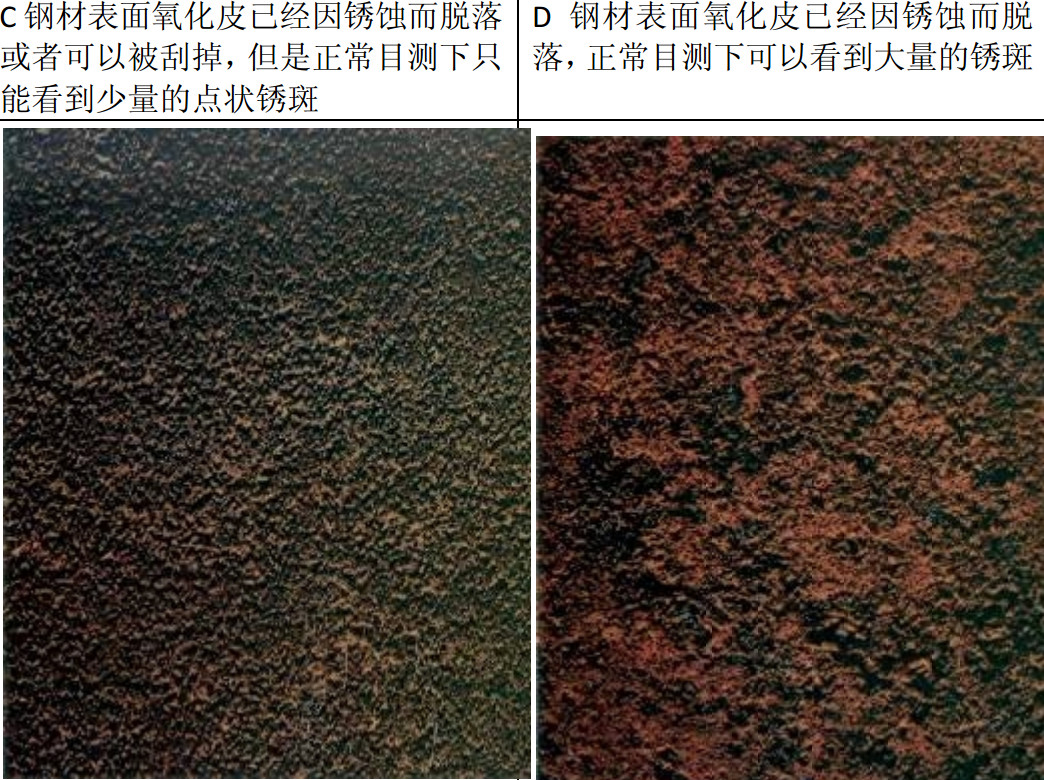
除锈等级
钢材表面除锈等级以代表所采用的除锈方法的字母“Sa”(磨料喷射)、“St”(工具打磨)或“F1”(火焰清理)表示。如果字母后面有阿拉伯数字,则其表示清除氧化皮、铁锈和油漆涂层等附着物的程度等级。
01喷射或抛射除锈
喷射或抛射除锈以字母“Sa”表示。喷射或抛射除锈前,厚的锈层应铲除。可见的油脂和污垢也应清除。喷射或抛射除锈后,钢材表面应清除浮灰和碎屑。对于喷射或抛射除锈过的钢材表面,分为四个除锈等级。
(1)Sal 轻度的喷射或抛射除锈钢材表面应无可见的油脂和污垢,并且没有附着不牢的氧化皮、铁锈和油漆涂层等附着物。
(2) Sa2 彻底的喷射或抛射除锈钢材表面会无可见的油脂和污垢,并且氧化皮、铁锈和油漆涂层等附着物已基本清除,其残留物应是牢固附着的。
(3) Sa2*0.5 非常彻底的喷射或抛射除锈钢材表面会无可见的油脂、污垢、氧化皮、铁锈和油漆涂层等附着物,任何残留的痕迹应仅是点状或条纹状的轻微色斑。
(4) Sa3 使钢材表观洁净的喷射或抛射除锈钢材表面应无可见的油脂、污垢、氧化皮铁锈和油漆涂层等附着物,表面应显示均匀的金属色泽。
02手工和动力工具除锈
用手工和动力工具,如用铲刀、手工或动力钢丝刷、动力砂纸盘或砂轮等工具除锈,以字母“St”表示。手工和动力工具除锈前,厚的锈层应铲除,可见的油脂和污垢也应清除。手工和动力工具除锈后,钢材表面应清除去浮灰和碎屑。对于手工和动力工具除锈过的钢材表面,本标准订有二个除锈等级,如下:
(1)St2 彻底的手工和动力工具除锈钢材表面应无可见的油脂和污垢,并且没有附着不牢的氧化皮、铁锈和油漆涂层等附着物。
(2)St3 非常彻底的手工和动力工具除锈钢材表面应无可见的油脂和污垢,并且没有附着不牢的氧化皮、铁锈和油漆涂层等附着物。除锈应比St2更为彻底,底材显露部分的表面应具有金属光泽。
03火焰除锈
火焰除锈以字母“FI”表示。 火焰除锈前,厚的锈层应铲除,火焰除锈应包括在火焰加热作业后以动力钢丝刷清加热后附着在钢材表面的产物。 FI 火焰除锈 钢材表面应无氧化皮、铁锈和油漆涂层等附着物,任何残留的痕迹应仅为表面变色(不同颜色的暗影)。
03磷化:磷化处理是用铁、锰、锌、镉的正磷酸盐溶液去处理金属工件,能在金属工件表面形成一层不溶性磷酸盐保护膜,该涂膜可提高金属工件的防腐性能和绝缘性能。
04铬化:铬化是最常见的一种化学转化钱处理方法,铬化膜提高了金属与涂层之间的附着力,改善了涂层的防腐性能。
小编有话要说~工作中,常会遇到客户不注重前期的表面处理,而出现各种各样的问题,再回过头来翻修,更加得不偿失。基材表面处理是防腐涂料施工前的第一道工序,也是基础工作,直接关系到整个涂装体系的防腐蚀性能和防护寿命。长期的实践证明,许多防护体系提前失效,其原因的70%以上是由表面处理不当引起的。
03 干膜厚度
防腐效果的好坏受到 涂装道数 与 漆膜厚度 的影响,尤以在严酷腐蚀环境下的重防蚀涂料,必须达一定的干膜厚度。而漆膜厚度又受到涂装道数的影响,涂装道数又与涂料固含量高低有直接的关系,如果固含量高的话则会减少涂装道数,反之增加涂装道数,为了保证在严重腐蚀环境下能够起到长久的保护功效,通常采用多道薄涂的施工工艺,即便是高固体含量的环氧漆也采用这种涂装方法,优点是各层之间相互遮盖缺损部位,其耐蚀性、机械性能要比单层漆膜更能保证整个涂料系统的防腐效果。
很多大型的防腐工程上采用的多道数涂装,现如今所有漆膜在涂装过程难免会缩孔、气泡现象,导致漆膜受损,如果不加注意的话这些现象将会埋藏在漆膜当中,大面积施工时无法得到完整无缺的漆膜,首先在缺损薄弱部位发生腐蚀。虽然厚浆涂料有节省工时、减少污染的优点,但是也会带来较大的内应力,致使涂层在使用过程中,由于外力或温度的变化极易发生开裂。除了涂装道数与固含量影响漆膜厚度之外,还受到施工技术的影响,为了确保一定的漆膜厚度,要求施工人员必须掌握一定的涂装技巧,随时使用漆膜测厚仪测量漆膜厚。
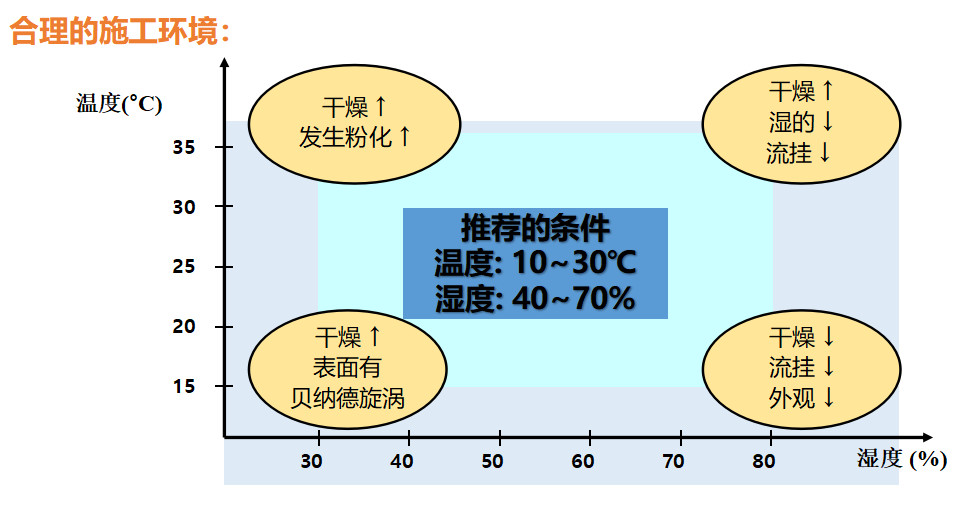
小编有话要说~虽然说,防腐蚀涂层的厚度与防腐蚀效果有直接的关系,但千万不能为追求效率,一遍涂装。特别是氧化干燥型(醇酸、环氧酯等),因为太厚则 表层吸氧皱皮 而内层不干。若涂料含溶剂,太厚会使溶剂不能充分挥发,少量溶胶残留在涂层中 而降低耐蚀性。因此,在保证优异成膜的前提下谈干膜厚度,才有意义。
04 干燥环境
涂料施工需要有适宜的环境与条件,如温度、湿度、光线、通风、卫生等才能做出好的效果。
01 温度、湿度与溶剂型涂料不同,水性漆不仅要考虑到温度,还要考虑到湿度。温度低于5℃或超过35℃,湿度超过来85%时不适于施工。
施工最好在常温(15-30℃)条件下进行,温度过低,涂料成膜变慢,易导致漆膜硬度不良发生后期返白现象,温度过高(超过35℃),固化快易出现桔皮、暗泡、针孔等现象,性能将受不利影响。潮湿空气,对大多数涂料都不利,会造成发白或干燥缓慢等弊病,最终导致成膜不良,影响涂膜性能。
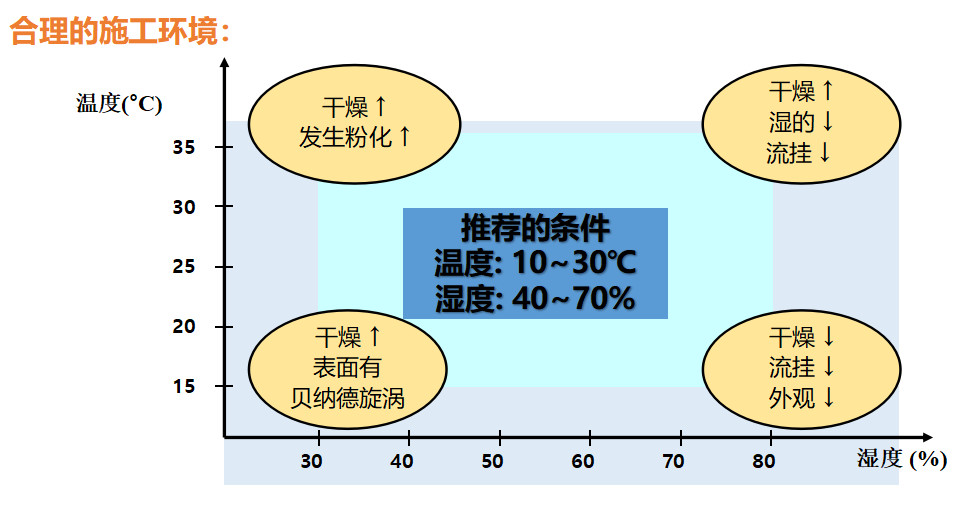
02 光线如果是在室内施工,充足的光线有助于看清漆面,辨别施工涂膜是否均匀,及时避免漏喷或流挂,因此应选在光线充裕的房间进行施工。
03 通风施工场地应有通风设备,以保持适量的新鲜空气流通。这样既有利于施工者的健康,利于涂料成膜,又可减少火灾隐患。但空气流通的速度不可过快,以免影响涂层质量。
04 灰尘要防止灰尘对涂料成膜时的影响,灰尘会影响漆膜的光泽和美观。施工环境必须保持干净,在施工过程中产生的粉尘与磨屑应立即清除干净,否则会影响到面漆漆膜的最终效果。
小编有话要说~在实际涂装过程中由于施工方法不当而达不到预期防蚀效果的例子很多。特别是许多性能优异的防腐蚀涂料对施工方法极为敏感,只有严格按照其各自的施工条件进行施工才可形成正常的涂层,达到预期的防蚀保护作用。
05 成膜性能及配方调整
成膜的好坏直接影响着涂膜的性能,其中,成膜助剂的选择也非常重要。除此之外,配方中,其他助剂如:分散剂 、基材润湿剂、消泡剂、防闪锈助剂、流变助剂等,以及防锈颜料的选择,颜积比的设定等,都会最终在不同程度上影响涂膜的防腐性能~
更多关于材料方面、材料腐蚀控制、材料科普等方面的国内外最新动态,我们网站会不断更新。希望大家一直关注国家材料腐蚀与防护科学数据中心http://www.ecorr.org