在铁路车辆领域,由于货车车体及油罐车极易发生腐蚀现象,因此需要及时有效地对车体腐蚀情况进行检测以保证铁路车辆的运行安全 [1] 。当前国内学者对车体腐蚀损伤特性开展了一系列的研究,如刘建平 [2] 对敞车车体腐蚀情况及其防腐措施开展了研究;林兴录 [3] 对煤矿铁路货车车体腐蚀及防腐措施进行了详细探讨;赵洪伦 [4] 对货车车体结构腐蚀损伤与疲劳寿命进行了相关研究;谢芬 [5] 对铁路罐车的腐蚀防护工艺方法进行了探讨。然而,对于已经出现的腐蚀情况,如车体和罐车的腐蚀缺陷,相应的检测或监测研究十分有限。
目前,对于腐蚀的检测或监测,通常使用超声波测厚技术对腐蚀区域的壁厚进行多点检测,通过测厚值评估腐蚀区域的壁厚减薄情况实现腐蚀特性的评价。然而超声测厚法并不能获得腐蚀区域的检测图像,因此无法直观有效评估腐蚀区域的缺陷分布;另外,当腐蚀缺陷出现于超声探头无法直接扫描检测的位置时,该方法则无法使用。因此为了实现铁路车辆车体或罐车腐蚀缺陷的全方位、快速和有效检测,发展新的无损检测技术至关重要。
近年来超声相控阵检测技术得到了极大的发展,在腐蚀检测方面也已得到一定的应用,如相控阵检测技术已成功应用在钻杆内壁腐蚀检测 [6] 、法兰密封面腐蚀缺陷检测 [7] 、压力管道加厚弯头凹坑腐蚀减薄检测 [8] 等方面。然而,当前研究并未对成像原理及缺陷定量做出研究,且对位于探头无法直接扫描区域的腐蚀缺陷检测并未开展研究。为了充分理解相控阵检测技术对腐蚀缺陷的检测原理,并实现该技术在腐蚀缺陷检测中的应用,本文利用通过具有腐蚀坑缺陷的板材,分别采用相控阵 C 扫描检测以及相控阵导波 B 成像检测进行理论和实验研究,以实现所有缺陷的有效检测。
1 相控阵检测方法
1.1 相控阵纵波 C 扫描成像方法
相控阵超声的基本概念来源于相控阵雷达技术,相控阵超声探头由多个晶片按一定的规律排列,通过软件可以单独控制每个晶片的激发时间,从而控制发射超声波束的形状和方向,实现超声波束的扫描、偏转和聚焦 [9] 。相控阵超声的发射和接收原理见第 83 页图 1。发射时,数据采集单元触发相控阵列单元,相控阵列单元按照设置的延时法则依次触发激励方波脉冲激励探头,使探头中的每个晶片发出的超声波在预定位置实现聚焦;接收时,由缺陷反射回来的超声波到达每个接收晶片,相控阵列单元根据每个接收晶片的回波信号按照设置的延时法则合成为一个信号送数据采集单元。因此,相控阵每发射并接收一次信号将会获得一个由多晶片采集并进行合成的 A 扫描信号。
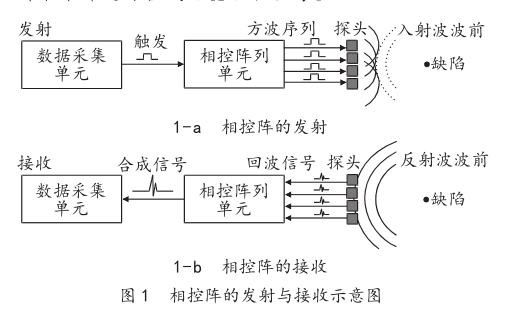
相控阵超声具有独特的电子扫描和聚焦特点,可在不移动探头的情况下实现工件断面的扫描检测。当前相控阵超声常用扫描方式包括线形扫描(L-Scan)和扇形扫描 (S-Scan)。
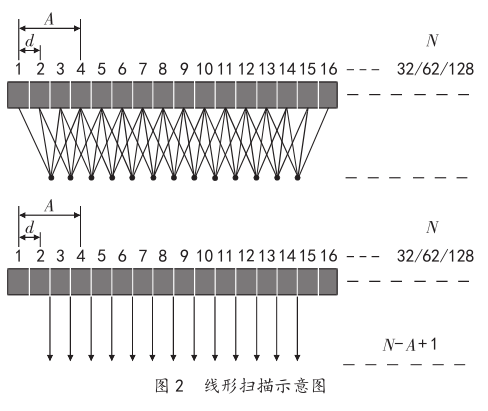
扫描过程中,将具有相同聚集法则的超声波施加在相控阵探头的不同晶片组,被激活晶片组将产生特定角度的超声波束,通过改变被激活晶片组的位置,使该超声波束沿晶片阵列方向前后移动,以实现类似常规手动超声波检测探头前后移动的检测效果。
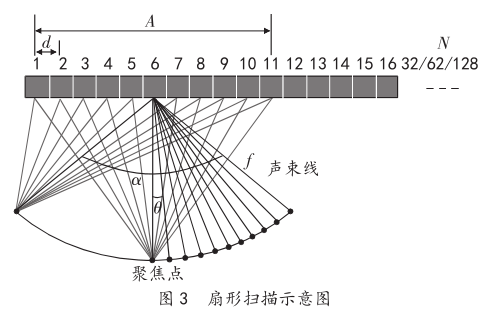
图中:d 为阵元间距;A 为激励孔径 (激发晶片组);N 为探头阵元数目;f 为焦距;α 为扇扫角度范围;θ 为角度步进。扇形扫描又称变角度扫描,用具有特定聚集法则的超声波激发相控阵探头中的部分或全部晶片,使被激发晶片组形成的超声波束在设定的角度范围内以一定的步进值变换角度扫过扇形区域。
超声 C 扫描成像可实现对扫描区域缺陷的可视化。常规的单晶探头扫描成像通常采用锯齿形的扫查方式;采用相控阵电子扫描不需要移动探头就可以实现工件一定宽度的断面扫查,因此,只需单轴直线扫查便可获得工件的 C 扫描图像。常规扫查方式与相控阵扫查方式的对比见图 4,由于相控阵扫查方式仅需在一个方向移动即可实现 C 扫描成像,因此其效率明显提高。
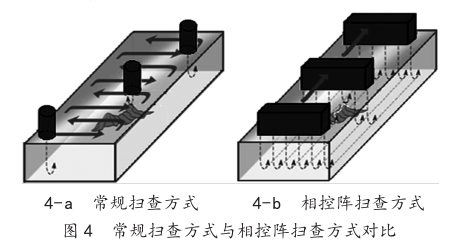
1.2 相控阵导波 B 扫描成像方法
超声相控阵纵波 C 扫描成像技术可简单直观地反应腐蚀缺陷的特性,但遇到相控阵探头无法直接扫描的区域时,如铁道车辆车体或罐车等的缺陷,超声纵波 C 扫描检测技术将无法有效检测缺陷。因此为了实现板材腐蚀缺陷的全面有效检测,有必要发展新的相控阵扫描检测技术。超声导波可在板材内部传播,该检测方法无需探头位于缺陷上方,因此可配合超声纵波 C 扫描检测方式实现被检测工件的全方位扫描。
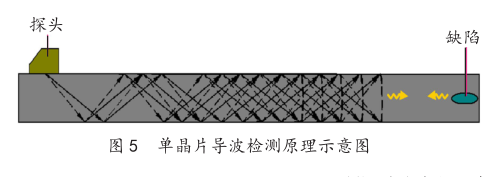
图 5 为单晶片导波检测原理示意图。单晶片超声导波探头发出的超声波可在工件中激励出沿工件传播的导波,当该导波遇到缺陷时,会产生反射,反射回波被探头接收,然后通过分析回波的信号特征和传播时间即可实现缺陷大小和位置的判别。通过直线移动探头,则可形成扫描区域导波 B 的扫描图像。当采用相控阵导波探头时,根据相控阵电子扫描原理,相控阵超声检测仪每发射接收一次就可形成一条合成超声波束,因此通过电子扫描获得的所有导波声束就可构成导波 B 扫描图像。导波 B 扫描图像是指超声导波数据的二维显示,由扫查过程中采集的 A 扫描信号连续拼接而成,一个轴代表探头的移动距离,另一个轴代表水平方向的有效检测长度。采用相控阵线形扫描方式形成的相控阵导波B 扫描图像,图 6 为其构成原理示意图。
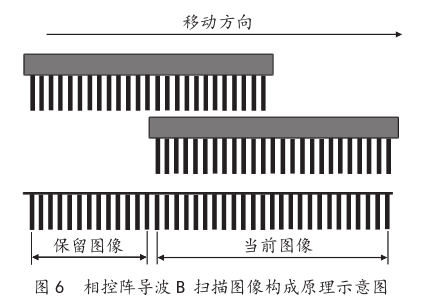
图 6 中,保留图像是指探头移动之后屏幕应绘制的图像,当前图像是指相控阵探头实时的电子扫描图像。设编码器移动的扫查步进为 s,超声波束间距为 d。设当前实时导波扫描图像的刷新重复频率为 F,在 1/F 时间内,探头移动距离小于等于导波探头超声波束覆盖的宽度,若编码器移动的距离为 M 倍扫查步进,探头移动的电子扫描超声波束数为 N,则有 M*s=N*d。当 s=d 时,则保留图像为M 条电子扫描超声波束。当 s≠d 时,需将 N*d 宽度内的超声波束总数插值或压缩为 M 条:当 s<d时,需要进行超声波束插值;当 s>d 时,需要进行超声波束压缩,然后再进行图像绘制。例如:M=20,s=0.5 mm,N=10,d=1.0 mm,因此需要将电子扫描的 10 条超声波束插值为 20 条超声波束。
在实际应用时,一般要求 s 与 d 的关系是整数倍的关系,这样实现插值和压缩较为方便。进行相控阵B 扫描成像检测时,为了提高扫查速度,可增大相控阵导波探头的阵元数目来获得更大的有效覆盖宽度。
2 腐蚀检测实验及分析
2.1 实验设计
本文试验检测对象为具有腐蚀坑缺陷的板材试块 (见图 7),试块规格为 300 mm×120 mm×4 mm,腐蚀坑缺陷采用数字编号进行编排,其中数字 1,2,3,…,7 的位置为单个腐蚀坑缺陷,数字 8 的位置为连续腐蚀坑缺陷,数字 9 的位置为密集腐蚀坑缺陷。板材另一侧为未出现腐蚀的光滑平面,试验时以板材试块未腐蚀的一侧作为检测面进行。
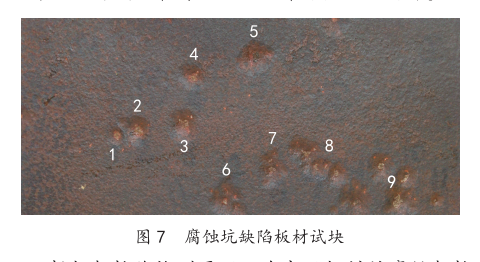
根据相控阵检测原理,为实现板材的腐蚀相控阵 C 扫描检测,采用相控阵轮式探头扫查器进行检测。轮式探头采用频率为 7.5 MHz,阵元数为 64个,阵元晶片尺寸为 10 mm×1 mm 的相控阵探头,阵元间距为 0.8 mm,轮式探头扫查器见图 8。
腐蚀检测相控阵导波探头扫查器见图 9。为实现板材腐蚀的导波扫描检测,相控阵导波探头扫查器的导波探头位于扫查器腹部,探头规格为2.5L64-1.0×10,探头频率为 2.5 MHz,阵元数为 64个,阵元晶片的尺寸为 10 mm×1 mm,阵元间距为1.0 mm。
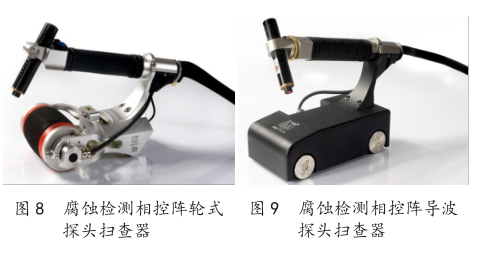
2.2 超声测厚实验
为了准确地了解腐蚀坑的腐蚀减薄情况,采用单点测量法利用 CTS-400+型超声波测厚仪对编号1~7 位置的腐蚀坑缺陷进行腐蚀减薄测厚,即对腐蚀坑缺陷的某一点用探头进行两次测厚, 两次测量探头的分割面夹角为 90°,取较小值为被测工件厚度值。
对位置 8 采用连续测量法,即用单点测量法沿指定路线连续测量,间隔为 5 mm,取最小值作为被测工件厚度。对位置 9 采用 30 mm 区域多点测量法,即以一个测定点为中心,在直径约为 30 mm 的圆内进行多次测量,取最小值为被测工件厚度值。
超声测厚法的测量结果见第 85 页表 1。从表 1 可以看出腐蚀坑的减薄情况,但该检测结果并不能直观地反应缺陷的位置以及大小。
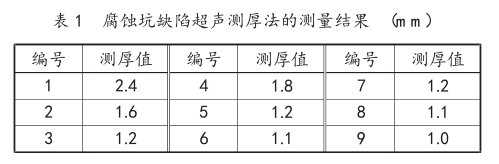
2.3 相控阵纵波 C 扫描实验
为了确定腐蚀坑的腐蚀面积和缺陷分布情况,通过 CTS-2018PA 相控阵超声检测仪和轮式探头扫查器对腐蚀坑缺陷进行相控阵 C 扫描成像检测。采用线形扫查方式,扫描聚集法则参数如下:激励孔径为 8 mm,焦距为 5 mm,检测范围为 10 mm,C扫描成像方式为跟踪闸门 G 监控界面波变化,成像闸门 A 监控底波变化,当界面波发生偏移时,成像闸门 A 根据跟踪闸门 G 的反馈信息进行随时调整。
针对 1 号、2 号、3 号腐蚀坑进行相控阵 C 扫描检测实验,实验结果选取 2 号、3 号腐蚀坑的 A+L+C (A 波信号,线型扫描成像和 C 扫描成像)同步显示图 (见图 10)。从图 10 看到,在 A 波数据中难以得到有效的检测信息。在 L 扫描图中,2 号和 3 号腐蚀坑的底波完全消失,腐蚀坑表面回波与界面波重叠在一起,可见,试图通过 L 扫图像来测量腐蚀坑的深度难度较大。但 C 扫图中可以清晰地显示腐蚀区域的位置和形状,测量腐蚀坑的面积则较为容易。
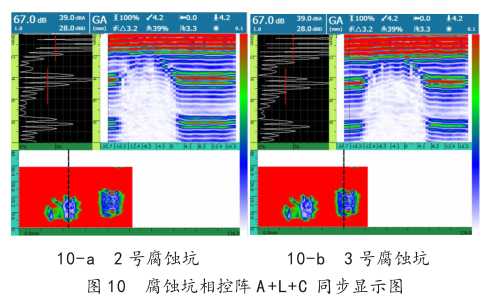
由于 C 扫描图像可以有效实现腐蚀的检测,因此对所选试块进行整体 C 扫描成像。由于板材试块较宽,使用轮式探头扫查器无法一次性全覆盖,故该试验采用多次扫查并将 C 扫图像进行合成,合成后的 C 扫描图像见图 11。从图 11 可以看出,1 号和 2 号腐蚀坑由于间距比较小,两个腐蚀坑的图像基本挨在一起;3 号至 7 号腐蚀坑由于间距比较大,显示均为独立的腐蚀坑图像;8 号连续腐蚀坑缺陷相互之间间隙较小,形成的 C 扫图像为带状图像;9 号密集腐蚀坑图像显示为 3 个大腐蚀坑图像挨在一起。图 11 的 C 扫描合成图像可以清晰反映板材腐蚀分布情况,与实际情况的一致性符合。
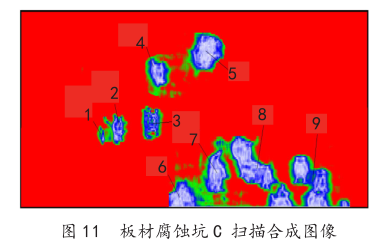
2.4 相控阵导波 B 扫描成像实验
由于相控阵超声 C 扫描检测中,可能存在探头无法达到缺陷上方的情况,无法实现完整 C 扫描成像。因此通过 CTS-2108PA 相控阵超声检测仪和导波探头扫查器,对腐蚀坑缺陷进行相控阵导波 B 扫描成像检测。检测时线形扫描聚集法则参数如下:
激励孔径为 24 mm,焦距为 300 mm,检测范围为300 mm。本文针对板材试块的 6 号、7 号、8 号腐蚀坑进行相控阵导波线形扫描。
相控阵导波线形 B 扫描图像见图 12,图像中相控阵线形扫描图像的超声波束总数为 34 条,每条超声波束的间距为 1.0 mm。从图 12-a 中测得 6号腐蚀坑与探头入射点距离为 70.4 mm,从图 12-b测得 7 号腐蚀坑与探头入射点距离为 100.5 mm,从图 12-c 中测得 8 号腐蚀坑与探头入射点距离为124.6 mm。由图 12-a 中的超声波束 [6 号] 与图12-b 的超声波束 [18 号] 可以确定 6 号腐蚀坑与 7号腐蚀坑之间的水平距离为 12 mm,同理 7 号腐蚀坑与 8 号腐蚀坑之间的水平距离为 12 mm,定位距离与实际情况符合。
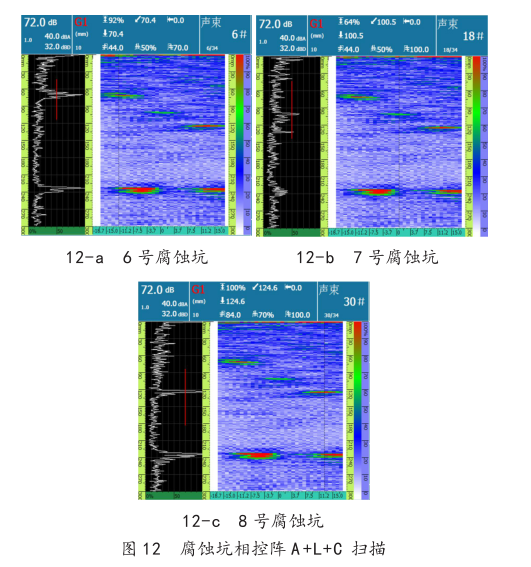
3 结论
本文主要通过相控阵纵波 C 和相控阵导波 B 对具有腐蚀坑缺陷的薄板试块进行扫描检测,从试验检测结果得出如下结论。
1)相控阵 A+L+C 同步显示图可有效描述腐蚀坑缺陷的分布情况以及测量腐蚀坑的面积,通过监控底波消失形成的腐蚀坑面积与实际腐蚀坑的面积相吻合。
2)相控阵导波线形及扇形 B 扫描图像均可有效检测腐蚀坑,较好表征腐蚀坑的位置和了解腐蚀坑的分布情况,但前面腐蚀坑的存在会影响到后面腐蚀的回波,因此当多个腐蚀坑在同一检测声超声波方向时,可以发现处于前面的腐蚀坑,而后面的腐蚀坑容易漏检。
3)当探头可布置在检测对象的腐蚀缺陷上方时,利用相控阵 C 扫描检测,可以快速测量腐蚀缺陷信息和了解腐蚀缺陷分布。当检测对象无法在腐蚀缺陷上方放置探头时,利用相控阵导波 B 扫描检测是一个比较好的检测方式,相控阵导波可以检测距离探头一定水平距离的特定区域。
4)相控阵检测的多晶片探头可以一次性覆盖较宽的检测区域,通过导波 B 扫描和纵波 C 扫描检测成像技术能够实现板材所有区域腐蚀缺陷的检测。因此利用相控阵检测方法对板材腐蚀缺陷进行检测评估具有较大优势,是一种值得推广的检测技术,可以借鉴推广到货车车体及油罐车内壁腐蚀的检测研究。
更多关于材料方面、材料腐蚀控制、材料科普等方面的国内外最新动态,我们网站会不断更新。希望大家一直关注国家材料腐蚀与防护科学数据中心http://www.ecorr.org