发电厂水冷壁管突然爆裂,幕后黑手竟然是管道腐蚀......
2018-09-20 11:58:41
作者:任凯 来源:理化检验—物理分册
事故背景
某垃圾发电厂锅炉于2015年7月29日投入运行,2016年7月23日该锅炉第一烟道水冷壁管发生爆管事故。
爆裂水冷壁管材料为20G钢,规格为?64mm×6mm,工作温度为460℃,炉内压力为6.4MPa,管内冷却水压力约为7MPa。
锅炉运行记录显示,该部位自投运首次发生爆裂事故,水冷壁管爆裂失效前锅炉运行正常。本次因水冷壁管发生爆裂失效导致机组停机,为查找失效原因,笔者对爆裂失效的水冷壁管进行了检验和分析,以期杜绝此类事故的再次发生。
理化检验
1宏观分析
对爆裂失效的管道进行宏观观察,可见管道的向火侧外壁发生严重的腐蚀,爆裂位置的形貌如图1a)所示。爆裂位置位于炉膛内靠近弯管约20cm处。爆裂处管体壁厚明显减薄,最薄处约为0.61mm,如图1b)所示;外壁腐蚀严重有腐蚀产物形成,附近有一条长约9mm的裂口,如图1c)所示。在远离爆裂位置的背火侧,管道表面有明显的腐蚀产物形成,内、外壁均未见明显裂纹。

图1 爆裂失效水冷壁管的宏观形貌
2化学成分分析
分别对新管、爆管附近和远离爆管处取样进行化学成分分析,结果见表1,可见其化学成分均符合GB 5310-2008《高压锅炉用无缝钢管》对20G钢成分的要求。
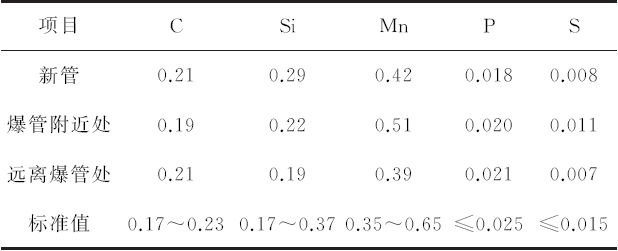
表1 水冷壁管的化学成分(质量分数)
3金相检验
在向火侧爆裂位置附近沿轴向切取金相试样进行观察,如图2所示。可见其显微组织为铁素体+珠光体,未见明显晶界熔化及魏氏体组织,晶粒度为7.5~8.0级,如图2a)所示。管体内壁发现约79μm厚的脱碳层,如图2b)所示;外壁腐蚀坑深度约213μm,如图2c)所示;内壁腐蚀坑深度约105μm,如图2d)所示。未发现珠光体球化及高温蠕变特征,从而排除管道超温运行的情况。对其进行非金属夹杂物含量评定,结果为:球状氧化物夹杂D类1.5级,DS类0.5级。
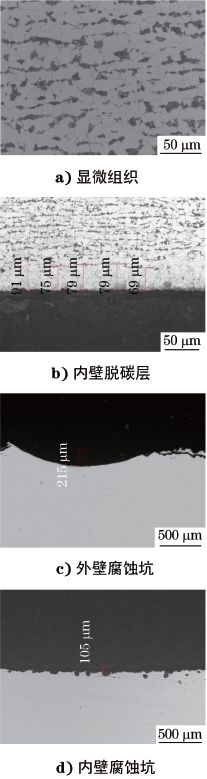
图2 爆裂位置水冷壁管显微形貌
在远离爆裂位置的背火侧取样,观察其显微组织和脱碳层形貌,如图3所示。可见背火侧(内壁)脱碳层厚度约为40μm,其显微组织和晶粒度均符合GB 5310-2008的要求。
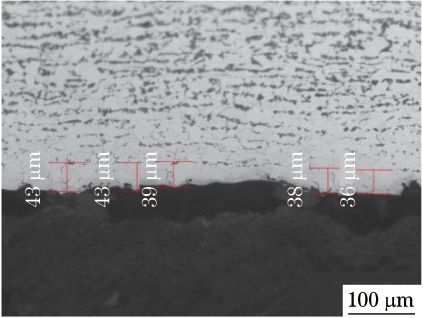
图3 远离爆裂位置背火侧水冷壁管显微组织形貌
4力学性能测试
在靠近爆裂位置的向火侧取纵向试样进行力学性能测试,并与新管的力学性能测试结果进行对比,结果见表2,可见其均符合GB 5310-2008的要求。
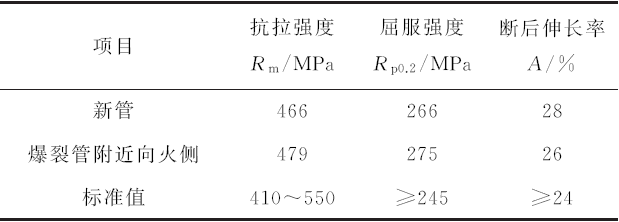
表2 水冷壁管的力学性能测试结果
分析与讨论
通过以上理化检验可知,造成水冷壁管爆裂的原因是外壁在高温烟气的冲刷及腐蚀下,金属与烟气中的硫以及管壁上沉积的硫酸盐及氯化物等发生反应产生腐蚀,烟气中的有害物质不断接触管体,对管壁持续冲刷导致管壁减薄直至强度不足,使得管道在使用过程中爆裂。内压破裂强度计算公式如下:

通过计算,新管64mm×6mm的标准最低屈服强度的抗内压强度为5825.67b·in-2(40.17MPa)。而实际测量残余管体最薄处的厚度为0.61mm(0.024in),此时的抗内压强度为592.44b·in-2(4.08MPa)。
燃烧室的工作温度为460℃,管道外壁的接触温度为实际工作温度,管体的屈服强度会随着温度的升高而显着降低。因此,当设备启动瞬间或者有运行波动时,若管体内外压差大于4.08MPa,都将会在腐蚀最严重区域发生管体破裂,造成爆管事故。
结论及建议
高温烟气和烟气中所含的有害物质造成水冷壁管外壁的腐蚀减薄,导致水冷壁管抗内压强度严重降低而发生破裂。
建议在日常的运行过程中加强对水冷壁管的监测,在停机维护期间使用超声波测厚仪对管体进行检测,管体的减薄部位要及时更换,避免爆管事故的再次发生。
更多关于材料方面、材料腐蚀控制、材料科普等方面的国内外最新动态,我们网站会不断更新。希望大家一直关注国家材料腐蚀与防护科学数据中心http://www.ecorr.org
免责声明:本网站所转载的文字、图片与视频资料版权归原创作者所有,如果涉及侵权,请第一时间联系本网删除。