随着现代工业的高速发展,金属材料也得到了广泛应用。例如铝及铝合金因其重量轻、耐腐蚀性好两大突出特点,使其成为当前最经济适用的材料之一,用途十分广泛,大大推动了航空、建筑、汽车三大重要工业的发展。与此同时,金属材料的腐蚀问题也日益凸显,腐蚀造成的破坏后果不言而喻。一方面腐蚀会造成材料的质量损失,如使机器设备的尺寸发生变化或设备破坏等;另一方面,腐蚀也会使金属材料的性质发生变化,如造成强度下降及外观变化等。如何对金属材料进行有效防护,成为了人们长期以来致力于解决的重大问题。涂料固化后作为一种固态薄膜,通过将被涂物体与周围环境隔离开,从而达到防护目的,并对被涂物进行装饰,在各个工业或建筑行业得到了广泛的应用。如建筑铝型材的粉末喷涂,汽车行业轮毂及其他零部件的有机涂层的涂装等都有了高速长足的发展。随之而来的在沿海潮湿地区或工业污染的大气环境中,有机涂膜下的丝状腐蚀也引起了广泛关注。
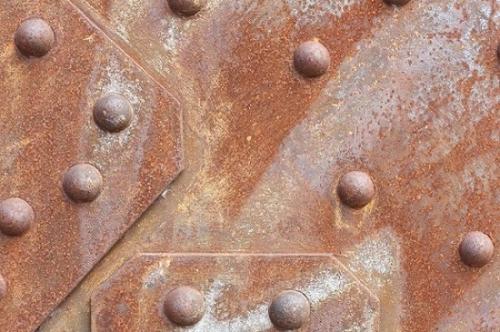
1 丝状腐蚀的产生及特点
丝状腐蚀是发生在色漆、清漆或其他涂膜下的一种外观为头发细丝状的腐蚀现象,腐蚀主要发生在有机涂层下的金属钢、铝或镁上。由于丝状腐蚀多数情况下主要发生在涂膜下,且在金属表面呈线性不断向前延伸生长,一般向基体金属纵向生长的深度很浅,腐蚀深度约在2-10?m之间,因此丝状腐蚀通常也被称为膜下腐蚀。
丝状腐蚀在涂装的设备、设施或机器零部件上可被观察到,如在兵器工业中的药筒涂膜下、沿海地区或海上服役的航空器涂膜下、建筑用的铝型材涂膜下以及汽车铝轮毂涂膜下等较容易发现。
丝状腐蚀作为一种典型的阳极破坏的电化学腐蚀现象,腐蚀一般从涂膜的切割边缘或局部损伤处等缺陷部位开始。腐蚀的发生可分为两个阶段:(1)丝状腐蚀的引发或活化阶段;(2)丝状腐蚀的生长和发展阶段。在引发或活化阶段,涂层有缺陷的薄弱部位所产生的涂层与金属基体之间的剥离界面,有足够的间隙能使环境中的氧气、水分和电解质凝聚,形成腐蚀所需要的电解液滴,当凝聚的电解液的量足以维持电化学反应时,腐蚀反应即开始发生,电解液中溶解的氧气因参与去极化作用而不断消耗。由于涂层的微观缺陷、基体金属表面的不均匀性而导致的涂层与金属界面的不均匀性、以及涂层与金属基体之间产生的剥离界面的前区与后端的氧气含量差异等综合因素的协同作用,使得电化学反应的阴极区和阳极区得以形成,从而形成氧浓差电池。氧的浓度决定着丝状腐蚀的走向,丝状腐蚀的前端活性头是向缺氧区或低氧区发展的。因此,丝状腐蚀的生长环境需要同时满足电解质、水分和氧气能源源不断的供应,尤其在空气相对湿度范围为60%-95%、涂膜表面或环境中有吸湿性盐类作为电解质时,丝状腐蚀极易发生。随着腐蚀不断地向前延伸生长,腐蚀产物累积,涂膜拱起,形成一条犹如头发丝状的腐蚀痕迹,腐蚀丝的宽度主要取决于引发或活化阶段初期电解液滴的大小,在延伸生长过程中宽度变化不大,主要是长度的增加,一般大约以0.15-0.4mm/d的速度由引发点向前延伸发展,踪迹宽度一般为0.1-0.5mm。
本文选取了一个在实际使用中发生丝状腐蚀的铝轮毂样品,对其丝状腐蚀现象进行了微观分析。图1为丝状腐蚀发生区域的光学显微镜图片,由于该有机涂膜为透明粉末涂料,从图片上可以清晰的看出在涂膜下呈丝线状的腐蚀踪迹。然后对腐蚀区域进行切割,得到腐蚀处有机涂膜和铝基材的截面,并进一步用扫描电子显微镜(SEM)对截面进行了微区分析,从SEM图片(见图2)上可以看出,有机涂层和基材发生了剥离。用手术刀片将表面的涂层小心地刮掉,并用能谱仪(EDX)分析腐蚀处基材表面的元素,检测到了氯和钠元素(见图3)。
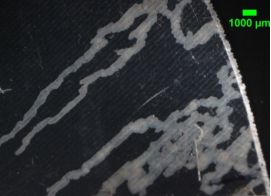
图1丝状腐蚀区域样品涂膜表面的光学显微镜图像
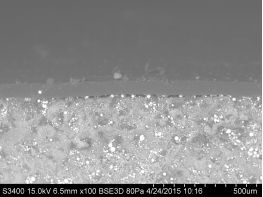
图2丝状腐蚀发生区域的截面图(SEM图像)
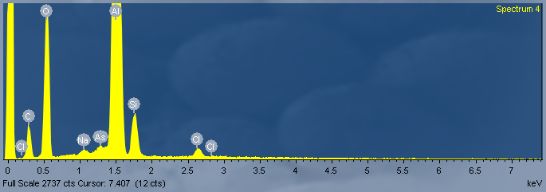
图3有机涂膜下基材腐蚀处的元素分析(EDX谱图)
2 丝状腐蚀产生的影响因素
2.1 温度
根据丝状腐蚀的产生机理可确定温度和相对湿度是影响丝状腐蚀的主要因素。温度升高,分子运动加剧,腐蚀速度越快。由阿伦尼乌斯定律可知,温度每升高10℃,反应速度可提高2~3倍。同时温度升高电解质溶液的导电率也相应增加,从而加剧电化学腐蚀反应的速度。
2.2 相对湿度
丝状腐蚀一般在环境相对湿度为60%~95%时容易发生。但当涂膜表面有吸湿性盐类如氯化物盐类时,即使环境相对湿度较低,丝状腐蚀也会发生。然而当环境相对湿度高于95%时,丝状腐蚀会缓慢生长直至停止发生,因为当环境相对湿度高至95%时,空气中的氧气含量会相应下降,从而大幅降低腐蚀反应的速度。
2.3 氧含量
有研究表明氧含量是影响丝状腐蚀的主要影响因素,相关研究表明,当环境中的氧体积分数为35%时就能较快的加速丝状腐蚀;当环境中的氧体积分数升高至50%左右时能最有效的促进丝状腐蚀。
2.4 其他因素
温度、相对湿度和氧含量是影响丝状腐蚀的最主要因素。此外,涂膜基底金属的表面前处理方法、涂层体系以及大气环境中的污染介质都对丝状腐蚀具有明显的影响。如采用磷酸锌盐的磷化前处理方法比采用磷酸铁盐磷化的抗丝状腐蚀性能好,Ti-Zr系钝化前处理方法的抗丝状腐蚀性能弱于铬化前处理。
3 表面涂膜的丝状腐蚀试验方法
通过实验室加速试验方法模拟自然环境下的丝状腐蚀现象,不仅重复性、再现性较好,还可在较短时间内对漆膜耐丝状腐蚀性能进行评估,从而对不同产品的耐丝状腐蚀性能进行比较,并通过改变工艺改善其性能。
3.1 测试标准及测试方法简述
丝状腐蚀常用的测试标准有GB/T 13452.4,GB/T 26323,ISO 4623-1, ISO 4623-2,美国汽车工程师学会标准SAE J2635及一些企业标准。其中GB/T 13452.4(ISO 4623-1)是针对钢铁基材丝状腐蚀的测试标准,主要是通过将试样浸泡在0.1% wt的 NaCl溶液中30~60s或放入盐雾中暴露一定时间后,用纸巾或棉布抹去表面溶液,留下划痕处溶液,随后放入(40±2)℃ & (80±5)%RH的试验箱中进行丝状腐蚀试验;而GB/T 26323(ISO 4623-2)是针对铝基材丝状腐蚀的测试标准,主要是通过将试样暴露在饱和盐酸蒸汽中引入少量盐酸至划痕处,然后置于(23±2)℃,(50±5)%RH恒温恒湿条件下放置15~30min后,将试样放于(40±2)℃,(82±5)%RH的试验箱中进行丝状腐蚀试验。
本文以下内容主要介绍SAE J 2635标准关于轮毂表面上涂膜丝状腐蚀的测试方法试验过程。
3.2 试验过程
(1)试样划痕
样品表面用划痕工具划一条垂直的“丨”线,长度建议100mm,至少40mm,距离边缘至少15mm,划痕方向应与样件在箱体中的放置方向保持一致,划痕完后可用万用表查看是否有持续电流来检验样件是否划至金属底材,若未完全到底材,则需在距离任一条划痕或边缘至少15mm处重新划痕。
(2)盐雾引发
将划痕后的样件置于ASTM B 368标准条件下的CASS试验箱中6h,样件表面及划痕以45°角放在非金属样品架上。该过程主要是利用盐雾腐蚀环境使样品接触腐蚀氛围,在划痕处形成“生长引发点”。
(3)去离子水清洗
盐雾引发后准备一个至少5加仑的容器,里面装满流动的去离子水(ASTM D 1193,type 4),将样件垂直浸入流动的去离子水中,在水平方向左转90°,右转90°返回至初始位置后垂直取出,以除去漆膜表面携带的多余的CASS溶液,整个过程用时约3s。
(4)湿热放置
将样件以45°倾斜角放置在温度(65±1)℃ &空气湿度(85±3)%RH &气流(6~24m/min)的恒温恒湿试验箱内,放置时间672h,每隔168h检查样件表面上丝状腐蚀的生长情况,中期检查时每次样件被拿出湿度箱的时间不能超过15min。
3.2.1腐蚀结果评价
测试结束后对丝状腐蚀的结果进行评价,划痕两端的各5mm忽略不作为评价范围,腐蚀长度的测量必须垂直于划痕,而不是沿着腐蚀蔓延的方向,且测量的时候避免将划痕包括在内,记录划痕两边最大的腐蚀长度,并查看其他区域是否有丝状腐蚀现象出现。
3.2.2测试结果的影响因素及条件控制
丝状腐蚀试验过程由多个步骤组成,任一环节出现偏差都可能对实验结果造成较大影响[12],以SAE J 2635为例,影响试验结果重复性及再现性的主要因素有:
(1)划痕工具:不同类型的划痕工具其划痕宽度、划痕均匀性及划痕深浅均有所不同,导致在盐雾环境过程中划痕处的腐蚀量及去离子水冲洗样件过程中划痕处盐雾残留量不同,从而对测试结果产生一定的影响,因此,实验室测试过程中应采用同一划痕工具,且刀头角度及划痕深度应保持一致。划痕工具的示例如图4所示。
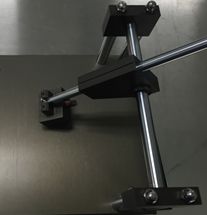
图4 划痕工具的示例图
(2)盐雾试验箱:盐雾试验箱的参数条件应严格按照标准运行,盐雾环境的变化将会导致划痕处“生长引发点”的变化,从而导致腐蚀生长发生变化。
(3)样件清洗过程:样件取出后应尽快清洗,以防时间较长盐溶液干燥形成颗粒不易去除,使得腐蚀结果加重;且冲洗时间应严格控制,以保证样件上盐雾残留量保持适量;同时还应保证去离子水的质量以及更换频率。
(4)湿热试验箱:湿热试验箱参数控制对腐蚀生长具有重大的影响,除了要控制温度及相对湿度使其稳定并维持在标准要求范围内以外,还应控制风速及隔板位置,使得湿热箱内每层风速都能达到标准要求,从而保证整个试验箱内的腐蚀均匀性。
3.3 丝状腐蚀试验的质量控制及意义
为保证丝状腐蚀结果的可靠性,除需对测试结果产生影响的参数进行严格控制外,每次试验时还应采用专业机构提供的具有已知腐蚀增长量的标准板(如图5)对实验过程进行监控,或采取其他适合的方法进行实验室间的比对,对实际样件(如图6)的实验结果进行校正,以确保测试结果的准确性。
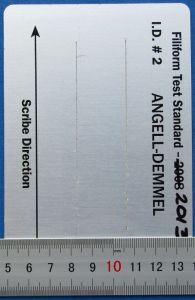
图5 标准板丝状腐蚀
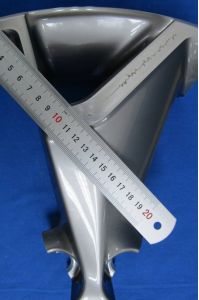
图6 实际样件丝状腐蚀
4 结语
材料腐蚀不仅给国民经济带来了巨大损失,同时也造成了金属资源和能量的大量浪费,还可能造成环境污染,大大阻碍了可持续发展。因此对腐蚀的科学研究具有很重要的意义。丝状腐蚀开始时一般主要是外观问题,但丝状腐蚀的产生会破坏涂层的完整性(如涂层发生剥离、起泡等),从而使水汽进一步进入,引发更严重的腐蚀问题]。丝状腐蚀一方面可破坏涂层附着力,使涂层剥蚀并失去防护作用,加剧基体的进一步腐蚀破坏;另一方面,丝状腐蚀区域还可能造成应力集中,加速金属的腐蚀疲劳,导致强度下降。因此,在基材的表面处理以及防护涂层的工艺方面如何有效防止丝状腐蚀的产生至关重要。通过实验室丝状腐蚀加速试验,可有效模拟实际应用中的腐蚀现象,从而为产品的研发、工艺改进以及产品的质量控制提供技术支持。
更多关于材料方面、材料腐蚀控制、材料科普等方面的国内外最新动态,我们网站会不断更新。希望大家一直关注国家材料腐蚀与防护科学数据中心http://www.ecorr.org