航空表面涂层技术是航空制造技术的重要组成部分之一。采取一定的表面工程手段在飞行器零部件表面制备具有特定防护或功能涂层,可以使零部件表面具有隔热、减摩可磨耗封严、耐磨防腐蚀、抗高温氧化、吸波隐身等功能。目前,航空表面涂层技术发展最快也是最重要的涂层,包括热障涂层(TBCs)、超高温复合材料(C/C、C/SiC、SiC/SiC)部件表面环境障涂层(EBC)、高温可磨耗封严涂层、WC-Co 及氧化铝钛等耐磨涂层、吸波及红外隐身涂层等技术,涂层的应用大幅度提高了航空产品的性能、可靠性、经济性、服役寿命及战机的生存能力。涂层新材料、新技术的出现在推动表面工程科学发展的同时,也节约了资源、减少了有害物质排放,促进了环境友好型绿色制造、可持续发展战略的落实。
航空表面涂层技术的发展现状
航空表面涂层的成熟运用对欧美F-22、F-35、波音787、空客A380、A400M 等新型飞机的商业化起到了重大推动作用。热障涂层、高温可磨耗封严涂层的应用提高了发动机涡轮进口温度、工作效率,节省了燃油。MCrAlY、PtAl 等高温抗氧化涂层的成熟应用提高了发动机高温部件服役寿命,降低了维护成本。飞机起落架超音速火焰喷涂WC-Co-Cr 涂层代替传统硬铬电镀层,大幅度提高了起落架耐磨性能,寿命成倍延长。
热障涂层是发动机高温部件最重要的防护涂层之一,具有隔热功能,同时具备抗冲蚀、抗高温氧化、防熔盐腐蚀等功能,可大幅度提高燃烧室及涡轮高温部件耐久性、可靠性。图1 为机器人自动喷涂发动机部件热障涂层照片。
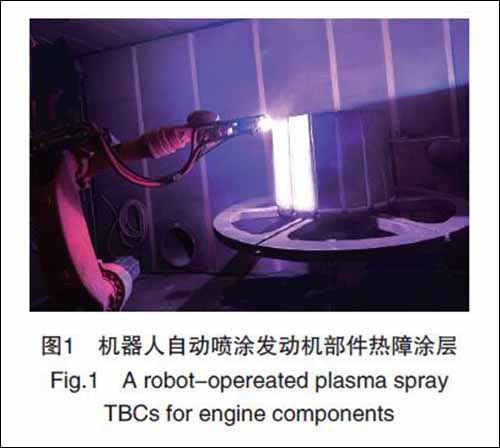
美国NASA 有成熟的高温封严涂层可磨耗性能试验系统,开发的MCrAlY 基合金型高温可磨耗封严涂层可提高涡轮机匣的寿命。国内发动机高温部件用超高温热障涂层、高温抗氧化涂层技术及可磨耗封严涂层技术近年来得到了快速发展,取得了很多实验室成果,但与国外先进技术相比,仍有很大差距,主要是热障涂层、高温抗氧化涂层、高温可磨耗封严涂层可靠性、使用寿命不足。近年来国内多家大学、科研院所及发动机主机厂开发了多种稀土锆酸盐及稀土铈酸盐类超高温热障涂层,微观上大多呈烧绿石结构或萤石结构,其导热系数明显低于Y2O3-ZrO2 传统热障涂层,但其关键技术指标——抗热冲击性能还有待提高。
虽然国内高温封严涂层早已实现工程化应用,但没有建立起高温封严涂层可磨耗性能及可靠性评价标准体系,而涂层发动机试车考核成本高昂,时间漫长、致使高温可磨耗封严涂层新材料及其涂层制备新工艺研究进展缓慢,涂层使用寿命仍然明显低于国外同类产品。在飞机耐磨涂层方面,近年来最大的进展是飞机起落架广泛采用超音速火焰喷涂WC-Co-Cr 涂层代替传统硬铬电镀层,耐磨性及使用寿命大幅增长,并消除了电镀污染。美国纳米集团(USNANO GROUP,INC.)开发的纳米碳化钴、纳米氧化铝钛涂层推广应用于航空轴类、环类部件,用于耐磨及篦齿封严,涂层具备高硬度、高韧性、高抗弯强度,其耐磨性能远超传统同类涂层,应用前景十分广阔。
航空表面涂层技术的新进展
1 超高温热障涂层
航空发动机现广泛采用的3.5~4.5mol%Y2O3 部分稳定ZrO2 热障涂层的长期工作温度不能超过1200℃,否则在随后冷却过程中将发生四方相向单斜相相变,该过程中材料体积膨胀约4%,使涂层开裂剥落失效。为进一步提高燃气涡轮发动机工作温度、延长相关高温部件热循环寿命,新型超高温热障涂层材料成为业界研究热点。由于氧化钇部分稳定氧化锆涂层在1200℃以下表现出优异的热学及力学性能,氧化钇稳定氧化锆理所当然成为研究和开发新型超高温热障涂层材料体系的基础。北京航空制造工程研究所开发的Sc2O3、Gd2O3、Yb2O3 三元稀土氧化物复合稳定ZrO2 及Sc2O3、Y2O3 二元稀土氧化物复合稳定ZrO2 热障涂层,工作温度可达1500℃,为单一四方相结构,长期工作无相变,使热障涂层承温能力提高了200℃,有望实现工程化应用。Sulzer Metco(现为Oerlikon Metco)开发的Gd2O3、Yb2O3、Y2O3 三元稀土氧化物复合稳定ZrO2 工作温度1500℃仍可保持相稳定,涂层热导率明显低于一般热障涂层。多元稀土氧化物复合掺杂ZrO2 是超高温热障涂层材料重要发展方向。
国内近年开发了系列锆酸镧、铈酸镧或铈锆酸镧热障涂层材料,如L a2C e2O7、L a2Z r2O7、S m2Z r2O7、La2(Zr0.7Ce0.3)2O7。为消除热收缩现象还研制了一些成分更为复杂的改性材料,如La1.8W0.2Ce2O7.6、La2Zr1.7Ta0.3O7.15 等,这些稀土锆酸盐类化合物大多数呈烧绿石结构、萤石结构或者缺陷萤石结构,其导热系数明显低于稀土氧化物稳定ZrO2热障涂层材料,但抗热冲击性能还有待提高。如将这些锆酸盐类化合物与传统3.5~4.5mol%Y2O3 部分稳定的ZrO2 组成双陶瓷层结构热障涂层,则可发挥传统材料热膨胀系数大、断裂韧性高的优点,明显延长热障涂层热循环寿命,同时保留稀土锆酸盐类化合物不发生相变、抗烧结、热导率低、抗腐蚀的优点,这是未来发展使用温度超过1300℃的超高温热障涂层的重要途径之一。需要特别强调的是,不管是采用等离子喷涂(PS)还是电子束物理气相沉积(EBPVD)制备稀土锆酸盐类化合物热障涂层,涂层最终组成往往不同于粉末喂料或靶材,为保持制备的涂层组成符合设计的化学计量比例,粉末或靶材成分设计、沉积工艺过程精确控制十分重要,并将决定最终涂层性能及使用寿命,而使用寿命是其能否成功应用于航空产品的关键所在。
研究表明,CMAS 严重影响热障涂层耐久性及最高使用温度。CMAS为CaO、MgO、Al2O3、SiO2 等组成的硅酸盐类物质,CMAS 在约1250℃熔化,它可熔解热障涂层材料,还会浸润热障涂层、通过毛细作用沿孔隙及柱状晶之间间隙渗入热障涂层内部,使热障涂层表面变粗糙、内部变疏松,并在发动机停车冷却循环过程中,CMAS 熔盐凝固成玻璃态物质,其贯穿层模量会上升,热障涂层应变容限将骤降,随后热循环中热障涂层将可能大范围剥落,大幅降低发动机涡轮叶片耐久性,甚至造成涡轮叶片烧蚀而出现灾难性后果。预防CMAS 腐蚀的方法一般是在热障涂层表面制备一层与CMAS 熔盐反应形成固态致密层的物质,资料报道含大直径稀土阳离子的萤石或烧绿石结构材料能与CMAS 熔盐反应形成高熔点固态致密层,可有效阻止CMAS 进一步贯穿侵蚀。
2 高温复合材料表面环境障涂层
C/C 复合材料在高温条件下存在严重的氧化和烧蚀问题,C/SiC、SiC/SiC 陶瓷复合材料部件在高温水蒸气环境下存在性能退化及易受CMAS 熔盐侵蚀问题。环境障涂层(EBC)是为提高C/C、C/SiC、SiC/SiC高温复合材料部件环境稳定性的表面防护涂层。EBC 为多层结构,如C/SiC 复合材料基体表面制备Si+ 莫来石+BSAS 复合EBC。EBC 顶层材料至关重要,一般采用BaO-SrOAl2O3-SiO2 材料(BSAS)。但BSAS在1300℃以上环境工作仍然存在化学稳定性问题,BSAS 会与SiO2 反应生成一种低熔点玻璃相(熔点低于1300℃),导致EBC 在工作温度超过1300℃时过早剥落失效,这就限制了其在更高温度下的使用。
NASA Glenn 研究中心研究表明,一些稀土硅酸盐Re2Si2O7(Re 为Sc、Lu、Yb、Tm、Er 及Dy 等)有良好的高温化学稳定性,1500℃长期无相变,在1400℃与莫来石化学相容性好,其在1500℃下抗水蒸气腐蚀能力优于BSAS。但稀土硅酸盐作为EBC 面层材料,与莫来石热膨胀系数匹配不如BSAS,易在热循环过程中产生裂纹,而影响涂层可靠性和防护性。现也有在BSAS 涂层上再沉积稀土硅酸盐Yb2SiO5 涂层的,Yb2SiO5涂层可提升EBC 抗CMAS 侵蚀能力。总之,稀土硅酸盐作为EBC 涂层组成材料应用研究还不够成熟,但具有作为新一代EBC 面层材料的应用开发潜力,值得深入研究。
3 高温可磨耗封严涂层
高温可磨耗封严涂层用于发动机涡轮气路密封,可减小涡轮叶片叶尖与涡轮外环之间的间隙,进而减少气体泄漏、提高发动机效率。一般设计要求在涡轮叶片与封严涂层发生接触刮擦时涂层被刮削而叶片磨损甚小,并且摩擦系数要小,以免刮擦产生的高温造成涂层或叶片烧蚀开裂,因此高温可磨耗封严涂层需具有一定的减摩功能。一般来说,金属基可磨耗封严涂层抗气流冲蚀性能优良,而氧化物陶瓷基可磨耗封严涂层抗气流冲蚀能力相对较差,因此在材料组成及涂层制备工艺参数控制方面必须予以高度关注,以保证涂层使用寿命。近年来,等离子喷涂MCrAlY 高温合金型(如NiCrAlY、CoCrAlY、NiCrAlYSi 等)可磨耗封严涂层及陶瓷基(如稀土氧化物稳定ZrO2、Al2O3 等)可磨耗封严涂层获得了明显进展,涂层可磨耗性能和抗冲蚀性能明显提高。MCrAlY 具有高温抗氧化和抗热腐蚀作用,一般添加聚苯酯作为造孔剂,聚苯酯加热去除后在涂层内留下大量细小均匀分布的孔隙可以降低涂层硬度、增强涂层可磨耗性、减轻涂层对涡轮叶片的磨损。添加六方BN 或氟化物作为减摩自润滑材料,降低摩擦系数。高温可磨耗封严涂层厚度一般超过1.5mm,必须采用机器人自动喷涂技术,喷涂参数计算机闭环控制、涂层厚度在线监测,这样才能保证涂层组织结构及厚度均匀性及再现性。采用纤维增强涂层技术可明显提高封严涂层热循环寿命,图2 为纤维增强可磨耗封严涂层扫描电镜照片。
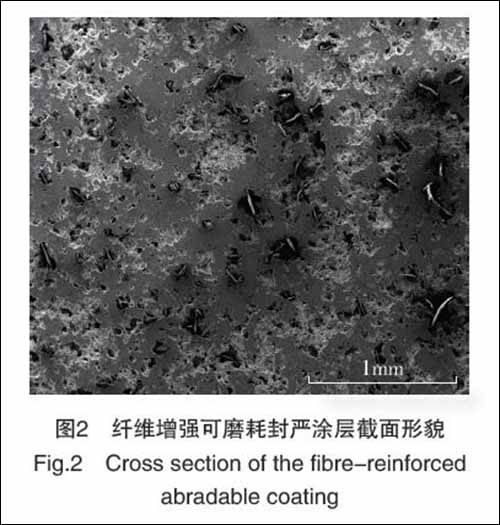
Oerlikon Metco 研制的Dy2O3-ZrO2-hBN- 聚苯酯高温可磨耗封严涂层用于航空发动机高压涡轮气路封严工作温度可达1200℃,工作寿命比普通Y2O3-ZrO2-hBN- 聚苯酯高温封严涂层提高4 倍以上。对于SiC/SiC 陶瓷复合材料(CMC)涡轮部件,在EBC 的基础上制备多孔Yb2Si2O7 及Yb2O3、Sm2O3 或Gd2O3 等掺杂ZrO2 涂层作为可磨耗涂层,目前取得了积极进展。
4 热喷涂陶瓷涂层代替硬铬电镀层技术
因电镀硬铬对环境有持久的危险性,电镀废液中的六价铬更是严重危害人体健康,减少直至取消电镀硬铬工艺意义重大。近年来超音速火焰喷涂(HVOF、HVAF)WC-Co、WC-Co-Cr、Cr3C2-NiCr 金属陶瓷涂层、等离子喷涂Cr2O3 及A12O3-TiO2氧化物陶瓷涂层在工业上获得广泛应用,全面取代电镀硬铬工艺已是必然。HVOF 喷涂WC-Co-Cr 涂层在空客、波音、洛克希德· 马丁等生产的先进军民用飞机(包括空客A380、波音787、F-35 等)已成功应用,结果表明HVOF 喷涂的WC-Co-Cr 涂层在耐磨、防腐蚀、抗疲劳等关键性能指标明显优于传统硬铬电镀层。Cr3C2-NiCr 涂层广泛用于高温摩擦磨损环境,涡轮导向器篦齿封严采用HVOF 喷涂Cr3C2-NiCr 硬质涂层(主动磨削涂层)或等离子喷涂A12O3-TiO2 陶瓷硬质涂层,具有耐蚀、高温抗氧化、耐磨损等能力。等离子喷涂Cr2O3 陶瓷硬质涂层在发动机动密封及飞机运转部件磨损防护方面应用广泛,其耐磨性及防腐蚀性比传统硬铬电镀层提高数倍。
5 纳米涂层
纳米材料技术是20 世纪80 年代诞生并仍快速发展的新技术,受到世界各国高度重视。PVD(物理气相沉积)、热喷涂、CVD(化学气相沉积)、MBE(分子束外延)、化学沉积、电沉积等方法是获得纳米涂层或薄膜的典型方法。近10 年来研究人员利用PVD(包括磁控溅射、离子束溅射、射频放电离子镀、等离子体离子镀、EB-PVD 等)在制备纳米单层膜及纳米多层膜方面取得很多成果,如纳米Ti(N,C,CN)、(V,Al,Ti、Nb、Cr)N、SiC、β-C3N4、α-Si3N4、TiN/CrN、TiN/AlN、WC-Co 薄膜或涂层可用于飞机轴类零件耐磨防腐,等离子喷涂纳米A12O3-TiO2 涂层已用于航空发动机气路封严,纳米Y2O3-ZrO2涂层已用于涡轮叶片隔热防护,添加石墨烯、碳纳米管复合涂层具有雷达隐身功能。总之,近年来在基础研究和应用开发方面纳米涂层已取得巨大进展,有的已在航空、舰船等产品的防腐、耐磨、隔热、吸波隐身、防海洋生物附着、自清洁等功能涂层上获得应用。
热喷涂是制作纳米涂层的极有竞争力的方法之一,与其他技术相比,具有许多优越性,如工艺简单、涂层材料和基体选择范围广、可制备厚涂层、沉积速率高、涂层成分易控制、容易形成复合功能涂层等,适用于大型零部件。采用纳米团聚粉末作为热喷涂喂料,通过严格控制工艺参数,缩短纳米材料在焰流中的停留时间、限制原子扩散和晶粒长大,可制备纳米涂层。美国纳米集团英佛曼公司(Inframat Co.)开发的等离子喷涂纳米A12O3-TiO2 复合涂层与传统A12O3-TiO2 涂层相比,耐磨损能力提高5 倍、抗疲劳能力提高10 倍、弯曲180° 无裂痕(传统A12O3-TiO2 涂层弯曲180° 后开裂剥落)、涂层附着力提高4倍,纳米涂层表现出极其优异的性能。
表面涂层设备重要进展
1 冷气动力喷涂
冷气动力喷涂,简称冷喷涂,根据不同喷涂材料及零件基体,冷喷涂中工作气体可为N2 或He,工作气体1将固态粒子加速至300~1200m/s,与零件基体碰撞发生剧烈的塑性变形而沉积形成涂层,粒子沉积主要靠其动能来实现。冷喷涂可有效避免喷涂粉末材料的氧化、分解、相变、晶粒长大,对基体几乎没有热影响,可用来喷涂对温度敏感的易氧化材料、纳米材料。需特别注意的是冷喷涂对喷涂粉末材料粒度、形态及纯度(如含氧量)要求十分严格,国际上只有少数几家粉末材料供应商可提供冷喷涂粉末货架产品,且价格昂贵。冷喷涂制备Al、Cu、Cu 合金、Ti、Ta、TiAl、FeAl、AlNi、Ni 合金等涂层非常成功,通过真空扩散热处理可实现冷喷涂涂层与零件基体间冶金结合,结合强度可达200MPa 以上。图3为典型高压冷喷涂枪体。
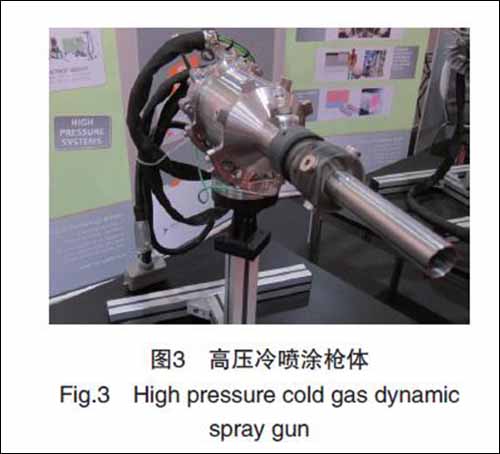
2 超低压等离子喷涂
超低压等离子喷涂(PlasmaSpray-Physical Vapor Deposition,PSPVD),是在低压等离子体喷涂(LowPressure Plasma Spray,LPPS,喷涂时压力为几千帕)基础上,进一步降低真空室的工作压力至几百帕甚至100Pa 以下,同时大幅度提高等离子喷枪功率,将粉末加热熔化、并有部分气化,在等离子射流中同时存在气液两相,沉积形成涂层的过程。通过粉末颗粒加热状态控制可获得气相沉积与颗粒沉积的混合组织,既可制备薄膜,也可制备厚度数百μm 的涂层。制备的MCrAlY 涂层孔隙率低,结合强度可达80MPa 以上,通过扩散处理可进一步提高结合强度。制备的YSZ 陶瓷涂层呈现类似EBPVD的柱状晶结构,如图4 所示。
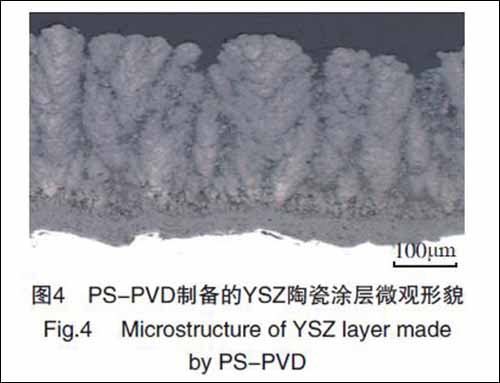
3 溶液等离子喷涂
溶液等离子喷涂根据液体喂料不同,分为前驱体溶液等离子喷涂(Solution Precursor Plasma Spray,SPPS)和微纳米颗粒悬浮液等离子喷涂(Suspension Plasma Spray, SPS),将液体喂料直接送入等离子焰流在零件表面沉积形成涂层。采用前驱体化合物液体直接喷涂制备纳米结构热障涂层,简化传统纳米氧化锆粉末喷涂涂层制备的复杂工序,可降低材料损耗和工艺过程成本。并且溶液等离子喷涂制备纳米结构热障涂层能有效避免纳米晶粒长大,涂层孔隙细小、分布均匀。美国英佛曼公司采用前驱体化合物液体喂料,采用大气等离子喷涂设备成功制造带垂直裂纹结构的纳米热障涂层,其热冲击寿命超过EB-PVD 工艺制备的热障涂层,比传统粉末等离子喷涂工艺制备的热障涂层寿命提高1 倍以上。图5为溶液等离子喷涂技术制备的带垂直裂纹的热障涂层典型照片。采用悬浮液作喂料可解决普通粉末送粉器无法直接输送微纳米粉末的难题,在制备高孔隙率TiO2、Al2O3、ZrO2 等功能涂层方面有较大进展,但存在设备喷涂功率需求大、涂层沉积效率低、结合强度低等缺点,要大面积推广还有大量工作要做。
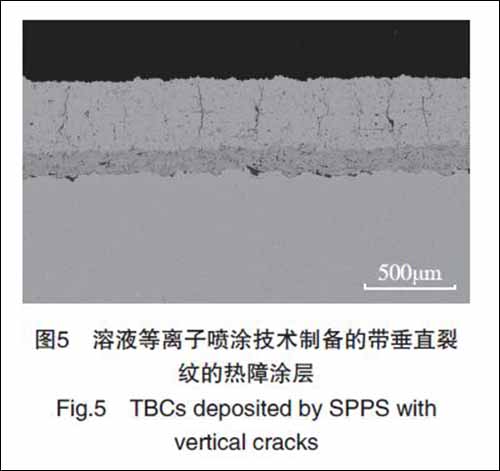
结束语
表面涂层技术是制造技术重要组成部分,以个人技术经验为主的传统表面涂层技术已不能满足现代航空工业发展需要。现需抓紧建立大型表面涂层应用数据库,以大数据技术、传感技术、计算机自动控制技术、机器人技术、网络技术为基础,根据零部件外形与功能、服役环境与使用寿命需求,实现涂层材料与涂层结构设计、涂层制备加工方法选择与工艺实施、涂层质量检测与评价等整个涂层制备过程自动化、智能化,促进航空表面涂层技术又好又快的发展。(转载:航空制造技术)
更多关于材料方面、材料腐蚀控制、材料科普等等方面的国内外最新动态,我们网站会不断更新。希望大家一直关注国家材料腐蚀与防护科学数据中心http://www.ecorr.org