地效飞行器在波浪中起降的过程位于气水交界面上,受到高航速和波浪的双重作用,这就对地效飞机的材料选择提出了较高的要求,既要具有良好的抗冲击性、抗海水腐蚀性以及足够的强度、刚度、抗疲劳性能,又要尽量减轻结构重量。铝合金材料作为飞机设计的传统材料,在强度、刚度、抗冲击性方面性能优异,但是其抗海水腐蚀性能差,而地效飞机的服役环境以海洋为主,海水的腐蚀极大增加了飞机的维护成本,降低了结构寿命。先进的复合材料由于比强度比刚度高、可设计性强、抗疲劳断裂性能好、耐腐蚀、结构尺寸稳定性好等一系列优点,其在飞机上的应用量已成为当今衡量飞机先进性的重要指标。地效飞机应用复合材料不仅可解决飞机的海水腐蚀问题,同时由于复合材料可剪裁设计和便于大面积整体成型的独特优点,可减轻结构重量,减少机械连接及整机的装配任务量,在一定程度上降低了工装成本。
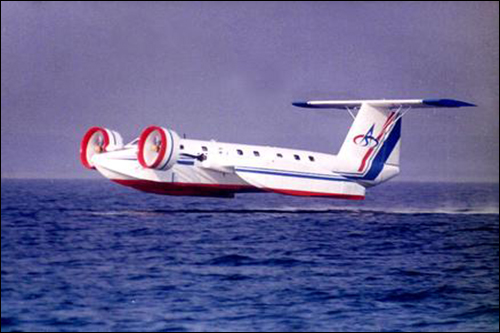
国外复合材料应用现状
当今世界上存在着一种飞机结构复合材料化的趋势,飞机设计要求为减重每1克重量而奋斗,比重仅为1.6g/cm3的先进复合材料,能够给飞机结构带来20%~30%的减重,这是其他手段无法企及的。此外复合材料还具有可设计性强、疲劳性能好、耐腐蚀、便于整体成型等一系列的优点。国外飞机结构设计中复合材料应用技术已十分成熟。
大型客机方面,以波音公司的B787为例,其复合材料用量占结构重量的50%以上,包括机翼、机身、垂尾、平尾、发房、地板梁及部分舱门、整流罩等。在设计过程中采用了多项复合材料关键技术,包括新材料体系的研发、先进的结构形式、低成本的制造工艺等,使飞机结构重量大大减轻,运行成本也大幅下降,座公里数比其他同类飞机低10%,燃油消耗比其他同类飞机低20%,检修时间由500小时提高到1000小时,检修率相对降低30%。
军机方面, 复合材料在军机上的应用范围远高于民机。以F-22为例,其复合材料的总用量占结构重量的25%,以双马树脂为主的热固性复合材料占24%,热塑性复合材料占1%。在制造过程中采用RTM技术制造的复合材料件达400件,占复合材料结构重量的25%,采用该技术后比原设计节省开支达2.5亿美元。美国F-35的垂尾采用整体成型技术,制成了单件最大、最复杂的RTM成形航空结构件,制件长3.65m,重约90kg,减少紧固件1000多个,降低成本60% 。
地效飞机方面,由韩国设计的20座级的地效飞机,其机翼、水平尾翼、操纵面均采用复合材料,为梁-蒙皮-泡沫夹层结构,材料选用碳纤维增强环氧树脂复合材料,泡沫为聚氨酯泡沫。机翼的重量仅为371.4kg,比目标重量轻了11.6kg。水平尾翼的重量为150kg,比目标重量轻了30kg。
复合材料在军机及民机上应用的成熟技术,对于地效飞机同样适用,这些型号的经验积累为复合材料应用于地效飞机打下了坚实的基础。
国内复合材料应用现状
我国飞机结构上对复合材料的应用追随着国际上先进国家的脚步,发展的历程基本相同。军民用飞机的各类舵面上选择复合材料结构已经很普遍。国内最早在歼8飞机的垂尾上应用复合材料,在苛刻的飞行条件下飞行使用近20年,地面检查无任何问题。在运7系列支线飞机的腹鳍、方向舵等次结构上应用了先进复合材料。到了90年代中期设计、研制成功了运7复合材料垂尾,并取得了适航证。中国自行研制的歼8Ⅱ带整体油箱的复合材料机翼自1995 年装机飞行12 年来亦毫无问题,至今仍在服役。歼10作为三代战机的代表,垂尾及内外侧副翼等都采用复合材料。复合材料的大量使用以及采用先进的机动外形和高性能发动机,使我国战机作战能力有了极大的提升。ARJ21在客舱地板、货舱天花板、侧壁板、前后短板以及方向舵都采用了复合材料设计,其复合材料用量占结构重量的2%。目前,复合材料的适航验证工作即将完成。运12F的升降舵、方向舵、副翼、翼尖、翼身整流罩等部件都采用了复合材料设计,操纵面的调整片也都选用碳纤维面板和全高度蜂窝夹层结构设计,目前运行状态良好。
地效飞机应用复合材料好处
地效飞机服役环境以海洋为主,复合材料的应用会带来铝合金材料无法比拟的优异性能,主要表现在以下几个方面:
减重效益 复合材料为各向异性材料,单层性能具有明显的方向性,因此复合材料层合板刚度和强度性能可“剪裁”,即通过调整每个单层的铺设角、铺层比、铺层顺序来获得所需的强度和刚度性能,恰似量体裁衣,这种特殊的剪裁性能使复合材料相对于铝合金材料明显的减轻结构重量,提高飞机有效载荷。研究表明,飞机结构应用复合材料相对于铝合金材料可减重20%~30%。
提高抗腐蚀能力 复合材料具有优异的抗腐蚀性能,比强度、比刚度大,在地效飞机上应用复合材料可有效避免腐蚀问题。
降低工装成本 传统的铝合金结构往往采用分离式制造方法,多个零件单独加工后再通过紧固件装配成组件,期间还有可能会用到大量的连接角材,既浪费了重量又增加了装配成本。以长桁加筋壁板为例,若采用复合材料制造,基本蒙皮和长桁可通过共固化或共胶接的形式做成整体壁板,整个过程不会用到一个紧固件,既降低了重量又节约了成本。
此外,复合材料还可以通过铺层设计和组件化整体设计实现在一个结构内包括不同材料、性能差异的分组件,甚至包括金属、陶瓷件等,减少了零件数量,简化了装配程序,降低了工装成本。
地效飞机复合材料关键技术
海洋环境湿热影响 在湿热环境下,树脂基体会吸收水分,导致复合材料构件力学和物理性能下降。地效飞机服役环境以海洋为主,考虑海面湿气及海水对复合材料浸泡侵蚀的影响,应用于地效飞机的复合材料在材料选择阶段,要考虑最高使用温度和长时间高温下材料饱和吸湿,在设计验证阶段,要着重验证湿/热条件下复合材料的压缩性能。
提高材料的抗冲击性 地效飞机在水面起降的过程中,海浪对飞机结构有很强的冲击力,要求材料具有良好的抗冲击性。目前国内外就提高复合材料抗冲击性做了大量研究,主要包括以下几点:
增韧树脂基体 树脂基复合材料抗低速冲击能力在很大程度上取决于树脂的韧性。习惯上,以复合材料冲击后压缩强度CAI值划分树脂基体的韧性等级。冲击能量67J/cm冲击后,CAI值大于195MPa为韧性树脂基体。
提高纤维模量 为满足新一代高性能飞机的减重要求,航空工业对碳纤维提出了韧性要求,即将纤维拉伸强度和拉伸模量提高30%~40%,使纤维断裂伸长率提高20%,并要求与韧性树脂基体组合提高抗损伤能力。
三维增强体 通过编、缝、织等在厚度方向引入纤维的3D复合材料可有效抑制复合材料的损伤增长,已广泛地用于提高复合材料抗层间断裂能力和冲击损伤容限。
先进的树脂和纤维在大型飞机主承力结构上的应用说明改进的复合材料的抗冲击性可以与金属材料媲美,地效飞机上应用先进复合材料能够满足海浪冲击的要求。
纵观目前复合材料以及复合材料的成型技术发展状况,实现复合材料在地效飞机上的应用必须从以下几条入手:
材料体系设计 在材料选择时,主要在湿热环境和冲击环境下综合考虑树脂、纤维、树脂和纤维的界面三个方面的性能。树脂主要考虑最高使用温度、饱和吸湿量及树脂的韧性。纤维主要考虑纤维的强度、模量及抗腐蚀能力。同时,要着重考虑纤维和界面的粘附能力。
抗冲击的复合材料结构设计技术 复合材料结构用于地效飞机可以带来抗腐蚀、结构强度高、刚度大和重量轻的好处。同时也引入了复合材料的一个缺点,就是抗面外冲击能力弱的特点。通过研究不同的结构形式、增强纤维的种类、树脂的类型、铺层方式、纤维含量及铺层数量相关内容,提高复合材料结构的抗冲击性。
数字化设计技术 通过数字样机可以实现全机各零部件的优化设计,设计阶段即可以对制造过程仿真,精确分析复合材料零部件公差,合理分配,确保一次制造出合格的制件。