蠕者,慢也。蠕变时效成形技术,是一种慢心态的技术。
1.什么是蠕变时效成形
在讲时效成形之前,先来科普一下什么是蠕变。蠕变是指固体材料在一定的温度和较小的恒定外力作用下,其形变随时间增加而逐渐增大的现象。举个生活中常见的栗子,家里用的晾衣绳,刚挂上去的时候绷得很紧,但晾晒衣服用得久了绳子就变得松弛了。

松弛的晾衣绳
最为关键的一点是,材料的变形不是像塑性变形那样在短时间较大的力作用下完成,而是远小于其屈服强度的力长时间持续缓慢作用的结果。
有了蠕变的概念,我们再来看看什么是蠕变时效成形。蠕变时效成形(creep-age forming)主要是将材料的人工时效与零件成形相结合,同时利用材料在弹性应力作用下于一定温度时发生的蠕变变形,从而得到带有一定形状的结构件。
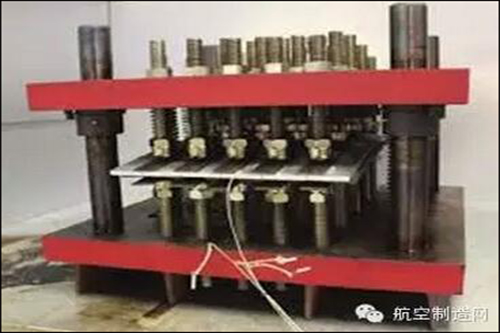
铝合金蠕变时效成形
2.蠕变时效成形的过程
蠕变时效成形工艺过程可分为3个阶段:
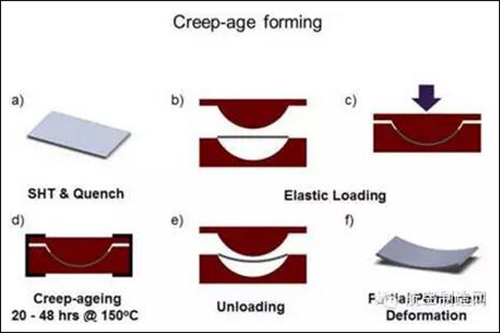
蠕变时效成形工艺过程
1)加载。在室温下,将零件通过一定的加载方式使之产生弹性变形,并固定在具有一定外形型面的模具上。
2)人工时效。将零件和模具一起放入加热炉或热压罐内,在零件材料的人工时效温度内保温一段时间,材料在此过程中受到蠕变、应力松弛和时效机制的作用,内部组织和性能均发生较大变化。
3)卸载。在保温结束并去掉模具的约束后,所施加到零件上的部分弹性变形在蠕变和应力松弛的作用下,转变为永久塑性变形,从而使零件在完成时效强化的同时,获得所需外形。
3.蠕变时效成形的力学特性
下图是蠕变时效成形过程中应力与应变的关系曲线。
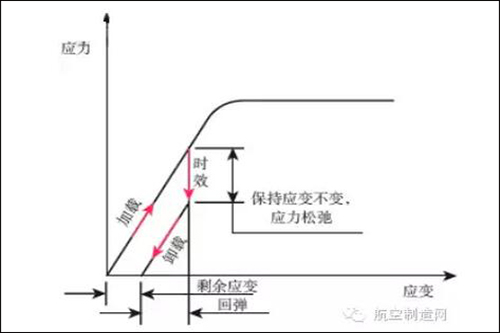
时效成形过程的应力应变路径
在初期弹性加载的过程中,弹性应变逐渐增加;当进入时效保温过程时,随着加载时间的增加,蠕变变形逐渐增加,而弹性形变因总变形不变而逐渐减少,由于弹性变形降低引起应力相应地减少产生应力松弛;最后,去除外加约束,零件自由回弹,由于蠕变应变的存在,零件将无法回弹到初始状态,从而保留了一定的外形。
4.蠕变时效成形的优势
与传统的冷加工塑性变形相比,蠕变时效成形的优点主要有:
1)蠕变时效成形时,成形应力通常低于其屈服应力,因此相对于常规塑性变形而言,时效成形减小了零件因进入屈服状态后而引发失稳甚至破裂的危险,大大降低了零件发生加工裂纹的几率;
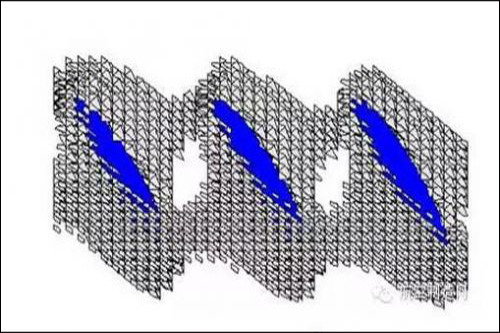
塑性变形中的裂纹扩展
2)利用材料时效强化和应力松弛特性,在成形的同时,还完成了对零件材料的人工时效强化,从而改善了材料的微观组织,提高了材料强度;
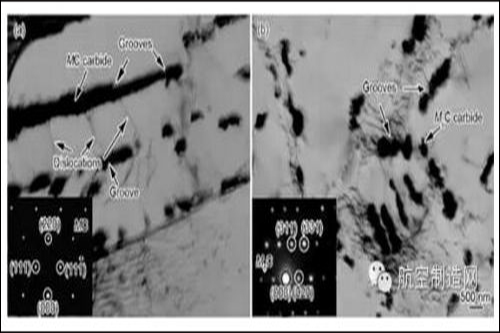
蠕变时效成形中长条状碳化物逐渐变成颗粒状
3)蠕变时效成形的零件具有很高的成形精度、可重复性和成形效率。在成形复杂外形和结构的零件时,时效成形技术仅需要一次热循环就可使零件的外形达到所需精度,外形精度误差小于1mm;

蠕变时效成形加工的高精度飞机薄板结构
4)蠕变时效成形的零件内部残余应力几乎完全被释放,尺寸稳定,不会出现像喷丸成形的零件在放置一段时间后因内部残余应力释放而造成外形变化等问题。此外,对于焊接整体壁板,还可有效降低焊接残余应力,增强耐应力腐蚀能力,延长零件的使用寿命。

低残余应力的飞机薄壁结构
5.蠕变时效成形的关键技术
01工装外型面优化技术
由于受到材料本身时效周期的限制,无法将试件内已有的弹性变形全部转变为塑性变形,因此成形后均存在一定的回弹量。通常,回弹量可达到总应变量的70%以上。因此,应用蠕变时效成形工艺需要精确预测回弹量,并将回弹量补偿到模具型面上,只有解决这一关键问题,才能得到所需的零件外形。
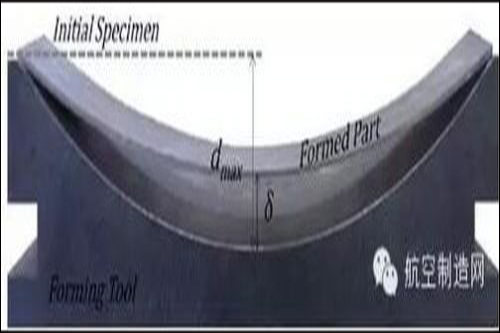
蠕变时效成形中的回弹现象
最初,对于零件成形后回弹量的确定主要是采用试错法,通过大量的基础工艺试验以及经验公式的外推来完成对模具型面的设计。由于这种方法效率不高,而且适应性较差,数值模拟被引入到了蠕变时效成形技术的研究中。
一种方法是通过有限元模拟的方法从宏观角度进行应力应变分析,利用有限元建立能够描述蠕变成形的材料本构模型。然而由于该方法忽略了成形过程中时效强化和塑性应变之间的相互作用,因此还无法对蠕变时效成形过程进行全面准确的描述。
当前,随着材料微观组织演化模拟理论的不断完善以及各种测试手段的出现,研究材料微观组织演变和蠕变时效成形过程工艺参数之间的关系,建立它们之间的本构方程,已成为当前该领域研究人员的主要研究方向。
02蠕变时效成形工装
蠕变时效成形发展之初,主要是通过机械压板或卡板使零件产生弹性变形,使用普通热处理炉即可进行。该种工装比较容易实现,但由于机械加载所产生的压紧力不够大且分布不均匀,因此该种方法一般仅限于成形不太厚的、厚度均匀的和加强筋与成形轴线平行的零件。
20世纪80年代中期,美国Textron公司开发了热压罐蠕变时效成形工艺。其基本的成形过程是先用真空袋和密封装置将零件和工装的型面密封起来,通过抽真空,使零件在上下表面空气压差的作用下固定到工装的型面上,然后一同放入热压罐内,通过热压罐的压力系统对零件施加足够的均匀压力,使零件完全贴合到工装型面上,与此同时加热到一定温度并保温一定时间,完成对零件的精确时效成形。因此,该工装工艺能够很好地控制零件的外形,特别适合具有复杂外形和结构的大型整体壁板构件的成形。
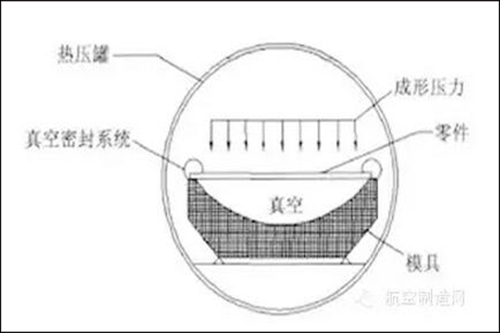
热压罐式蠕变时效成形原理图
6.蠕变时效成形与航空制造
由于蠕变时效成形具有诸多优点,因此欧美等国很早就开展了对时效成形技术的相关研究,并已将该技术广泛应用于飞机蒙皮和壁板制造中。
军用飞机方面,以美国B-1B超音速战略轰炸机的上下机翼壁板为典型案例。
在当时,这被认为是飞机工业使上所成形的最大、最复杂的机翼壁板。该零件材料采用可热处理强化的铝合金2124和2419,厚度突变从2.54mm增加到63.5mm,展向有整体加强桁条。该壁板的生产采用热压罐时效成形技术,壁板表面十分光滑,形状准确度高,装配贴合度可控制在0.25mm以下。
在民用飞机的应用方面,空客、波音和麦道的早期机型已经部分采用该项技术,如MD82、A330/340和A380等大型民用飞机的整体壁板制造中。
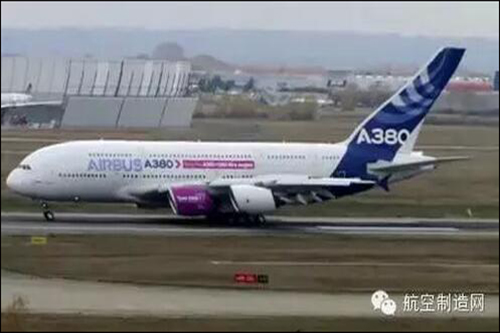
A380飞机
其中采用蠕变时效成形技术制造的A380飞机,机翼上壁板材料为铝合金7055,零件长33m,宽2.8m,变厚度3mm~28mm,成形后外形贴合度小于1mm。
2000年美国NASA的IAS(Integral airframe structures)研究计划将该技术列为整体机身结构的制造技术之一。