复合材料与金属、高聚物、陶瓷并称为四大材料。今天,一个国家或地区的复合材料工业水平,已成为衡量其科技与经济实力的标志之一。先进复合材料是国家安全和国民经济具有竞争优势的源泉。到2020年,只有复合材料才有潜力获得20-25%的性能提升。环氧树脂是优良的反应固化型性树脂。在纤维增强复合材料领域中,环氧树脂大显身手。它与高性能纤维:PAN基碳纤维、芳纶纤维、聚乙烯纤维、玄武岩纤维、S或E玻璃纤维复合,便成为不可替代的重要的基体材料和结构材料,广泛运用在电子电力、航天航空、运动器材、建筑补强、压力管雄、化工防腐等六个领域。本文重点论述航空航天先进树脂基体复合材料的国内外现状及中国的技术软肋问题。
1树脂基复合材料的发展史
树脂基复合材料(Resin Matrix Composite)也称纤维增强塑料(Fiber Reinforced Plastics),是技术比较成熟且应用最为广泛的一类复合材料。这种材料是用短切的或连续纤维及其织物增强热固性或热塑性树脂基体,经复合而成。以玻璃纤维作为增强相的树脂基复合材料在世界范围内已形成了产业,在我国不科学地俗称为玻璃钢。
树脂基复合材料于1932年在美国出现,1940年以手糊成型制成了玻璃纤维增强聚酯的军用飞机的雷达机翼的飞机,并于1944年3月在莱特-帕特空军基地试飞成功。1946年纤维缠绕成型技术在美国出现,为纤维缠绕压力容器的制造提供了技术贮备。1949年研究成功玻璃纤维预混料并制出了表面光洁,尺寸、形状准确的复合材料模压件。1950年真空袋和压力袋成型工艺研究成功,并制成直升飞机的螺旋桨。60年代在美国利用纤维缠绕技术,制造出北极星、土星等大型固体火箭发动机的壳体,为航天技术开辟了轻质高强结构的最佳途径。在此期间,玻璃纤维-聚酯树脂喷射成型技术得到了应用,使手糊工艺的质量和生产效率大为提高。1961年片状模塑料(Sheet Molding Compound, 简称SMC)在法国问世,利用这种技术可制出大幅面表面光洁,尺寸、形状稳定的制品,如汽车、船的壳体以及卫生洁具等大型制件,从而更扩大了树脂基复合材料的应用领域。1963年前后在美、法、日等国先后开发了高产量、大幅宽、连续生产的玻璃纤维复合材料板材生产线,使复合材料制品形成了规模化生产。拉挤成型工艺的研究始于50年代,60年代中期实现了连续化生产,在70年代拉挤技术又有了重大的突破。在70年代树脂反应注射成型(Reaction Injection Molding, 简称RIM)和增强树脂反应注射成型(Reinforced Reaction Injection Molding, 简称RRIM)两种技术研究成功,现已大量用于卫生洁具和汽车的零件生产。1972年美国PPG公司研究成功热塑性片状模型料成型技术,1975年投入生产。80年代又发展了离心浇铸成型法,英国曾使用这种工艺生产10m长的复合材料电线杆、大口径受外压的管道等。从上述可知,新生产工艺的不断出现推动着聚合物复合材料工业的发展。
进入20世纪70年代,对复合材料的研究发迹了仅仅采用玻璃纤维增强树脂的局面,人们一方面不断开辟玻纤-树脂复合材料的新用途,同时也开发了一批如碳纤维、碳化硅纤维、氧化铝纤维、硼纤维、芳纶纤维、高密度聚乙烯纤维等高性能增强材料,并使用高性能树脂、金属与陶瓷为基体,制成先进复合材料(Advanced Composite Materials, 简称ACM)。这种先进复合材料具有比玻璃纤维复合材料更好的性能,是用于飞机、火箭、卫星、飞船等航空航天飞行器的理想材料。
自从先进复合材料投入应用以来,有三件值得一提的成果。第一件是美国全部用碳纤维复合材料制成一架八座商用飞机--里尔芳2100号,并试飞成功。第二件是采用大量先进复合材料制成的哥伦比亚号航天飞机,这架航天飞机用碳纤维/环氧树脂制作长18.2m、宽4.6m的主货舱门,用凯芙拉纤维/环氧树脂制造各种压力容器。在这架代表近代最尖端技术成果的航天收音机上使用了树脂、金属和陶瓷基复合材料。第三件是使用了先进复合材料作为主承力结构,制造了这架可载80人的波音-767大型客运飞机,不仅减轻了重量,还提高了飞机的各种飞行性能。复合材料在这几个飞行器上的成功应用,表明了复合材料的良好性能和技术的成熟,这对于复合材料在重要工程结构上的应用是一个极大的推动。
2先进复合材料工业上通常使用环氧树脂的品种、性能和特性
复合材料工业上使用量最大的环氧树脂品种是缩水甘油醚类环氧树脂,而其中又以双酚A型环氧树脂为主,双酚F型环氧树脂(DGEBF)和双酚S型环氧树脂 。其次是缩水甘油胺类环氧树脂和缩水甘油酯类环氧树脂。其他还有酚醛环氧树脂;间苯二酚型环氧树脂、间苯二酚-甲醛型环氧树脂、四酚基乙烷型环氧树脂、三羟苯基甲烷型环氧树脂、富有柔韧性脂肪族多元醇缩水甘油醚型环氧树脂、环氧丙烯酸树脂和耐候性的脂环族环氧树脂,其可单独或者与通用E型树脂共混,供作高性能复合材料(ACM)。
缩水甘油胺类环氧树脂的优点是多官能度、环氧当量高,交联密度大,耐热性显著提高。目前国内外已利用缩水甘油胺环氧树脂优越的粘接性和耐热性,来制造碳纤维增强的复合材料(CFRP)用于飞机二次结构材料。
3复合材料使用的增强纤维
复合材料所用各种纤维材料性能比较见表1。对一些材料的性能进行了比较。由表1可见,仅玻璃纤维就比金属材料的比强度、比模量分别提高了540%、31%,碳纤维的提高则更为显著。据文献报道,由键能和键密度计算得出的单晶石墨理论强度高达150GPa[1]。因此碳纤维的进一步开发潜力是十分巨大的。日本东丽公司的近期目标是使碳纤维抗拉强度达到8.5 GPa、模量730 GPa。毋庸置言,碳纤维仍将是今后固体火箭发动机壳体和喷管的主要材料。
开发碳纤维复合材料的其他应用大有作为,如飞机及高速列车刹车系统、民用飞机及汽车复合材料结构件、高性能碳纤维轴承、风力发电机大型叶片、体育运动器材(如滑雪板、球拍、渔杆)等。随着碳纤维生产规模的扩大和生产成本的逐步下降,在增强混凝土、新型取暖装置、新型电极材料乃至日常生活用品中的应用也必将迅速扩大[2~4]。我国为配合北京奥运会,拟大力开发新型CFRP建材及与环保,日用消费品相关的高科技CFRP新市场[5]。
碳纤维是一种高强度、高模量材料,理论上大多数有机纤维都可被制成碳纤维,实际用作碳纤维原料的有机纤维主要有三种:粘胶纤维、沥青纤维、聚丙烯腈纤维。当前固体火箭发动机结构件用的碳纤维大多由聚丙烯腈纤维制成[6]。
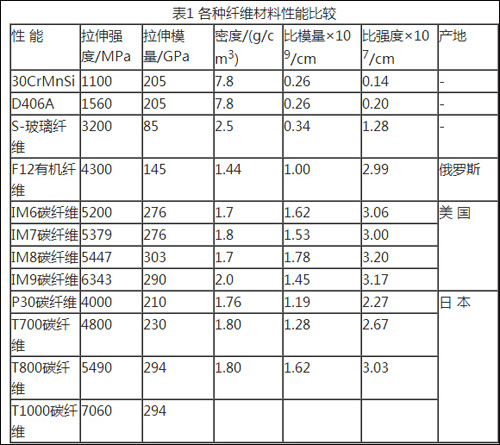
碳纤维的开发始于二十世纪六十年代,起初用于耐烧蚀喉衬、扩张段材料,后来逐渐在其它结构件上应用。自八十年代以来,碳纤维发展较大:① 性能不断提高;七、八十年代主要以3000MPa的碳纤维为主。九十年代初普遍使用的IM7、IM8纤维强度达到5300MPa。九十年代末T1000纤维强度达到7000MPa,并已开始工程应用。② 品种不断增多。以日本东丽公司为例,1983年生产的碳纤维品种只有4种,到1995年碳纤维品种达21种之多。不同种类、不同性能的碳纤维可满足不同需要,为碳纤维复合材料的广泛应用提供了坚实基础[5]。
4国防、军工及航空航天用树脂基复合材料
据有关资料报导,航天飞行器的质量每减少1干克,就可使运载火箭减轻500千克,而一次卫星发射费用达几千万美元。高成本的因素,使得结构材料质轻,高性能显得尤为重要。利用纤维缠绕工艺制造的环氧基固体发动机罩耐腐蚀、耐高温、耐辐射,而且密度小、刚性好、强度高、尺寸稳定。再如导弹弹头和卫星整流罩、宇宙飞船的防热材料、太阳能电池阵基板都采用了环氧基及环氧酚醛基纤维增强材料来制造。处于航天航空飞行及其安全的考虑所需,作为结构材料应具有轻质高强、高可靠性和稳定性,环氧碳纤维复合材料成为不可缺少的材料。
高性能环氧复合材料采用的增强材料主要是碳纤维(CF)以及CF和芳纶纤维(K-49)或高强玻璃纤维(S-GF)的混杂纤维。所用基体材料环氧树脂约占高性能复合材料树脂用量的90%左右。高性能复合材料成型工艺多采用单向预浸料干法铺层,热压罐固化成型。高性能环氧复合材料已广泛应用在各种飞机上。以美国为例,20世纪60年代就开始应用硼/环氧复合材料作飞机蒙皮、操作面等。由于硼纤维造价太贵,70年代转向碳/环氧复合材料,并得到快速发展。大致可分为三个阶段。第一阶段应用于受力不大的构件,如各类操纵面、舵面、扰流片、副翼、口盖、阻力板、起落架舱门、发动机罩等次结构上。第二阶段应用于承力大的结构件上,如安定面、全动平尾和主受力结构机翼等。第三阶段应用于复杂受力结构,如机身、中央翼盒等。一般可减重20%~30%。目前军机上复合材料用量已达结构重量的25%左右,占到机体表面积的80%。高性能环氧复合材料在国外军机和民机上的应用实例较多。
我国于1978年首次将碳-玻/环氧复合材料用于强-5型飞机的进气道侧壁。据有关会专家介绍,20世纪80年代在多种军机上成功地将C/EP用作垂直安定面、舵面、全动平尾和机翼受力盒段壁板等主结构件。
宇航工业中除烧蚀复合材料外,高性能复合材料应用也很广泛。如三叉戟导弹仪器舱锥体采用C/EP后减重25%~30%,省工50%左右。还用作仪器支架及三叉戟导弹上的陀螺支架、弹射筒支承环,弹射滚柱支架、惯性装置内支架和电池支架等55个辅助结构件。由于减重,使射程增加342km。德尔塔火箭的保护罩和级间段亦由C/EP制造。美国卫星和飞行器上的天线、天线支架、太阳能电池框架和微波滤波器等均采用C/EP定型生产。国际通讯卫星V上采用C/EP制作天线支撑结构和大型空间结构。宇航器“空中旅行者”的高增益天线次反射器和蜂窝夹层结构的内外蒙皮采用了K-49/EP。航天飞机用Nomex蜂窝C/EP复合材料制成大舱门,C/EP尾舱结构壁板等。
4.1 国内外发展现状及趋势
航天高新技术对航天先进复合材料的要求越来越高,促使先进复合材料向几个方向发展:① 高性能化,包括原材料高性能化和制品高性能化。如用于航空航天产品的碳纤维由前几年普遍使用的T300已发展到T700、T800甚至T1000。而一般环氧树脂也逐步被韧性更好的、耐温更高的增韧环氧树脂、双马树脂和聚酰亚胺树脂等取代;对复合材料制品也提出了轻质、耐磨损、耐腐蚀、耐低温、耐高温、抗氧化等要求。② 低成本化,低成本生产技术包括原材料、复合工艺和质量控制等各个方面。③ 多功能化,航天先进复合材料正由单纯结构型逐步实现结构与功能一体化,即向多功能化的方向发展。
碳纤维增强复合材料(CFRP)是目前最先进的复合材料之一。它以其轻质高强、耐高温、抗腐蚀、热力学性能优良等特点,广泛用作结构材料及耐高温抗烧蚀材料,是其它纤维增强复合材料所无法比拟的。
4.2用于固体发动机壳体的树脂基体
环氧树脂由于力学、热学性能优异,电气性能优良,耐化学介质性、耐候性好及工艺性优良等优点,数十年来一直是固体火箭发动机复合材料树脂基体的主体,预计今后相当长时间内仍将如此。环氧树脂的缺点是耐冲击损伤能力差,耐热性较低(<170℃),在湿热环境下力学性能下降明显。这些年来环氧树脂的发展经历了刚性环氧→柔性环氧→刚性环氧的过程。但居主导地位的一直是刚性双酚A二缩水甘油醚型环氧树脂。如美国“三叉戟-1”、“三叉戟-2”导弹以及“飞马座”火箭采用的HBRF-55A配方就以E-PON826为主。多年来各国都在通过加入柔性单元改进环氧树脂的韧性,通过加入新型刚性链单元结构或使用芴型芳香胺固化剂来提高耐热性,并分别取得了预期的效果[7,8]。
4.3用于固体发动机喷管的耐热树脂基体
耐高温结构复合材料用的新型热固性树脂一般指芳杂环高聚物,如聚酰亚胺、聚苯砜等,它们的耐热性比改性环氧和多官能团环氧更高,其中聚酰亚胺是目前耐热性最好、已实现工业化生产的重要品种。聚酰亚胺中的双马来酰亚胺(BMI)既具有聚酰亚胺耐高温、耐湿热、耐辐射的特点,又有类似于环氧树脂较易加工的优点。但缺点是熔点高、溶解性差、脆性大,如HexcelF650是成熟的第二代BMI树脂。在非常潮湿的情况下,最高连续使用温度为204.4℃,采用HexcelF650基复合材料的导弹经喷气式战斗机超声速冲刺后,能承受比预料更严酷的热环境。如能应用于固体发动机壳体,对其综合性能的提高十分有利。目前的主要问题是BMI的固化温度(约300℃)和固化压强(约1.5MPa)均比较高,使缠绕型组合芯模和壳体内绝热层难以承受[6,9,10]。
氰酸酯树脂(CE)是二十世纪八十年代开发的一类新型树脂。主要用途有:高性能印刷电路板、高性能透波结构材料(如雷达罩)、航空航天用高韧性结构复合材料。最早应用于宇航领域的商品化氰酸酯基复合材料为美国Narmco公司的R-5254C,它是碳纤维增强的CE与其它树脂的混合物。随后,一些供应CE基复合材料预浸料的公司,在CE中加入玻璃化温度高于170℃的非晶态热塑性树脂如聚碳酸酯(PC)、聚砜(PS)、聚醚砜(PES)等,使CE保持优良耐湿热性能和介电性能的同时,冲击后压缩强度(CAI)值达到240~320MPa,其使用温度与改性后的PI、BMI相当。如Ciba-geigy生产的ArocyL-10和RTX366的熔融物粘度极小,只有0.1Pa·s,特别适用于纤维速浸法制预浸料,在SRM研制中有着广阔的应用前景。“YLA公司”使用XU71787-07试制成碳纤维增强预浸料,经质量评估认为可制作卫星天线[11~13]。
液晶聚合物是热塑性树脂中较为独特和优异的一类,目前主要有芳族均聚酯和共聚酯。它们是一种自增强材料,高分子主链是由刚性或半刚性链段和柔性链段通过分子裁剪设计而成,在熔融状态呈液晶态,在冷却过程中这种有序性保留,使材料获得优异的力学性能。典型牌号有美国的Vectra树脂,Ekond树脂等。液晶聚合物既可以单独成型(如美国在1990年研制了所有结构部件均由液晶聚合物制作的固体火箭发动机),也可以作为复合材料的树脂基体。通过注塑、模压、挤压成型、或制成带状、薄膜状材料缠绕成型发动机壳体[14,15]。
国内外喷管用树脂基防热材料的发展经历大致相同,从玻璃/酚醛、高硅氧/酚醛到碳/酚醛、碳/聚芳基乙炔,从单功能到多功能、低性能到高性能,树脂体系经历了从酚醛树脂、改性酚醛树脂到高性能树脂。目前对聚苯并咪唑、聚喹口恶啉、聚苯并唑、聚苯并噻唑、聚芳基乙炔等高性能树脂的应用研究已成为热点,是树脂基防热材料发展的方向。由于碳/酚醛复合材料具有生产周期短、制造成本低、性能适中等特点,是目前固体发动机喷管烧蚀防热材料中广泛使用的材料之一,主要用在如喷管扩张段一类受热流强度较低的部件上;又因其价格低廉,甚至在美国航天飞机助推器的喷管喉衬上也使用碳/酚醛材料。国外典型的碳/酚醛材料有FM5055、MX4957A等牌号,所用酚醛树脂多以Ba(OH)2、NH4OH等为催化剂合成。酚醛树酯虽耐烧蚀性优良,但重现性不好,烧蚀可预示性差[1,16]。
酚醛树脂典型的改性途径有共聚改性,包括引进氰基、硼元素、芳环有机硅,以及采用二苯醚甲醛树脂、芳烷基甲醛树脂改性等;如氰基酚醛树脂的热氧化稳定性明显提高,分解温度达440℃,1000℃下的产炭率达68%~70%。为了使酚醛树酯获得更高性能,我国广大科技工作者在酚醛树脂改性方面做了大量的研究工作,相继开发了硼酚醛、钼酚醛、高成碳酚醛等新型酚醛树脂。
聚芳基乙炔(PAA)是一种最有可能取代酚醛树脂作为烧蚀防热材料基体的树脂。它是一种仅含碳元素和氢元素的高度交联的芳族亚苯基聚合物,由二乙炔基苯和苯乙炔聚合而成。理论成炭率高达90%;聚合时无低分子副产物逸出;树脂吸水率极低,仅为0.1%~0.2%,远远低于酚醛树脂的5%~10%。
PAA最主要的优点是玻璃化温度极高,烧蚀重现性好,高温力学性能保持率高。美国宇航公司用T300和PAA制作的复合材料试件。室温下层间拉伸强度为5.3MPa,400℃时降为1.4MPa;标准碳/酚醛(FM5055)制作的室温层间拉伸强度仅为4.2MPa;260e时已下降到0.3MPa[1]。我国华东理工大学已能制备出应用于航天领域的耐烧蚀PAA树脂,树脂成碳率达85%。航天四院43所进行了聚芳基乙炔树脂成碳率、复合工艺性能、力学性能等方面的探索性研究,试验表明,碳/聚芳基乙炔复合材料成碳率、耐烧蚀性能远远优于迄今已应用的碳/酚醛复合材料。目前存在的主要问题是PAA的多苯环结构所引起基体性脆以及PAA与碳布浸润性差带来的复合材料层间力学性能不佳。
碳纤维复合材料因其较高的比强度、比模量在国外先进战略、战术固体火箭发动机方面应用较多,新型陆基机动固体洲际导弹一、二、三级发动机壳体、新一代中程地地战术导弹发动机壳体。如美国“侏儒”小型地对地洲际弹道导弹三级发动机燃烧室壳体由IM-7碳纤维/HBRF-55A环氧树脂缠绕制作,壳体容器特性系数PV/W≥39KM;三叉戟(D5)第一、二级固体发动机壳体采用碳/环氧制作,其性能较凯芙拉/环氧提高30%[17~20];“爱国者”导弹及其改进型,其发动机壳体开始采用D6AC钢,到/PAC-30导弹发动机上已经采用了T800纤维/环氧复合材料;此外,由美国陆军负责开发的一种新型超高速导弹系统中的小型动能导弹(CKEM),其壳体采用了T1000碳纤维/环氧复合材料,使发动机的质量比达到0.82。美国的战略导弹“侏儒”三级发动机壳体,“三叉戟”一、二、三级发动机壳体的复合材料裙,民兵系列发动机的喷管扩张段,部分固体发动机及高速战术导弹如美国的THAAD、ERINT等。从二十世纪六十年代末开始,航天领域中以S玻纤和Kevlar-49纤维复合的金属内衬轻质压力容器逐渐取代传统的全金属压力容器。美国在1975年开始了轻质复合材料气瓶及储箱研制,采用S-玻纤/环氧、Kevlar/环BADCy/E-51/线性酚醛树脂氧缠绕复合材料。随着碳纤维性能提高及成本大幅度下降,碳纤维与低成本铝内衬制造技术相结合,使得费用低、质量轻、性能高、可靠性好的高压容器的生产成为现实。表2是美国SCI(Structural Composites Industries)生产的两种金属内衬碳纤维缠绕压力容器材料及性能比较情况。由表2看出,目前空间用复合材料基体主要采用环氧树脂。
此外,国外以复合材料取代金属制造空间飞行器(卫星、空间站、航天飞机等)构件目前已取得一定程度的应用。表3是国外复合材料在空间飞行器上的一些应用情况[18~20]。
由于碳纤维的密度、耐热性、刚性等方面的优势,增强纤维以碳纤维为主。碳纤维复合材料在空间技术上的应用,国内也有成功范例,如我国的第一颗实用通信卫星应用了碳纤维/环氧复合材料抛物面天线系统;第一颗太阳同步轨道“风云一号”气象卫星采用了多折迭式碳纤维复合材料刚性太阳电池阵结构等。
随着航空航天工业的迅速发展,对材料的要求也日益苛刻,一个国家新材料的研制与应用水平,在很大程度上体现了一个国家的国防和科研水平,因此许多国家都把新材料的研制与应用放在科研工作的重要地位。
4.4火箭发动机壳体用韧性环氧树脂基体
为了适应航空航天领域日益苛刻的要求,通用环氧树脂已不能满足要求,世界各国都在致力于开发各种高性能环氧树脂,以便于开发同高性能增强材料(如芳纶、碳纤维等)相匹配的树脂体系。
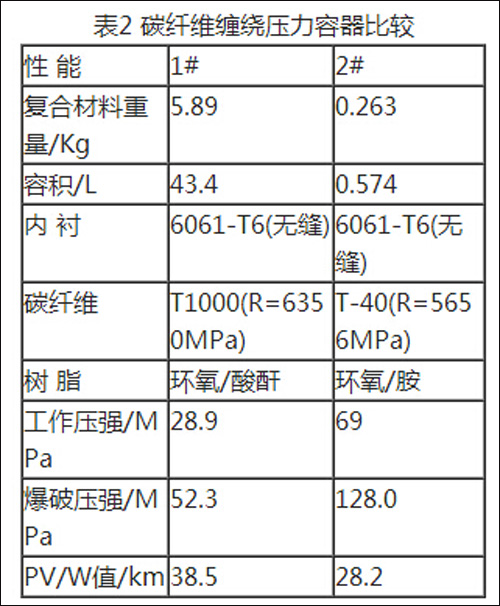
但总结起来,大都是在保证环氧树脂优异的工艺性的前提下,实现环氧树脂的多官能化,以改善其固化物的耐热性和粘接性。
比较常用的有4,4‘-二氨基二苯甲烷四缩水甘油胺(TGDDM),鉴于性能价格比,它可能是最实用的高性能环氧树脂。它具有优良的耐热性,长时高温性能和机械强度保持率,固化收缩低,化学和辐射稳定性好,还可用于高性能结构胶粘剂,结构层压板和耐高能辐射材料,国内外有许多学者从事TGDDM环氧体系的研究与开发工作,并取得了较大成绩。
特别值得指出的是,我国科技工作者经多年研究,开发了商品名为TDE-85的三官能团环氧树脂,其化学名为4,5-环氧己烷-1,2-二甲酸二缩水甘油酯,其分子中含有两个反应活性高的缩水甘油酯基和一个反应活性与前者差别很大的脂环环氧基。该树脂是一种工艺性、耐热性均很优异的高性能环氧树脂,西北工业大学、哈尔滨玻璃钢研究所等单位用TDE-85环氧树脂为基体材料制作的复合材料,应用在某些有特殊需要的产品上已获得令人满意的结果。
以碳纤维为增强剂的先进树脂基复合材料是航空航天工业中最重要材料之一。飞行器减重仍然是今后面临的关键问题。此外,对包括飞行器在内的许多国防装备的隐身也是需要解决的另一关键问题。因此,对先进复合材料,不仅要求其具有高的比强度、比模量和韧性,而且要求具有隐身性能,即兼有结构及功能性能。发展先进复合材料关键之一是开发综合性能优异的树脂基体。目前研究树脂基体主要目标是:
a. 高韧性的树脂基体,如复合材料的冲击后压缩强度(CAl)>300 MPa的树脂基体。
b. 具有高透波率的树脂基体,其tan&约0.3X 10-2。
c. 吸收雷达波的树脂基体。
d. 耐热300℃以上的树脂基体。
e. 适用于RTM等新型工艺的树脂基体。
其中,a、b、d和e已研制成功,但我国尚有一定差距。c仍为空白。研究和开发树脂基体的途径是以原有树脂改性为主,合成新品种并重。
环氧树脂由于性能优异,数十年来一直是火箭发动机壳体用复合材料树脂基体的主体,预计今后相当长时间内仍将如此.这些年来曾经历过刚性环氧-柔性环氧-刚性环氧的再认识过程,但居主导地位的一直是刚性双酚A二缩水甘油醚的环氧混合物。环氧树脂的固有缺点是耐冲击损伤能力差,耐热性能也较低(小于170℃),火箭发动机在高速下飞行,外表面必须良好绝热,以防御气动加热影响,这样则加大了发动机的惰性质量。多年来各国都在努力改进环氧树脂性能,例如提高韧性或耐热性,以不断提高发动机的性能。许多研究工作表明环氧树脂改进仍有很大潜力。
4.4.1橡胶类弹性体增韧环氧树脂
这一类最常用的是液体橡胶。橡胶改性剂(弹性体)通常带有活性端基(如羧基、羟基、氨基等)与环氧基反应形成嵌段。在树脂固化过程中,这些橡胶类弹性体嵌段一般能从基体中析出,在物理上形成两相结构,其断裂韧性GIC比未增韧的树脂有很大幅度的提高。研究表明,正确控制反应性橡胶与环氧树脂体系中的相分离过程是增韧能否成功的关键。
4.4.2热塑性工程塑料增韧环氧树脂
80年代又兴起用耐热性强韧性热塑性树脂来增韧环氧树脂。这些热塑性树脂本身具有良好的韧性,而且模量和耐热性较高,作为增韧剂加入到环氧树脂中同样能形成颗粒分散相,它们的加入使环氧树脂的韧性得到提高,而且不影响环氧固化物的模量和耐热性。但热塑性树脂的加入,往往导致体系的粘度增大,且增韧的效果在一定范围内随添加量增大而增大,这给这类树脂的工程应用带来了诸多难题,尤其是诸如火箭发动机壳体的缠绕成型工艺,但热塑性树脂还是一种很有前途的环氧增韧剂。
近年来发展了用耐热性高、力学性能良好的热塑性工程塑料来增韧热固性树脂,如聚醚砜、聚碳酸酯、聚醚醚酮和聚酰亚胺。从而在不降低体系的玻璃化温度、强度和硬度等优点的情况下改善高交联体系的韧性。八十年代初首次报道用Ultem1000a聚醚酰亚胺(PEI)改性环氧树脂的研究。李善君等合成了一系列与环氧树脂具有良好相容性的结构新颖的可溶性聚醚酰亚胺PEI。在Epon-828和TGDDM环氧树脂体系中取得了非常优异的增韧效果。材料断裂能提高5倍,模量和玻璃化温度维持不变[21,22]。以少量组分的聚醚酰亚胺PEI构成网状连续相而形成了“双连续”和“相反转”的相结构。因此控制体系的相结构成为制备高性能复合材料基体树脂和粘合剂的重要手段。在此基础上,深入开展了新颖聚醚酰亚胺对热固性树脂的增韧改性研究[23~27]。通过对聚合反应诱导相分离规律的研究和应用,研究固化反应和相分离速度的各种影响因素,了解相分离所遵循的动力学模型,控制分相条件,成功获得了高强度耐热性能优良的、能适用于航空航天工业的高性能基体树脂。
4.4.3热致性液晶聚合物增韧环氧树脂
液晶聚合物(LCP)中都含有大量的刚性介晶单元和一定量的柔性间隔段,其结构特点决定了它的优异性能。它在加工过程中受到剪切力作用具有形成纤维状结构的特性,因而能产生高度自增强作用。TLCP增韧环氧树脂的机理主要为裂纹钉锚作用机制。少量TLCP原纤存在可以阻止裂纹发展,提高了基体的韧性,而材料的耐热性及刚度则基本不损失。随着研究的进展,热致性液晶聚合物增韧环氧树脂作为一种新的技术,必将在工程应用中发挥重要的作用。
4.4.4改变交联网络的化学结构增韧环氧树脂
增韧的根本潜力在于提高基体的屈服形变能力。有关这方面的研究主要集中在,在保证基体达到一定的热变形温度下,尽可能多地在其分子结构中引入柔性段。具体地说,可以通过加第二组分或改变固化剂两种方法来实现。鉴于我们采用环氧树脂作纤维缠绕壳体用树脂主要是因为其良好的粘接性和优异的工艺性,故选用合适的增韧剂以改变体系的结构作为一种廉价、易行的方法,在工程中将有很广阔的应用前景。
4.5火箭发动机壳体用耐热增韧改性环氧树脂基体
4.5.1氰酸酯改性环氧树脂
氰酸酯改性环氧树脂是一种新型的高性能复合材料基体,同环氧树脂相比,具有优良的介电性能、耐湿热性能,同氰酸酯树脂相比,其性能/价格比更好,并在某些性能上超过氰酸酯树脂(如吸湿性和韧性),同时具有良好的加工性能。氰酸酯改性环氧树脂主要用作复合材料共聚预浸料和高性能复合基体材料。现在大多数商品化的氰酸酯树脂是氰酸酯/环氧树脂。以改性环氧树脂为树脂基体制备的复合材料具有良好的铺覆性和贮存稳定性,其复合材料板材具有优异的力学性能、耐热性和耐湿性[28]。氰酸酯改性环氧树脂能形成有工程实用价值的新型材料树脂基体,这类树脂基体主要用于飞机舱内材料/飞机发动机用管材、透平机用树脂基复合材料、摩擦材料和复合材料等,因此在电子元器件、电绝缘涂料、航空材料、纤维填充材料等方面有广阔的应用前景[29]。在国外,氰酸酯改性环氧树脂广泛应用于航天航空、电子电气、机电、机械等众多领域。我国在应用方面的研究报道并不多[30~37,38~44] ,且多集中在电路板研制领域。据报道[29]以氰酸酯改性的环氧树脂覆铜板,可有效提高覆铜板的电性能,其性能超过了FR-4标准环氧树脂覆铜,能够满足现代工业要求。
4.5.2双马来亚胺树脂改性环氧树脂复合材料
随着航空航天工业的发展,对复合材料的性能要求越来越高,高性能复合材料需要高性能树脂作基体树脂。通常高性能树脂基体具有特殊的化学结构和成型特性,在高温下具有高的尺寸稳定性、优异的热氧化稳定性、低吸湿性、耐磨性、耐辐射、优异的综合力学性能。
以高性能树脂为基体的复合材料能在高温氧化、腐蚀等恶劣环境下作为结构材料长期使用。以环氧树脂为基体的复合材料已不能满足高性能要求,聚酰亚胺树脂以其优异的耐热性和良好的力学性能、介电性能、耐湿热性、抗辐射性等特点作为环氧树脂的改性材料得到了广泛地关注[45]。
采用芳香族二胺和BMI树脂共改性环氧树脂在耐热性、力学性能、介电性能保相对稳定的同时,改善其工艺性和韧性。环氧、二胺、双马来酰亚胺与7628M玻璃布复合板的性能见表4。以二氨基二苯甲烷、双马来酰亚胺树脂共同改性的环氧树脂在常温下为棕色透明液体(溶剂为二甲基甲酰胺),在室温下存放时间长;以此树脂为基体制得的玻璃纤维布预浸料具有良好的储存稳定性;复合材料具有优异的力学性能、耐热性、耐湿热性能和介电性能,可广泛地应用于高性能结构材料领域。
BMI/DDM/EP/2MZ体系可使固化反应的温度降低,成型工艺性好,固化产物增韧效果明显,以其为基体制作的玻璃纤维复合材料具有优良的力学性能,在150℃的高温强度保留率达80%以上。
该复合材料是一种性能较好成本较低的耐高温复合材料可广泛用于国民经济各领域[46,47]。
针对环氧树脂(EP)耐湿热性差和韧性不足的缺点,用双马来酰亚胺(BMI)对常用的芳香族二元胺(DA)固化剂进行扩链改性,研究了改性4,4′-二氨基二苯砜(DDS)固化剂,对7种环氧树脂固化物的力学性能、热性能和工艺性能的影响,优化出一种BMI改性环氧树脂基体,改性树脂浇铸体韧性好,耐热性高:断裂韧性GIC 195J/m2;断裂延伸率3.37%;Tg218℃;135℃弯曲强度保持率72.2%;沸水饱和吸湿率3.3%;其碳纤维复合材料综合性能良好,断裂韧性高,耐湿热性好,横向拉伸强度75.5MPa,层间断裂韧性GIC267J/m2;135℃湿态弯曲强度保持率70.5%;132℃湿态层间剪切强度保持率49.5%[48]。
4.5.3用于基体树脂基复合材料的耐热增韧改性剂 — 烯丙基苯基化合物
二烯丙基双酚A (DABPA) 是烯丙基苯基化合物的一种,其最主要的用途是作环氧树脂等反应固化性树脂的耐热增韧改性剂。其结构如右式:自从1984年美国Ciba-Geigy公司推出其优秀品牌Xu292 ( Matrimid5292 ) [49]以来,因其性能和工艺颇佳引起国内外高度重视,成为耐热高韧性基体树脂研究热点。这个树脂体系的主要料就是DABPA通过与双马来酞亚胺(BMI)共聚,使质脆的BMI树脂的断裂韧性显著提高,使BMI型树脂基复合材料很快实现了实用化,其构件已在F-22等先进战斗机的主承力部位得到应用。我国的这类BMI型基体及其复合材料的研究,已达到较高水平并开始了实用化,为BMI和环氧等基体树脂的研制和生产提供优质的国产配套材料。
4.6巡航导弹、超声速巡航导弹、高超声速巡航导弹树脂基结构复合材料[50]
从2007年开始,树脂基结构复合材料在国内巡航导弹领域迎来了重大的发展契机,以下一代巡航导弹、超声速巡航导弹、高超声速巡航导弹为先锋的新型导弹武器研究工作全面启动,在耐高温、大射程、轻质化,树脂基结构复合材料在巡航导弹结构件上的发展突飞猛进,越来越多的结构部件复合材料化,复合材料应用比例的高低已成为衡量新一代巡航导弹先进水平的一个重要标尺。
树脂基复合材料在航天结构件上的应用主要有两大阵地:战略导弹和巡航导弹。一直以来,对战略导弹及运载火箭领域的树脂基复合材料开展的研究较多,但对以巡航导弹为代表的战术导弹却少有涉及。然而,巡航导弹却是未来航天领域树脂基复合材料大范围应用的最广阔舞台之一。新一代巡航导弹发展的趋势是:射程远、速度快、命中精度高、突防能力强等。这就要求导弹轻质化、高精度、高可靠、低目标特征、低成本等。这些需求带动了低成本结构复合材料、耐高温结构复合材料、结构/功能一体化复合材料的迅速发展。
在树脂基复合材料中,环氧树脂(EP)是巡航导弹弹体结构所用复合材料中最主要的基体材料,在所有树脂基复合材料结构中所占的比例高达90%。但随着飞行速度的提高,超声速巡航导弹研究的日益深入,目前树脂基复合材料的研究重点已由环氧树脂向双马来酰胺(BMI)、聚酰亚胺(PI)树脂、氰酸酯树脂转移。Bryte公司最近开发了一系列氰酸酯树脂基体,玻璃化转变温度达335℃,短时工作温度达300℃,可以代替BMI和聚酰亚胺,氰酸酯树脂已成为未来结构/功能一体化的有力候选材料,可以作为超声速巡航导弹复合材料舵面和弹体通常选用的树脂。
雷锡恩导弹系统公司试图在超声速巡航导弹研制中确定BMI作为选用的树脂。PMR型聚酰亚胺复合材料在国外的超声速巡航导弹的弹体结构上已经得到广泛应用,利用PI在400℃下良好的承载/透波能力,超声速巡航导弹的耐高温天线罩主要采用了PI作为基体材料,而在美国的“X-43高超声速飞行器”研究过程中,PI复合材料以优异的综合性能成为弹体主承力结构最有力的竞争者。而在树脂基结构复合材料的成型技术方面,国外的巡航导弹已普遍采用了先进的低成本制造技术,如树脂转移成型(RTM)、真空辅助树脂转移成形(VARTM)、树脂膜熔渍工艺(RFI)、纤维铺放技术和热固化工艺、共注射树脂转移(CIRTM)等技术。
4.7防弹结构复合材料[51,52]
由于东欧政治和经济的变革,以及越来越频繁的过境暴力犯罪,使得子弹和碎片防护结构的需求急剧上升。军事用途防御设备的开发,不能仅仅是部分应用于民用领域。树脂基复合材料在高性能设备方面具有越来越多的用途[82,83]。其中一个最重要的应用是,它们可为弹道冲击提供有效的保护。这种材料可以显著吸收子弹头的动能,且还具有高的比强度和比刚度。我们的研究目标是开发出能够吸收高冲击能,可用于防弹门和结构生产,或能加强在建及已使用结构的刚性复合材料板材。
Bay Zoltan 科学技术研究院的Gabriella Faur-Csukat研究了碳纤维、玻璃纤维(E-和S-型)、芳纶纤维、聚乙烯纤维织物增强不同环氧树脂复合材料的力学性能和弹道性能。用低速(却贝和落锤试验)和高速(两个不同口径弹道)冲击试验检验了手糊样品的性能。研究发现,复合材料的能力吸收容量受增强纤维性能、织物结构和树脂弹性的显著影响
4.8 先进战斗机用复合材料树脂基体[53]
在Narmco公司研制的双马来酰亚胺树脂系列中,以5250颇受重视。Rigidite 5250-2被美国YF-22战斗机(即F22原型机)所选用。525Q-4正式被F-22战斗机型号接纳。占F-22飞机结构23.5%的先进复合材料结构,包括几乎所有的外部蒙皮和某些框、梁和骨架,其基体材料是5250-4双马来酞亚胺树脂,并以5050-4/A S-4体系为主,对要求高抗损伤的少数部位则采用5250-4/IM-7体系。
Rigidite 5250-4是一种耐湿、抗冲击、耐高温的一种优质基体树脂,其刚性和湿热性能均优于5245C。与其他树脂体系一样,许多复合材料的力学性能、冲击韧性与成型固化条件有关。按F-22飞机结构复合材料件实际成型所采用的规范所测数据均为吸湿后状态,吸湿条件是在71℃水中浸泡2周,并于82℃下测定。
碳纤维复合材料系5250-4/IM-7层压板为由24层准备向同性取向铺迭而成,采用6.7kJ/m能量落锤冲击,随后压缩直至破坏,试样与试验按波音标准(BMS-276C)进行,固化条件为F-22复合材料结构件实际采用的固化规范,相对应的冲击压缩强度(CAl)值165MPa。5250-4纯树脂性能见表5。表5中树脂的固化条件是177℃/6 h和随后的227℃/12 h的后固化,从表中可见经上述规范处理的树脂其弹性模量高,刚性较好,热变型温度高、耐温性好。5250-4复合材料的高温性能非常突出。
5250-2碳纤维复合材料在湿态环境下仍有高的压缩强度,以相同纤维层数(24层),相同纤维取向(准各向同性),相近纤维体积分数(60%~62%)与5245C和5208(四官能团环氧)相比较,见图1。
4.9航天器用外热防护涂层材料
固体火箭发动机的外防护主要包括气动热蚀防护和发动机燃气防护两部分。气动热蚀防护主要以树脂基复合材料为主,如法国宇航公司为战略导弹研制的防热涂料,主要成分为硅树脂和中空二氧化硅颗粒,是一种导热系数0.1~0.15w/(m k),密度0.6g/m3的可喷涂涂层[54];俄罗斯研制的C-300导弹使用了牌号为ВЩ 027的防热涂层材料,大型“质子号”运载火箭使用了以氯磺化聚乙烯弹性体为基体,加入不同填料及轻质中空微球[55,56]的外热防护材料;美国的气动热蚀防护材料品种较多,广泛应用于航天飞机和导弹等航天产品,其基体材料主要为环氧树脂、氯磺化聚乙烯、酚醛、环氧-聚氨酯、聚硫-环氧和硅橡胶等,美国公司生产的供宇宙飞船及重返大气设备表面用耐烧蚀防热涂层,使用的基体是双组分室温硫化硅橡胶[57]。
4.10 飞机结构受力构件用的高性能环氧树脂复合材料
4.10.1 T-300/4211体系
它是北京航空材料研究所和北京航空工艺研究所1984年研制成功的。4211环氧基体由648酚醛环氧树脂和BF3·MEA组成。交联密度大,弹性模量较高,耐热性好,其突出优点是有良好的工艺性,预浸料可在室温下存放。缺点是脆性大,对湿热敏感。T-300/4211复合材料可在120℃以下使用。已用于几种型号飞机的垂直安定面,飞机进气道外侧壁板等。
4.10.2 T-300/5208体系,它是美国Narmco公司1972年研制成功的。5208基体由4,4’-二氨基二苯甲烷四缩水甘油胺环氧树脂(TGDDM)和4,4’-二氨基二苯砜(DDS)组成。该体系的性能好,能在177(下使用,因而美国绝大多数飞机复合材料结构件都采用碳纤维和5208或5208同系树脂体系制成。5208被称为第一代树脂基体。类似的体系还有美国Fiberite公司的934,美国Hercules公司的3501,(此二体系中加有BF3·MEA),我国北京航空材料研究所的5222,Hexcel公司的F263,日本东丽公司的3601,三菱公司的A401,东邦公司的1101等。所用的TGDDM树脂有:Ciba公司的MY-720,Reichhold公司的37-106,日本的Epiclon 430,Glyamine 120,YH-343,ELM-434及我国上海合成树脂研究所的AG-80等。
这些牌号的TGDDM树脂的平均相对分子质量和极性不完全相同,因此在性能上也有些差异。T300/5208复合材料耐热性及力学性能好,尤其是层剪性能优异。可在-55~177℃使用。预浸料的铺覆性好,使用期长。其缺点是吸水性大,在湿热条件下Tg、模量及压缩强度下降严重;韧性差,复合材料90。方向的延伸率小,层间剥离强度低,耐冲击性能差,尤其是冲击后压缩强度CAI(Compression after impact)低,对缺口敏感性大,不能满足飞机主受力结构件的要求。T-300/934复合材料是波音公司广泛用于民机上的环氧结构复合材料。
为了提高基体的韧性达到主受力结构复合材料的要求,主要从以下几方面进行改进。通过增加交联点间的距离来增加固化物的延伸性,开发出了一些新型高韧性环氧树脂和固化剂。但韧性的增加往往伴随着耐热性的降低。另一种方法是用橡胶增韧环氧树脂。能显著提高基体的韧性和CAI。但其耐热性、耐湿热性往往会下降。第三种方法是用热塑性耐热树脂来增韧环氧树脂。不仅能提高基体的韧性、复合材料层间性能和CAI,同时其耐热性不降低,甚至还有所增加。为了提高环氧树脂与热塑性树脂的界面性能,可选用末端为氨基的聚醚砜和聚醚酮以及末端为环氧基的聚醚砜等。被称为第二代树脂体系。如BASF/Narmco公司的Rigidite X5255-3的CAI高达345MPa;Toray-Hexcel公司的3900-2/T800H的CAI为368MPa;ICI-Fiberite公司的977-1/IMT的CAI为348MPa;我国北京航空材料研究院研制的热塑性树脂增韧环氧树脂复合材料T-300/5228和T800/5228的CAl分别为190MPa和250MPa,在湿热条件下的使用温度为130℃。
改进基体耐湿热性的途径是尽量减少基体中的极性基团(如羟基等)以及引入脂环和杂环结构。
4.10.3 T-300/LWR-1体系
它是北京航空工艺研究所和黑龙江石化所1989年研制成功的。LWR-1基体由E-54,DDS及促进剂组成,它可中温(120~130℃)固化。具有良好的耐湿热性能。可在80C以下使用。已用于前机身。
4.10.4 T-300/914C体系
它是目前欧洲空中客车飞机和海豚直升机等广泛使用的高性能环氧复合材料。914C是一种改性环氧树脂。T-300/914C预浸料由Ciba公司生产。T-300/914C复合材料的性能与T-300/5208复合材料相当。可在-50~180℃使用。
目前我国环氧树脂在微胶囊技术,带压粘接堵漏技术和单组分包装技术上已得到广泛的应用。一种钛材经磷酸盐氟化物处理后,涂布底胶待部分固化后,用FM一73(改性环氧胶)粘接,其剪切强度(-40℃)也可达到35.8MPa。这种环氧胶目前国外已广泛用于飞机、宇航飞船机体及表皮。美国第四代战斗机主体材料就是采用二氨基二苯砜(DDS)固化的二胺基二苯甲烷四官能环氧树脂(TGDDN)复合材料。另外,二异丙四缩水甘油胺环氧树脂(HPTl071)与芴型二缩水甘油醚环氧树脂也因具有较高热性能,而被视为21世纪飞机结构材料之一。美国F/A-14型战斗机的主体机翼结构系采用碳纤维-环氧树脂复合材料。我国上海MD-90双喷气客机推力装置短舱壁板等部件也是采用英国Westlant Gvond公司生产的碳纤维—环氧树脂复合材料。实践证明,采用热塑性树脂来改性环氧树脂可改进其韧性,提高复合材料的综合性能。一种采用纳米蒙脱土作为填料,通过插层复合的方法可制备出一种纳米蒙脱土/环氧树脂胶粘剂,其涂层综合性能要比纯环氧树脂胶粘剂性能好的多。这些领域已得到国内高度重视,并进入了开发或应用阶段。
4.11碳纤维增强树脂基复合材料在航空航天中的其它应用
复合材料正在迅速发展成为航天航空工业的基本结构材料。高性能聚合物基复合材料在航空航天工业的用量占其全部用量的80%。由于碳纤维具有高比强度、比模量、低热膨胀系数和高导热性等独特性能,因而由其增强的复合材料用作航空航天结构材料,减重效果十分显著,显示出无可比拟的巨大应用潜力。
4.11.1在航天飞机上的应用
碳纤维增强树脂基复合材料用做航天飞机舱门、机械臂和压力容器等。
4.11.2在火箭与导弹上的应用
在火箭和导弹上使用碳复合材料减重效果十分显著。因此,采用碳纤维复合材料将大大减轻火箭和导弹的惰性重量,既减轻发射重量又可节省发射费用或携带更重的弹头或增加有效射程和落点精度。
4.11.3在人造卫星上的应用
人造卫星展开式太阳能电池板多采用碳复合材料制作。
4.11.4在航空工业上的应用
随着碳纤维和基体树脂性能的不断提高,碳纤维增强树脂基复合材料的耐湿热性和断裂延伸率得到显著改善和提高。在飞机上的应用已由次承力结构材料发展到主承力结构材料,拓宽了在飞机工业中的应用。
4.11.5隐身材料
新型隐身材料对于飞机和导弹屏蔽或衰减雷达波或红外特征,提高自身生存和突防能力,具有至关重要的作用。在雷达波隐身材料方面,除涂层外,复合材料作为结构隐身材料正日益引起人们的关注,主要为碳纤维增强热固性树脂基复合材料(如C/EP、C/PI或C/BMI)和热塑性树脂基复合材料(如C/PEEK,C/PPS),目前已经得到了某些应用。
5民用大飞机复合材料
复合材料在航空制造业的应用趋于广泛,世界上大型飞机如波音787,空客380等机型的结构件复合材料的用量占到了40-50%,先进直升机结构件复合材料用量甚至占到了80%以上,可以说复合材料就是构成空中飞行器的“血肉”。
日本Yokohama橡胶公司[58]开发了一种用于空中客车A380的复合材料部件的环境友好的无粘接剂预浸料。该预浸料用于飞机机翼整流罩,由碳纤维增韧环氧树脂制成。A380的机翼构造为蜂窝状内层夹在纤维增韧塑料板材中间。该预浸料省去了需要使用环境友好,无味的溶剂融解预渍料以便模塑的工艺,应用时只须加热即可融解模塑,同样,只须加热即可固定蜂窝内层,无需粘接剂,这减少了整流罩安装的一个步骤,提高了生产效率。该公司也成为首家获得为空中客车供应这类材料许可的日本公司。
Nordam Group Inc[59]获得了波音公司的许可,为其供应787大型客机复合材料窗框。该窗框将采用HexcelCorp的HexMC-一种专门设计用于压缩模塑的高填充环氧片状模塑料,该材料具有高强度,低密度,结实,富于刚性的特点。该窗框与原先的铝质窗框相比,重量减轻了50%,具有高耐破坏性,这是首次将复合材料窗框用于商业大型客机,也是飞机机身构造的一次创新。首批产品巳交付波音公司机身合作制造商。
LH-10 Ellipse[60]是一种纵排双座运动型飞机,该飞机全部采用碳纤维/环氧树脂复合材料制成,目前已成套出售。其飞行速度可达到370km/h, 比其他同类飞机快100-150 km/h。其特色为在飞机后部装有带螺旋桨推进器的中型发动机和碳纤维主轴。
5国内大飞机复合材料
5 .1国内大飞机复合材料现状
当然与军机相比,民机还可以采用国际采购的方式来弥补技术上的差距,如飞机发动机、部分机载设备、零部件和材料都可以采用这种方式。但是民机制造中仍有许多东西是用钱买不来的,如飞机的总体设计能力,尤其是集成能力得靠经验上的累积。又如电传操作,这是核心技术,空客在这个方面已比较成熟,波音777也采用了电传操作技术,其中有些还是光传技术,这种技术人家是不会卖给我们的,只有靠自己研发。
据了解,现在国产化的T300飞机复合材料正在研制之中,可望不久能投入批量生产,以替代目前进口的T300。在复合材料的制造工艺上,国内的一些主要飞机厂也正在加快更新设备。如西飞,其应用飞机复合材料的主要设备热压罐原来的最大直径为3.5米,现在准备上直径六米的热压罐。国内航空产品制造业中少数能够依托自主研发, 引进、消化国际先进技术,实现产品国际取证和销售的生产企业。
哈飞股份与空中客车公司共同在组建合资制造中心, 生产A350XWB宽体飞机项目的复合材料零部件, 正式切入全球飞机制造产业链中.并向空中客车公司成功交付第一架份复合材料机体结构件, 此举不但标志着哈飞股份已成为空中客车公司合格供应商之一,重要的是,在中国自主研发制造的大飞机中,哈飞股份的复合材料必将得到更大规模的运用,公司的复合材料制造面临飞跃,从而使公司的发展空间更加广阔。
航空制造业战略机遇空前。飞机制造业是巨大的系统工程,是基础科学和制造业企业通力合作的结果,哈飞股份拥有除军机的军械加装和试飞以外的较完整的业务链.几十年生产军、民用直升机,轻型及支线固定翼飞机研制,参与国际航空的转包产品生产都为公司参与到大飞机项目中做好了一定的技术储备。除生产和销售直9系列, HC120,EC120机身,运12等产品外,另外3个长期投资单位涉及的方向则是民用支线飞机以及中型民航客机的研制生产, 其中安博威公司主要生产销售50座级涡扇ERJ145支线飞机, 该机型采用当代先进的涡轮风扇发动机和集成化航空电子设备, 其安全性,舒适性和各项性能指标不亚于大型干线飞机,目前该系列飞机全球销售量已超过700架, 2006年所签大单生产任务排到2010年。公司在原有的制造直升机和中型飞机(ERJ145支线飞机)所取得的技术储备和经验是使公司在参与到大飞机项目时更具优势。
5.2国产大飞机的软肋还是技术问题
技术问题一直是我国发展大型客机的最基本问题。近年来虽然有些关键技术获得了突破,但是大型客机的整机研制能力与世界先进水平相比仍是全方位的差距,尤其是波音、空客新的机型大规模采用复合材料后,大型客机的研制能力又一次与世界先进水平拉开了距离。
民机技术储备极少。由于历史的原因,我国民机在技术上投入非常少,民机的技术储备更少。原上航集团党委书记潘继武说,尤其是我国的民机在实践上停滞了很多年后,飞机设计的参数、定值积累极少,民机设计能力相对较弱,在技术上突破需要花费很多力量。
西安飞机工业(集团)有限责任公司(简称西飞)、第一飞机设计研究院、中国飞行试验设计研究院三家曾共同完成了一份资料,对本世纪初我国飞机的研制能力做出了一个详细的评估。这份资料称,我国飞机设计水平与国际水平相比差距约20年。在超音速巡航技术、喷管矢量技术、高推重比技术及无人驾驶控制技术等方面都有一定差距,综合设计能力也低,设计实践经验欠缺,设计规范落后。在飞机制造技术方面,与世界飞机制造加工基地相差10至20年,如数控效率只有波音的1/8。
5.3复合材料之惑
更让人焦虑的是,随着近年来复合材料在飞机上的大量应用,我国民机研制的能力有进一步与世界先进水平拉开的危险。
飞机上的复合材料主要是指碳纤维的复合材料。以前国际上的大型客机采用的材料都是以先进铝合金为主,飞机的设计、制造都建立在这种材料基础上。以波音777为例,其机体结构中,铝合金占到70%、钢11%、钛7%,复合材料仅占到11%,而且复合材料主要用于飞机辅件。但到波音787时,复合材料的使用出现了质的飞跃,不仅数量激增,而且开始用于飞机的主要受力件,现在波音787的复合材料用量已占到结构重量的50%。
飞机结构件大规模使用复合材料,是现代飞机制造史上的一次革命性变化。它使飞机重量更轻、强度更高、耐疲劳耐腐蚀性更好,而且复合材料中的高强度碳纤维进行大规模工业化生产后,可以使飞机的制造成本更低。同时在计算机技术、激光、C扫描等先进科技的支持下,复合材料制造飞机结构件的质量能够更加可靠地保证飞机的安全性。根据波音和空客公开的研究资料表明,到2020年它们的飞机将全部采用复合材料。
而我国目前仅掌握金属飞机的研制能力,复合材料只能少量地用在飞机辅件上,在主结构上的应用还需要进一步预研。这就好比是空客、波音已经能用钢筋水泥造房子,而我国仅掌握全套的用“秦砖汉瓦”造房子的办法,现在才开始学着使用钢筋水泥。更要命的是,用于飞机的复合材料我国现在还需要进口,尤其是像T800这样广泛应用的飞机复合材料我国还不会生产。
艰难的追赶
我国进行大型客机的研制,面临的技术困难是巨大的。在日趋激烈的航空市场上,没有技术领先、具有竞争力的飞机,即使生产出来了,也无法占据市场。在波音和空客用复合材料飞机替代金属飞机的大背景下,我国要研制大型客机,只有迎头赶上,生产出与之抗衡的飞机才行,这需要广大技术人员付出更多的努力。
目前国内的飞机专家都已认识到了这个问题,一批专家已提前进行飞机的预研。据中国航空工业第一集团公司科技委副主任冯培德透露,现在已有上亿元的经费投入到预研中,其中就包括材料。
“冰冻三尺,非一日之寒”,我国民机技术全方位地落后于欧美国家,是由于多方面的因素造成的,其中主要有三个:一是由于我国民机的型号研制频度太低,无法有效积累大量数据;二是由于民机生产至今还没有相关的研究所,民机直到现在还没有转向研究开发型;三是我国科技转化生产力水平较低,与欧美航空工业相比,我国航空企业还没有成为真正的科技转化生产力的主体,科技转化生产力体制机制的最佳模式还没形成。
6 结语
我国现在开始抓飞机复合材料的预研,当然有利于缩小与世界先进水平的差距。但是从长远来看,要从根本上解决我国民机技术上的差距,还得从解决我国民机技术长期落后的三个原因做起,即要加大民机研制的频度、成立专门的民机研究所、建立科技转化生产力体制机制的航空工业最佳模式。
高性能树脂基体及其改性是我门树脂行业的责任和义务。努力做好这方面的研发和产业化才能使我们从一个生产消费大国变成真正的生产消费强国。
参考文献:
[1] 林德春;张德雄.;固体火箭发动机材料现状、前景和发展对策;航天四院建国五十周年科技论文集.1999
[2] 吴良义等,罗兰温晓蒙;热固性树脂基体复合材料的应用及其工业进展,,[J].热固性树脂,2008,23(增):22
[3] 张建艺;先进纤维及其复合材料在西部开发中的机遇;固体火箭发动机复合材料工艺,2000,2:59~63
[4] 赵稼祥;碳纤维复合材料在民用航空上的应用;[J] 高科技纤维与应用,2003,3:1~5
[5] 罗益锋;世界高科技纤维正形成三足鼎立之势(二);[J] 高科技纤维与应用,2003,2:1~6
[6] 丘哲明等编著;固体火箭发动机材料与工艺;[C] 宇航出版社,第一版.1995
[7] 徐璋编著;环氧树脂应用工艺学;[C] 43所研究生讲义.1995
[8] 邢雅清;郭杨;复合材料用高性能环氧树脂基体的新发展;[J] .纤维复合材料,1996,2:1~6
[9] 梁国正;顾媛娟;双马来酰亚胺树脂. [C] 化学工业出版社.北京:1997,3
[10] Satomi,Ohno;Moon-HwanLee;Kuen,YLin;et.al.;Thermal degradation of IM7/ BMI5260 composite materials:characterization by X-ray photoelectron spectroscopy.Materials Science and Engineering,2000, A293:88~94
[11] IHamerton,HHermanetal.Multivariate analysis of spectra of cyanate ester/bismaleimide blends and correlations with properties.Polymer,2002,43:3381~3386
[12] BLLee.Effects of moisture and hermal cyclingonin-planeshear properties of graphite fiber-
Rein-forced cyanate ester resin composites.CompositesPartA,1996,27A:1015~1022
[13] JohnM.Barton,LanHameton et al.;Mechanical properties of tough,high temperature carbon fiber composites from novel functionalized aryl cyanate ester polymers. Polymer, Vol37No201996,37(20):4519~4528
[14] TracyR Reed ;Development and testing of liquid crystal polymer solid rocket motors, ADA304707MF,363
[15] JamesS,B;Chewand,John Rusek;Solid rocket propulsion applicationsFor advanced polymers,ADA304707MF,103~110
[16] 霍肖旭;曾晓梅;炭纤维复合材料在固体火箭上的应用. [J] 固体火箭发动机复合材料工艺;2000,1:55~61
[17] 沃西源;先进复合材料将成为卫星结构的主要材料,
[18] 金烽;国际空间站桁架结构和材料;
[19] 赵稼祥;碳纤维在美国国防军工上的应用;[J] .高科技纤维与应用,2003,1:6~9
[20] 谢佐慰等;复合材料在战略导弹和运载火箭结构上的应用情况简介;
[21] 刘润山;双马来酰亚胺增韧及用作先进复合材料基体的发展,;[J] .复合材学报,1990,7(4):79~84
[22].Li S.J. et al, San Diego Abstra Pap,1994,207,26
[23].Cui J,Chen W J, Zhang Z.C.et al, [J] .Macromol Chem.Phys.,1997,198(6):1865
[24].Lingqing Peng;Shanjun Li;etal; [J] .Macromol.Chem.Phys.2000,201,699-704
[25].Xianguo Wu;Shanjun Li;etal; [J] . Macromol.Rapid Commun.2001,22,409-41
[26].Wenjun Gan; Shanjun Li;etal; [J] .Macromolecules,2003,36,7746-77
[27].Wenjun Gan;Shanjun Li;etal; [J] .Macromol.Rapid Commun.2003,24,952-956
[28] 秦华宇,吕玲,梁国正,等.环氧树脂改性氰酸酯复合材料的研究[J]纤维复合材料,1999(2):1
[29] 邢雅清,郭扬.复合材料用氰酸酯树脂基体的性能和应用[J]纤维复合材料,1996,13(3):6
[30] Martin M D, Ormaetxea M.Cure chemo-rheology of mixtures based on epoxy resins and ester cyanates [J] Eur Polym J,1999,35:57-68
[31] 陈平,程子霞,雷清泉,环氧树脂与氰酸酯的共固化反应的影响[J].高分子学报,2000(4):472-475
[32] 包建文,唐邦铭,陈祥宝. 环氧树脂与氰酸酯共聚反应研究[J]. 高分子学报,1999(2):151-155
[33] Shimp D A, Wentworth J H. Cyanate ester-cured epoxy resin structural composites [A].37<sup>th</sup> Int. Sampe Symposium [C].1992,293
[34] Pascault J P. Chemistry and technology of cyanate ester resins [M]. Glas-gow UK:Champman and Ha 11,1994 [35] 郭宝春,贾德民,李建中,等.湿热老化对氰酸树脂/酚醛环氧树脂共混物结构与性能的影响[J]复合材料学  
报,2002,19(3):6
[36] 陈平,程子霞,朱兴松,等.环氧树脂与氰酸酯的共固化产物性能的研究[J]复合材料学报,2001,18(3):10
[37] 郭宝春,汪磊,贾德民,等.氰酸酯树脂/环氧共混物的化学和性能 [J].热固性树脂,2001,16(2):26
[38] 陈平,程子霞,朱岩松,等.低錼低tanFr-4印刷电路基板的研制[J]纤维复合材料,2001,(1):20
[39] 曾志安,陈立新,唐玉生.氰酸酯树脂在高性能印刷电路板中的应用概况[J]中国塑料,2003,17(5):19
[40] 潘玉良,项小宇,袁漪.高频线路板基板-三嗪覆铜板[J]热固性树脂,1998,(1):32
[41] 陈平,唐忠鹏,孙明.覆铜板用环氧树脂的改性研究进展[J]纤维复合材料,2003,20(3):6
[42] 包建文;氰酸酯树脂改性环氧及马来酰亚胺树脂的进展[J]航空制造工程,1997,(7):3
[43] 秦华宇,吕玲,梁国正;环氧树脂改性氰酸酯树脂的研究[J]机械科学与技术,2000,19(1):139
[44] 赵磊,孟季茹,梁国正,等;改性氰酸酯树脂的研究进展.玻璃钢/复合材料,2000,(5):38
[45].甘文君,余英丰,李善君,热塑性PEI改性TGDDM环氧树脂的相分离研究,[J] .工程塑料应用,2003,31(1):5-8
[46] 王汝敏;陈立新;张宏伟;双马来酰亚胺改性芳香胺固化环氧树脂的研究;[J] .中 国 塑 料;2000,19(6):30-34
[47] LeeS;MechanicalTesting of Toughened Resin Composite Materials [J]. Composites;1988;19(4):300~310.
[48] 梁国正,顾媛娟等.双马来酰亚胺树脂的应用概况.热固性树脂 [J],1995,2
[49] Ghaudhan M, Galvin T, King J. Characterization of bismaleimide system, Xu292 [J] SAMPE J,1985,21(4):17~21
[50] 许亚洪巡航导弹树脂基结构复合材料的应用与发展,[J].热固性树脂,2008,23(增):36
[51] T.Czigany;[J] JMater,Sci.Forum ,2005,59-66:5609
[52] T.Czigany,K.Poloskei,J.Karger-Kocsis,[J].J of Mat.Sci.2005,40:5609
[53] 赵渠森,先进战斗机用复合材料树脂基体,[J] 高科技纤稚与应用,2000,25 (2):1-7
[54] Luchmann W A. Aerothermal ablative characterization of selected insulator candidates [R]. AIAA 93-1857.
[55] Chow L External insulation for tactical missile solid rocket motor propulsion systems[R]. AIAA 89-2425
[56] 胡连成.前苏联轻质防热材料和碳/酚醛-复合材料 [J].宇航材料下艺,1992 ,(3): 56
[57] 居滋善.涂料工艺 [Ml.北京:化学工业出版社‘1994
[58] Solvent-free epoxy prepreg for aeroplane fairings [J].Advanced Composites Bulletin,2006(11):1
[59] Airliner window frames pass inspection[J].Advanced Composites Bulletin,2007(4):12
[60] Two-seat sport aircraft designed in carbon/epoxy composite [J].Composites,2007(34):54. <!-- Baidu Button BEGIN -->
免责声明:本网站所转载的文字、图片与视频资料版权归原创作者所有,如果涉及侵权,请第一时间联系本网删除。