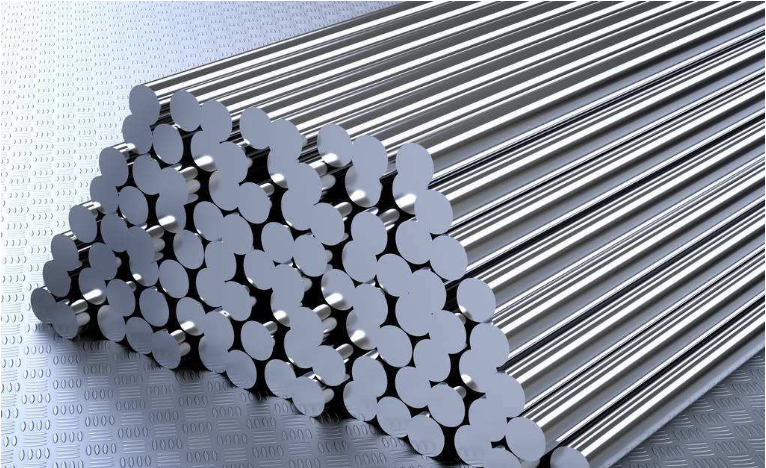
洁净钢是指钢中五大杂质元素(S、P、H、N、O)含量较低,并且对钢中非金属夹杂物进行严格控制的钢种。早期洁净钢生产对钢材性能和洁净度要求不高,转炉成为生产洁净钢的主要工艺。当时的洁净钢技术研发重点是解决顶吹转炉反应效率低、渣钢反应偏离平衡和吹炼过程不平稳等技术问题。研发的一些主要技术包括:氧气底吹转炉和喷粉技术,各种复吹转炉以及铁水脱硫和炉外精炼等。
20世纪70年代以后,由于制造业的快速发展,对钢材洁净度要求更加苛刻,如无间隙原子深冲钢要求[C+N]≤50ppm、轴承钢要求T.O≤6ppm等,单纯依赖转炉很难达到质量要求。这一时期的研发重点是针对转炉功能的解析与转换,形成洁净钢生产流程,突破洁净钢冶炼的技术极限。主要研发的技术包括:铁水“三脱”(脱硫、脱硅、脱磷)预处理、转炉智能吹炼、多功能真空精炼等。
自2000年以来,洁净钢生产工艺的研究热点从单纯追求突破洁净度极限,转变为降低生产成本、提高生产效率、实现绿色化生产。主要研发成果包括:钢中最大夹杂物控制、连铸轻压下和小压缩比连铸,及建立高效低成本洁净钢生产平台等。
1 高效铁水“三脱”技术
脱磷、脱硫是钢水提纯中最重要的冶金反应。和转炉相比,铁水“三脱”(脱硫、脱硅、脱磷)工艺的主要特点是将脱磷、脱硫反应从高温、高氧位转移到低温、低氧位条件下实施,更有利于反应的发生,进而解决了传统炼钢中回硫、低碳脱磷和钢渣过氧化等弊病。
为了开发更经济、更高效的“三脱”工艺,有专家推荐以下技术:一是根据耦合反应理论,设计在同一反应器内分阶段进行脱硅、脱磷和脱硫。二是加强熔池搅拌,开发低FeO渣脱磷工艺(控制渣中TFe≤5%,R=2-2.5),提高脱磷效率达80%以上,半钢[P]≤0.02%。三是喷粉解决熔池法造渣困难问题,高Ca/O比操作,形成高碱度、低FeO渣深脱硫,使脱硫率≥90%。四是通过灵活调节Ca/O比,精确控制“三脱”反应过程中的氧化还原程度。五是吹炼期采用溢渣工艺,及时排出各反应期生成的炉渣,并实现在线炉渣改质。
2 提高夹杂物控制水平的措施
近年来,业界对夹杂物控制提出更高的要求,在降低夹杂物总量的基础上,要求严格控制夹杂物最大尺寸,大幅提高钢材的各项性能。
为实现这一目标,应采取以下技术措施:一是用真空碳脱氧代替合金沉淀脱氧,减少脱氧夹杂物;二是抑制或减少精炼中渣钢反应,避免生成大颗粒变性、卷渣和脱硫夹杂物;三是加强钢水保护,避免浇铸中钢水的二次氧化,从而产生新的夹杂物。
改变脱氧工艺的技术关键是提高真空循环脱气(RH)界面反应速度,促使真空下,碳氧反应接近气相平衡。具体措施如下:一是扩大真空室表面积;二是真空室吹氩气,加快钢液表面的更新速度,增大界面流量;三是采用微气泡技术(PERM法),在RH精炼前,吹入H2或N2,提高钢中气体含量,利用真空脱气功能,在后期形成大量微气泡,促进熔池脱碳并有利于夹杂物上浮。
中间包冶金对钢中夹杂物控制有重要作用,其目标不是进一步提纯钢水,而是严格控制浇铸过程的污染,避免产生二次氧化、卷渣和变性夹杂。具体措施包括:采用大容量中间包,合理设计中间包形状,避免钢水形成紊流;加强中间包密封,控制中间包气氛中的氧含量PO2≤0.1mol%;采用镇静开浇工艺,可使铸坯表层夹杂物富集带中夹杂物面积率从镇静5min开浇的1%下降到镇静10min开浇的0.2%;采用无渣浇铸工艺,如日本山阳特钢厂生产超纯净轴承钢,采用无渣浇铸工艺,可控制钢中最大夹杂物尺寸≤12μm。
3 建立高效的洁净钢生产体系
以日本住友钢厂1座210t脱磷炉和2座脱碳炉配合2台KR脱硫站、2台RH精炼炉和3台连铸机,构建的高效快节奏生产平台为例,其高效快节奏的洁净钢生产特点如下:
一是全部产品高品质化。采用100%铁水“三脱”、100%快节奏生产、100%钢水真空处理和100%铸坯热装直轧(≥850℃),全部产品杂质总量Σ[S+P+T.O+N+H]≤100ppm。
二是压缩辅助时间,缩短冶炼周期。通常转炉辅助时间与吹炼时间之比为1∶1,而双联转炉吹炼时间≤10min,要求压缩辅助时间≤10min,保证20min周期。加快生产节奏,解决了脱碳炉热量不足的问题,日产45炉钢时,冷却能与传统转炉相当,日产55炉钢时,冷却能提高7.2%。
三是建立以转炉为中心的快节奏生产体系。生产周期长于转炉的KR和RH,采用2台设备配1台转炉;3台连铸机同时生产时,连铸周期为1h,2台连铸机同时生产时,连铸周期为40min。
四是缩短铁水罐周转时间,提高周转次数,铁水入炉温度提高46℃。
五是简化炉外精炼,提高钢包周转率,出钢温度比传统转炉降低30℃,不配置LF炉。
建立高效快节奏的生产方式具有很大的经济效益:一是提高设备作业率,减少设备台数,降低管理成本;二是缩短辅助时间,加快钢包(铁包)周转,减少辅助能耗和在线钢包数量;三是大幅度提高劳动生产率,降低人员成本。
4建立绿色低成本洁净钢生产平台
传统流程以炉外精炼控制钢材纯净度,以铁水“三脱”为基础的洁净钢生产新流程,可以通过以下途径,降低生产成本:
一是提高反应效率。该流程通过提高渣钢间磷、硫分配比,抑制钢渣过氧化,减少脱氧夹杂物以及提高锰资源回收率等措施,降低渣量,减少辅料、钢铁料和铁合金消耗,降低生产成本。
二是实行高效快节奏生产。该流程通过加快生产节奏,提高设备作业率,降低辅助时间能耗和铁水、钢水周转过程温降等措施,降低生产能耗;通过减少设备台数简化备件管理,提高全员劳动生产率,进一步降低生产成本。
三是简化炉外精炼工序。国内钢厂普遍采用LF精炼。LF工序能耗高、周期长,渣钢反应易产生大颗粒夹杂物,国外先进钢厂已开始抑制LF渣钢反应甚至取消LF精炼炉。
四是颠覆传统流程。高品质特钢须采用电渣(ESR)或真空感应+真空自耗(VAR)等特种冶金和锻造工艺生产,规模小、成本高。这种状况已开始改变,如SKF公司通过超低硫冶炼和硫化物控制,使轧材横、纵向性能偏差从50%降低到10%以下,实现以轧代锻生产风电轴等产品。日本山阳特殊钢公司通过改善夹杂物控制工艺,完全消除20μm以上的大型夹杂物,使轴承钢的疲劳寿命≥108,生产的航空轴承质量已超过采用ESR或VAR工艺生产的产品。
更多关于材料方面、材料腐蚀控制、材料科普等方面的国内外最新动态,我们网站会不断更新。希望大家一直关注国家材料腐蚀与防护科学数据中心http://www.ecorr.org