2014年,央视315曝光的某款汽车边梁腐蚀穿孔问题已成为人们日益关注的重点问题之一。目前,汽车制造所用的材料以金属为主,在使用过程中受到自然界湿热环境的影响,如工业污染、太阳幅射、道路石击、沿海城市海洋性气候及北方地区冬季道路防滑盐等,加速了对汽车的腐蚀。汽车的腐蚀问题,将严重影响汽车的外观、车身结构强度、使用寿命以及安全性能。本文主要从环境、材料、工艺、车身结构方面分析汽车腐蚀的原因及其影响要素,提出了防止汽车腐蚀的建议方案。
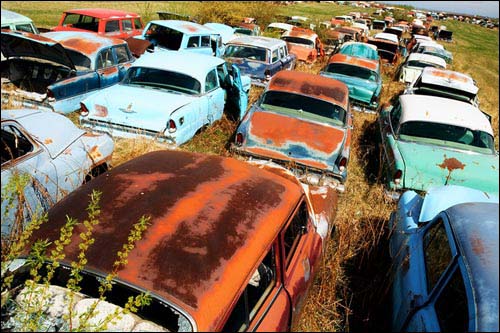
1、影响汽车腐蚀的因素
主要有:大气环境,材料型号,制造工艺,结构设计,等几方面。
1.1大气环境对汽车腐蚀的影响
大气环境主要有农村大气、海洋大气、城郊大气和工业大气。这些大气中都含有腐蚀金属的杂质。汽车在含不同有害杂质的大气环境中运行,对汽车的腐蚀程度也不一样。
1.2气象因素对汽车腐蚀的影响
1)相对湿度的影响:钢板处在温度0℃以上,湿度80%以上的时间越长,腐蚀越严重。
2)温度的影响:年平均气温较高的地区,腐蚀速度较快,昼夜气温变化,加之不同介质散热不一样会在金属表面产生结露,加速汽车的腐蚀。
3)降雨的影响:雨水沾湿金属表面,冲刷破坏腐蚀产物保护层,促进腐蚀。
4)酸雨的影响:石油、煤燃烧时产生的SO2等气体,SO2气体被氧化成SO3形成酸雨,造成金属表面的腐蚀。
5)氯化物的影响:氯化物的影响随地区而异,离海岸较近的地方,大气中氯化物的含量较大。一般在离海岸线几公里以内,氯化物对汽车腐蚀非常严重。
1.3道路环境对汽车腐蚀的影响
1)泥沙和碎石飞溅:飞溅的泥沙、碎石会划破漆膜,造成车身腐蚀;
2)路面积水:由于车轮旋转而飞溅到汽车各处,使其表面形成含酸碱性泥沙的水膜,同时维持潮湿状态,造成车身不同程度的腐蚀;
3)道路撒盐:地处寒带的道路为了保证冬季的行车安全常在道路上人工撒盐,汽车在这样的道路上行驶,其底盘件很容易被腐蚀。
1.4材料对汽车腐蚀的影响
1)钢板材料的影响
近20多年,汽车使用钢铁材料虽然占绝大多数,但镀锌层钢板、铝合金、塑料等材料的应用在不断增加。欧美的汽车公司一般采用镀锌层钢板、镀锡铁合金及超高强度热成型钢板制造,全铝、全塑轿车已在某些车型上采用,内涂膜板等耐腐蚀金属板材料解决穿孔腐蚀问题。由于合金化热镀锌板成本和质量的优越性,日本汽车界从2005年起汽车用板全部用合金化热镀锌板,取代现有的电镀锌合金板。
为了防止汽车车身钢板的腐蚀,20世纪70年代开始采用镀锌薄钢板,德国首次推出全热镀锌薄钢板车身,即,轿车内腔全部采用热镀锌钢板制作,外覆件选用电镀锌钢板制成。大部分镀锌层是热浸锌、电镀锌、电镀锌镍或锌铁合金及热浸锌铁合金。纯镀锌层厚度从7μm到10μm,电镀锌镍合金层从2μm到5μm。除使用预涂材料外,在底部空腔、缝隙使用防护蜡也会提高耐腐蚀等级。此后,镀锌薄钢板的增长率不断上升。
目前,我国很多车身采用冷轧钢板,采用镀锌层钢板制造的车身相对较少。汽车生产企业要降低生产成本,采用部分冷轧板代替耐腐蚀板。冷轧钢板的防腐蚀性能不如镀锌钢板,可通过优化车身空腔结构和提高电泳漆泳透率等方法来解决车身腐蚀的问题。通常汽车生产企业会在平衡成本和质量的前提下,对不同级别车型的选材有差异。(见表1)
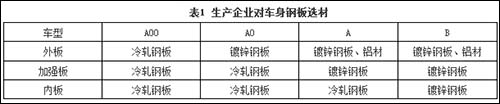
2)油漆材料的影响
随着汽车制造业的不断发展,汽车涂装材料不断朝着高品质、低能耗、低污染和低涂装成本方向发展。
涂装除了装饰作用外,另一主要作用是防腐蚀,因此涂装材料防腐性能对汽车腐蚀至关重要。汽车涂料中电泳漆对整车防腐性能起到关键性作用,因此针对不同厚度的电泳做中性盐雾试验,以验证其影响;实验结果显示电泳膜厚较厚的试验结果较好。(见表2)

现如今车身外涂层耐腐蚀性、耐候性已赶上国际同类产品水平,即外观耐候性使用3年仍完好如新。但10年或30万公里不产生穿孔和影响结构强度的腐蚀将是下一目标,应使用高锐边防腐、高耐候性、膜厚中/厚可调、高泳透率电泳漆,有效提高车身腔体漆膜厚度,降低车身表面漆膜厚度。
3)抗石击胶与密封胶的影响
由于车身底部、车身侧裙部位和轮罩内表面经常处于雨水冲刷和砂石撞击的恶劣环境中,因此底部的钢板结构件对涂装的防腐性能要求较高。生产厂家一般对以上部位喷涂丙烯酸改性沥青抗石击涂料或橡胶改性弹性防腐胶,此类材料采用高压喷涂,具有防水、耐腐蚀、耐冲击、防震、附着力强的优点。
对于舱内和舱外涂装为避免出现防腐盲区经常大量采用胶粘、密封工艺,对各处的缝隙、空腔结构进行打胶密封,隔绝腔内基体表面与腐蚀介质的接触,防止缝隙或夹层内出现进水和流锈水现象。
通常对薄板焊接结构处或车辆长期涉水处钣金缝在焊接前涂抹焊缝密封胶、点焊密封胶、折边胶、结构胶等填充材料。
4)防护蜡的影响
为了提高抗腐蚀,一般采用喷蜡或注蜡工艺防止车身空腔的腐蚀,欧洲部分高档车还采用灌蜡工艺。如果缝隙中没使用粘接剂的话,用防护蜡处理很必要,如车身底围的点焊缝,翼子板和车轮罩之间缝隙,在没有使用预涂材料的情况下,使用4年后其表面50%以上会严重腐蚀,使用防护蜡工艺后,情况要好很多。
经试验及权威机构试验表明:钢板材料和涂装材料对整车防腐起着关键性作用。如镀锌钢板和冷轧钢板防腐性能差异就非常明显,没有经过涂装材料保护和经过保护的防腐能力差距很大,因此选择合适的钢板材料和涂装材料是整车防腐控制中非常重要的环节。
1.5工艺对汽车腐蚀的影响
选择好的涂装材料和使用合理的涂装工艺都是保证车身防腐性能的重要因素;工艺水平的好坏以及施工性能的稳定直接影响了整车的防腐水平;目前有的厂家经过多年的研究和整理,从工艺设备和工艺技术路线上逐步调整,现已达到国际领先水平。如目前电泳采用Rodip-3电泳工艺,大大提高了内腔防腐能力;机器人喷涂PVC工艺及喷蜡技术的完善,也提高了车身的防腐能力。
1.6车身结构设计对汽车腐蚀的影响
合理的设计能够有效降低腐蚀,延长汽车的使用寿命,防腐在设计中常考虑以下因素:
1)温度循环设计,腐蚀的发生频率和程度与温度循环关系密切;
2)排水孔设计;
3)空气的排出效率设计;
4)缝隙与空气接触和对流的能力设计;
5)气流飞溅引起的泥土与道路盐的沉积;
6)不正确的搭接和缝隙处无法覆盖电泳涂层;
2、防止汽车腐蚀所采取的措施
2.1过程验证
根据以上影响因素分析,进行了数据调查和实车分析。
2.2实车解剖
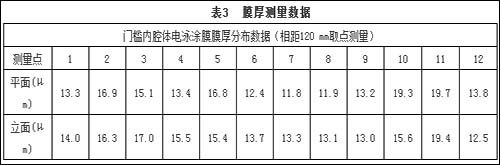
从表3解剖车身数据来看,在车身腔体结构较复杂的情况下,内腔电泳上膜情况良好(膜厚>11μm),涂膜厚度完全达到目前欧美中高档轿车车身腔体上膜要求。
2.3海南试验
环境对整车防腐影响因素中,道路环境中盐的影响因素最大;在沿海地区车身外部(车顶)的盐化累积是最高的。其次是气候条件对整车防腐影响,根据防腐蚀试验研究证明,高温高湿时(相对湿度98%、温度为50℃),这一环境条件对汽车腐蚀有明显的加速作用。另外行驶环境对整车防腐也有影响,其中城市或者工业区对金属的腐蚀影响较大。
目前,国内海南汽车试验场的环境可模拟汽车在最苛刻的环境下(高湿、高温、高盐份)的使用情况。其模拟过程是:让车辆负载其最大装载重量的60%,给整车喷盐雾15min,再以正常行驶速度经过碎石路、沙土路、盐水路、泥浆路、盐水搓板路、波形路、石块路、搓板路进行路试,然后进入中温高湿(温度为50℃±2℃、相对湿度为95%±3%)的环境中停放12h,验证整车防腐情况。下面选取了部分车辆在海南防腐验证的结果:
1)涂层应用基本一致,外覆盖件涂层性能良好;
2)油箱口盖膜厚不均匀,边缘轻微锈蚀;
3)车身内腔性能优良,除车身底部门槛接缝和流水部分有部分锈蚀外,其他性能良好;
通过试验验证,在车身设计和材料选择过程中,我们应该做到以下几方面:
1)封闭部分与滞留处设计,应尽量避免封闭区,如避免不了就开孔,让封闭区的通风与排水良好。进口孔位置要能防止水汽与碎石的直接进入,排水孔应位于封闭区和滞留处的最低点。
2)零部件外形设计,结构设计上要尽量避免尖锐边缘,减少粗糙面。
3)减少空腔及点焊结构,设计上推广激光拼焊,使焊点缝隙减少到最低限度。
3、防止车身腐蚀的建议方案
1)选用7~10μm镀锌层的钢板;外覆盖件和腰线以下部位用镀锌钢板;
2)加油口盖、后视镜座及支架、左右翼子板等零部件在保证功能的前提下尽量选用非金属材料、铝合金或复合材料;
3)选用防腐性能良好的阴极电泳底漆,局部位置可选用抗石击涂料。
4)左右翼子板、前后轮罩、前后立柱内外板焊缝等焊接处使用密封胶能有效防止缝隙腐蚀;
5)底围缝隙表面、无法封闭的空腔、发动机舱和车门铰链处采用防锈腊进行处理。