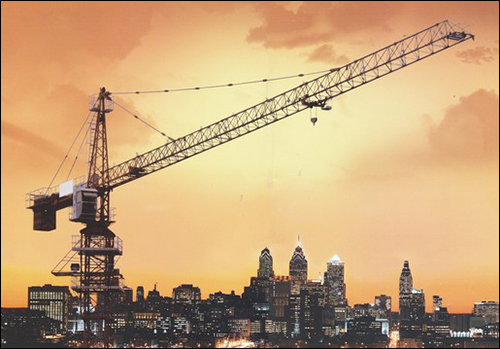
1、前言
中国塔机行业从无到有,从小到大,逐步形成了较为完整的生产体系,如今中国已经能生产100千牛米到52000千牛米的塔机,不但满足国内工程建设的需求,而且出口到世界各地,特别是小批量已经出口到欧美等发达国家和地区。近年来,随着我国大量基础设施建设及房地产行业的快速增长,塔机行业发展十分迅速,2010~2014年是中国塔机制造业增长最快的三年,三年中塔机制造企业从280多家猛增到近600多家,2013年产量达到5.53万台,就总产量而言,我国已成为世界民用塔机的生产大国,也是世界塔机主要需求市场之一。随着制造技术的发展以及客户对产品质量越来越高的要求,塔机涂装技术也在不断进步,越来越多的企业开始注重塔机产品表面质量和涂装环保技术,本文对此进行了研究与探讨。
2、国内塔机行业涂装现状
总体而言,与汽车、工程机械等行业进行对比,由于产品性价比相对较低,使用环境恶劣,塔机行业涂装技术水平仍相对落后,具体表现在以下几个方面:
(1)结构件前处理采用人工除锈:砂轮打磨或简单喷砂除锈,生产效率低下。仅少数企业采用自动抛丸除锈。
(2)底漆采用低档醇酸或中档丙烯酸底漆,面漆也为醇酸或丙烯酸漆;涂漆后晾干,无烘干工序,漆膜厚度<80μm,防腐装饰性能较差。只有少数企业采用高性能的环氧底漆+聚氨酯面漆,涂层厚度>80μm以上。
(3)部分小型企业涂装采用人工就地喷漆,工件喷漆采用空气喷涂,无专门的喷漆房或简易的干式喷漆室,涂料浪费严重,对周边环境污染较大。仅少数企业采用静电喷枪喷涂和采用带空调送风的湿式喷漆室。
(4)工件输送系统落后,工序间流转采用行车或电动平车输送,生产效率低下。仅少数企业采用自动输送线(积放链或自行葫芦)运送工件。
(5)缺少专业涂装工程师进行涂装质量标准体系管理,检测检验手段差。
3、塔机涂装工艺分析
3.1塔机企业规模及产品特点
国内塔机行业规模差别较大,不同企业之间所采用涂装工艺也存在较大差异。规模小的企业年产几百台,规模大的企业年产量达到几千台。塔机产品为桁架结构,产品相对规整,典型产品最大尺寸12000mm×3000mm×3000mm,标准节长度一般≤6000mm,最大工件重量一般≤12t,因此工件通常需要组合吊挂。
3.2塔机涂装工艺说明
(1)涂装前处理:塔机涂装前处理目前多采用喷、抛丸清理工艺,以去除工件表面氧化皮、锈蚀等污物,提高表面附着力,并去除工件表面焊接应力;喷丸处理效率较低,一般只适用于小批量生产。喷抛丸清理后的工件一般直接喷涂溶剂型涂料,但对喷粉工艺来说,则需要进行磷化处理,以提高粉末涂层的附着力,目前硅烷等新型环保前处理剂在塔机上应用正在验证中。
(2)涂装材料及涂层体系:塔机涂装材料目前以溶剂型涂料为主,因产品外观要求相对较低,多数企业采用二涂层体系,多采用低端的醇酸底漆、丙烯酸面漆组合,较少采用双组份环氧底漆、聚氨酯面漆涂料;粉末涂料则采用耐候性较好的聚酯粉末。
(3)喷涂和烘干方式:喷涂以空气喷涂或无气喷涂为主,静电喷涂应用不多。由于产品结构的特殊性,涂料利用率较低,笔者认为应推广粉末涂料的应用。涂料干燥以晾干或低温烘干为主,很多厂家从成本因素考虑以晾干为主,粉末涂料则需要高温固化,成本会适当加大。
(4)生产线输送方式:塔机涂装线输送在小批量时采用地面输送方式,中、大批量生产大多采用积放链输送。采用积放链输送时可利用积放链的积放功能,将输送线延伸到焊接车间和装配车间;由于工件形状复杂,喷涂工序是生产的瓶颈工序,可根据生产纲领分为多条线路并联或多条生产线,以更好地满足生产需求;另外,由于标准节占工件总的比例较高,可以采用拆分组合吊挂的方式来提高生产效率。
3.3塔机典型涂装工艺流程
喷漆涂装线:工件上线→自动抛丸→清理除尘→喷底漆→底漆流平→喷面漆→面漆流平→面漆烘干→冷却→工件下线。
喷粉涂装线:工件上线→自动抛丸→清理除尘→脱脂→水洗→表调→磷化→水洗→去离子水洗→吹水→水分烘干→冷却→粉末喷涂→高红外预热→粉末固化→冷却→工件下线。
国内主要塔机涂装生产线情况比较见表1。
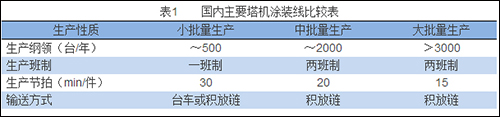
4、塔机涂装线中新技术的应用
4.1化学前处理技术应用
由于喷粉工艺需要,塔机结构件采用先进的脱脂水洗磷化等工序前处理工艺,脱脂液彻底去除工件表面油污,经过清水冲洗,增强后续磷化效果;工件经磷化液处理后,在工件表面沉积形成一层不溶于水的结晶型磷酸盐转化膜,从而提高涂层与工件基层附着力,增加产品的耐蚀性。设备各工序采用间歇式喷淋清洗,溶液循环使用;水洗采用逆流补水的方式,既保证清洗效果,又节约水源。
4.2粉末静电喷涂技术应用
采用粉末静电喷涂技术,通过静电吸附作用将粉末喷涂在工件表面,经过高温固化形成良好致密的表面涂层。实验表明粉末静电涂装与传统油漆喷涂相比,其防腐蚀能力可提升~60%。粉末还可以循环使用,不会造成浪费,涂装综合成本可降低~20%。粉末涂料与普通溶剂型涂料相比是一种新型的不含溶剂的100%固体粉末状涂料。具有不用溶剂、无污染、节省能源和资源、减轻劳动强度等特点。
(1)高效:由于是一次性成膜,立体感强,减少施工次数,可提高生产率30~40%;
(2)节能:静电喷涂效果好,节约资源,降低能耗约30%;
(3)污染少:无有机溶剂挥发,不含油漆涂料中甲苯、二甲苯等有害气体;
(4)涂料利用率高:可达95%以上,且粉末回收后可多次利用;
(5)涂膜性能好:采用户外型聚酯粉末,成膜厚度可达50~300μm,其附着力、耐蚀性等综合指标都比油漆工艺好。
(6)成品率高:在未固化前,可根据需要进行二次喷涂。
4.3智能化重型积放链输送系统[2]
采用空中积放式重型输送链自动化输送,融合了机械、电气、信息等多功能PLC程序控制管理,实现了机电一体化,多工位上下件、工位小车升降、工件编码识别、小车组自动组合拆分、吊具组合吊挂、行走快慢链转换、各工位连锁、互锁、故障诊断、报警等多功能控制,使工人操作灵活方便,减轻了劳动强度,极大地提高了劳动生产率。
4.4自动输漆调漆系统
在生产纲领较低情况下,多数采用人工调漆,而生产纲领较大的情况下,采用集中输漆调漆系统则更为有利:各喷漆工位集中调漆、供漆,实现了油漆涂料自动配比、自动搅拌、集中输送、系统控制调节喷漆量大小等,保证了作业场所供漆管路安全可靠、清洁卫生,节省能源效率高。
4.5自动抛丸清理技术应用
配合智能化输送系统,对焊后结构件进行整体抛丸清理除锈,清除氧化皮、焊渣焊瘤,消除工件内应力,增加表面粗糙度,确保工件表面清洁、无锈蚀,提高工件表面与涂层结合的附着力,保证产品表面涂装质量。
设备配置多台高效抛丸器,抛丸器采用计算机三维仿真布置设计,工件通过抛丸区时,一次性将锈蚀抛打干净,无死角;室体防护采用高耐磨轧制Mn13钢板,室体开口处采用迷宫式多层密封,防止弹丸飞溅,粉尘处理采用沉流式滤筒除尘器,二级除尘,除尘效率>99.5%以上。
4.6高红外固化技术应用
采用节能环保型高红外固化技术:粉末固化工件需要较高的烘干温度,采用传统的热风循环加热需要较长的烘干时间,生产线就需要布置较长的室体,生产线占地面积大;采用高红外辐射加热可以快速将工件表面加热到需要的烘干温度,升温快,热效率高,大大降低了粉末固化的工艺时间,占地面积小,节省能源,能耗少。
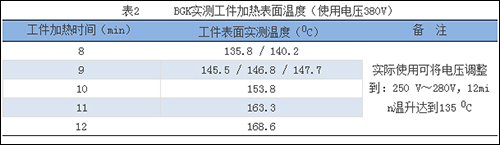
5、塔机涂装线环保措施
5.1废气处理
(1)含尘废气:喷、抛丸清理室的粉尘处理采用旋风+滤筒二级除尘,滤筒除尘器除尘效率≥99.5%以上,粉尘排放符合《大气污染物综合排放标准》(GB16297-1996)中表2的要求。
(2)喷漆室废气:较早建成的涂装线,一般采用水旋喷漆室通过水洗吸收及大风量稀释直接高空排放。随着新环保法规的实施,需要针对喷涂废气进行治理,新设计的塔机涂装线其喷漆室废气采用“过滤—活性炭吸附—热风脱附浓缩—催化燃烧”装置进行处理,也可同时处理流平室废气。其工作原理见图2。
(3)烘干室废气:烘干室废气一般通过“四元体”加热炉焚烧处理,根据加热方式不同,间接加热时将烘干室废气引入燃烧室,直接加热时则含有废气的循环风直接通过燃烧室加热循环,有机废气经焚烧处理后达标排放。
5.2废水处理
废水主要为喷漆废水,如采用脱脂、磷化处理,则还有清洗废水。按照规范分类收集,分质处理,达到国家和地方排放标准要求。在禁磷地区,磷化废水按照零排放设计,或可以采用硅烷替代工艺。
5.3废渣处理
涂装过程产生的废漆渣、磷化渣属于危险固体废弃物,送到具有资质的单位进行无害化处理。
5.4噪声处理
塔机涂装线喷、抛丸工作时,噪声可达到90~93db(A),目前设备上没有可行的降噪方法,通常是给工人配备个人劳动防护用品,按标准执行工人每日接触限时操作。对于喷漆、烘干设备,其主要噪声源为风机、水泵,一般采用减震、隔声等处理措施,使操作区周边噪声≤85db(A)。
6、结语
涂装技术的应用一般会受到产品性能、配置以及管理等诸多种因素的影响,随着人们对环保意识的增强、国家环保法规的进一步完善以及涂装技术的进步,涂装技术将进一步向高效节能、环保、健康安全方向发展。对于塔机涂装而言,采用高固体份涂料或粉末涂料,提高涂料利用率,进一步降低VOC排放,合理进行涂装涂层体系设计,提高产品防护装饰性能,将是今后的发展方向。