身披中远关西防腐涂层的深中通道沉管隧道首节钢壳顺利出运
2019-08-14 11:15:40
作者:本网整理 来源:中远关西涂料、深圳晚报
2019年6月26日上午,身披中远关西防腐涂层的深中通道沉管隧道首节“巨无霸”E1管节钢壳顺利出运。中远关西总经理王居仁、营销总监杨春玉应邀参加了出运仪式。
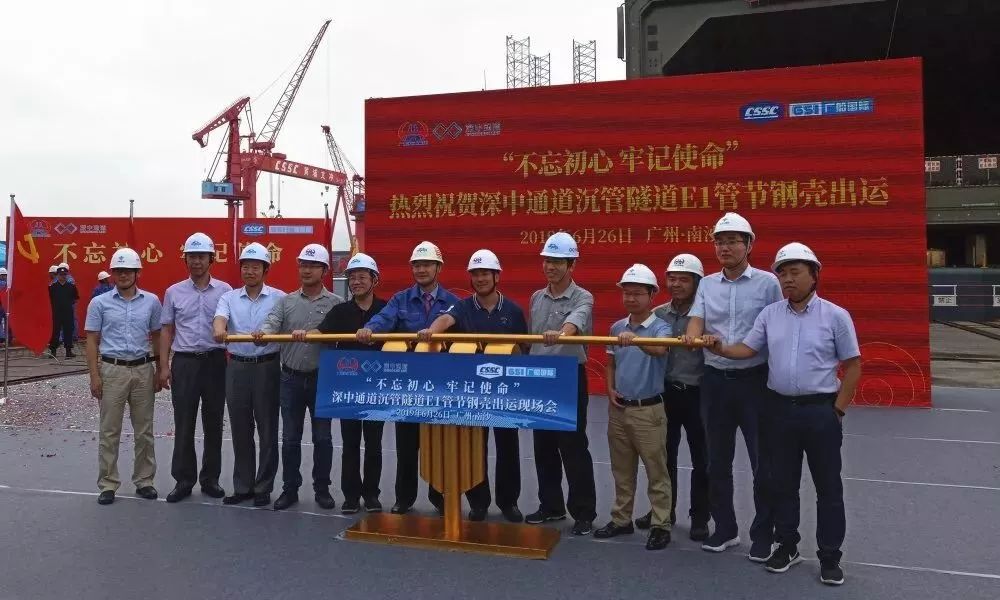
深中通道水下钢壳沉管防腐工程是中远关西继港珠澳大桥后又一世界级项目工程。该项目位于珠江三角洲核心区域,总投资约446.9亿。主体工程全长约24Km,采用东隧西桥方案,是世界超级大型“桥、岛、隧、水下互通”集群工程。
● “巨无霸”管节海上航行8小时
26日上午7时30分,装载着长123.8米、宽46米、高10.6米,总重达8716吨深中通道首个钢壳管节(E1)的半潜船“黄船030”缓缓离开制造基地港池码头,经过约8个小时的“海上航行”,当天下午3时30分抵达位于伶仃洋上的珠海桂山镇牛头岛预制场。“巨无霸”管节将在这里进行自密实混凝土浇筑、一次舾装、二次舾装等工序,为隧道沉管安装进行准备。
深中通道沉管隧道长约6.8公里,沉管段长约5.035公里,共32节。深中通道沉管隧道采用钢壳混凝土组合结构形式,该结构为国内首次应用。其中,两种标准管节尺寸分别为46×10.6×165米及46×10.6×123.8米,同时项目还包括5个总长为615米的变宽管节,其断面宽度从46米逐渐变宽至55米,是目前世界上最宽的海底沉管隧道。
● 智能生产线,每30天制造一节管节
据了解,根据深中通道项目的建设计划,平均30天要完成一节管节的制造。“深中通道沉管隧道标准管节排水量达到了8万吨,超过一艘中型航母的排水量。如果按照传统的人工制造方式,不可能在这么短的时间内完成管节制造。”深中通道管理中心岛隧工程管理部副部长钱叶祥介绍,为了提高制造工效,深中通道管理中心和船厂合作,结合BIM信息技术平台,建设了钢壳智能制造“四线一系统”,大力推行智能钢壳制造,大规模应用机器人智能化焊接、智能化打砂、智能化喷涂。这也是国内首条在超大型构件制造上大规模应用的智能制造系统。
● 高精度制造,确保隧道“滴水不漏”
为了保证隧道管节对接的精度、密实度,确保隧道“滴水不漏”,深中通道项目隧道沉管钢壳的制造精度要求极高。“在一个比标准足球场还要大一些的平面上,我们要做到正负的平面高差不超过10毫米,远超造船的精度要求。”广船国际深中通道GK01标项目部副经理邓凯介绍,经过检测,首节钢壳46米×10.6米的端钢壳平面平整度严格控制在了4毫米以内,管节的横向垂直度拟合面与竖向倾斜度拟合面差均控制在3毫米以内,充分满足超高精度质量的要求。
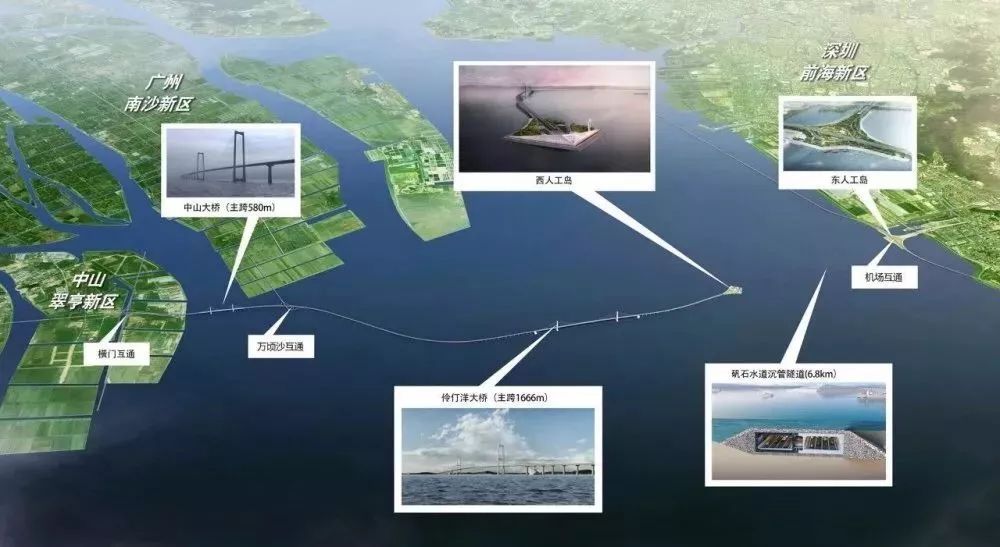
作为国内桥梁防腐行业佼佼者的中远关西,项目初期在公司总经理的亲自指挥下,销售、技术协同生产等相关部门精诚协作,克服了重重困难,最终顺利签下了深中通道GK01和GK02两个标段的涂料供应合同。同时,在管节施工过程中,公司领导亦亲自督战,精心组织,抽调各部门的骨干力量积极参与指导现场工作,现场技术服务工程师团队也充分发挥现场技术支持优势,与广船国际涂装部密切配合,确保这一百年工程不出一丝纰漏,圆满顺利的完成了深中通道沉管E1管节钢壳防腐涂装工作。
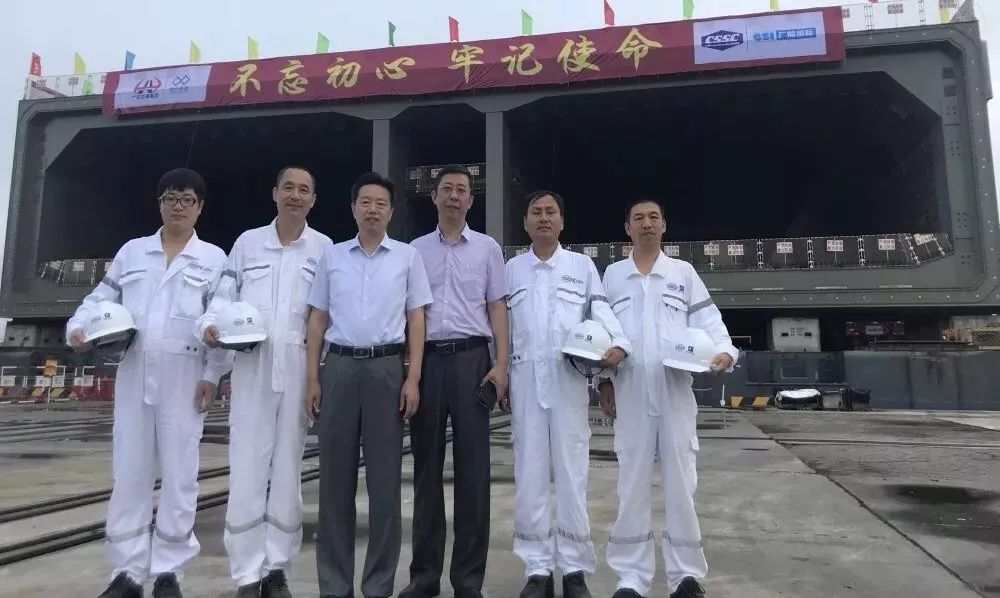
免责声明:本网站所转载的文字、图片与视频资料版权归原创作者所有,如果涉及侵权,请第一时间联系本网删除。