镁合金挤压技术及其工艺的研究
2016-11-17 16:56:32
作者:本网整理 来源:镁途
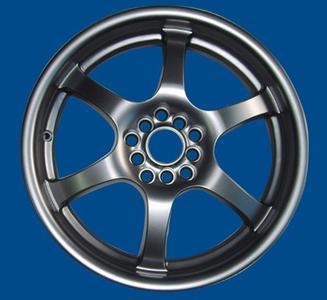
镁及其合金是实际工程应用中最轻的金属结构 材料,具有密度低、比强度和比刚度高、阻尼减震性 好、导热性好、电磁屏蔽效果佳、机加工性能优良、零 件尺寸稳定和易回收等优点,成为航空、航天、汽车、 计算机、电子、通信 和家 电等 行 业的重 要 新 型材 料 。镁合金的开发和应用存在着巨大的空间和 潜力,正如著名材料专家Cahn 所指出的,“在材料 领域中还没有任何材料象镁那样存在潜力与现实如 此大的颠倒。”
目前,压铸是镁合金成形的主要方式;但是压铸 件力学性能较差,并且容易产生微小的气孔,因此阻 碍了镁合金产品的进一步发展。变形镁合金因其良 好的综合力学性能而受到了重视。由于变形加工细 化了晶粒,消除了铸造过程中产生的一些缺陷,因 此,变形镁合金可以获得更高的强度和延伸率(见图1所示)。
1 挤压加工与其他加工方法相比的优势
任何金属材料进入市场的主要产品都是板材、 型材、管材、棒材、线材和箔材。其中,板材是塑性加 工中最重要的材料之一,板材的发展决定了型材和 线材的发展。其主要的塑性加工方法有挤压、轧 制和锻造等。挤压加工相比的优势如下。
1)工艺流程简单。例如,镁合金的板材目前以 轧制为主,需要通过多次的反复轧制才能成形,这样 工序多,生产效率较低。若采用挤压加工,在三向压 应力的作用下发生变形,通过一次挤压就可以制造 所需要的板材,从成本上来说,是十分有利的。张来 青等将铸造出的镁合金棒材,挤压获得不同厚度 的薄板,再通过轧制、退火制备出晶粒尺寸较小的镁 合金薄板,其具有良好的力学性能。
2)挤压技术生产的镁合金产品范围很广。板、 管、棒、线和型材都可以通过挤压加工来生产。其 中,许多断面形状的型材是采用其他塑性加工方法 所无法成形的。
3)提高了镁合金的变形能力。细化晶粒是提高 镁合金塑性最主要的方式。在挤压变形区中,镁合 金材料处于强烈的三向压应力状态,可有效的防止 由于塑性成形差而造成开裂。挤压加工很合适镁合 金这样低塑性难变形的合金加工。
4)产品的质量高。挤压变形可以改善金属材料 的组织,提高其力学性能。余琨等研究证明了ZK60镁合金经过挤压和T5热处理后,硬度和强度 都大幅度提高。汪凌云等研究挤压的镁合金管材, 其晶粒直径<20μm。
2 镁合金挤压变形技术
传统的镁合金挤压变形方法一般包括正向挤压 和反向挤压。随着挤压技术研究的不断深入,静液 挤压、连续挤压、等温挤压以及大塑性变形(Serve Plastic Deformation, SPD)挤压等先进挤压技术得 到迅速的发展。
2.1 连续挤压技术
连续挤压技术有CONFORM连续挤压、连续 铸挤和链带式连续挤压法等。其中,CONFORM连 续挤压已经得到了工业中的实际应用。国内镁合 金的连续挤压技术研究主要集中在CONFORM连 续挤压上面。
在工艺方面,杨俊英等以AZ31镁合金为研 究对象,研究了挤压轮转速对坯料各层面速度分布 的影响机制。结果表明,在连续挤压的过程中,金属 在不同变形区域的流动速度有差异。挤压轮转速越 大,不同层面金属的流动速度差值越大,流动的程度 越不均匀。这种流动分布特点是由于轮槽面的摩擦 驱动力与型腔壁摩擦阻力的相互作用形成的。吴桂 敏等对Z31镁合金连续挤压成形的工艺条件进 行了研究,结果表明,变形金属的等效应力在压实轮 下方最高,等效应变在模具入口处最大,型腔内的温 度最高。
在对显微组织的影响方面,宁海石等发现随 着挤压轮转速的增高,镁合金芯部区域的晶粒尺寸 逐渐增大;当转速达到一定速度时镁合金的表层和 芯部区域的显微组织达到均匀分布。杨俊英等 研究发现,加热温度对AZ31镁合金组织有显著影 响,随着温度的提高,显微组织的均匀程度也在提 高,当达到450℃时,芯部晶粒有长大的现象。由于 温度的提高,使材料发生充分的再结晶,材料的抗拉 强度增强,伸长率变化不大。连续挤压使得晶粒细 化,这是由于材料在挤压过程中经历了多种变形。
2.2 SPD挤压技术
SPD挤压技术是指材料经过SPD可以获得大 的塑性变形,极大细化晶粒组织,制备出亚微米级尺 寸的晶粒。细化晶粒是提高镁合金塑性的最有效的 途径,所以研究变形镁合金的SPD挤压技术,对提 高镁合金材料的性能有重要的理论意义和实际意 义。镁合金的SPD挤压技术包括等通道转角挤压(ECAP)、往复挤压(CEC)和S型等径侧向挤压 和大比率挤压(HRE)等。其中,等通道转角挤压是 目前最具有工业应用前景的挤压技术,所以在此主 要介绍ECAP技术的发展情况。
在工艺方面,任国成等研究了温度对AZ31镁合金ECAC挤压塑性变形机制的影响。结果表 明,在挤压过程中,试件存在明显的温度梯度,其中 在模具转角部分温度最高。通过XRD分析及微观 组织的观察发现,AZ31镁合金在经过挤压变形之 后,可以明显提高其锥面衍射的强度,而且可以加快 镁合金的再结晶速度,使其与变形温度成正比。刘 英 等研究了挤压道次对AZ31镁合金的性能影 响。结果表明,挤压次数的增多,晶粒明显细化,但 是不同的挤压路径对材料的性能影响不同,当到达 一定的挤压次数,镁合金的强度变化不大。
何云斌等从镁合金显微组织的角度分析,分 析了ZK60镁合金经过ECAP过程后不同部位所呈 现出来的显微组织特性。结果表明,在240℃ 下对 ZK60镁合金进行ECPA变形1道后,可以显著的 细化合金的晶粒,然而并不能使组织均匀。合金的 晶粒组织在剪切变形之前主要是粗而且大的晶粒, 而且还有很多孪晶,而在剪切变形之后,主要是再结 晶组织。ECAP过程中晶粒细化靠的是机械剪切以 及动态再结晶的综合效应。
3 镁合金挤压工艺
3.1 坯料均匀化处理
一般来说,在挤压之前,镁合金铸造坯料都需要 进行均匀化退火处理。这是因为 AZ系镁合金在铸 造冷却过程中易形成α-Mg+Mg17Al12,且随Al含 量的增加,γ-Mg17Al12相含量增加,并易呈粗大网状 分布于晶界。对该类合金进行均匀化退火处理, 可以使分布于晶界和枝晶间的粗大网状Mg17Al12相溶解,以细小颗粒分布于α-Mg基体中,从而显著 改善镁合金的塑性和可加工性。张丁非等研 究了在ZM61镁合金挤压过程中均匀化退火热处理 对其微组织和力学性能的影响。结果表明,均匀化 退火处理可以减小铸态组织中的残余应力,降低挤 压时所需要的温度和固溶时间,提高镁合金挤压后 的伸长率;但是均匀化处理并不一定会使镁合金挤 压后的力学性能提高。例如,对AZ91镁合金进行 均匀化退火处理,其伸长率由3.2%显著提高到11.2%。
与直接挤压相比,经过均匀化退火 处理的AZ91镁合金的伸长率有一定的提高,但是 抗拉强度和屈服强度并无明显变化。这可能是在较 大挤压比的条件下,基体发生动态再结晶,晶粒得到 细化,第二相在剧烈的塑性变形过程中被充分的破 碎,大量的第二相沿着挤压方向均匀的分布在基体 中,改善了铸造过程中第二相分布不均的状态,从而 提高了镁合金的力学性能,使其表现出与经均匀化 退火后,挤压态镁合金相当的综合力学性能;但由于 此时组织中已有较多的第二相存在,不利于随后的 时效强化处理。
3.2 挤压温度
温度是决定动态再结晶程度的重要因素。挤压 时,温度越高,所需要的挤压力越低,动态再结晶进 行得就越充分;但是,温度的升高也会导致晶粒的长 大,使组织晶粒粗大,降低了材料的力学性能。温度 相对较低时,可以得到细化的晶粒组织;但是挤压时 所需要的挤压力比温度高时需要的大,制件的残余 应力也变大。因此,合适的挤压温度是能否得到良 好的镁合金挤压件的关键。本文总结了AZ系列镁 合金试验最佳挤压温度。
3.3 挤压比
在镁合金的挤压过程中,挤压比与镁合金晶粒 的尺寸成反比。在挤压比小于一定比例时,挤压比 与镁合金的延伸程度成正比,当挤压比大于一定比 例时,延伸程度逐渐下降。出现这种情况的主要是 因为变形程度与组织特征有一定的关联性,当增大 变形程度时,位错密度也在变大,这样就会增加位错 运动过程中产生的位错塞积、割阶和缠结等,进而对位错的继续运动产生钉扎效应,提高抗拉强度,同时 增加变形晶粒的畸变能,使动态再结晶更加充分,从 而细化晶粒,组织更均匀,提高塑性;但是当挤压比 达到一定数值之后,因为不均匀的变形和应力分布, 会出现残余应力,进而造成金属内部的物理特性及 力学状况不均匀,最后出现塑性下降的情况。
3.4 挤压速度
挤压速度对镁合金挤压时所需的挤压力、凹模 模口坯料金属的峰值温度、产品的显微组织和室温 力学性能都有很重要的影响。张保军等通过有 限元分析模拟了AZ31镁合金薄壁管的分流挤压, 发现随着挤压速度的增大,模口的温度逐渐升高,挤 压力的最大值不断减小,当挤压速度到达一定程度 后,挤压力不再变化。罗永新等通过调节挤压速 度的方法,解决了镁合金挤压时温度范围窄的问题, 保持了挤压模口温度的稳定。赵秀明等发现,合 理的控制挤压速度可以获得细小均匀的晶粒和良好 的综合力学性能,挤压速度越大,合金发生动态再结 晶越充分,组织越均匀;当挤压速度较低时,合金强 度高但是塑性差,这是由于发生部分再结晶;当挤压 速度较高时,合金强度下降,伸长率明显提高,这是 由于发生完全再结晶,晶粒明显长大。
3.5 模具结构
合理的凹模结构可以降低挤压力,提高挤压时 金属的流动性,减少产品表面的裂纹。张丁非等 研究了模具结构对AZ31镁合金棒材表面裂纹的影 响。结果表明,相比锥模,采用流线模挤压能避免表 面裂纹的产生,死区产生的可能性减小。这是由于 表面的附加拉伸应力降低。黄东男等研究了模 具结构对AZ91镁合金的挤压过程温度场、速度场 及应力场的影响。结果表明,采用锥模和流线模挤 压时,当定径带长度为15~20mm时,可在挤压速 度达到5mm/s的条件下成形出表面光滑无裂纹的 镁合金棒材;而采用平模挤压时,当定径带长度为 10~20mm时,获得良好表面质量的挤压速度达到2.5mm/s。
4 总结与展望
1)成本问题一直阻碍着镁合金的工业应用,而 连续挤压可以实现无间断连续生产,提高了生产效 率,对降低镁合金的生产成本有重要作用。国内的 连续挤压技术主要是对铜、铝合金方面的研究,关于 镁合金的连续挤压研究较少。工艺条件是决定连续 挤压技术能否在镁合金上应用的关键。加深对这方 面的研究,可以推动镁合金的工业应用发展。
2)等通道挤压技术对镁合金显微组织的优化作 用是显著的,但其要应用到工业生产中,还需要解决 以下问题:a.模具的加工和维护比较困难,导致成本 过高;b.至今没有足够成熟的工艺参数,在镁合金 的研究当中尚属于起步阶段。
3)凹模挤出口对镁合金的影响是重大的,但无 论是平模、锥模还是流线模上,研究都不够深入。应 从如下2个方面进行深入研究:a.采用新的凹模尖 角结构,将锥面变成若干个小斜面,可以增加镁合金 挤出的过程中受力方向和次数; b.深入研究尖角角 度对显微组织的影响。
4)挤压温度、挤压速度和挤压比都是影响产品 的重要工艺参数,但是国内对各个型号镁合金挤压 工艺的研究并不详细,已有的工艺手册往往给出的 数值范围太宽泛;因此,系统的研究镁合金挤压技 术,归纳出较为准确的工艺参数,是镁合金挤压技术 工业应用的前提。
免责声明:本网站所转载的文字、图片与视频资料版权归原创作者所有,如果涉及侵权,请第一时间联系本网删除。