CFM准备从2016年开始由CFM56的生产逐渐过渡到LEAP-X发动机,到2020年实现年产1700台发动机。为实现这一产能需求,计划投资7.5亿美元,在美国密西西比州埃利斯维尔新建和扩建厂房,总面积扩至139350m2,用于量产CMC材料部件。
1)为了提高航空发动机的推重比和降低燃料消耗,最根本的措施是提高发动机的涡轮进口温度。而涡轮前温度与航空发动机热端部件材料的最高允许工作温度直接相关。陶瓷基复合材料是21世纪中可替代高温合金的发动机热端结构首选材料。
2)20世纪80年代,法国率先研制出SiC/SiC陶瓷基复合材料,并成功应用于M88-2发动机和F100型发动机。法国赛峰集团设计的陶瓷基复合材料(CMC)尾喷口在2015年6月16日搭载在CFM56-5B发动机上完成了首次商业飞行。CFM公司针对单通道客机的新一代发动机LEAP-X预计于2016年投放市场。
3)GE公司预测:2013-2023年航空发动机市场对CMC的需求将递增10倍。2013年6月GE投资1.25亿美金建设1.16万m2的生产基地。为确保高端SiC纤维的供应,2012年4月GE还携手SNECMA对外发布,将联合日本碳素公司合资成立NGS公司,生产和销售“Nicalon”品牌SiC连续纤维。GE正努力将CMC应用到发动机的各种部件,预计到2016~2018年间将日产800个CMC成品部件。CFM准备从2016年开始由CFM56的生产逐渐过渡到LEAP-X发动机,到2020年实现年产1700台发动机。为实现这一产能需求,计划投资7.5亿美元,在美国密西西比州埃利斯维尔新建和扩建厂房,总面积扩至139350m2,用于量产CMC材料部件。
4)SiC纤维位于SiC/SiC陶瓷基复合材料的上游,是整个产业链至关重要的一环。目前世界上仅日本和美国能批量提供通用级和商品级的SiC纤维,已实现产业化产能达百吨级的仅有日本碳公司和日本宇部兴产株式会社。根据纤维组成、结构及性能的发展变化过程,先驱体法制备的SiC纤维可分为三代,第一代为高氧碳SiC纤维,第二代为低氧高碳含量SiC纤维,第三代为近化学比SiC纤维。
5)我国从20世纪80年代开始,就有张立同院士领导的西北工业大学研发团队,以及中航工业复材中心、航天材料及工艺研究所、国防科大、中科院硅酸盐研究所等单位先后跟踪国际前沿启动研发工作。我国研究SiC纤维的主要单位有国防科技大学、厦门大学等,并取得了卓有成效的成果;苏州赛力菲陶纤有限公司是我国首家成功实现连续SiC纤维产业化生产的企业。目前国内已经突破第二代SiC纤和SiC/SiC复合材料研制关键技术,具备了构件研制和小批量生产能力,但在工程产业化方面与西方发达国家尚存在明显差距。
目录
1.SIC/SIC陶瓷基复合材料概述
1.1SIC/SIC陶瓷基复合材料——航空发动机高温合金首选替代材料
1.2SIC/SIC陶瓷基复合材料的性能特点
2.SIC/SIC陶瓷基复合材料构件的应用
2.1SIC/SIC陶瓷基复合材料构件的应用趋势
2.2国外SIC/SIC陶瓷基复合材料研制脉络
2.3世界三大航空发动机巨头对陶瓷基复合材料的应用研究
2.3.1GE公司
2.3.2罗·罗公司
2.3.3普·惠公司
3.SIC/SIC陶瓷基复合材料制造工艺与加工工艺
3.1SIC/SIC陶瓷基复合材料制造工艺
3.2SIC/SIC陶瓷基复合材料加工工艺
4.SIC纤维概述
4.1SIC纤维生产工艺
4.2SIC纤维的代际划分及主要性能
5.国内SIC陶瓷基复合材料及SIC纤维研制概况
5.1国内SIC陶瓷基复合材料构件研制情况
5.2国内SIC纤维研制情况
6.SIC陶瓷基复合材料构件及SIC纤维市场前景
6.1国际航空发动机巨头对SIC陶瓷基复合材料市场前景的判断
6.2SIC陶瓷基复合材料在我国航空航天发动机领域的应用前景
一、SiC/SiC陶瓷基复合材料概述
SiC/SiC陶瓷基复合材料——航空发动机高温合金首选替代材料
为了提高航空发动机的推重比和降低燃料消耗,最根本的措施是提高发动机的涡轮进口温度。数据显示航空发动机涡轮前温度每提高100度,在发动机尺寸不变的条件下,推重可以增加10%。涡轮前温度与航空发动机热端部件材料的最高允许工作温度直接相关。
50至60年代,发动机热端部件材料主要是铸造高温合金,其使用温度为800~900°C;70年代中期,定向凝固超合金开始推广,其使用温度提高到接近1000°C;进入80年代以后,相继开发出了高温单晶合金、弥散强化超合金以及金属间化合物等,并且热障涂层技术得到了广泛的应用,使热端部件的使用温度提高到1200~1300°C,已接近这类合金熔点的80%。虽然通过各种冷却技术可进一步提高涡轮进口温度,但作为代价降低了热效率,增加了结构复杂性和制造难度,而且对小而薄型的热端部件难以进行冷却,因而再提高的潜力极其有限。
陶瓷基复合材料正是人们预计在21世纪中可替代高温合金的发动机热端结构首选材料。
陶瓷材料的耐高温、低密度、高比强、高比模、抗氧化和抗烧蚀等优异性能,使其具有替代金属成为新一代高温结构材料的潜力。但陶瓷材料的脆性大和可靠性差等致命弱点阻碍了它的实用化。而连续纤维增强陶瓷基复合材料(CFRCMC,Continuous Fiber Reinforced Ceramic Matrix Composites,简称CMC)弥补了陶瓷材料的短板。
它基于陶瓷组分,采用高强度、高弹性纤维与成分相同或相近的陶瓷基体相互复合而成。由连续纤维补强增强陶瓷基体复合成材的混搭组合,类似于“钢筋+混凝土”的优势互补,连续的陶瓷纤维根据需要,可编织成二维或三维的“钢筋”骨架(即纤维预制体)、“混凝土”则为骨架周围紧密填充的陶瓷基体材料“水泥”,形成“1+1>2”的效果,具备高比模、耐高温、抗烧蚀、抗粒子冲蚀、抗氧化和低密度的优势。它可以具有类似金属的断裂行为、对裂纹不敏感、没有灾难性损毁。连续纤维增强陶瓷基复合材料主要包括碳纤维增强碳化硅(C/SiC)和碳化硅纤维增强碳化硅(SiC/SiC)两种。由于C/SiC抗氧化性能较SiC/SiC差,国内外普遍认为,航空发动机热端部件最终获得应用的是SiC/SiC。
SiC/SiC陶瓷基复合材料的性能特点
SiC/SiC陶瓷基复合材料是指在SiC陶瓷基体中引入SiC纤维作为增强材料,形成以引入的SiC增强纤维为分散相,以SiC陶瓷基体为连续相的复合材料。
SiC/SiC陶瓷基复合材料保留了SiC陶瓷耐高温、高强度、抗氧化、耐腐蚀、耐冲击的优点,同时兼具SiC纤维增强增韧作用,克服了SiC陶瓷断裂韧性低和抗外部冲击载荷性能差的先天缺陷。这种材料可以在1316°C的高温环境下保待其理化特性不退化。当SiC/SiC材料表面喷有热障涂层时,其最高工作温度可继续增加至1480°C。尽管现代商用发动机涡轮前温度可达1650°C,额外的170°C温差仍需采用压气机引气冷却来弥补,但这一引气量相比使用传统高温合金材料的叶片已大为减少。
据初步计算,采用耐温1480°C的CMC材料高压涡轮叶片可使发动机燃油消耗率降低6%。同时,采用CMC材料制成的燃烧室高温衬垫所需的冷却气量也大幅减少,进而降低冷却空气同燃油掺混后不完全燃烧生成氮氧化物的机会,其氮氧化物的减排潜力可达33%。
二、SiC/SiC 陶瓷基复合材料构件的应用
SiC/SiC陶瓷基复合材料构件的应用趋势
SiC/SiC陶瓷基复合材料在航空领域的应用主要包括发动机燃烧室内衬、燃烧室筒、喷口导流叶片、机翼前缘、涡轮叶片和涡轮罩环等部位。
国外在碳化硅陶瓷基复合材料构件的研究与应用方面,基于先易后难(先静止件后转动件,从低温到高温)的发展思路,首先发展中温和中等载荷的静止件,例如尾喷管调节片/密封片和内椎体等;再发展高温、中等载荷静止件,例如火焰筒、火焰稳定器及涡轮外环、导向叶片。更高载荷的静止件或转动件,例如涡轮转子和涡轮叶片还处于探索阶段。
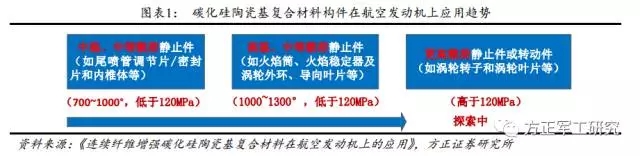
国外 SiC/SiC陶瓷基复合材料研制脉络
20世纪80年代,法国率先研制出牌号为CERASEPR系列的SiC/SiC陶瓷基复合材料,并成功应用于M88-2发动机(配套法国阵风战斗机)喷管外调节片和F100型发动机(配套美国F-15/F-16战斗机)调节片上。
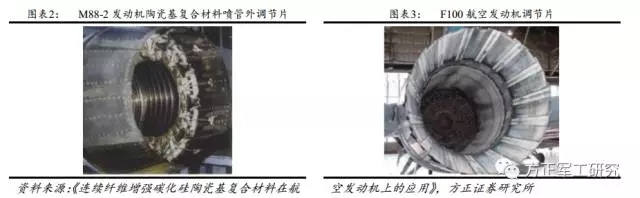
随后各个国家持续加大对SiC/SiC陶瓷基复合材料制造技术领域投入,如美国NASA的HIPTET、HSR/EPM和UEET计划,日本的AMG计划等,SiC/SiC陶瓷基复合材料制造技术逐渐成熟,应用范围也日益广泛。据报道,SiC/SiC陶瓷基复合材料目前已经成功应用于F110-GE-129发动机尾喷管、F136发动机涡轮叶片、F414发动机和CFMLEAPX发动机涡轮罩环等构件。
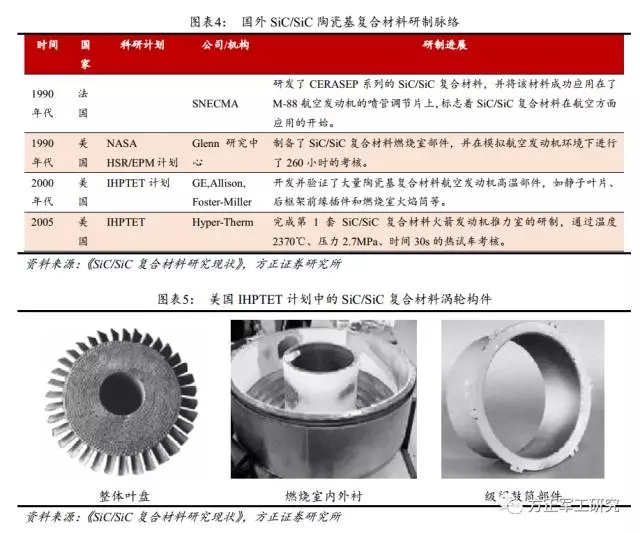
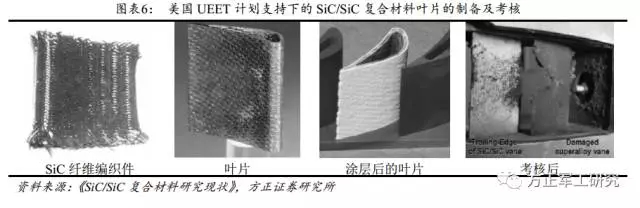
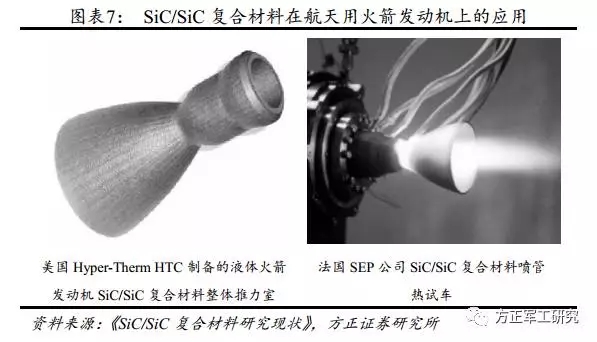
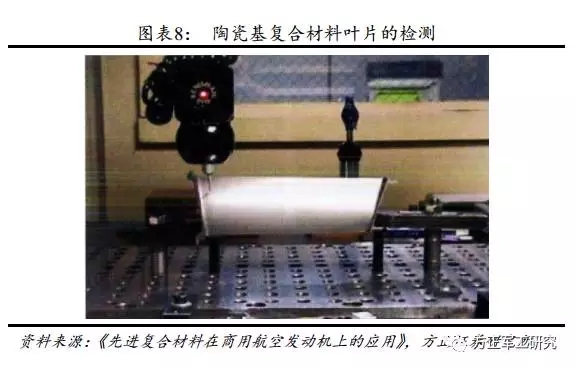
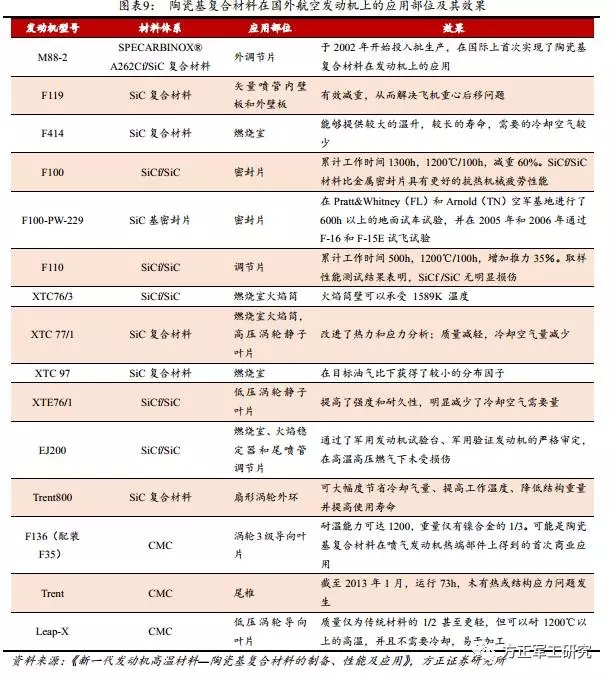
CFM是GE和法国赛峰集团(SAFRAN)旗下斯奈克玛公司(SNECMA)对半合资成立的公司,已向波音和空客提供了2.5万余台中型客机用喷气发动机。其经典之作CFM-56是全球装机最多的一款发动机产品,堪称传奇。
法国赛峰集团设计的陶瓷基复合材料(CMC)尾喷口在2015年6月16日搭载在CFM56-5B发动机上完成了首次商业飞行。赛峰通过旗下两家公司Herakles和SNECMA设计、制造了该尾喷口验证件并进行了地面试验。在2012年于A320上执行了初始试验后,CMC尾喷口验证件于2015年4月2日通过欧洲航空安全局(AESA)商业飞行使用认证。赛峰认为这项认证确认了其开发先进CMC零件的能力,能够满足日益增长的航空要求。
CFM公司针对单通道客机的新一代发动机LEAP-X预计于2016年投放市场,该发动机将配备由CMC材料制造而成的高压涡轮导向叶片。这被业内公认为商用发动机制造技术的又一次革新。
世界三大航空发动机巨头对陶瓷基复合材料的应用研究
1、GE 公司
21世纪初,GE公司引入CMC材料制造地面燃机的涡轮罩环,同时从静子部件、开始扩展CMC在喷气发动机上的应用范围。2016年投入使用的LEAP-1发动机的涡轮罩环由CMC材料制造,将实现CMC在商用航空发动机上的首次应用。一旦GE9X发动机在2020年之后投入使用,将极大扩展CMC在商用发动机上的应用范围。该发动机的燃烧室火焰筒、第一级高压涡轮喷管和罩环以及第二级高压涡轮喷管都由CMC制造。
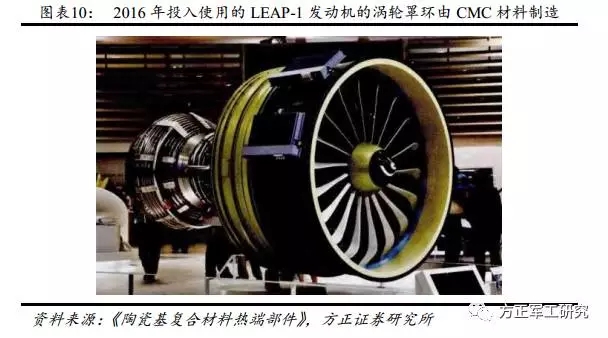
2015年初,GE9X发动机的首个全套CMC零部件在一台改造过的GEnx-1B发动机上开始试验。2014年末,GE在一台F414涡扇发动机平台上验证了由CMC制成的低压涡轮叶片的耐温性和耐久性,这是CMC材料在旋转部件上的首次成功应用。
2、罗· 罗公司
罗·罗计划将CMC引入其军民用发动机产品线。其计划内容包括在Advance系列的较小型号发动机上使用带有CMC内衬的无罩环涡轮以及urtraFan概念里的CMC喷管。2015年前后,罗罗公司还与Orbital-ATK公司一道加入了波音公司的787环保演示验证机项目,在美国联邦航空管理局(FAA)的Cleen项目指导下利用一台Trent1000发动机测试陶瓷喷管。试验结果显示CMC材料系统的耐高温性能超过了超合金,重量比钛合金降低了20%,有效降低了燃油消耗。
罗·罗公司2015年收购了位于美国加州的专业CMC生产商Hyper-Therm公司,该公司与NASA合作开发了首先用于液体火箭推进系统的主动冷却、连续纤维增强SiC基复合材料推力室。
3、普· 惠公司
普·惠公司十分注重耐高温陶瓷基复合材料在军民用发动机热端转子部件上的应用研究,而对CMC在热端静子部件上的应用效果却并不看好。一部分原因源于普·惠新发动机的低压涡轮级数配置,另一部分原因则是普·惠更加偏爱现金合金材料的热传导性能。与其他厂商5~7级的低压涡轮相比,普·惠发动机的低压涡轮只有3级,因此普惠主要关注能够承受2700°C以上高温的CMC材料,并认为CMC应用于转子件上才能带来最大收益。普·惠还打算在未来高压涡轮转子叶片上使用耐高温能力更强的CMC材料,这也是CMC材料低密度特性的价值所在。
普·惠公司认为,除制造成本外,CMC在静子件的应用还面临很多问题,其中一个问题就是热传导性。CMC的传热性相对较弱,而静子部件的重量要求又没有转子部件那么苛刻,因此具有更强传热能力的合金材料可能比CMC更适合制造静子部件。
三、SiC/SiC陶瓷基复合材料制造工艺与加工工艺
SiC/SiC陶瓷基复合材料制造工艺
SiC/SiC陶瓷基复合材料的制造工艺主要包括聚合物浸渍裂解工艺(PIP,Polymer Infiltration and Pyrolysis)、化学气相渗透工艺(CVI,Chemical Vapor Infiltration)和反应浸渗工艺(RI,Reaction Infiltration)等。日本和法国分别以PIP和CVI技术见长,德国在RMI技术领域技术世界领先,美国以CVI和PIP技术为主。目前在SiC/SiC陶瓷基复合材料制造工艺领域领先的研究机构主要有法国Boreleaux大学、美国Oak-Ridge国家实验室和日本OsakaPrefecture大学等。上世纪七十年代初期法国Bordeaux大学Naslian教授发明了CVl制造连续纤维增韧碳化硅陶瓷基复合材料(简称CMC-SIC)的新方法,现已发展成为工程化技术,而后美国购买了法国专利。
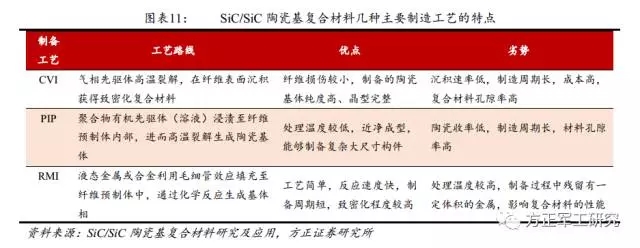
SiC/SiC陶瓷基复合材料加工工艺
由于SiC/SiC陶瓷基复合材料的硬度大,特别是材料由基体、纤维等多部分构成,具有明显的各向异性,加工后SiC/SiC陶瓷基复合材料的表面形貌、尺寸精度和位置精度等对构件的安全性、可靠性和使用寿命等都有重要影响,已成为制约SiC/SiC陶瓷基复合材料构件工程化应用的主要瓶颈之一。
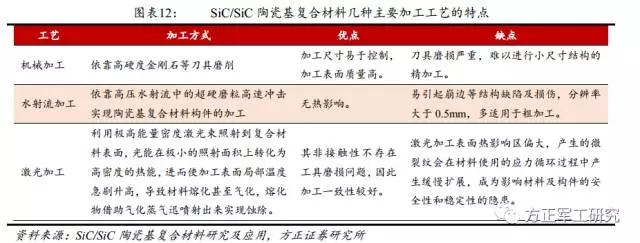
SiC/SiC陶瓷基复合材料的加工主要包括切边、钻孔、三维成型和微槽成型等内容。加工工艺主要包括机械加工、水射流加工、激光加工3类。
四、SiC 纤维概述
SiC纤维生产工艺
SiC/SiC陶瓷基复合材料通常由SiC纤维、界面层、SiC陶瓷基体和热防护涂层组成。
SiC纤维位于SiC/SiC陶瓷基复合材料的上游,是整个产业链至关重要的一环。由于SiC纤维有着其它纤维无可替代的作用,发达国家纷纷投入大量资金致力于此类陶瓷纤维的研制与开发。目前世界上仅日本和美国能批量提供通用级和商品级的SiC纤维,已实现产业化产能达百吨级的仅有日本碳公司和日本宇部兴产株式会社,典型产品牌号分别为Nicalon NL-200及Tyranno Lox M。
目前制备连续SiC纤维的方法主要有:先驱体转化法(3P, Preceramic Polymer Pyrolysis)、化学气相沉积法(CVD,Chemical Vapor Deposited)、活性碳纤维转化法(CVR,Chemical Vapor Reaction)等。其中,化学气相沉积法已逐渐被淘汰,先驱体转化法是目前比较成熟且已实现工业化生产的方法,是SiC纤维制备研究的主流方向。
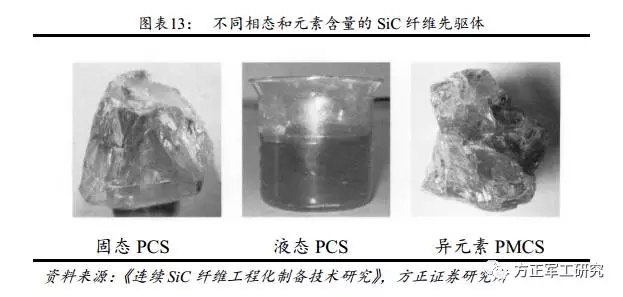
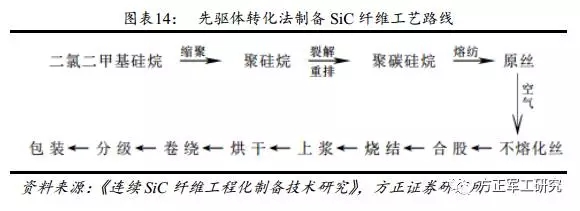
先驱体转化法制备SiC纤维,其工艺路线可分为聚碳硅烷(PCS)合成、熔融纺丝、不熔化处理和高温烧成4大工序,即首先由二甲基二氯硅烷脱氯聚合为聚二甲基硅烷,再经过高温(450~500℃)热分解、重排、缩聚转化为聚碳硅烷;在250~350℃下,聚碳硅烷在多孔纺丝机上熔纺成连续聚碳硅烷纤维,再经过空气中约200℃的氧化交联得到不熔化聚碳硅烷纤维,最后在高纯氮气保护下1000℃以上裂解得到SiC纤维。
SiC纤维的代际划分及主要性能
1975年日本东北大学的Yajima(矢岛圣使)教授用先驱体转化法成功开发出连续SiC纤维,奠定了先驱体法制备SiC纤维工业化的基础。1978年日本碳公司取得Yajima教授的SiC纤维专利实施权后,在日本新技术开发事业团的支持下,组织国内30多名顶级材料专家,经近10年的努力,耗资约11亿日元,于1989年完全实现了纤维的工业化生产,产品以Nicalon商品名正式进入市场销售。日本宇部兴产公司也于1988年产业化制成功另一种连续Si-Ti-C-O纤维,以Tyranno商品名销售。美国也于同期制备了多晶纤维,并以Sylramic商品名销售。
根据纤维组成、结构及性能的发展变化过程,先驱体法制备的SiC纤维可分为三代,第一代为高氧碳SiC纤维,第二代为低氧高碳含量SiC纤维,第三代为近化学比SiC纤维。其中,第一、二代SiC纤维基本是低密度、高碳含量、无定形纤维,其耐温性能一般不超过1300℃;第三代为高密度、近化学计量比、多晶SiC纤维,其耐温性能大于1700℃,能够满足许多尖端装备需要。
第一代SiC纤维:以日本碳素公司(NipponCarbon)的Nicalon200纤维和宇部兴产(UbeIndustries)的TyrannoLOX-M纤维为代表的高氧碳SiC纤维,一代纤维均采用氧化交联方式,最终纤维中的氧质量分数为10%~15%,当使用温度达到1200℃以上,纤维中的SiCxOy相发生分解反应,纳米SiC晶体长大,导致力学性能急剧下降。
第二代SiC纤维:以日本碳素公司的Hi-Nicalon纤维和宇部兴产公司的TyrannoLOX-E、TyrannoZM和TyrannoZE等低氧、高碳含量SiC纤维为代表,主要采用电子束交联,第二代SiC纤维中氧的质量分数降低,自由碳的质量分数相对较高,SiC晶粒尺寸较第一代大,纤维使用温度由1200℃提高到1300℃。
第三代SiC纤维:以日本碳素公司的Hi-NicalonTypeS、宇部兴产的TyrannoSA以及美国道康宁(DowCorning)公司的Sylramic等牌号的近化学计量比SiC纤维为代表,在组成上接近SiC化学计量比,游离碳和杂质氧含量明显降低,在结构上表现为高结晶度的SiC多晶结构,其耐温能力大幅提升至1700℃。
五、国内 SiC 陶瓷基复合材料及 SiC 纤维研制概况
国内SiC陶瓷基复合材料构件研制情况
我国从20世纪80年代开始,就有张立同院士领导的西北工业大学研发团队,以及中航工业复材中心、航天材料及工艺研究所、国防科大、中科院硅酸盐研究所等单位先后跟踪国际前沿启动研发工作。“硅陶瓷基复合材料”课题被列入总装“九五”预研计划,要求该课题在“九五”期间完成制备工艺研究,并对CMC-SiC的模拟件在发动机试验台上考核,结果仅用5年时间就实现了由制造工艺研究到构件考核的跨越。
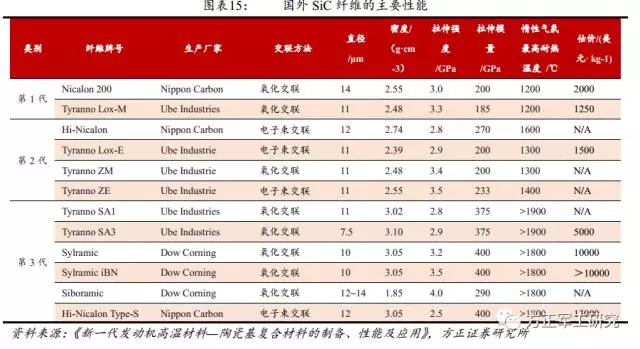
目前国内已经突破第二代SiC纤维和SiC/SiC复合材料研制关键技术,具备了构件研制和小批量生产能力,但在工程产业化方面与西方发达国家尚存在明显差距。根据西北工业大学张立同院士2003年1月发表在《航空制造技术》上的《新型碳化硅陶瓷基复合材料的研究进展》,“我国高推重比航空发动机的研制对陶瓷基复合材料也提出了需求,CMC-SiC燃烧室浮壁模拟件和尾喷管调节片构件已分别在发动机试验台和发动机上成功地进行了初步验证。”;“西北工业大学超高温复合材料实验室经过近7年的努力,自行研制成功拥有自主知识产权的CVI法制备CMC-SiC的工艺及其设备体系,CVI-CMC-SiC的整体研究水平已跻身国际先进行列。”;“目前已成功研制了20余种160余件CVI-CMC-SiC构件,其中液体火箭发动机全尺寸C/SiC喷管通过了高空台试车,CMC-SiC浮壁瓦片模拟件和调节片分别通过了航空发动机环境的短时间考核,C/SiC固体火箭发动机导流管通过了无控飞行考核。”由此可见早在十余年前我国碳化硅陶瓷基复合材料的工程化研制工作就已取得较大进展。
根据2006年10月西工大张立同院士及厦门大学陈立富教授联合署名发表的《高性能碳化硅陶瓷纤维现状、发展趋势与对策》,“我国已打破国际封锁,自主攻克了碳化硅陶瓷基复合材料构件批量制造技术,但是由于缺少高性能SiC纤维,目前只能用碳纤维代替。但是碳纤维耐氧化性差,严重限制了SiC/SiC在高温长时热力氧化环境中的应用,不能满足航空发动机热结构部件的要求。”由此可见,十年前我国SiC纤维的研制工作尚无法满足下游结构件的发展需要。
国内 SiC 纤维研制情况
SiC纤维因其特殊性,一直被作为军事敏感材料,国外对我国实行技术封锁和产品垄断。国内必须独立自主的开发和研究SiC纤维,尤其是耐超高温的SiC纤维,才能促进国内先进复合材料的发展和武器装备的研制,提高我国军事实力和综合国力。我国研究SiC纤维的主要单位有国防科技大学、厦门大学等,并取得了卓有成效的成果;苏州赛力菲陶纤有限公司是我国首家成功实现连续SiC纤维产业化生产的企业。我国从20世纪80年代开始SiC纤维的研究,比日本晚8年左右,而与美国和德国几乎同步。
20世纪90年代和21世纪初,国防科技大学和厦门大学分别开展了含铝SiC纤维和低氧SiC纤维、含杂SiC纤维的研究。在师昌绪、才鸿年、张立同和刘大响等一批院士的建议和支持下,这些研究获得国家有关科技计划的支持。国防科技大学是我国最早开展先驱体法制备SiC纤维和含钛SiC纤维研究的单位,经历了实验室制得短纤维到制备连续纤维和工业化开发过程。以冯春祥教授为首的科研团队经过艰苦的探索,于1991年建成了国内第一条连续碳化硅纤维实验生产线。目前已建成了产能500kg/年的SiC纤维中试生产线,制得了具有较好力学性能的连续SiC纤维及含钛碳化硅纤维。
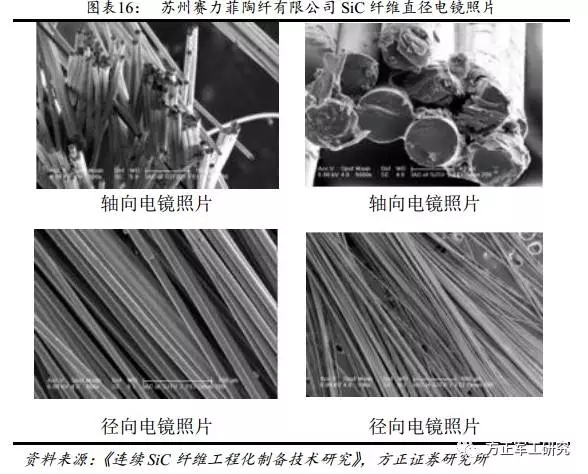
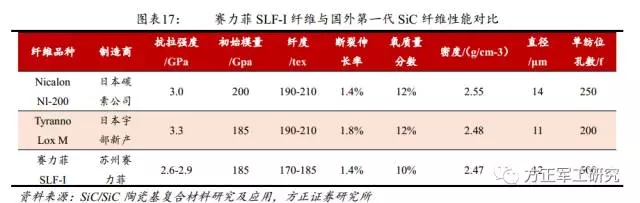
中国工程院张立同院士的领导下,厦门大学特种先进材料实验通过自主开发以及与国际合作研制,形成了国际先进、国内唯一的高性能连续陶瓷纤维的制造平台。制得的SiC纤维性能接近日本同类产品水平,目前正在进行小批量生产技术的完善。厦门大学的特色在于通过电子束辐射和热化学交联的方式,实现了SiC原丝纤维的非氧气氛交联,制得低氧含量的交联纤维,再经过高温烧成制得低氧含量的高耐温SiC纤维。
苏州赛力菲陶纤有限公司(简称苏州赛力菲)2005开始进行碳化硅材料研发,技术来源于国防科大。2011年,苏州赛力菲成功实现连续SiC纤维的产业化,并开始向国内相关单位提供可用纤维,使我国成为继日本和美国后又一个能实现连续SiC纤维产业化的国家。目前苏州赛力菲已经实现连续第一代SiC纤维SLF-I纤维的工程化生产,基本突破第二代SiC纤维制备关键技术,2~3年时间内可实现连续第二代SiC纤维工程化生产(年产能吨级)。
与国外产品相比,赛力菲SLF-I纤维的力学性能与编制性能接近或达到国外产品,但在综合性能和产能上仍有一定的差距。目前苏州赛力菲陶纤有限公司已经实现产能吨级连续SiC纤维,产能10吨/年的产业化基地正在建设中。
六、SiC 陶瓷基复合材料构件及 SiC 纤维市场前景
国际航空发动机巨头对SiC陶瓷基复合材料市场前景的判断
来自GE公司官方的预测:2013-2023年航空发动机市场对CMC的需求将递增10倍。据此,为应对CMC部件需求增长带来的产能压力,2013年6月GE投资1.25亿美金,在美国北卡罗莱纳州的阿什维尔建设1.16万m2的生产基地,用以支撑LEAP-X发动机CMC部件的量产,也为日后GE9X发动机供应所需CMC批产部件,并将逐步应用到为波音787和747-8提供动力的GEnx上,以及在CFM的新一代LEAP发动机上全面推广。
为确保高端SiC纤维的供应,2012年4月GE还携手SNECMA对外发布,将联合日本碳素公司合资成立NGS公司(NGSAdvancedFibersCo.Ltd.),生产和售“Nicalon”品牌SiC连续纤维,以确保“两强”对CMC关键原材料SiC纤维的持续供应能力。
GE正努力将CMC应用到发动机的各种部件,包括涡轮叶片升级用到F414中,预计到2016~2018年间将日产800个CMC成品部件,以兑现大力拓展CMC发动机部件应用的承诺。CFM准备从2016年开始由CFM56的生产逐渐过渡到LEAP-X发动机,到2020年实现年产1700台发动机。为实现这一产能需求,计划投资7.5亿美元,在美国密西西比州埃利斯维尔新建和扩建厂房,总面积扩至139350m2,用于量产CMC材料部件。
SiC陶瓷基复合材料在我国航空航天发动机领域的应用前景
根据《中国航天报》2014年5月的报道,中国航天科技集团公司六院11所研制生产的陶瓷基复合材料喷管首次参加地面试车,顺利通过了发动机方案验证。
根据中国商用航空发动机公司研究员2014年发表在《航空制造技术》的《商用航空发动机陶瓷基复合材料部件的研发应用及展望》,我国商用航空发动机处在追赶先进的研制阶段,不远的将来,也将推出装配具有自主知识产权CMC部件的国产长江系列商用航空发动机。
由此可见,我国航空航天发动机产业对SiC陶瓷基复合材料的研制正在稳步推进。SiC陶瓷基复合材料与SiC纤维应用前景值得期待。
更多关于材料方面、材料腐蚀控制、材料科普等方面的国内外最新动态,我们网站会不断更新。希望大家一直关注国家材料腐蚀与防护科学数据中心http://www.ecorr.org