解读电子封装无铅化及晶圆凸点电镀技术应用
2015-05-07 13:21:30
作者:本网整理来源:=$docheckrep[1]?ReplaceBefrom($ecms_gr[befrom]):$ecms_gr[befrom]?>
无铅化挑战组装和封装材料
铅的毒性已经广为人知,人们虽然仍在争论电子元件中的铅是否真的对人类和环境造成威胁,但人们已经更为关注废弃的电子器件垃圾中铅的渗透并产生的污染。大多数欧洲联盟成员国,已经在执行禁止在电子器件中使用铅的法律。欧盟关于铅等危险物的限制原则是尽量替换铅,只有在“技术上无法替换”时才可以使用铅。欧联的无铅法律将影响全球的电子产业,一来是由于供应链的全球化,再者也是由于在其它国家已经开始有类似的法律。为了实现无铅化,人们需要对倒装芯片封装、晶圆级封装、SMT和波峰焊进行广泛的材料研究和工艺评价,需要为板上倒装芯片和芯片级封装技术研究合适的材料和工艺。
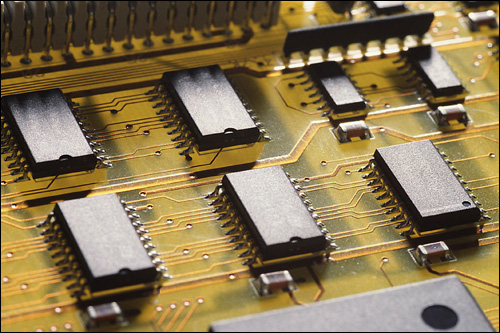
镂板印刷制作凸点
用镂板印刷或电镀制作的晶圆凸点,显示了无铅在倒装芯片和芯片级封装和组装领域的可行性。在凸点制备工艺中,需要给凸点底层金属(UBM)覆盖上新的焊材。印刷工艺之后,要在高于焊料熔点20℃的温度下进行回流,然后再进行清洗和凸点检查。UBM必须与新的焊料相匹配,采用化学镀镍工艺。晶圆加工是在一序列的化学池中进行的,在焊点清洗之后,紧接着进行的工艺包括:锌酸盐处理,表面活性化处理,镍(5mm)的淀积,金层的生长。该项工艺为FraunhoferIZM与柏林技术大学合作开发。采用化学镀镍工艺的UBM稳定性好,良率高,已被广泛使用。
焊膏印刷需要使用小间距模板、能适应微细间距要求的焊膏,以及优化的印刷参数。焊膏供应商已经生产了几种无铅焊膏,包括SnAg3.5、SnAgBixx和SnCu0.9。Sn95.5Ag4Cu0.5是共晶铅焊料的替代品,工艺良率成功通过了与SnPb的对比测试。滚刷速度、模板剥离和检查条件将决定产量。使用厚度为80mm的模板,能实现~110mm的凸点高度。使用SnAgCu0.5焊膏时,熔点温度由183上升到217℃,相应的回焊炉的温度设置也需从~205上升到235℃,典型的回流焊环境是使用氮气,它可以将氧化降到最小程度。
同时,为了确保良好的工艺控制,必须对凸点制备中的晶圆实施自动检测。最新的研究显示对凸点实施非100%的测试也能满足对凸点质量进行控制的要求,这样还能减少检测时间。SnAgCu凸点的光学检测由于其粗糙表面(与以前的SnPb焊膏的光亮表面相比)的影响实,施起来不太容易,所以,这一步显得更加关键,需要更加小心。抛开某些特例,成本核算表明,在FCOB的大批量生产中,用SnAgCu00.5替代SnPb的话,凸点制备工艺的成本可以达到低于每晶圆50美金。
迄今为止,倒装芯片凸点技术仍然是技术的亮点。小间距芯片级封装(>0.5mm间距)的出现,使得使用镂板印刷方法,可能替代固体植球方法。
可靠性问题
世界正在迈向无铅电子时代,汽车电子也对高熔点焊料提出了需求,这一切推动了产业对于新的焊料系统的选择。对于新焊料系统,关键之一就是可靠性。SnAgCu与SnPb37相比,二者的疲劳寿命和失效机制基本相同,实际应用中,受热历程和焊点形状决定疲劳寿命。研究等证明对于无电镀镍UBM,SnPb37和Sn95.5Ag3.8Cu0.7焊膏具有极佳的剪切性能。而且,底部填充料——PCB薄板上的倒装芯片都需要它来保证可靠性——能减少焊点的大部分应力,因而也就延长了它的寿命。
倒装芯片通常要使用两次回流焊工艺,一次是在晶圆上球点的形成时,另一次是在组装的时候。Ni3Sn4是无电镀镍UBM上的SnPb焊料以及SnAgCu焊料形成的金属互化物。经过两次回焊,金属化后,Sn95.5Ag3.8Cu0.7的形态基本正常而且厚实。在较高的温度下倒装芯片的老化显得十分关键。150和170℃时老化1000个小时,SnPb及无铅合金会随着镍的消耗,转化成小于2mm的Ni3Sn4。对于Sn95.5Ag3.8Cu0.7,其镍的耗散厚度大约是SnPb的两倍。同样的,对于Sn95.5Ag3.8Cu0.7,在170℃而不是150℃时老化,镍的厚度消耗会增加4倍。
在150℃环境里保存2000小时后,对焊接凸点的剪切力测试的结果表明,Sn95.5Ag4Cu0.5的剪切力大于SnPb37。而且,对于Sn95.5Ag4Cu0.5,经过高温高湿(85℃和85%RH)保存,以及温度循环(-40到150℃,1000cycles)之后,剪切力测试结果表明其可靠性比SnPb37稍好。对-40到125℃温度循环后的倒装芯片封装进行测试,结果显示Sn95.5Ag3.8Cu0.7的效果要好于SnPb37。但是Sn95.5Ag4Cu0.5的可靠性不如常规的SnPb37(循环温度-55到125℃,及-55到150℃)。上述两种情形,填充底料的选择,熔化物残留的多少,以及实际结合高度将决定哪一种连接方式更好。这表明合金的选择对于产品的可靠性仅仅是第二号的因素。在150℃的环境下,现在流行采用含锡焊料。而在更高的温度环境下,共晶的金锡(Au80Sn20)焊料或充银焊料能支持到200℃。
CSP的连接通常不使用任何填充底料,人们希望无铅焊料的较大的机械弹力能够有效提高其器件的寿命。然而,必须注意的是,失效模式可能在厚的金相处由疲劳开裂转为碎裂,或者金属焊点会从底材分离,因为柔软的SnPb的蔓延导致固体凸点中产生的应力无法得到释放,只能通过弹性无铅焊料传递到表面。
#p#副标题#e#
超细间距焊膏和无铅焊料
晶圆凸点制备需要的是6型焊膏,它能确保焊膏均匀,因而减小回流焊后凸点高度的改变。与PCB板上传统的SMT焊锡膏印刷相比,超细间隙焊膏的细小焊点,需要焊膏具有更高的粘性,对印刷性能、以及焊膏与模板的脱离有较大影响。增大的面积和体积比意味着焊料合金的氧化性增大,因而焊膏中氧化物含量较高,所以回流焊工艺需要氮气保护。相同的技术适用于SnPb37焊膏,也同样适用于三元或四元小间距焊膏。
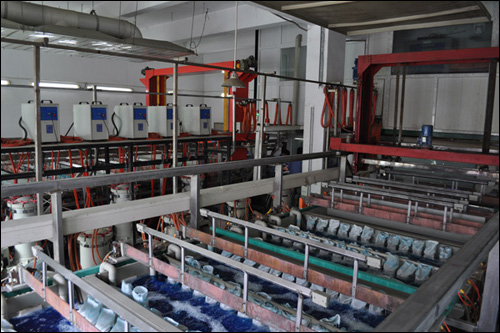
晶圆凸点的电镀
镂板印刷的适用间距极限是150-200mm。对于间距小,凸点尺寸范围宽的高互连密度的情形,电镀技术是首选。FraunhoferIZM采用了间距小于40mm的电镀工艺。国际半导体技术蓝图研讨会(ITRS)预测,随着倒装芯片技术的发展,其凸点间距将呈现减小趋势,对于高I/O芯片和高能芯片,减小的趋势是,从2002年的160mm减小到2010年的90mm,2016年更减小到70mm。
电镀时,凸点高度的均匀性要求在±1mm之内,这大大超过了镂板印刷的均匀性指标。这是由于模板材料厚度和激光切割的精度变化较大,而且在模板的开口处会有少量焊膏残留,其典型的变化范围在±7mm。
电镀的成品率损失在ppm量级甚至更低。按照失效标准的定义,从凸点高度均匀性的角度来看,电镀比镂板印刷的损失要小。因此,对于高产量,大尺寸IC来说,电镀是一项低成本技术,而成品率的损失使得镂板印刷失去了可比性。
电镀时UBM要镀上Ti/W/Cu,它们被均匀溅射在整个晶圆表面上,其后进行光刻,形成凸点焊点。镀上的附加层铜,会被回流焊和金属化合物热应力部分地消耗掉。焊料金属是以电化学的形式——基于甲基硫酸的方式——进行淀积。电镀加工时间的长短取决于凸点的高度——与焊膏楼板印刷正好相反——即电镀时间受限于较小凸点的高度。电镀膜脱膜之后,以刻蚀方法去掉Ti/W/CuUBM。将晶圆上的淀积焊料回流,形成球形凸点,然后进行清洗,去掉有机残留物。在FraunhoferIZM,人们完成了数种无铅焊料的电镀,并进行了深入观察。SnPb焊膏的最佳替代是SnAg,因为它有某些特殊特性。银的电极势差较高,因而比起锡来更容易淀积。所以,需要对银离子添加超强配位剂以抑制银的过早淀积。
然而,Sn-Pb的二元相图表明,焊料成分的小的差异并不会给熔点造成多大影响。而对于SnAg,影响却十分明显。含银3.5%的共晶中增加一点点银的话,熔点就会极大地升高。此外,FraunhoferIZM的研究还表明,对含银4%时,大块状的Ag3Sn金属化合物的生长更快,给互连的可靠性带来严重损害。对于共晶SnAg3.5电镀,电镀池和合金成分的控制,显得及其重要。三元合金的电镀加工更加困难,甚至不予考虑。另一方面,由于UBM的铜电镀层会部分溶解于SnAg,因此回流焊凸点总会包含SnAgCu合金,而且会受到回流焊温度的影响。与SnPb相比,使用SnAg时铜电镀基材的消耗更多。因此,提供的电镀铜必需有一定的厚度。如果再考虑到加工成本的话,SnPb电镀和SnAg电镀没有本质的差别。
总之,镂板印刷的实现和电镀晶圆凸点的制备代表了先进互连技术无铅化的现状,也证明了无铅化技术是切实可行的。
相关文章